With the rapid development of 3D printing technology, its applications in the machine tool and manufacturing industries are becoming increasingly widespread. However, many still have questions: is 3D printing truly suitable for real-world production? Can it improve manufacturing efficiency, reduce production costs, or achieve complex designs that traditional processes struggle to create? Driven by these questions, many people are turning their attention to 3D printing, hoping to understand its advantages and practical uses.
At its core, 3D printing is an “additive manufacturing” technology, building objects layer by layer, completely different from traditional “subtractive manufacturing” methods like cutting and milling. This process brings greater flexibility to production, making it ideal for rapid prototyping, complex part fabrication, and small-batch customization. In the machine tool industry, 3D printing serves not only as an effective standalone production tool but also as a powerful complement to traditional manufacturing methods.
In this article, we will explore 3D printing’s key benefits, typical applications, selection guidelines, and optimization techniques from a practical standpoint. Our goal is to help you fully understand the potential and suitability of this technology, making 3D printing an indispensable asset in your production processes.
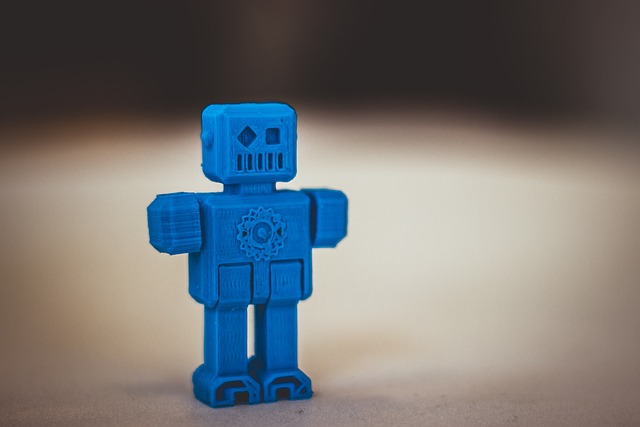
I. Why Choose 3D Printing: Meeting Practical Application Needs
Whether aiming to shorten development cycles, produce complex parts, or reduce production costs, 3D printing provides solutions to meet these demands. Let’s look at these practical needs to understand why 3D printing holds unique advantages:
1. Rapid Prototyping: Significantly Shorter Development Cycles
In traditional manufacturing, new product development often involves multiple steps, such as design, mold-making, prototyping, and testing. With 3D printing, the mold-making step is no longer needed, as parts can be created directly from digital models, reducing prototyping time to mere hours or even minutes. This allows companies to quickly validate product designs and make adjustments based on test results, avoiding the cost and time associated with repeated mold revisions. As a result, development cycles become shorter, and trial-and-error costs are significantly lowered.
2. Complex Structure Manufacturing: Achieving Designs Difficult for Traditional Methods
In traditional processing, creating parts with complex internal structures or unique shapes can be challenging and costly. 3D printing, however, can build intricate geometries layer by layer, such as hollow structures, internal channels, and honeycomb supports, which are especially valuable in aerospace and medical fields. For instance, airplane components often require structures that are both lightweight and durable. With 3D printing, it’s possible to produce such complex, lightweight structures directly. Boeing, for example, 3D prints engine support parts, reducing their weight by nearly 30%, which greatly enhances fuel efficiency.
3. Reducing Material Waste: Saving Costs and Meeting Environmental Standards
Compared to traditional methods, 3D printing is an additive process, meaning it only uses the materials necessary for the structure, rather than removing excess through cutting or drilling. This approach minimizes material waste and achieves a material utilization rate of over 95%. For high-cost materials like titanium alloys and specialty ceramics, 3D printing is particularly advantageous, as it reduces production costs and supports green manufacturing goals. In the medical field, 3D printing technology is used to create custom titanium implants, significantly reducing material waste while enabling on-demand production.
4. Small-Batch Production and Customization: Flexibly Adapting to Market Changes
There is a growing demand for small-batch, customized products that traditional large-scale manufacturing methods struggle to accommodate. 3D printing eliminates the need for molds, allowing flexible response to small-batch and personalized requirements. Additionally, it can produce items on demand, shortening delivery times. For example, many custom products in the medical and consumer electronics industries rely on 3D printing to meet client needs quickly and efficiently.
II. How to Choose and Optimize 3D Printing Technology: Focus on Practical Needs and Technical Performance
Once the practical applications of 3D printing are clear, the next step is to choose the right 3D printer and optimize its effectiveness. Below are essential steps to guide you in making informed decisions when selecting and using a 3D printer:
1. Define Printing Requirements and Choose the Right Technology
There are several types of 3D printing technology, including FDM (Fused Deposition Modeling), SLA (Stereolithography), and SLM (Selective Laser Melting). Each technology suits different fields and offers unique benefits:
- FDM: Suitable for producing larger, simpler plastic parts at a low cost, making it ideal for prototyping.
- SLA: Achieves high precision and excellent surface quality, best for manufacturing small, intricate parts.
- SLM: Enables the production of high-strength metal parts and is perfect for custom complex structures.
Recommendation: If the primary goal is prototyping and the budget is limited, FDM is a good choice. For high-precision metal parts, SLM may be more suitable.
2. Focus on Material Characteristics and Printing Costs
The types and prices of 3D printing materials vary greatly, and each material has different printing characteristics and performance. For instance, plastic is affordable and easy to print but has lower strength and heat resistance. Metal powders provide high strength but are more expensive and require specific printing conditions. Choosing the right material based on production needs can help achieve desired print quality and control costs.
Optimization Tip: Balance quality and cost when selecting materials. Compare material performance to determine the best option, and consider bulk purchasing frequently used materials to reduce per-print costs.
3. Evaluate Print Precision and Surface Quality
For certain parts, surface quality and precision are critical, as they directly impact product functionality and appearance. For example, in the consumer electronics field, printed products need a certain level of smoothness; otherwise, post-processing may increase costs. Since different 3D printer types vary in precision and surface quality, choose a printer that meets your specific requirements.
Practical Advice: If surface quality is crucial, consider SLA or SLM printers that provide better surface finish and plan for any necessary secondary processing.
4. Assess Printing Speed and Optimize Production Workflow
Printing speed affects production efficiency, especially in small-batch production where faster printing becomes crucial. Selecting faster equipment can shorten production cycles and improve delivery times. In practice, printers with multiple nozzles or dual-material capabilities can improve efficiency and meet more complex production needs.
5. Focus on Smart Features for Enhanced Management Efficiency
Modern 3D printers often include smart features such as remote monitoring, automatic calibration, and material recognition. These capabilities not only reduce manual steps but also lower the risk of human error. Choosing a 3D printer with intelligent features can improve overall production management efficiency and provide visual control over the production process.
III. Future Trends in 3D Printing
Over the coming years, 3D printing technology will continue to mature with advancements in material science and manufacturing processes. It is expected to see broader applications in the following areas:
- Mold Manufacturing and Repair: it can quickly produce complex molds, reducing the time and cost of traditional mold making. Additionally, additive manufacturing allows damaged molds to be repaired, extending their lifespan.
- Small-Batch Custom Production: With faster print speeds and more material options, it will become increasingly capable of small-batch custom production, especially in aerospace, medical devices, and high-end consumer goods.
- New Material Development: In the future, more types of 3D printing materials will be developed, including high-strength alloys and functional ceramics. New materials will expand 3D printing’s market and technical scope, further enhancing its practical value in industrial applications.
- Educational and Research Applications: 3D printing is already widely used in education and research, and in the future, it will support more experimental projects and help train a new generation of technical talent.
Conclusion
As an emerging force in manufacturing, 3D printing provides unique solutions for accelerating product development, enabling complex designs, reducing material waste, and meeting customization demands. By thoroughly understanding the core advantages of 3D printing and selecting the right equipment and materials based on actual needs, businesses and individuals can maximize its potential to boost production efficiency and control costs. Although challenges remain, continuous advancements in technology and material options will bring even more innovative opportunities to manufacturing.
3D printing serves not only as a production tool but also as a key technology for helping companies gain an edge in a competitive market. By applying 3D printing strategically, businesses can achieve greater flexibility and faster response times, paving the way for a future of more efficient, eco-friendly, and customized manufacturing. If you would like to explore how 3D printing can benefit your production processes, please visit our company website. Our professional team is ready to provide you with technical support and tailor-made solutions.