Manual Lathe
Minno, as a high-precision manual lathe manufacturer in China, we can supply the best quality manual metal machine tools, welcome to contact us for quotation!
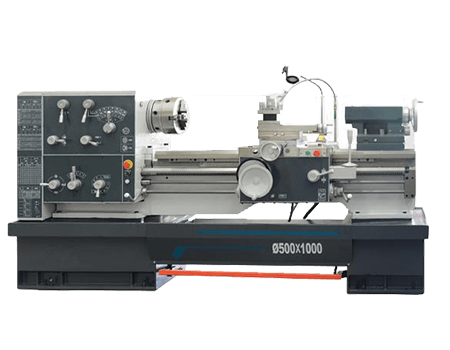
PRODUCTS CATEGORY
Intelligent Manufacturing Production Line
+Machining centers
+Lathe Machine
+Milling Machine
+Grinding Machine
+Drilling Machine
+Metal forming equipment
+Boring machine
+Machine Tool Accessories
+Related News
Manual Lathe
Manual lathe, also known as conventional lathe, hand-operated lathe, is a conventional metal cutting machine tool, is also one of the most widely used machine tools, accounting for about 65% of the total number of lathes. It is mainly used for turning by rotating the workpiece and following a straight path with a single-edged tool to produce accurate cylindrical, conical or shaped external surfaces.
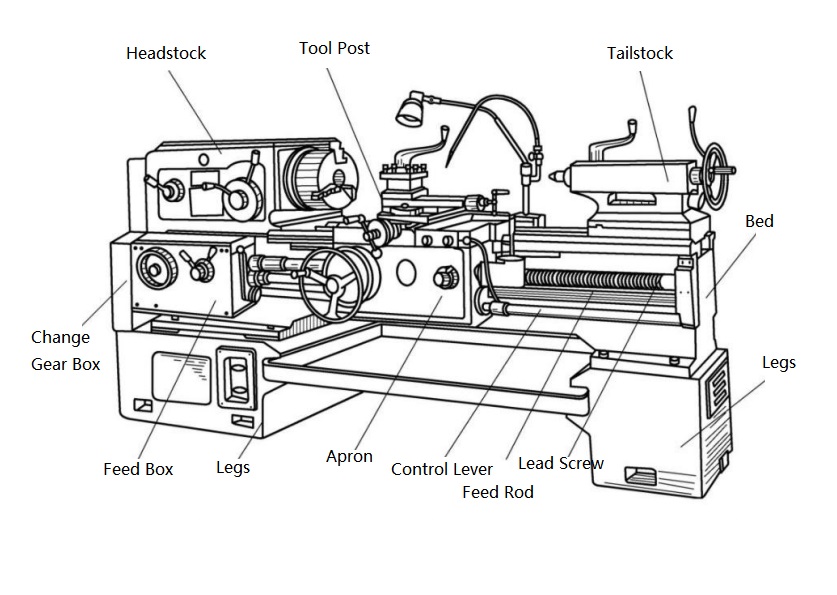
Manual Lathe Structure
Manual Lathe Structure Performance
Manual lathes feature a horizontal structure with high power and robust rigidity, providing a wide range of spindle speed adjustments. This makes them suitable for heavy-duty or high-speed cutting operations. They are capable of performing a variety of machining processes, including turning the inner and outer cylindrical surfaces, taper surfaces, and end faces of shafts and discs, as well as grooving, chamfering, drilling, and tapping. Additionally, manual lathes can handle threading operations for metric, imperial, module, diametral pitch, and taper threads. The tool post allows for the motorized turning of short tapers, while the combination of longitudinal feed and tool post feed enables the machining of long tapers, demonstrating exceptional capabilities in handling large and complex parts.
By focusing on these versatile functionalities, manual lathes are highly regarded for their adaptability in various machining tasks, making them an indispensable choice for workshops needing precision and flexibility.
Key Structural Features
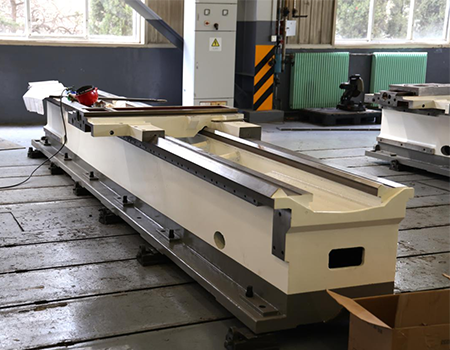
This lathe utilizes a traditional horizontal layout with an integrated design that ensures excellent rigidity and compliance with safety standards. Major foundational components, such as the bed and headstock, are made from resin sand castings that undergo manual aging treatment, providing exceptional overall stability. The bed is constructed from HT300 cast iron, and the bed guideways are induction-hardened to a hardness of HRC48, significantly enhancing the longevity of the guideways.
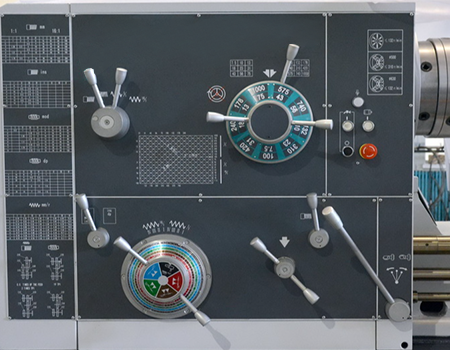
The lathe's headstock is designed with centralized control handles for easy and flexible operation. The spindle system utilizes a three-point support structure, ensuring high precision and strong rigidity in the front and rear bearings. The spindle's braking and forward/reverse rotation are hydraulically controlled, providing responsive and reliable braking. Speed changes can be made without stopping the machine, using a push-button for seamless operation. The headstock is equipped with a forced lubrication system using pressure oil, contributing to its aesthetically pleasing appearance, excellent rigidity, high precision, smooth operation, low noise, ease of assembly, and minimal spindle thermal deformation.
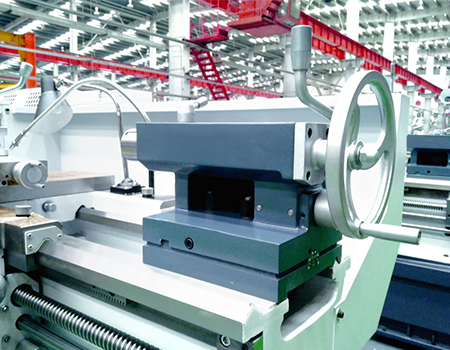
The tailstock sleeve features a metric bore of φ75 mm and utilizes a top clamping mechanism, ensuring reliable clamping and enhanced overall rigidity of the tailstock. Additionally, options for tailstocks with a φ200 mm or φ240 mm rotating spindle are available, providing users with flexibility to choose according to their specific machining needs.
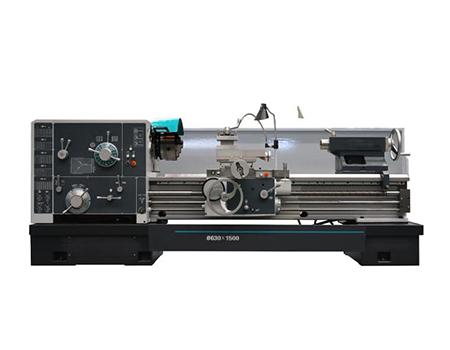
The lathe is equipped with a full range of functionalities, offering easy operation, stable precision, and reliable performance. It also features an aesthetically pleasing and elegant overall design.
Minnuo Manual Lathe Machine: Quality in Every Detail
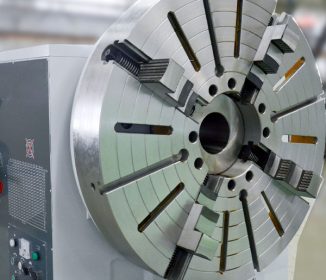
Metal Chuck
Three-jaw/four-jaw chucks can be assembled according to customer requirements for lathe models.
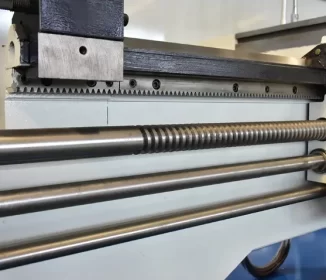
High Precision Screw
Good wear resistance and accuracy retention, ensuring a long service life of the machine.
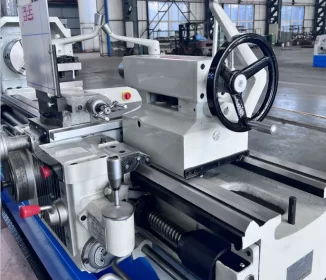
Quenched Tailstock
The tailstock sleeve is treated with high-frequency quenching and carefully ground to prevent wear and tear.
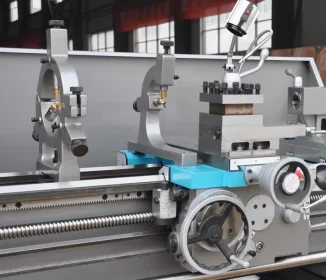
Lathe Body
Hardened-tempered casting body makes high rigidity, high precision, and long Life.
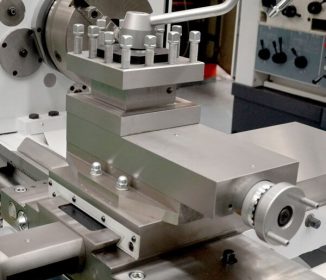
Four-station Tool Holder
Four-station tool holder can be operated with one hand, and tool holder protection is optional.
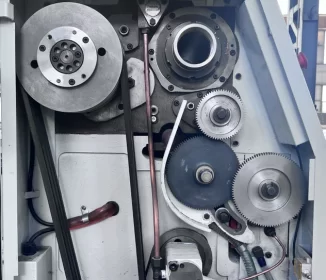
Spindle HeadBox
Strictly Processed Hardened-Tempered casting gears make the spindle head box perform precisely.
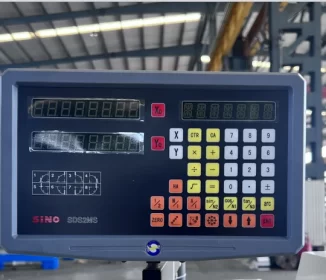
2 Axis DRO
2 Axis Digital Read Out is available as an option.
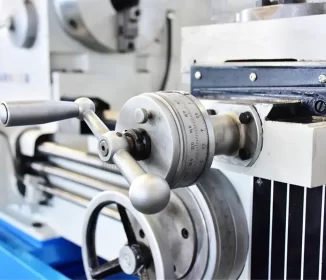
Fast moving device
Quick advance and retreat of sliding carriage box.
Manual Lathes Types
Manual lathes come in various types, each designed for specific machining tasks. Below are some common types of manual lathes:
- Engine Lathe: The most common and versatile type of lathe, suitable for a wide range of tasks such as turning, facing, drilling, and threading. It is often used for machining workpieces of varying sizes.
- Turret Lathe: Equipped with a rotating turret that allows quick switching between multiple tools, making it ideal for repetitive production tasks.
- Toolroom Lathe: A high-precision lathe used for fine machining and the manufacture of small, complex parts, typically employed in tool and die making.
- Bench Lathe: A smaller version of the engine lathe, designed to be mounted on a workbench. It is suitable for light-duty machining tasks and small workpieces, commonly found in workshops or hobbyists’ workspaces.
- Gap Bed Lathe: Features a removable or adjustable bed section to accommodate large-diameter workpieces, suitable for parts that cannot be clamped on a standard lathe.
- Speed Lathe: A simple lathe without automatic feed or carriage, primarily used for woodturning, metal spinning, and polishing, typically operated at high speeds.
- CNC Cam Lathe: Similar to a turret lathe but better suited for mass production, capable of quickly producing identical parts with minimal setup time.
Each type of manual lathe is designed for specific applications and offers unique advantages based on machining needs. If you are unsure which type of lathe is suitable for your needs, you can provide your workpiece drawings or the model of the machine you previously used, and our professional engineers can offer you more tailored advice!
Manual Lathe Video
Product Applications
Manual lathes have a wide range of applications, spanning from heavy industry to precision engineering. Below are some of the main areas where manual lathes are utilized:
Machinery Manufacturing: Used for machining mechanical components such as shafts, gears, and bearing housings.
Automotive Industry: Employed in the manufacturing of automotive parts, manual lathes are used for precision machining of engine components, drive shafts, and more.
Aerospace: In the aerospace sector, manual lathes are utilized to machine high-precision parts, such as turbine blades and landing gear components.
Mold Making: Manual lathes are used in mold making to machine precise molds and models.
Repair and Maintenance: During maintenance and repair operations, manual lathes are employed to refurbish or modify existing mechanical parts.
Precision Engineering: Manual lathes are capable of meeting strict tolerance requirements in applications requiring high-precision machining.
Education and Training: In technical schools and vocational training centers, manual lathes are used for teaching and hands-on practice for students.
Small Production Workshops: In small workshops focusing on low-volume production or prototyping, manual lathes are widely used due to their flexibility.
Manual lathes maintain an important position across various industrial and engineering fields due to their ease of operation, cost-effectiveness, and reliance on operator skill.
Why Choose a Manual Lathe (Compared to CNC Lathes)
How to Operate a Manual Lathe ?
Equipment Inspection and Preparation: Before starting any work, ensure that all components of the lathe are functioning properly and clear the workspace to maintain safety. Minnuo’s manual lathes are renowned for their high precision and stability, providing you with a more reliable operating experience.
Workpiece Clamping and Tool Installation: Select the appropriate chuck to securely clamp the workpiece onto the spindle, ensuring no movement. Choose the correct tool for the machining task, install it on the tool post, and adjust the tool height to align with the centerline of the workpiece. Our manual lathes are expertly designed for easy adjustment, ensuring more accurate tool alignment. Different series of manual metal lathes are equipped with three-jaw chucks, four-jaw chucks, and square tool posts, with additional configurations available.
Setting Speed and Feed: Set the appropriate spindle speed based on the workpiece material and machining requirements. Using the manual feed handle, smoothly bring the tool close to the workpiece to start the cutting operation. Minnuo lathes feature an efficient transmission system and precise feed mechanism, helping you enhance productivity while ensuring machining quality. We can also provide a maximum speed of 2000 rpm/min.
Precision Machining and Monitoring: During the machining process, pay attention to the cutting depth of the tool and maintain a consistent feed rate while constantly monitoring the surface quality of the workpiece. Our manual lathes are known for their exceptional stability and high precision, allowing you to easily complete complex machining tasks.
Inspection and Cleaning: After machining, use measuring tools to thoroughly inspect the workpiece, ensuring that its dimensions and surface quality meet the required standards. Then, clean the lathe and prepare for the next operation. Minnuo’s manual lathes are easy to maintain and highly durable, saving you time and costs.
By choosing Minnuo’s manual lathes, you not only get high-performance machining equipment but also benefit from our top-notch after-sales support, making each operation smoother and more efficient.
How We Support You Before Your Purchase Decision ?
Technical Support
Our team provides comprehensive technical support tailored to your machining needs. We offer the best solutions and recommendations to help you optimize your production processes and increase efficiency.
Quick Response
Our sales team is committed to responding to your inquiries within 24 hours. We promptly address your questions and concerns to ensure you have all the information you need.
Customized Solutions
We offer customized product configurations and solutions based on your specific requirements. Whether you need special attachments, software, or unique configurations, we are here to meet your specific machining needs.
Professionalism and Integrity
With years of industry experience, our professional team is dedicated to providing you with the highest quality pre-sales service. We uphold the values of professionalism and integrity, ensuring you receive reliable and trustworthy support.
Why Choose MINNUO Machine Tools ?
Minnuo Group Co., Ltd. has established two modern industrial bases covering an area of 200,000 square meters.These bases focus on the research, development, and manufacturing of CNC machine tools, flexible manufacturing systems, automated complete sets of technology and equipment, as well as the industrialization of functional components. The current equipment inventory comprises nearly 2500 units of equipment, including “primary, large, precision, and rare” categories, along with over 80 effective patents. The company serves over 100 countries and regions globally in industries such as automobiles, rail transit, construction machinery, oil machinery, mining and metallurgy, communication equipment, and vocational education, providing high-quality products, services, and comprehensive solutions.
Our Manufacturing Process and Quality Control
- 1. Rigorous Quality Checks at Every Stage
- 2. State-of-the-Art Manufacturing Facilities
- 3. Skilled Technicians and Engineers
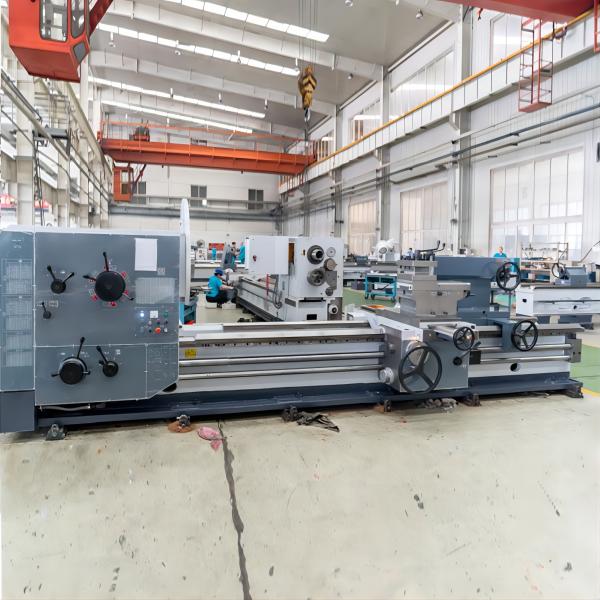