5-Axis Machining is a mode of CNC machining that enables a machine tool to move a part or a tool on five different axes simultaneously, thereby facilitating complex shapes, angles, and finishes to be machined in a single setup.
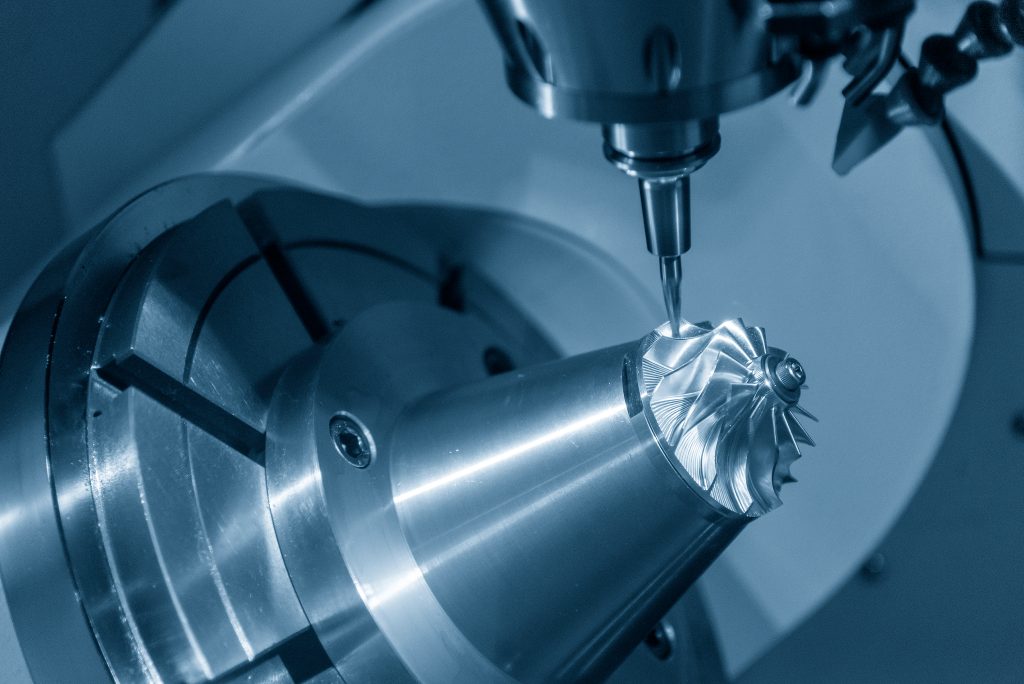
The Origins of 5-Axis Machining
The concept of 5-axis machining dates back to the 1960s when the need for complex and precise manufacturing became apparent in industries like aerospace and automotive. The 5-axis methodology offered a solution, extending upon the traditional 3-axis system (X, Y, and Z directions) by including two additional rotational axes (A and B or C). This effectively revolutionized the machining landscape, enabling manufacturers to create complex and intricate parts.
The journey from initial concept to industry standard was anything but straightforward. Early 5-axis machines faced limitations like technical complexity and high costs, restricting their adoption to only large-scale industries. However, with continual improvements in technology and software capabilities, the prowess of 5-axis machining reached smaller companies. Today, robust design, efficient performance, and streamlining of production processes have entrenched 5-axis machining as the go-to technology for precision manufacturing across diverse sectors.
How Does 5-Axis Machining Work?
At the core of 5-axis machining lie five different planes of movement: three linear axes (known as X, Y, and Z) and two rotational axes (referred to as A, B, or C depending on their orientation). These axes provide the ability to cut parts from multiple angles and directions in a single setup, which subsequently leads to complex geometries and better precision jobs.
Understandably, managing all five axes simultaneously requires advanced controlling software that works in tandem with the hardware. Most commonly, this takes the form of computer-aided design (CAD) or computer-aided manufacturing (CAM) software.
The process unfolds in the following manner:
- Design and Simulation: Initially, a design is made using CAD software. This design is then fed into CAM software, which simulates the cutting process and generates a program for the CNC machine controller. The program includes not only the path that the cutting tool will follow, but also the speed at which the tool will move, and any rotation of the part or tool involved in the process.
- Toolpath and G-Code Generation: This step involves converting the CAD model into a series of instructions, known as G-code, for the machine to follow. The software calculates the movements needed on all five axes to ensure optimal cutting paths and to prevent any collisions between the tool and the workpiece.
- Machine Initiation: The CNC machine reads the G-code instructions which direct the motion of the machine tool. Through these instructions, each axis of the machine is controlled independently but synchronously, permitting the desired paths and angles to be achieved. The cutting tool will then start to perform the machining tasks on the workpiece.
- Monitoring and Adjustments: As the machine operates, it also continuously monitors the position of the cutting tool in relation to the workpiece. This allows the fine control needed for precise machining tasks. The software can make real-time adjustments if needed, further ensuring accuracy and quality of the parts created.
5-axis machining achieves what would be either impossible or extremely time-consuming on 3 or even 4-axis machines. It enables not only the creation of extremely complex shapes, but it also reduces tool changes and setup time, leading to shorter lead times and increased efficiency.
3+2 vs Simultaneous 5-Axis
When we delve into the world of 5-axis machining, two concepts often crop up: 3+2-axis machining and simultaneous 5-axis machining. While there may be a shared foundation, the two methodologies are markedly different in their approach and use cases.
3+2-Axis Machining:
Fundamentally, 3+2-axis machining – also referred to as positional or indexed 5-axis machining – operates by statically positioning the workpiece using the rotational axes and then engages in machining using the traditional three linear axes. This results in an efficient, adaptable process that is less prone to inconsistencies or errors.
- Advantages: Relative simplicity offers cost savings on machine purchase and maintenance. Lower skill requirements for programmers and operators.
- Limitations: Limited in dealing with complex surfaces as the tool can’t adjust the angle in real-time.
Simultaneous 5-Axis Machining:
On the other hand, simultaneous 5-axis machining utilizes all five axes concurrently. The cutting tool or workpiece moves across the linear axes, while the rotational axes adjust simultaneously. This quintessential “dance” enables highly complex geometries, better finishes, and superior accuracy.
- Advantages: Ideal for highly intricate or organic shapes, often needed in industries like aerospace or healthcare. It reduces time by eliminating the need for multiple setups.
- Limitations: Greater physical complexity and cost. Requires more advanced programming and higher operator skills.
Is 5-Axis Machining Right for Your Business?
Deciding if 5-axis machining is right for your business involves considering several factors. Operating on five planes of motion, it delivers great versatility and precision, but it also comes with complexities and cost considerations. Below are key points to contemplate.
- Part Complexity: If you largely produce parts with intricate geometries, undercuts, or organic shapes, upgrading to a 5-axis milling machine provides significant benefits.
- Production Efficiency: With fewer setups and tools needed, 5-axis machining reduces production time and error rate.
- Cost & ROI: While the initial cost of a 5-axis milling machine, its operation, and the necessary training are sizable, returns can be substantial when treated as a long-term investment.
- Skills & Training: Lastly, the complexity of 5-axis CNC machining demands specialized software knowledge and operating skills. You might need to hire experts or train existing employees, imposing additional costs and preparation time.
Ultimately, the decision must balance the potential of 5-axis machining against your operational and financial reality.
Optimal Utilization of 5-Axis Machines
Extracting maximum benefits from your 5-axis machines requires strategic planning and intelligent use of the tools at your disposal. Here are some tips and tricks for optimal utilization.
- Part Programming: An intricate part of 5-axis machining is the software programming. Ensuring you use optimal tool paths and advanced CAM software capable of high-quality 5-axis programming is key.
- Tool Selection: Align your selection to the needs of specific projects. Using streamlined tools, like ball nose end mills, for complex profiling can improve surface finish and tool life.
- Training: Continuous education and training of machine operators enhance their proficiency with the equipment. Encourage them to stay updated about technological advancements.
- Maintenance: Regular checkups and maintenance of the machining center increase the machinery lifespan. Ensuring that all five axes are well-calibrated to preserve precision is vital.
- Managing Speed: Adjusting feed rates and spindle speed appropriately can significantly reduce tool wear, increase efficiency, and enhance part quality.
- Test Runs: Evaluating new strategies in a controlled environment using test runs helps to streamline operations. Making small adjustments based on these tests avoids costly errors during full-scale production.
Different 5-Axis Machines
Understanding different types of 5-axis machines is imperative to select the most suitable option for your needs. Here is a brief synopsis of various popular types.
- 5-Axis Vertical Machining Center: In this type, the spindle moves up and down vertically, providing z-axis movement, while the table moves on the x and y axes. Two rotational axes enable the table to tilt and rotate, allowing work on all five sides of a part without repositioning.
- 5-Axis Horizontal Machining Center: Here, the spindle operates horizontally, and the table moves in the x, y, and one rotational (B or C) axis, allowing the machine to reach five sides of a workpiece. An additional rotary axis on the table provides the fifth axis, often making these machines more efficient for bulkier parts.
- Multitasking (Mill-Turn) Machines: These machines combine milling and turning operations. They offer a high degree of flexibility, executing both tasks in one setup. They can machine complex parts much faster, reducing production time dramatically.
- Trunnion-Style Machines: In these machines, the entire workpiece rotates instead of the head, offering better rigidity and accuracy during machining. Trunnion machines typically have better structural rigidity, making them suitable for heavy-duty jobs.
- Swivel-Head Machines: These machines have a head that can tilt and rotate to offer the B and C axes. The stationary table provides the conventional X, Y, and Z movements.
Our 5-Axis Machines
Choose Minnuo Machine for premium 5-axis machining solutions. Our machines balance top speeds, commendable precision, and efficient tool management, while being compatible with leading CAM software for faultless part programming. Embrace our advanced tooling capabilities to elevate your multi-material machining, supported by comprehensive training from industry experts.