Imagine standing before a machine so powerful and precise that it can shape massive blocks of metal into intricate components for aircraft or heavy machinery. This is the realm of the bridge mill, a workhorse in modern manufacturing.
Bridge mill, also known as a bridge milling machine, is a versatile and powerful machining tool specifically designed for working on large and heavy workpieces. Distinguished by its rigid bridge structure, it ensures precision, stability, and efficiency in various industrial applications.
The article will give you the definition, structure, advantages of bridge milling machine in comparison with other machine tools and show you how to choose the right machine for you.
What is Bridge Mill?
A bridge mill, is a type of machining tool characterized by its bridge-like structure that spans over the workpiece. The bridge mill is specifically designed for working on large and heavy workpieces, offering both vertical and horizontal machining capabilities. The key feature of a bridge mill is its rigid bridge, which ensures exceptional stability and precision during the machining process. This makes bridge mills ideal for industries that require machining of large-scale components with high accuracy, such as aerospace, automotive, energy, and heavy machinery sectors.
Bridge mills differ from other milling machines, such as gantry mills and vertical machining centers (VMCs), in their ability to handle extremely large workpieces while maintaining high levels of precision. They can accommodate multi-axis machining, making them versatile and efficient for complex operations. Whether you’re machining massive components for aerospace or delicate parts for the automotive industry, bridge mills offer the scalability and accuracy needed for the task.
Basic Components
The fundamental design of a bridge mill centers around several key components that work in harmony to provide its renowned stability and precision. These components include:
- Bridge Structure: The heart of the machine, providing unparalleled rigidity.
- Spindle Head: The tool’s powerhouse, moving along the bridge to machine workpieces with precision.
- Worktable: Capable of supporting massive components, ensuring stability during operations.
- Tool Magazine: Allows for automated tool changes, enhancing efficiency.
Types of Bridge Mills
Not all bridge mills are created equal. There are variations in design that cater to different machining needs. Let’s explore the different types and how they are tailored to various industrial applications.
- Fixed Bridge: The bridge remains stationary while the worktable moves. This design offers maximum stability, making it ideal for high-precision tasks.
- Moving Bridge: In contrast, the bridge itself moves, providing greater flexibility, especially for larger or longer workpieces. This type might sacrifice some stability for versatility.
Size and Capacity Considerations
The size and capacity of a bridge mill are crucial factors when choosing the right machine for your needs. Bridge mills come in various sizes, with some capable of handling workpieces weighing several tons. The size you choose depends on the specific requirements of your industry, whether you’re producing large aerospace components or precision automotive parts.
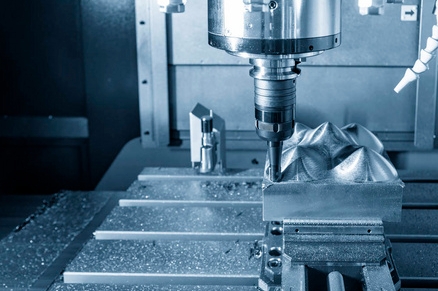
Operational Capabilities
While the design of a bridge mill is fundamental, its operational capabilities are where it truly shines. Let’s delve into how these machines perform in real-world scenarios.
Multi-Axis Machining
Bridge mills often operate with 3 to 5 axes, allowing for complex shapes to be machined in a single setup. This capability is crucial for industries where precision is non-negotiable, such as aerospace and automotive manufacturing.
Precision and Accuracy
Precision and accuracy are the hallmarks of any great machining tool, and bridge mills are no exception. Imagine crafting a jet engine component where even a tiny deviation could mean the difference between success and failure. Bridge mills ensure such precision through their rigid structure and advanced CNC controls.
Speed and Efficiency
In today’s fast-paced manufacturing environment, speed and efficiency are key. Bridge mills are designed to meet these demands without compromising on quality. With high-speed machining features, bridge mills can significantly reduce production time without compromising accuracy. This efficiency is essential for maintaining competitiveness in industries like automotive manufacturing, where time-to-market is critical.
Applications of Bridge Mills
The versatility of bridge mills allows them to be used across a wide range of industries. Let’s take a closer look at where these machines truly excel.
Industries Using Bridge Mills
- Aerospace: Machining large, complex components with high precision.
- Automotive: High-precision parts production where consistency is key.
- Energy: Manufacturing components like wind turbine blades, where both size and precision are critical.
- Heavy Machinery: Large-scale equipment manufacturing that requires robust and stable machining solutions.
Material Capabilities
Bridge mills can handle a variety of materials, from lightweight composites to heavy metals like steel and titanium, making them versatile tools in any manufacturing setup.
Advantages of Bridge Mills
The advantages of bridge mills become even more apparent when considering their application across different industries. Let’s explore what sets them apart.
High Structural Rigidity
The bridge design ensures that even under heavy loads, the machine remains stable, resulting in precise machining.
Large Work Envelope
Bridge mills are capable of machining large workpieces in one setup, reducing the need for multiple operations and increasing efficiency.
Flexibility and Versatility
These machines are not limited to milling; they can also handle drilling, boring, and other operations, making them a versatile addition to any manufacturing setup.
Improved Throughput and Productivity
Automation features like tool changers and multi-axis machining allow for faster, more efficient production runs.
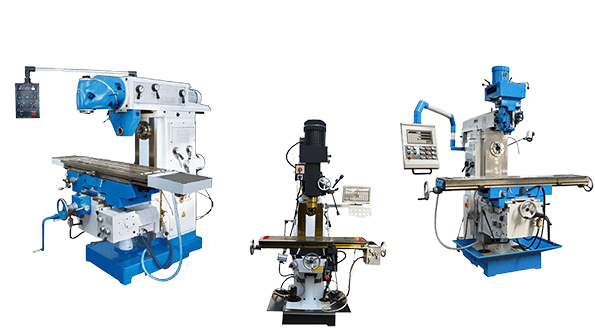
Comparisons with Other Milling Machines
To truly understand the value of a bridge mill, it’s important to compare it with other types of milling machines. Here’s how bridge mills stack up against their counterparts.
Bridge Mill vs. Gantry Mill
- Bridge Mill: Offers more rigidity due to its fixed structure, making it ideal for precision work.
- Gantry Mill: Typically has a moving gantry, offering more flexibility for very large workpieces but may lack the same level of precision.
If your priority is precision and stability, especially for complex, detailed work, a bridge mill is the better option. However, if your tasks involve very large parts with less stringent accuracy requirements, a gantry mill might be more appropriate.
Bridge Mill vs. Vertical Machining Center (VMC)
- Bridge Mill: Best for large, heavy-duty machining tasks requiring high precision and the ability to work on massive workpieces.
- VMC: More suitable for smaller, high-precision workpieces but limited by its work envelope.
Choose a bridge mill for larger projects where workpiece size and machine rigidity are crucial. Opt for a VMC if your focus is on smaller, high-speed, high-precision operations.
Bridge Mill vs. Double Column Milling Machine
- Bridge Mill: Generally more compact with a single bridge structure, making it versatile for a wide range of applications, including those that require flexibility.
- Double Column Milling Machine: Designed for even larger workpieces, offering maximum stability for heavy-duty applications but often at the expense of flexibility and space efficiency.
If you need a balance between a large work envelope and machine versatility, a bridge mill is ideal. For extremely large-scale or highly demanding tasks, a double column milling machine might be more suitable, though it comes with higher costs and space requirements.
Considerations for Selecting a Bridge Mill
Choosing the right bridge mill requires careful consideration of various factors, especially when comparing it with other milling machines. Let’s break down what you should keep in mind to make the best choice.
- Assessing Your Machining Needs
Imagine choosing a machine that fits your production needs perfectly, ensuring you don’t pay for capabilities you’ll never use.
- Budget and Cost Factors
Consider both the initial investment and long-term operating costs, including maintenance and energy consumption.
- Brand and Manufacturer Reputation
Opt for manufacturers known for reliability and robust customer support, as this can significantly impact your machine’s uptime and efficiency.
- Future-Proofing
Ensure that the bridge mill you choose can adapt to future production needs, either through upgrades or retrofitting.
Latest Trends and Innovations in Bridge Mills
As technology evolves, so do bridge mills. Let’s look at the latest trends that are shaping the future of these powerful machines and how they compare to other milling technologies.
Integration of Industry 4.0 Technologies: Smart machining systems with IoT connectivity are becoming standard, allowing for real-time monitoring and predictive maintenance.
Advances in CNC Control Systems: User-friendly interfaces and enhanced simulation capabilities are making these machines easier to operate and program, even for complex tasks.
Sustainable Manufacturing Practices: Modern bridge mills are designed with energy efficiency in mind, reducing the overall environmental impact of your manufacturing operations.
Automation and Robotics: Robotic arms for tool changing and automated workpiece handling are increasingly being integrated, further enhancing productivity.
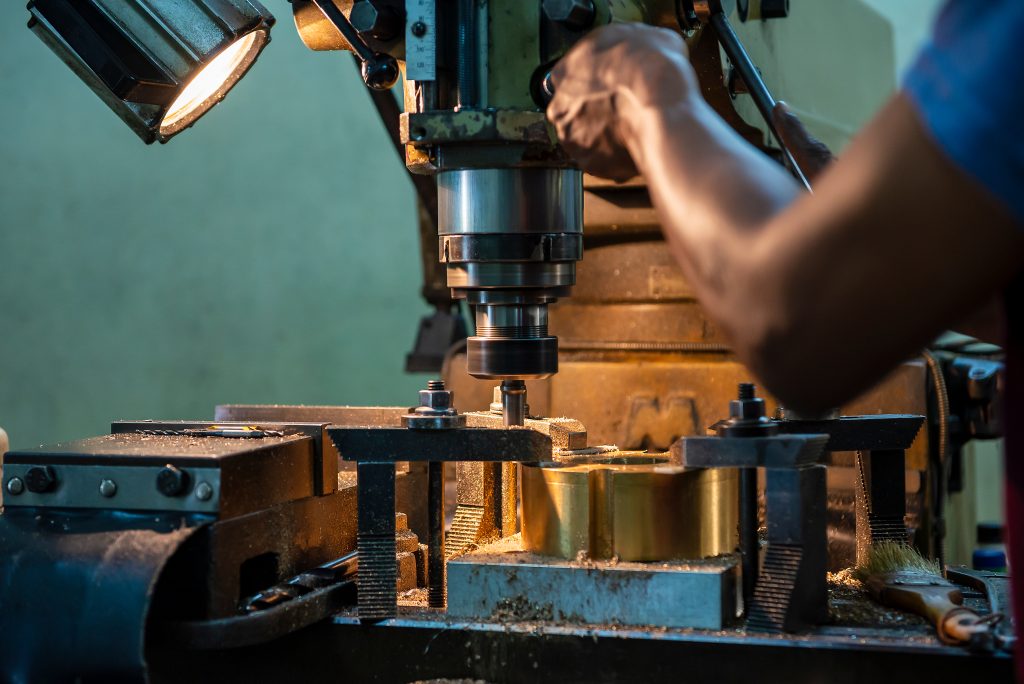
Challenges and Limitations
While bridge mills offer many advantages, they are not without their challenges. Let’s explore these limitations and see how they compare with those of other milling machines.
- Initial Investment Costs
While bridge mills are a significant investment, the long-term benefits often outweigh the upfront costs.
- Space Requirements
These machines require substantial floor space, which might be a limiting factor for smaller workshops.
- Maintenance and Technical Expertise
Operating and maintaining a bridge mill requires skilled personnel, making training and expertise crucial for maximizing its potential.
Conclusion
As we wrap up, it’s clear that bridge mills stand out in many aspects, but it’s essential to consider how they fit within the broader landscape of milling machines. As manufacturing continues to evolve, bridge mills will likely see further integration with smart technologies, making them even more efficient and versatile.
Consider your specific machining needs, budget, and future growth when selecting a bridge mill, and ensure you choose a machine that can grow with your business.
FAQs
Can a bridge mill handle high-precision tasks?
Yes, bridge mills are designed for high precision, making them ideal for tasks where accuracy is critical.
Is a bridge mill worth the investment?
If your production involves large, complex workpieces and you require high precision, the investment in a bridge mill can lead to significant efficiency gains and a high return on investment over time.
What are the alternatives to a bridge mill?
Alternatives include gantry mills, vertical machining centers, and double column milling machines, each suited to different types of workpieces and machining needs.