In the realm of CNC (Computer Numerical Control) machining, understanding the distinctions between CNC milling, CNC turning, and CNC mill-turn technologies is essential for optimizing production and achieving high-quality results. Each technology offers unique advantages and is suited to different types of machining tasks.
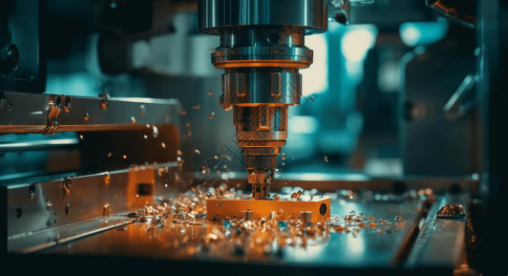
CNC Milling involves cutting material from a workpiece using a rotating tool controlled by a CNC system. This process is ideal for creating complex shapes and precision components. CNC Turning is a subtractive manufacturing process where a rotating workpiece is cut by a stationary CNC-controlled tool, commonly used for cylindrical parts. However,CNC Mill-Turn integrates both CNC milling and CNC turning operations in a single machine, offering versatility and efficiency for complex parts that require both processes.
This guide will delve into these CNC technologies, comparing their capabilities, advantages, and best-use scenarios, helping you make an informed decision for your CNC machining needs.
CNC Milling vs. CNC Turning
Basic Definitions and Principles
- CNC Milling: In CNC milling, the cutting tool rotates and moves across the surface of the workpiece, removing material to create flat or complex shapes. CNC milling machines can be vertical, horizontal, or universal, each offering distinct advantages depending on the application.
- CNC Turning: CNC turning involves rotating a cylindrical workpiece against a stationary cutting tool controlled by a CNC system to remove material. This process is typically performed on a CNC lathe and is ideal for producing cylindrical parts with high precision.
Operational Characteristics
CNC Milling: Can produce a variety of shapes including slots, pockets, and complex geometries. It requires precise CNC setup and tooling adjustments. CNC milling machines are versatile and can handle both soft and hard materials effectively.
CNC Turning: Best suited for producing parts with rotational symmetry. It generally requires simpler setups compared to CNC milling but is limited to cylindrical or conical shapes.
Performance Comparison
Precision and Surface Finish:
CNC milling typically provides superior surface finish and precision for complex shapes, while CNC turning excels in producing smooth, cylindrical surfaces.
Efficiency and Speed:
CNC mill-turn machines offer reduced setup times and increased productivity by performing both milling and turning operations in one machine.
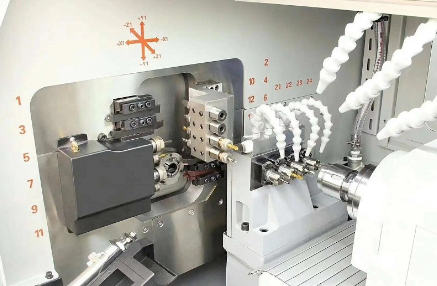
Material Removal Rates:
CNC milling can remove material at higher rates when dealing with complex geometries, while CNC turning is often more efficient for high-volume production of cylindrical parts.
Advantages and Disadvantages
CNC Milling: Offers flexibility and precision but can be more costly and time-consuming for setup and tooling.
CNC Turning: More cost-effective for cylindrical parts but lacks versatility for complex shapes.
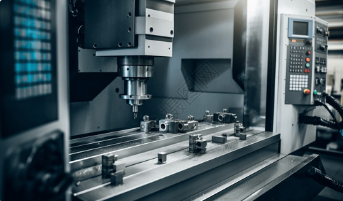
Applications
CNC Milling: Ideal for producing intricate components, including parts with multiple faces and geometric features.
CNC Turning: Best for parts such as shafts, pins, and other cylindrical components.
Comparative Analysis
Overall Performance speed and Accuracy: CNC mill-turn machines generally offer superior speed and accuracy for complex parts compared to traditional CNC milling and CNC turning.
Cost Considerations: CNC milling and CNC turning operations may have lower initial costs, but CNC mill-turn machines can be more cost-effective in the long run by reducing setup times and handling.
Flexibility and Versatility
CNC Milling and CNC Turning: Offer flexibility in different applications but may require multiple CNC machines and setups.
CNC Mill-Turn: Provides the most flexibility by combining both processes in one machine.
Setup and Maintenance
CNC Milling and CNC Turning: May involve more setup time and maintenance with separate machines.
CNC Mill-Turn: Simplifies setup and reduces maintenance by integrating multiple functions into one CNC machine.
Future Trends and Innovations
Advancements in CNC Milling and CNC Turning Technologies:
Continuous improvements in CNC technologies are enhancing precision and automation.
Emerging Trends in CNC Mill-Turn Technology:
Advances in multi-axis CNC machines and software are making CNC mill-turn technology more accessible and efficient.
Impact of Industry 4.0 and Automation:
Integration of smart technologies and automation is transforming traditional CNC machining processes and increasing efficiency.
Conclusion
In summary, CNC milling, CNC turning, and CNC mill-turn technologies each offer distinct advantages and are suited to different applications. CNC milling provides precision for complex shapes, CNC turning is efficient for cylindrical parts, and CNC mill-turn machines offer versatility and efficiency for parts requiring both processes. Evaluating your specific CNC machining needs will guide you in selecting the most appropriate technology.
Minnuo, as a professional industrial master machine manufacturer, we provide lathe, milling machine and multifunctional mill-turn machining centre. Our products are based on standardised, modular, series design concepts and developed multi-functional machine tools, which can achieve 5-axis, 7-axis, 9-axis and other multi-axis complex machining, and truly achieve the ability to integrate functions of a single machine, multi-process, multi-process machining. Choose us to add power to your precision machining!
FAQs
Q1: What is the primary difference between CNC milling and CNC turning?
A1: CNC milling involves rotating a cutting tool to remove material from a stationary workpiece, ideal for complex shapes. CNC turning involves rotating the workpiece against a stationary CNC-controlled tool to create cylindrical parts.
Q2: How does a CNC mill-turn machine improve efficiency compared to separate CNC milling and CNC turning operations?
A2: CNC mill-turn machines integrate both CNC milling and CNC turning processes into a single setup, reducing setup times, handling, and increasing overall productivity.
Q3: What are the key advantages of using a CNC mill-turn machine?
A3: CNC mill-turn machines offer enhanced versatility, reduced setup time, and the ability to perform complex machining tasks in a single CNC setup, which can lead to increased efficiency and precision.
Q4: Are CNC mill-turn machines suitable for all types of machining tasks.
A4:CNC mill-turn machines are particularly useful for complex parts that require both CNC milling and CNC turning operations. For simpler cylindrical parts or large-volume production, traditional CNC turning or CNC milling machines may be more cost-effective.
Q5: How does the cost of CNC mill-turn technology compare to traditional CNC milling and CNC turning?
A5: While CNC mill-turn machines generally have a higher initial investment, they can be more cost-effective over time due to reduced setup times and handling, making them a good investment for complex or high-precision parts.
Feature | CNC Milling | CNC Turning | CNC Mill-Turn |
Basic Operation | Rotating tool cuts stationary workpiece | Rotating workpiece cut by stationary tool | Integrates both milling and turning operations |
Best For | Complex shapes, multiple faces | Cylindrical parts, rotational symmetry | Complex parts needing both milling and turning |
Machine Types | Vertical, horizontal, universal milling machines | CNC lathes | Multi-axis CNC machines |
Complexity of Setup | High setup complexity for multiple operations | Simple setup for cylindrical parts | Combined setup for both milling and turning |
Material Removal Rate | High for complex geometriesintricate details | Efficient for cylindrical parts | Efficient for complex parts |
Surface Finish | High precision for intricate details | Smooth cylindrical surfaces | High precision across multiple operations |
Flexibility | High, but requires separate machines for different operations | Limited to cylindrical shapes | Very high, handles both operations in one machine |
Cost Considerations | Moderate, higher for complex setups | Generally lower for simple operations | Higher initial cost, potentially lower overall cost due to reduced handling |
Typical Applications | Aerospace, automotive, and intricate components | Shafts, pins, and other cylindrical components | Aerospace, automotive, and complex mechanical parts |
Setup and Maintenance | More time-consuming with separate machines | Simpler setup, less maintenance | Streamlined setup and reduced maintenance |
Efficiency | Lower for parts requiring both milling and turning | High for cylindrical parts | High for complex parts requiring both processes |