In today’s fast-paced manufacturing landscape, the choice between Electrical Discharge Machining (EDM) and conventional machining plays a critical role in meeting production demands.
When comparing EDM and conventional machining, it’s essential to understand that EDM is ideal for creating complex geometries and working with hard materials, while conventional methods are typically faster and more versatile for straightforward tasks. Conventional machining includes familiar processes like turning, milling, and drilling, EDM offers a revolutionary approach that utilizes electrical discharges to shape materials with remarkable precision.
What is Conventional Machining
Conventional Machining: This traditional method encompasses various processes such as turning, milling, and drilling, where material is physically cut away using sharp tools. The effectiveness of conventional machining relies on the sharpness of the tools and the physical properties of the workpiece. As advancements in CNC technology continue to evolve, conventional machining has gained enhanced precision, allowing for automated operations that increase productivity.
What is EDM (Electrical Discharge Machining)
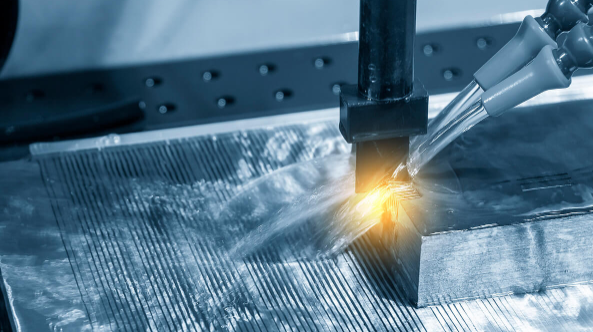
EDM (Electrical Discharge Machining): A non-traditional machining process that uses controlled electrical discharges to remove material. This technique is particularly effective for hard materials and complex shapes, utilizing two electrodes—one as the tool and the other as the workpiece. EDM operates by generating rapid, high-voltage electrical discharges, which create a controlled erosion effect, allowing for precise material removal. This unique capability makes EDM indispensable in high-tech industries where intricate features are critical.
Comparison of Key Features
To effectively evaluate EDM and conventional machining, it’s essential to consider several key features that impact their applications, efficiency, and suitability for various tasks. Below, we delve into specific characteristics that differentiate these two methods.
Material Compatibility:
- Conventional Machining: This method is versatile for a broad range of materials, including aluminum and mild steel. However, it faces challenges with harder materials, leading to increased tool wear. The adaptability of conventional machining makes it a preferred choice for many manufacturing tasks where material properties are manageable.
Precision and Tolerance:
- EDM offers unmatched precision, achieving tolerances as tight as ±0.005 mm. This level of accuracy is critical for applications requiring high performance and reliability.
Surface Finish:
- The surface finish produced by EDM is superior, often requiring no additional polishing. This characteristic significantly reduces post-processing time and enhances the quality of the final product.
- Conventional methods, on the other hand, can produce rough finishes that may necessitate further refinement, adding time and cost to the overall manufacturing process.
Machining Speed and Efficiency:
- Conventional machining is generally faster, particularly for simple shapes. This speed is advantageous in high-volume production settings, where efficiency is paramount.
- However, EDM can be more efficient for complex designs, despite its slower rate of material removal. The unique capabilities of EDM justify the time investment when intricate features are required.
Setup and Tooling Costs:
- Conventional machining typically has lower initial costs but may incur higher tool wear, which can affect long-term profitability.
- EDM, while initially more expensive due to custom electrode manufacturing, experiences minimal wear during operation. This can lead to reduced long-term costs, especially for projects requiring complex designs.
Applications
Understanding the applications of each machining method helps to clarify their unique advantages and where they excel in meeting industry needs. Below, we explore the primary uses of both conventional machining and EDM.
- Conventional Machining: Widely utilized across various industries, such as automotive and consumer goods, for producing parts like shafts, gears, and housings. The adaptability of conventional machining makes it a go-to for high-volume production runs. Its ability to work with a variety of materials and produce straightforward shapes efficiently solidifies its role in traditional manufacturing.
- EDM: Predominantly found in high-precision industries like aerospace and medical, EDM is utilized for producing intricate components such as molds, dies, and parts with complex geometries. Its ability to create detailed features makes it indispensable for specialized applications where traditional methods might struggle to deliver the required precision.
Advantages and Disadvantages
As we navigate the strengths and weaknesses of both machining methods, it’s essential to weigh the advantages and disadvantages to determine the best fit for specific manufacturing needs.
Conventional Machining
- Pros: Fast, versatile, and cost-effective for large production runs, making it suitable for a wide range of applications. Its familiarity among machinists also aids in faster setup times and operational efficiency.
- Cons: Limited by tool wear and the inability to effectively machine hard materials or complex shapes, which can constrain its application in specialized industries.
EDM
- Pros: Excellent for producing complex shapes and features with minimal tool wear. It is particularly capable of machining hard materials that pose challenges for conventional methods, opening doors for innovation in product design.
- Cons: Slower than conventional methods and typically involves higher operational costs, which can deter its use for simpler tasks where speed is critical.
Future Trends in Machining Technologies
As industries continue to innovate, EDM technology is incorporating automation and advanced software to enhance efficiency and precision. Innovations like real-time monitoring and adaptive control are being integrated, allowing for optimized machining processes. Concurrently, advancements in CNC technology are pushing conventional machining toward increased automation and flexibility, ensuring both methods remain relevant in a rapidly changing manufacturing landscape.
Conclusion
In the debate between EDM and conventional machining, the optimal choice hinges on specific project requirements. EDM stands out for its precision and capability to handle intricate designs, while conventional machining remains a robust option for speed and versatility. Understanding these differences is crucial for making informed decisions in manufacturing and optimizing production processes.
FAQs
1. What is EDM machining used for?
EDM is commonly used for creating complex shapes and intricate designs, particularly in high-tech industries such as aerospace and medical.
2. How does EDM compare to traditional machining?
EDM excels in precision and material versatility, especially for hard materials, while traditional machining is faster and more versatile for straightforward tasks.
3. What materials can EDM machine?
EDM is effective for hard metals like titanium, tool steel, and carbides, making it ideal for specialized applications where conventional methods struggle.
4. Is EDM more expensive than conventional machining?
Generally, yes. While EDM incurs higher setup costs, its precision and ability to handle complex designs can justify the expense in specific applications.
5. Can EDM produce a smooth surface finish?
Yes, EDM can achieve an excellent surface finish, often eliminating the need for further polishing, thus saving time and cost in finishing processes.