When it comes to precision and efficiency in various technical and industrial applications, understanding the difference between grinders and sanders is crucial. Both tools are essential in material processing, yet they serve distinct purposes and excel in different scenarios.
Grinders and sanders are both crucial for material processing but serve different purposes. Grinders are designed for heavy-duty material removal and shaping, utilizing abrasive wheels to work at high speeds. Sanders, on the other hand, are ideal for achieving smooth finishes and preparing surfaces, using abrasive pads or belts with variable speeds. While grinders are commonly used in metalworking for tasks like sharpening and shaping, sanders are preferred in woodworking and finishing applications for their ability to provide a smooth, even surface.
What is Grinder?
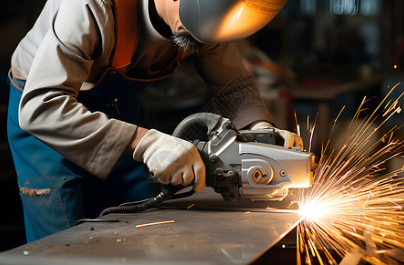
Grinders: These tools use abrasive wheels to remove material quickly. Types include bench grinders, angle grinders, and die grinders. Bench grinders are stationary and ideal for sharpening tools, while angle grinders are versatile, used for cutting and grinding metal. Die grinders, often used in precision work, are suitable for detailed grinding tasks.
What is Sander?
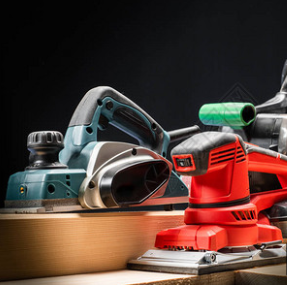
Sanders: Sanders use abrasive pads or belts to smooth surfaces. Types include orbital sanders, belt sanders, and detail sanders. Orbital sanders are versatile, suitable for general sanding tasks, while belt sanders are effective for rapid material removal. Detail sanders are designed for precision in tight or intricate spaces.
Tools Comparison
With a clear understanding of what each tool does, we can now compare them in various aspects to highlight their respective strengths and weaknesses. This comparison will help clarify which tool might be more suitable for specific tasks based on functionality, material compatibility, and precision.
Functionality:
- – Grinders: Best for heavy material removal, shaping, and sharpening. Ideal for tasks requiring significant material alteration.
- – Sanders: Perfect for surface finishing and smoothing. Excellent for preparing surfaces for painting or varnishing.
Material Compatibility:
- – Grinders: Effective on metals, plastics, and composites. Used extensively in metalworking.
- – Sanders: Typically used on wood, but also applicable to metals and plastics. Preferred for finishing wooden surfaces.
Precision and Control:
- – Grinders: High precision for detailed work, but can be aggressive. Suitable for tasks requiring precise shaping or sharpening.
- – Sanders: Provides a smooth finish with less aggressive material removal. Ideal for final surface preparation.
Key Features and Specifications
Transitioning from a comparison of the general functionalities, it’s important to dive into the specific features and specifications that differentiate grinders from sanders. This section will cover the unique characteristics of each tool, helping you understand their performance attributes and practical benefits.
Grinders:
- – Abrasive Wheels: Vary in type and grit size, essential for different grinding tasks.
- – Speed and Power: Typically high RPM, ranging from 3,000 to 10,000 RPM. More power allows for quicker material removal.
- – Safety: Includes features like guards and shields to protect against sparks and debris.
Sanders:
- – Abrasive Pads: Come in various grits and types, suitable for different finishing tasks.
- – Speed Settings: Variable speeds allow for control over the sanding process.
- – Dust Collection: Many sanders include built-in dust collection systems to maintain a clean work area.
Advantages and Disadvantages
Now that we’ve examined the key features of grinders and sanders, it’s important to consider their respective advantages and disadvantages. This will provide a balanced view of each tool’s strengths and limitations, guiding you in making the best choice for your specific needs.
Grinders:
- – Advantages: Efficient in material removal, versatile for various applications.
- – Disadvantages: Can cause overheating, high noise levels, and requires careful handling.
Sanders:
- – Advantages: Produces smooth finishes, generally easier to use for surface preparation.
- – Disadvantages: Slower material removal, may clog with dust or debris.
Applications in Industry
With a solid understanding of the advantages and disadvantages, it’s useful to explore how grinders and sanders are applied in different industries. This section will illustrate real-world scenarios where each tool excels, providing practical insights into their uses.
- – Manufacturing: Grinders are used for precise material shaping and sharpening tools, while sanders are employed for surface finishing and preparation.
- – Automotive: Grinders are utilized for metal repairs and modifications, whereas sanders are used for bodywork and painting preparation.
- – Woodworking: Sanders are essential for achieving a smooth, professional finish on wooden projects, while grinders are less commonly used.
- – Metalworking: Grinders excel in tasks like deburring and sharpening, whereas sanders are used for polishing and fine finishing.
Maintenance and Care
After understanding how each tool is used across various applications, maintaining and caring for them is crucial to ensure longevity and performance. Proper maintenance practices can extend the life of your tools and enhance their efficiency.
Grinders:
- – Regularly check and replace grinding wheels as needed.
- – Ensure proper alignment and maintenance to prevent overheating.
Sanders:
- – Replace sanding pads or belts when worn.
- – Clean dust filters and ensure dust collection systems are functioning properly.
Choosing the Right Tool
Having explored the maintenance aspects, it’s time to make an informed decision on which tool to choose. Consider the specific job requirements, material types, and desired finishes to determine which tool will best meet your needs.
When selecting between a grinder and a sander, consider the job requirements, material type, and desired finish. For heavy material removal and shaping, a grinder is your best choice. For achieving a smooth, polished surface, a sander is more appropriate. Evaluate the cost vs. benefit for each tool based on your specific needs and applications.
Summary Table
Feature | Grinders | Sanders |
Primary Use | Material removal, shaping, sharpening | Surface finishing, smoothing |
Types | Bench Grinders, Angle Grinders, Die Grinders | Orbital Sanders, Belt Sanders, Detail Sanders |
Mechanism | Abrasive wheels rotate at high speed | Abrasive pads oscillate or move in a belt |
Material Compatibility | Metals, plastics, composites | Wood, metals, plastics |
Precision | High precision for detailed work | Smooth finishes, less precise for removal |
Speed | Typically higher RPM (e.g., 3,000-10,000 RPM) | Variable speed, generally lower RPM |
Abrasive Types | Grinding wheels, discs | Sanding pads, belts |
Finish Quality | Coarse to fine, can be rough | Smooth and even |
Power Source | Electric, pneumatic | Electric, battery-operated |
Dust Management | Minimal dust collection | Often includes dust collection systems |
Safety Considerations | Potential for sparks and overheating | Risk of surface damage if misused |
Typical Applications | Metalworking, sharpening tools, heavy material removal | Woodworking, finishing, preparation for painting |
FAQs
Q1: What is the main difference between a grinder and a sander?
A: The main difference is their function. Grinders are designed for heavy material removal and shaping, while sanders are used for smoothing and finishing surfaces.
Q2: Can I use a sander for metalworking?
A: Yes, sanders can be used for metalworking, but they are typically more effective for finishing rather than heavy material removal.
Q3: How often should I replace the abrasive wheels on a grinder?
A: Abrasive wheels should be replaced when they become worn down, cracked, or damaged. Regular inspection will help determine when replacement is needed.
Q4: Are there any safety precautions I should take when using a grinder?
A: Always use safety guards, wear protective eyewear, and ensure proper ventilation to protect against sparks and debris.
Q5: What type of sander is best for woodworking?
A: Orbital sanders are popular for woodworking due to their versatility and ability to provide a smooth finish. Belt sanders are also used for rapid material removal.
This comprehensive guide should provide you with a solid understanding of grinders and sanders, helping you make informed decisions for your projects and applications.