People use these abrasive wheels to cut, shape, grind, or polish hard materials like metal, ceramics, and stone.Whether you’re smoothing metal surfaces, sharpening tools, or performing precision grinding, grinding wheels are indispensable in providing accuracy and efficiency.
Grinding wheels are abrasive tools made from a variety of materials like aluminum oxide, silicon carbide, and diamond, used primarily to cut, grind, or polish metal and other hard materials. They come in various types, including bonded wheels, cut-off wheels, and diamond wheels, each suitable for different applications in industries such as metalworking, tool and die making, and automotive manufacturing.
What is a Grinding Wheel?
A grinding wheel is a circular tool used for abrasive cutting, grinding, or polishing various materials. The wheel consists of abrasive grains held together by a bonding material, which creates the ability to cut away small pieces of the workpiece. Grinding wheels are used in machines, commonly referred to as wheel grinder machines, to smooth, sharpen, or remove excess material from metal surfaces.
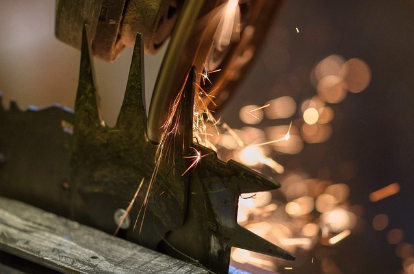
The basic components of a grinding wheel include:
- Abrasive Grains: These act as cutting tools that shear tiny chips from the workpiece during grinding.
- Bond: This holds the grains together and determines the wheel’s strength and rigidity.
- Pores: The empty spaces between grains and bonds that allow for chip clearance and cooling during grinding.
Types of Grinding Wheels
There are many different types of grinding wheels, each designed for specific purposes. Understanding the differences between these types will help you select the right wheel for your particular task. What are the most common types of grinding wheels and their typical applications?
Bonded Wheels:
- Bonded wheels are one of the most widely used types due to their versatility. These wheels are primarily used for general grinding and finishing tasks.
Cut-off Wheels:
- Cut-off wheels are thin and used for making precise cuts, especially in metals. They are essential for applications requiring accuracy, such as cutting metal pipes or sheet metal.
Diamond Wheels:
- Known for their durability and hardness, diamond wheels are designed for cutting hard materials such as stone, ceramics, and glass. They are often used in stone polishing wheels and for fine, detailed work.
Cylindrical and Surface Grinding Wheels:
- These wheels are used for grinding cylindrical surfaces or flat surfaces, providing a high surface finish on various materials.
Grinding Wheel Specifications
Each grinding wheel comes with specific characteristics that determine its best application. Grinding wheel specifications such as grain size, bond type, and wheel thickness play a crucial role in how well a wheel performs for a particular task. Understanding these specifications will help you make the right choice for your needs.
Grain Size
The grain size of a grinding wheel affects how fine or coarse the grinding action will be. Coarser grains are ideal for heavy-duty grinding and removing large amounts of material, while finer grains provide a smooth finish for precision work. Choosing the right grain size ensures you get the best performance for your application.
Bond Type
The bond type determines how the abrasive grains are held together. Different bonds, such as vitrified or resin, have unique properties suited for specific tasks. For example, vitrified bonds are ideal for precision grinding, while resin bonds offer more flexibility for general grinding.
Wheel Thickness
Thicker grinding wheels are more durable and can handle higher loads, making them ideal for heavy-duty applications like grinding steel or iron. Thinner wheels, however, provide greater precision and are commonly used for fine surface finishing tasks.
Hardness and Structure
Hardness refers to the wheel’s ability to resist wear and tear during grinding. A harder wheel will maintain its shape longer, while a softer wheel is more flexible but may wear out faster. The structure of the wheel, which refers to the spacing between abrasive grains, affects the wheel’s cutting action and heat dissipation.
Applications of Grinding Wheels
Grinding wheels have a wide range of applications, depending on the material being worked on and the desired outcome. Whether in metalworking, automotive manufacturing, or tool and die making, grinding wheels are used to shape, finish, or sharpen materials to precise specifications.
Tool and Die Making
In tool and die manufacturing, precision is critical. Grinding wheels are used to create sharp edges and fine surfaces on tools and dies. The wheels help achieve the exact measurements and smoothness required in high-precision applications.
Automotive Industry
In the automotive industry, grinding wheels play a significant role in manufacturing and maintaining parts. They are used for polishing, grinding, and shaping metal parts, ensuring that components fit perfectly and perform efficiently.
Aerospace and Defense
The aerospace and defense industries require parts with high precision and reliability. Grinding wheels, especially those made of abrasive materials like diamond and CBN, are ideal for handling tough materials like titanium and ensuring accuracy in part manufacturing.
What Are Grinding Wheels Used For?
Grinding wheels are used for many purposes, including sharpening tools, cutting metal, finishing surfaces, and shaping hard materials like stone or ceramics. In general, they are essential for removing material and achieving smooth, precise surfaces in various industries.
Selecting the Right Grinding Wheel
Selecting the right grinding wheel is essential for achieving the best results. Several factors must be considered, including the type of material being worked on, the precision required, and the wheel’s specifications. By carefully assessing these factors, you can choose the right grinding wheel for your project.
Factors to Consider
When choosing a grinding wheel, consider the material you’re working on, the type of grinding you need to perform, and the wheel’s grain size and bond type. These factors directly affect the grinding efficiency and quality of the finish.
Common Mistakes to Avoid
One of the most common mistakes when selecting a grinding wheel is using the wrong type for the material. For instance, using a metal grinding wheel on stone or a stone polishing wheel on metal can lead to poor performance and damage to both the workpiece and the wheel.
Advantages and Disadvantages of Grinding Wheels
Like any tool, grinding wheels come with both advantages and disadvantages. Understanding these can help you make better choices when selecting the right wheel for your needs.
Advantages
Grinding wheels offer several key advantages, including high precision, versatility, and the ability to work with a variety of materials. They are especially useful for creating smooth finishes and cutting hard materials that other tools can’t easily handle.
Disadvantages
Despite their benefits, grinding wheels also have some limitations. They wear out over time and need to be regularly maintained. Additionally, improper handling can lead to wheel failure, which can pose safety risks. Moreover, the heat generated during grinding may affect the material being worked on.
Safety Considerations
When using grinding wheels, safety should always be a top priority. Proper handling, maintenance, and use of personal protective equipment (PPE) are essential for preventing accidents and ensuring efficient operation.
Proper Handling and Storage
Grinding wheels should always be handled with care to prevent damage. Store them in a dry, cool environment to avoid deterioration and ensure they remain in optimal condition for use.
Personal Protective Equipment (PPE)
Always wear proper PPE, including safety goggles, gloves, and hearing protection, when using a grinding wheel. This helps protect you from flying debris, noise, and other hazards associated with grinding.
Understanding Wheel Failures
Wheel failures can be dangerous and cause serious injuries. It’s important to inspect the wheel for cracks or damage before use and avoid using excessive pressure or speed during operation.
Future Trends in Grinding Wheels
The future of grinding wheel is marked by technological advancements and a growing focus on sustainability. New developments are likely to bring about more efficient, durable, and eco-friendly grinding wheel.
Technological Advancements
As technology advances, grinding wheels are becoming more sophisticated. For instance, diamond and CBN wheels are being improved to handle even tougher materials with greater precision and longer wear life.
Sustainability in Grinding
The development of grinding wheels that use fewer raw materials and generate less waste is becoming a key focus for manufacturers.
Emerging Applications
As industries like aerospace and defense continue to grow, demand for high-precision grinding wheels for exotic materials will likely increase.
FAQs (People Also Ask and People Also Search For)
Can you cut metal with a grinding wheel?
Yes, cutting metal with a grinding wheel is possible, especially with cut-off wheels designed for metal cutting.
What are grinding wheels made of?
Grinding wheels are typically made from abrasive materials like aluminum oxide, silicon carbide, or industrial diamonds.
What are the different types of grinder wheels?
Common types include bonded wheels, diamond wheels, and cut-off wheels, each suited for different applications.
What is a grinding tool used for?
A grinding tool is used for cutting, polishing, and shaping hard materials, such as metal or stone.
Conclusion
In conclusion, grinding wheels are indispensable tools across various industries, from metalworking to precision tool making. Choosing the right type of wheel ensures efficiency, accuracy, and safety in your operations. By understanding the different types of wheels, materials, and applications, you can make informed decisions and enhance the overall productivity of your operations.