The article covers everything from the basic working principle, main components, and common types of grinding machines to their applications and machining precision in various scenarios. Additionally, it outlines the advantages and disadvantages of grinding machines and discusses common issues and solutions.
A grinding machine is a machine tool used for precision machining of workpiece surfaces. It removes very small amounts of material through the high-speed rotation of a grinding tool, such as a grinding wheel. Grinding machines play a key role in achieving high-precision surface finishes and delivering excellent dimensional accuracy and surface quality.
The article introduces various types of grinding machines in detail, such as surface grinders, cylindrical grinders, and CNC grinders. It explains their uses for different machining needs and industries, along with other related topics.
Working Principle of Grinding Machines
The working principle of a grinding machine primarily involves the relative movement between the grinding tool (such as a grinding wheel or abrasive belt) and the workpiece. This motion removes small amounts of material during the grinding process, achieving high precision and a smooth finish on the workpiece.
Process
- Workpiece Positioning or Movement: During grinding, the workpiece can either remain fixed on the worktable or move with it, depending on the specific grinding requirements.
- Tool Rotation: The machine’s spindle drives the grinding tool, rotating it at high speeds to perform efficient cutting. Higher tool speeds enhance grinding efficiency and surface quality.
- Cutting Action: As the rotating grinding tool contacts the workpiece, the abrasive grains cut into the surface with their sharp edges, removing tiny amounts of material. This process combines grinding, scraping, and polishing actions to achieve the desired finish.
Key Components of a Grinding Machine
Grinding Head
The grinding head serves as the core component of a grinding machine, responsible for holding the grinding tool and performing the actual grinding operation. Its design significantly impacts both grinding precision and efficiency.
- Composition: Typically includes a motor, spindle, and tool-holding device.
- Function: The grinding tool rotates at high speeds, enabling high-precision machining of the workpiece surface.
Grinding Tool
The grinding tool is essential for performing the grinding process, with its material, shape, and grit directly influencing the results.
- Types: Common types include diamond, silicon carbide, and aluminum oxide grinding tools.
- Selection: Choosing the right tool type and grit depends on the material and specific requirements of the job, ensuring optimal grinding results.
Worktable
The worktable holds the workpiece and provides stability, with its flatness and rigidity directly affecting grinding precision.
- Design: Typically made of cast iron, known for its rigidity and stability.
- Adjustment: Many worktables can move vertically and horizontally, adapting to different grinding needs.
Feed System
The feed system controls the relative position between the workpiece and the grinding tool, ensuring stable and precise grinding.
- Types: Available in manual or automatic configurations.
- Function: Precisely controls feed speed and direction to ensure uniform grinding, adjustable to meet processing requirements.
Spindle
The spindle, a crucial part of the grinding head, connects the grinding head to the motor and supports the grinding tool’s rotation.
- Characteristics: Spindle speed, rigidity, and precision are critical to achieving effective grinding results.
- Material: Typically made from high-strength alloy steel and undergoes precision machining for stable performance.
Cooling System
The cooling system reduces the temperature of both the grinding tool and the workpiece during grinding, preventing thermal deformation and tool wear.
- Methods: Common cooling methods include liquid and air cooling.
- Importance: Effective cooling improves grinding precision and extends the tool’s lifespan.
Control System
Modern grinding machines often feature CNC or PLC control systems, which manage all machine operations.
- Functions: Includes setting and adjusting parameters like grinding speed, feed rate, and grinding time.
- Advantages: Enhances automation, ensuring consistent and precise machining.
Support Frame
The support frame holds the grinding machine’s components, providing overall structural stability and rigidity.
- Structure: Typically made from steel or cast iron, designed for high resistance to deformation.
- Purpose: Provides a stable foundation, reduces vibration, and improves grinding precision.
Types of Grinding Machines, Their Applications, and Fields of Use
Surface Grinder
- Grinding Method: Uses parallel grinding, with the tool moving horizontally to process the workpiece’s flat surface.
- Main Application: Widely used for surface processing of metal and non-metal materials, such as molds, fixtures, and components.
- Purpose: Ensures the flatness and smoothness of workpiece surfaces, commonly used in aerospace, automotive, and machinery manufacturing.
Cylindrical Grinder
- Grinding Method: Grinds the external cylindrical surface of the workpiece, which is typically mounted on the main spindle.
- Main Application: Suitable for processing shafts, sleeves, and contour parts.
- Purpose: Improves diameter accuracy and surface finish, widely used in automotive, aerospace, and mechanical part manufacturing.
Internal Grinder
- Grinding Method: Uses a rotating grinding tool inside the workpiece bore, often with rotational support.
- Main Application: Designed specifically for internal bore processing, ideal for precision internal grinding.
- Purpose: Enhances bore accuracy and surface quality, suitable for mold-making and precision mechanical part processing.
Centerless Grinder
- Grinding Method: Eliminates center support; the workpiece grinds between two grinding tools, with automatic feed.
- Main Application: Ideal for high-volume production of cylindrical workpieces, such as shafts and rods.
- Purpose: Boosts production efficiency and consistency, widely used for automotive parts, bearings, and other mass-produced components.
Ultra-Precision Grinder
- Grinding Method: Utilizes ultra-precision grinding techniques with advanced control and fine parameter adjustments.
- Main Application: Used for components requiring extremely high precision, such as optical parts, precision instruments, and semiconductors.
- Purpose: Achieves nano-level surface quality and micron-level dimensional accuracy, suitable for optics, electronics, and high-end manufacturing.
CNC Grinder
- Grinding Method: Employs computer numerical control to automate the grinding process and handle complex shapes.
- Main Application: Ideal for grinding complex parts, particularly those requiring high precision and repeatability.
- Purpose: Extensively used in aerospace, automotive, mold-making, and precision engineering.
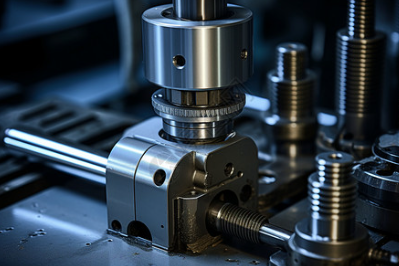
Surface Grinding Machine
- Grinding Method: Grinds with the flat surface of the tool, typically for surface treatment.
- Main Application: Suitable for grinding flat surfaces, grooves, and steps.
- Purpose: Enhances surface smoothness and dimensional accuracy, commonly used in mold-making, mechanical processing, and electronics manufacturing.
Face Grinder
- Grinding Method: Focuses on end-face grinding, with the tool’s axis parallel to the workpiece surface.
- Main Application: Processes and levels workpiece end faces.
- Purpose: Widely used for automotive parts, machine assembly, and precision component manufacturing.
Deep Hole Grinder
- Grinding Method: Specializes in deep-hole grinding, allowing the tool to grind along the length of internal bores.
- Main Application: Suitable for mold-making, cylinder bores, oil holes, and other deep-hole processing.
- Purpose: Increases dimensional accuracy and finish of deep holes, commonly applied in automotive and aerospace industries.
Multi-Purpose Grinder
- Grinding Method: Combines multiple grinding techniques, enabling various processes simultaneously.
- Main Application: Ideal for complex parts requiring multi-functional processing, such as external, internal, and face grinding.
- Purpose: Suits multi-step processing, widely applied in manufacturing high-precision and complex-shaped parts.
Ceramic Grinder
- Grinding Method: Designed specifically for ceramic materials, using specially crafted grinding tools.
- Main Application: Suitable for precision ceramic component processing.
- Purpose: Improves surface finish and dimensional accuracy of ceramic parts, applied in electronics and medical device fields.
Laser Grinder
- Grinding Method: Integrates laser technology for precise grinding and fine material removal with a laser beam.
- Main Application: Suitable for high-precision processing of thin-walled and small workpieces.
- Purpose: Extensively used in optics, electronic components, and micro-mechanical manufacturing for ultra-high precision.
Advantages and Disadvantages of Grinding Machines
Advantages of Grinding Machines
- High Precision:
Grinding machines achieve extremely high precision, often at the micron level, making them suitable for manufacturing parts with strict tolerances. - Excellent Surface Finish:
Grinding allows workpieces to achieve exceptional surface smoothness, reducing the need for further finishing. - Versatility:
Grinding machines handle various materials, such as metals and plastics, meeting the needs of different industries. - Capability for Complex Shapes:
Many grinding machines, like internal and centerless grinders, effectively process complex shapes, offering flexible machining solutions. - High Production Efficiency:
Grinding machines enable fast, efficient processing for mass production, helping to shorten production cycles.
Disadvantages of Grinding Machines
- High Equipment Costs:
Purchasing and maintaining grinding machines can be costly, posing a financial challenge for smaller businesses. - High Skill Requirements:
Precision grinding demands advanced skills and experience; improper operation may lead to part damage or substandard results. - Abrasive Wear:
Abrasives wear down during grinding and require regular replacement, which adds to maintenance costs. - Material Sensitivity:
Grinding machines impose specific material requirements; certain materials, like soft metals, may not be ideal for grinding. - Heat Impact:
Grinding generates heat, which can cause thermal deformation in the workpiece, affecting machining accuracy.
Grinding Machine Precision
Different types of grinding machines vary in design and functionality, leading to different precision levels. Choosing the right type depends on specific machining requirements and precision needs to ensure both effective results and productivity.
Internal Grinder
- Precision: Typically ranges from ±0.001mm to ±0.005mm. In high-precision applications, it can achieve around ±0.0005mm (0.5 microns), meeting higher accuracy demands.
Cylindrical Grinder
- Precision: Generally between ±0.001mm and ±0.005mm. For high-precision applications, it can reach ±0.0005mm (0.5 microns), ideal for ultra-high precision work.
CNC Grinder
- Positioning Precision: Typically between ±0.001mm and ±0.005mm, with some high-precision models reaching ±0.0005mm or better.
- Repeatability: Usually from ±0.001mm to ±0.002mm, with high-precision models achieving ±0.0005mm.
- Machining Precision: Varies by machine type, generally between ±0.005mm and ±0.01mm, with specific high-precision equipment achieving up to ±0.001mm or higher.
Surface Grinder
- Precision: Generally ranges from ±0.002mm to ±0.01mm. High-precision models can achieve ±0.001mm or better, ideal for applications requiring strict flatness and smoothness.
Plane Grinder
- Precision: Typically ranges from ±0.002mm to ±0.01mm. Some high-precision models can reach up to ±0.001mm, suitable for advanced requirements.
Tool Grinder
- Precision: Usually from ±0.001mm to ±0.005mm, and for high-precision applications, it can reach ±0.0005mm, ideal for ultra-precise tool production and sharpening.
Face Grinder
- Single Face Grinder: Achieves precision between ±0.005mm and ±0.01mm, suited for applications with moderate production speed and high accuracy demands.
- Double Face Grinder: Achieves between ±0.002mm and ±0.005mm, allowing simultaneous grinding of two faces, enhancing efficiency, ideal for high-volume, high-precision production.
Deep Hole Grinder
- Precision: Typically between ±0.005mm and ±0.01mm, with high-precision work reaching around ±0.002mm.
Multi-Purpose Grinder
- Precision: Ranges from ±0.002mm to ±0.01mm. For more demanding work, it can achieve ±0.001mm, ideal for processing complex shapes with multiple operations.
Ceramic Grinder
- Precision: Generally from ±0.001mm to ±0.01mm. Under specific conditions, ultra-precision work can reach approximately ±0.0005mm.
Laser Grinder
- Precision: Typically achieves ±0.005mm to ±0.01mm. For high-precision tasks, it can reach ±0.001mm or even bett
Ultra-Precision Grinder
- Precision: Ranges from ±0.0001mm (0.1 microns) to ±0.001mm. Under specific ultra-precision conditions, it can achieve ±0.00001mm (10 nanometers) or better.
Common Issues and Solutions
Poor Surface Finish
- Causes: Incorrect abrasive choice, improper grinding parameters, or unstable workpiece clamping.
- Solution: Select the right abrasive and grit size, adjust grinding speed and feed rate, and ensure the workpiece is securely clamped.
Excessive Vibration
- Causes: Unstable machine foundation, imbalanced grinding force, or worn tools.
- Solution: Check and reinforce the foundation, balance the tool and workpiece, and replace worn tools regularly.
Burn Marks on Workpiece
- Causes: Grinding speed too high, insufficient coolant, or overheating of the workpiece.
- Solution: Reduce grinding speed, increase coolant flow, and inspect the cooling system regularly.
Decline in Precision
- Causes: Worn machine components, improper adjustments, or incorrect operation.
- Solution: Perform regular maintenance and calibration, inspect for worn components, and replace them as needed.
Clogged Abrasive
- Causes: Abrasive grit too fine or workpiece material too hard.
- Solution: Choose a suitable grit size and adjust the feed rate accordingly.
Excessive Grinding Force
- Causes: Worn tools or incorrect grinding parameters.
- Solution: Replace or sharpen the tool, and adjust the grinding speed and feed rate.
Stiff Worktable Movement
- Causes: Dirty or worn guide rails.
- Solution: Clean the guide rails, and repair or replace them if necessary.
Contaminated Coolant
- Causes: Failure to replace coolant or poor coolant management.
- Solution: Regularly inspect and replace coolant to ensure it remains clean and effective.
Grinding Machine Lifespan
The lifespan of a grinding machine depends on various factors, including design quality, usage frequency, maintenance practices, and the working environment. Generally, the lifespan can be estimated as follows:
- Standard Grinding Machines: Typically last between 10 to 20 years, with lifespan heavily influenced by usage frequency and maintenance practices.
- High-End Grinding Machines: Designed for high loads and precision, these machines can last over 20 years, or even longer with proper care.
- Usage Frequency: Machines used frequently experience faster wear, which may require parts replacement or major repairs sooner.
- Maintenance: Regular maintenance and careful use can significantly extend a machine’s lifespan. This includes routine cleaning, abrasive replacement, and lubrication.
- Working Environment: In harsher environments (such as those with dust or high humidity), grinding machines may experience accelerated wear, potentially shortening their lifespan.
Power Requirements for Grinding Machines
- Small Grinding Machines:
Typically require between 0.5 and 3 kilowatts (kW), suitable for grinding small parts. - Medium Grinding Machines:
Generally require between 3 and 10 kilowatts, ideal for medium-scale tasks and capable of handling larger workpieces. - Large Grinding Machines:
Power can exceed 10 kilowatts, often reaching 20 kilowatts or more, making them suitable for high-load, high-volume production, and heavy-duty workpieces. - Specialized Grinding Machines:
Certain specialized machines, such as centerless or internal grinders, may require additional power depending on specific processin
Price Analysis for Grinding Machines
Prices for different types of grinding machines vary based on brand, model, specifications, and market demand. Specific pricing factors include equipment configuration, additional features, suppliers, and region. It is advisable to consult multiple suppliers for accurate quotes before purchasing.
Price Range and features
Surface Grinders
Entry-Level Manual Surface Grinder:
- Price Range: Around $3,000 to $10,000
- Features: Suitable for small workshops and tasks that don’t require high precision. Mostly manual operation, ideal for small-batch and basic surface grinding.
Mid-Range Automatic Surface Grinder:
- Price Range: Usually $10,000 to $50,000
- Features: Comes with automatic feed, suited for small- to medium-scale tasks. Capable of high-precision surface grinding, ideal for batch production with moderate complexity. Equipped with basic controls and cooling systems.
High-Precision CNC Surface Grinder:
- Price Range: Around $50,000 to $150,000
- Features: CNC-controlled with precise automatic feed and wheel dressing. Suitable for high-precision needs in mold-making and fine machining. Often meets aerospace, automotive, and electronics industry demands.
Ultra-Precision and Custom Surface Grinder:
- Price Range: Typically $150,000 to $500,000 or more
- Features: Ideal for large or ultra-precise workpieces. Features multi-axis control, automated measurement, thermal compensation, and temperature control. Used in aerospace, large mold-making, and other high-end applications.
Cylindrical Grinders
Entry-Level Manual Cylindrical Grinder:
- Price Range: Around $5,000 to $20,000
- Features: Ideal for small workshops, suited for simple external cylindrical grinding. Often manual and basic, fitting single-piece or small-batch production.
Mid-Range Automatic Cylindrical Grinder:
- Price Range: Usually $20,000 to $80,000
- Features: Automatic feed with basic CNC controls, suitable for medium-batch production and tasks requiring moderate precision. Higher automation boosts productivity and consistency.
High-Precision CNC Cylindrical Grinder:
- Price Range: Around $80,000 to $200,000
- Features: Advanced CNC system allows precise control over feed, speed, and grinding path. Suitable for batch production, complex shapes, and high-precision needs across automotive, aerospace, and mold industries.
Ultra-Precision and Large Custom Cylindrical Grinder:
- Price Range: Typically $200,000 to $500,000 or more
- Features: Ideal for ultra-precise and large-diameter workpieces, featuring multi-axis control, automated measurement, and temperature control for demanding industries like aerospace and high-end manufacturing.
Internal Grinders
Entry-Level Manual Internal Grinder:
- Price Range: Around $10,000 to $30,000
- Features: Generally manual or semi-automatic, suitable for small workshops and basic internal grinding tasks. Fits single-piece or small-batch production, with accuracy around ±0.01mm to ±0.005mm.
Mid-Range Automatic Internal Grinder:
- Price Range: Usually $30,000 to $100,000
- Features: Automatic feed enhances productivity, suited for medium-scale production and precision tasks. Typical accuracy ranges between ±0.005mm and ±0.002mm.
High-Precision CNC Internal Grinder:
- Price Range: Around $100,000 to $250,000
- Features: CNC-controlled for precise grinding paths, feed speeds, and processing parameters. Ideal for high-precision, batch production needs in aerospace, automotive, and fine machinery, with accuracy up to ±0.001mm.
Ultra-Precision and Large Custom Internal Grinder:
- Price Range: Typically $250,000 to $500,000 or more
- Features: Suitable for high-precision, large internal grinding, featuring multi-axis control, automated measurement, and temperature control.
Centerless Grinders
Entry-Level Manual Centerless Grinder:
- Price Range: Around $10,000 to $30,000
- Features: Suitable for basic external cylindrical grinding, often manually operated for small-batch and simple tasks with precision around ±0.01mm to ±0.005mm.
Mid-Range Automatic Centerless Grinder:
- Price Range: Usually $30,000 to $80,000
- Features: Automatic feed and basic controls enhance productivity and consistency, suitable for medium-scale production and moderate precision.
High-Precision CNC Centerless Grinder:
- Price Range: Around $80,000 to $200,000
- Features: CNC system for precise control over all grinding parameters, suitable for high-volume, high-precision needs in automotive and aerospace industries, with accuracy up to ±0.001mm.
Ultra-Precision and Large Custom Centerless Grinder:
- Price Range: Typically $200,000 to $500,000 or more
- Features: Ideal for large-diameter, ultra-precise cylindrical grinding, featuring multi-axis control and temperature control.
Ultra-Precision Grinders
Entry-Level Ultra-Precision Grinder:
- Price Range: Around $200,000 to $400,000
- Features: Basic ultra-precision functions, suitable for small-scale high-precision tasks, often achieving sub-micron accuracy.
Mid-Range Ultra-Precision Grinder:
- Price Range: Around $400,000 to $800,000
- Features: High precision and automation for micro-level accuracy in batch production. Commonly used for optical parts, precision molds, and microelectronics.
High-End Ultra-Precision Grinder:
- Price Range: Typically $800,000 to $2,000,000 or more
- Features: Achieves micro- to nano-level accuracy, equipped with comprehensive automation, real-time monitoring, vibration, and temperature control. Used in aerospace, semiconductors, and high-precision optical manufacturing.
CNC Grinders
Entry-Level CNC Grinder:
- Price Range: Around $20,000 to $50,000
- Features: Suitable for basic CNC tasks, ideal for small to medium-sized factories. Precision and features are basic, usually with 2-3 control axes.
Mid-Range CNC Grinder:
- Price Range: Typically $50,000 to $150,000
- Features: Offers richer features with precise CNC systems, automatic wheel dressing, and cooling, suitable for medium complexity tasks and high precision needs.
High-Precision CNC Grinder:
- Price Range: Around $150,000 to $300,000
- Features: Ideal for precision manufacturing in aerospace, automotive, and mold industries. Multi-axis control (4 or 5 axes) allows for complex shapes, with advanced measurement and temperature control.
Ultra-Precision Custom CNC Grinder:
- Price Range: Typically $300,000 to $1,000,000 or more
- Features: Designed for high-precision applications like semiconductors and optical manufacturing, often with 5+ axes, air-bearing spindles, and extreme temperature control.
Surface Grinders
Entry-Level Manual Surface Grinder:
- Price Range: Around $3,000 to $10,000
- Features: Ideal for small workshops with basic tasks, usually with manual feed and basic structure.
Mid-Range Automatic Surface Grinder:
- Price Range: Typically $10,000 to $50,000
- Features: Automatic feed and basic controls for medium-scale operations. Suitable for batch production with moderate precision needs.
High-Precision CNC Surface Grinder:
- Price Range: Around $50,000 to $150,000 or more
- Features: CNC control allows precise multi-axis and automated processing, meeting high-precision needs in aerospace and electronics.
Ultra-Precision Custom Surface Grinder:
- Price Range: Typically $150,000 to $500,000 or more
- Features: Suitable for large or ultra-precise tasks, with multi-axis.
Influencing factors
- Equipment Specifications
The specifications of a grinding machine, such as machining size and power, directly impact its price. Larger, high-performance grinders tend to have higher prices. - Brand and Manufacturer
Grinding machines from well-known brands and major manufacturers often come at a premium due to the superior after-sales service, quality assurance, and technical support they provide. - Condition
New machines are significantly more expensive than used grinders. While second-hand options may be cheaper, they can come with issues related to performance and reliability. - Additional Features
Grinding machines with automation or CNC capabilities usually cost more. Extra features and advanced technology add to the overall equipment cost.
How to Choose Grinding Wheel Specifications for Grinding Machines
- Material Being Processed:
Different materials, such as metals, plastics, and ceramics, require specific abrasives. Hard materials need higher-hardness abrasives, like diamond or CBN, while softer materials can use aluminum oxide. - Grit Size:
Grit size determines the coarseness of the grinding wheel. Coarse grit wheels (smaller grits, such as 16-60) work well for rough machining, while finer grit wheels (larger grits, such as 80-120) suit precision finishing. Choose grit size based on machining requirements. - Wheel Diameter and Thickness:
The diameter affects the grinding range and efficiency. Larger diameters are better for larger workpieces, while smaller ones suit detailed work. Thicker wheels tend to be more durable but less flexible, whereas thinner wheels are suitable for fine grinding. - Bond Type:
Bond choice impacts wheel toughness and strength. Resin bonds suit most applications, while ceramic bonds are ideal for high-temperature and high-strength grinding. - Operating Speed:
Match the grinding wheel’s operating speed to the machine’s specifications. Higher speeds require stronger wheels to prevent breakage. - Shape and Application:
The wheel shape should align with the machining needs. For instance, flat wheels are ideal for surface grinding, while internal grinding requires shapes suited for bore work. - Cooling Requirements:
Heat generated during grinding can impact quality, so choose wheels that accommodate appropriate cooling methods to help control temperature during the process.
When selecting a grinding machine, consider not only the machining needs but also the noise impact on the work environment.
Noise Comparison of Common Grinding Machine Types
Different types of grinding machines produce varying noise levels based on design, grinding method, and materials used. Here’s a comparison of noise levels for common grinding machines (measured in decibels [dB], with actual noise varying by specific equipment):
Surface Grinder
- Noise Level: Around 75 – 85 dB
- Features: Due to the large grinding area, noise is noticeable but generally acceptable.
Cylindrical Grinder
- Noise Level: Around 80 – 90 dB
- Features: High-speed rotation and grinding produce significant noise, so soundproofing measures are advisable.
Internal Grinder
- Noise Level: Around 75 – 85 dB
- Features: Similar to surface grinders, but internal structures can sometimes create resonance.
Centerless Grinder
- Noise Level: Around 80 – 90 dB
- Features: Noise levels are high, especially during high-production rates, often requiring enhanced noise control measures.
Ultra-Precision Grinder
- Noise Level: Around 70 – 80 dB
- Features: Designed for precision, these grinders produce relatively lower noise, suitable for noise-sensitive environments.
CNC Grinder
- Noise Level: Around 75 – 85 dB
- Features: Noise is similar to traditional grinders, though the automation may create varying sounds during specific operations.
Safety Performance Comparison of Common Grinding Machine Types
Surface Grinder
- Safety Performance: Sturdy construction and stable worktable reduce vibration impact on operations.
- User Protection: Most surface grinders include safety shields to protect operators from flying debris during grinding.
- Emergency Stop: Typically equipped with an emergency stop button for quick shutdown in case of an accident.
Cylindrical Grinder
- Safety Performance: Designed to ensure secure workpiece positioning, minimizing the risk of dislodgement during grinding.
- User Protection: Some models have shields to protect operators from metal chips and heat exposure.
- Emergency Stop: Equipped with a quick-stop function to enhance operational safety.
Internal Grinder
- Safety Performance: Requires higher safety standards due to its unique operation style and usually includes enhanced protective features.
- User Protection: Internal structures often have protective elements to prevent debris from flying out during grinding.
- Emergency Stop: Includes an emergency stop button to address unexpected situations.
Centerless Grinder
- Safety Performance: Designed for high-speed grinding, requiring special attention to operational safety.
- User Protection: Many centerless grinders come with safety shields to prevent injuries from dislodged workpieces.
- Emergency Stop: Typically includes an emergency stop function for swift response to potential hazards.
Ultra-Precision Grinder
- Safety Performance: Emphasizes stability and accuracy, enhancing safety due to its precise design.
- User Protection: Generally equipped with advanced protective devices to prevent accidents during high-precision machining.
- Emergency Stop: Features a robust emergency stop mechanism to prevent accidents caused by equipment failure.
CNC Grinder
- Safety Performance: High automation allows safe operation under programmed settings, reducing manual intervention risks.
- User Protection: Equipped with multiple safety features, such as safety doors and photoelectric sensors, ensuring operator safety.
- Emergency Stop: Integrated with an emergency stop function to quickly cut power and halt operations when needed.
Safe Operation of Grinding Machines
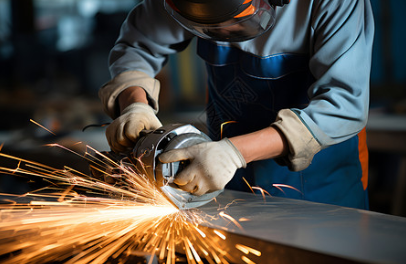
Personal Protective Equipment (PPE)
- Wear safety goggles for eye protection from debris.
- Use ear protection to minimize noise damage.
- Wear gloves to protect hands, but avoid when there’s a risk of entanglement.
- Dress appropriately, avoiding loose clothing and accessories.
Work Environment
- Keep the work area clean, regularly clearing any clutter around the grinder to prevent slips and trips.
- Ensure proper ventilation to reduce the concentration of harmful gases and dust.
Machine Inspection
- Check the machine’s condition before use, ensuring all parts are functional and free of wear or damage.
- Confirm that all safety features, such as guards and emergency stop switches, are intact and operational.
Operating Procedures
- Follow the manufacturer’s operation manual at all times.
- Securely install the workpiece and grinding tool, ensuring they remain stable during grinding.
- Adjust the feed rate according to the material and grinding requirements, avoiding speeds that are too fast or too slow.
Control and Monitoring
- Stay focused during machine operation, avoiding distractions and maintaining attention to the task.
- Regularly monitor the grinding process, checking for any abnormalities.
Emergency Procedures
- Familiarize yourself with the emergency stop mechanism, knowing how to quickly halt the grinder in urgent situations.
- In case of an accident, immediately stop operations and follow the emergency procedures, seeking professional assistance if necessary.
Training and Knowledge
- Participate in safety training to ensure operators understand machine operation and safety requirements.
- Continue learning by regularly updating safety knowledge and staying informed on new technologies and best practices.
Choosing the right grinding machine is a crucial decision that directly affects the quality, efficiency, and safety of grinding operations. By carefully considering factors such as machine type, material to be ground, required precision, wheel specifications, and safety features, you can make an informed choice that best meets your needs.