We stand amidst a craft with thousands of years of history, one that holds a vital place in the world of metalworking. So, what exactly is sand casting? With simple materials like sand and molten metal, how do we produce everyday or even unique metal creations? Whether we are newcomers to metalworking or seasoned professionals, exploring the mysteries of sand casting takes us into a fascinating world where art and engineering unite.
Sand casting is one of the most traditional and commonly used casting processes, primarily for producing various metal components. The basic principle involves pouring liquid metal into a pre-formed sand mold and allowing it to cool and solidify into the desired shape.
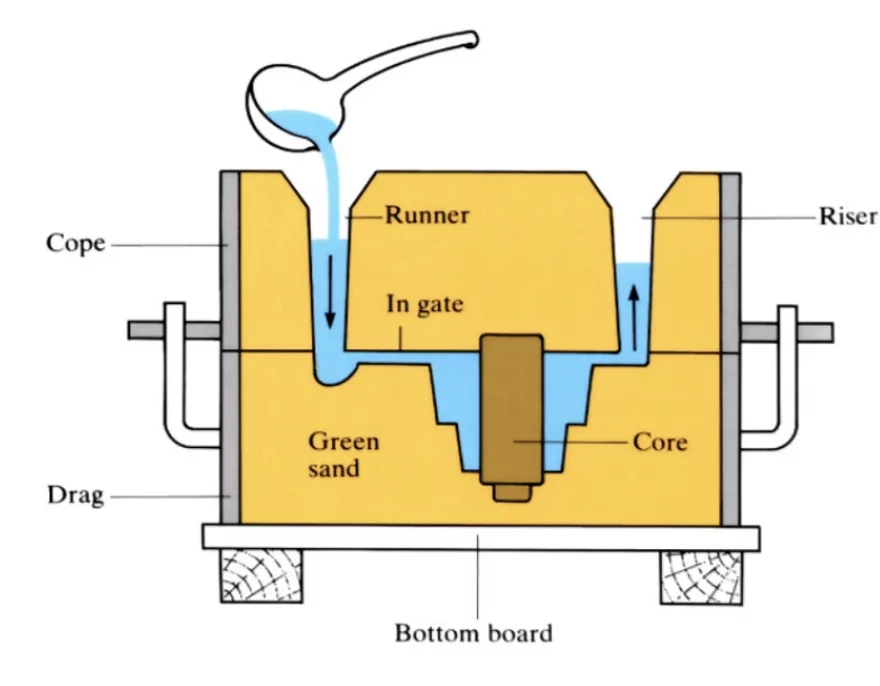
In this article, we’ll explore the fundamentals, historical background, and applications of sand casting, and why it continues to be an indispensable method in today’s manufacturing world.
Understanding Sand Casting: The Basics
Sand casting involves pouring molten metal into a sand mold, which holds the shape of the desired part. As the metal cools and solidifies, it takes on the intricate details of the mold, resulting in a precise and often complex metal part. The process sounds straightforward, but there’s a wealth of knowledge behind each step, from creating the mold to removing the final cast piece.
Quick overview of the it process:
- Creating the Mold: Workers pack a mixture of sand, clay, and water around a pattern of the desired shape. Once the sand settles and hardens, they remove the pattern, leaving a cavity shaped like the final piece.
- Melting the Metal: Workers heat the chosen metal in a furnace until it becomes molten.
- Pouring the Metal: Workers carefully pour molten metal into the mold cavity, filling every crevice.
- Cooling and Solidifying: The metal cools and solidifies within the sand mold, taking on the precise shape.
- Removing the Casting:After it cools, workers break away the mold to reveal the cast part, then clean and refine it.
Why is Sand Casting Still So Popular?
In a world filled with high-tech manufacturing methods, why does itremain so widely used? The answer lies in its versatility and efficiency. Sand casting offers several unique advantages:
- Flexibility: It works for almost any metal that melts and pours, including iron, steel, aluminum, and bronze.
- Cost-Effectiveness: Compared to other methods, it is relatively low-cost, especially for small batches or custom parts.
- Adaptability for Complex Shapes: With sand casting, it’s possible to achieve intricate geometries that are difficult to make with other methods.
- Scalability: From single custom pieces to large production runs, sand casting adapts to various production needs.
Where is it Used?
Sand casting finds its way into countless applications. Here are some areas where it plays a vital role:
- Automotive Industry: Many engine blocks, manifolds, and other automotive parts are produced through it.
- Aerospace Sector: Critical components that must withstand extreme conditions, like turbine blades and housings, are often sand cast.
- Construction and Architecture: From large structural pieces to decorative metalwork, it allows for the creation of durable and aesthetic metal components.
- Art and Sculpture: Many artists use it to create one-of-a-kind metal sculptures, statues, and custom metalwork.
The Sand Casting Process in Detail
While the basics of it are easy to grasp, each step in the process requires precision and skill:
- Pattern Design: The process begins with a pattern that mimics the shape of the final product. Workers make patterns from wood, metal, or plastic, designing them with allowances for the metal’s shrinkage as it cools.
- Mold Assembly: The mold typically consists of two halves, which align to form the final cavity. To ensure the mold stays intact, workers mix sand with bonding agents, which gives it the strength needed to hold shape under the weight of molten metal.
- Pouring and Cooling: Pouring the metal is a delicate process; it needs to be poured at the right speed and temperature. Too fast or too hot, and the mold may fail; too slow or too cold, and the metal may not fill the mold properly.
- Shakeout and Cleaning: After cooling, the mold is removed, and the casting undergoes cleaning to remove any sand or impurities, leaving a smooth, finished part ready for use or further processing.
Challenges of Sand Casting
While it is versatile, it has some challenges. Precision can be difficult to achieve compared to other casting methods, and the sand mold is destroyed in each cycle, meaning molds must be recreated for each casting. Additionally, porosity and surface defects can occur if the process isn’t carefully controlled. Despite these challenges, the benefits often outweigh the drawbacks, especially for applications requiring high durability and custom shapes.
The Future of Sand Casting
As technology advances, so does the potential for sand casting. Today, engineers and manufacturers use 3D printing to transform the way they create patterns and molds, enabling faster and more precise mold production. Environmental sustainability is also becoming a focus, with efforts to recycle sand and reduce emissions in casting foundries. Sand casting remains a vital and evolving process, blending tradition with innovation.
Conclusion
Sand casting is a time-honored method that still powers modern industries and inspires artists alike. Its ability to adapt to various metals, its cost-effectiveness, and its unique capacity for creating complex shapes make it indispensable. By understanding the ins and outs of it, you gain insight into a process that has shaped civilization, will continue to shape the future. Whether you’re interested in the craftsmanship, the science, or the endless possibilities it offers, it is truly a fascinating world to explore.