From the moment we took our first steps in manufacturing, creativity and passion have driven human progress. CNC machining and manual machining, each in their own way, have played essential roles in this long journey, offering us endless possibilities. CNC machining, known for its speed and precision, transforms cold, hard metal into intricate parts. It works tirelessly, day after day, as a reliable guardian of the modern factory, bringing consistency and efficiency to every task. Meanwhile, manual machining is like a seasoned craftsman, using experience and skilled hands to shape each piece into a unique work of art, breathing life into every material.
CNC machining uses computer numerical control to guide machine tools, allowing for precise control of the cutting path, which makes it ideal for high-precision, large-scale production. In contrast, manual machining relies on machinists to operate the equipment directly, with adjustments made by hand. This method is more flexible, fitting well with small batches and simpler custom jobs.
In this article, we will delve into these two very different machining methods and explore how each brings energy and innovation to today’s rapidly evolving manufacturing world.
What is CNC Machining?
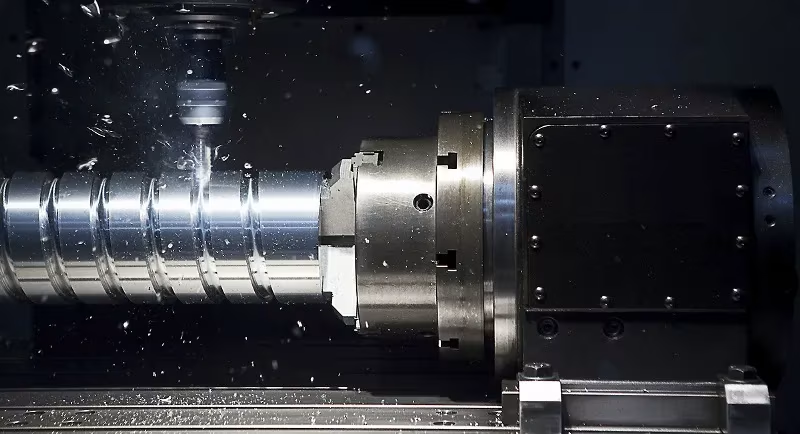
CNC (Computer Numerical Control) machining uses computer technology to control the movement and operation of machine tools. These machines precisely cut, shape, and drill materials using programmed commands, allowing manufacturers to achieve high levels of accuracy and consistency.
- Key Features:Speed, precision, repeatability, and the ability to handle complex shapes with ease.
- Benefits: CNC machines handle complex, intricate designs in ways that manual machining could never dream of achieving. They can run continuously, 24/7, making them ideal for high-volume production.
- Applications: Industries like aerospace, automotive, and electronics rely on CNC for high-precision parts.
What is Manual Machining?
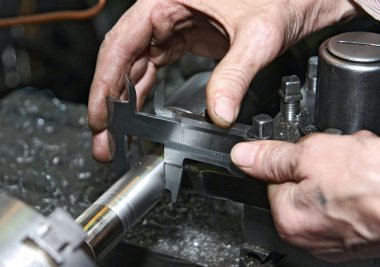
Manual machining relies on skilled machinists who operate tools by hand. Using levers, gears, and handwheels, machinists directly control the cutting tools, making adjustments as they go.
- Key Features:Hands-on control, flexibility for one-off or small batch parts, and the ability to feel and respond to the material.
- Benefits: Manual machining is perfect for simple parts, repairs, and custom work. Skilled machinists can adjust on the fly, making it an excellent choice for tasks that require human intuition.
- Applications: Ideal for custom or low-volume production, prototyping, and repairs.
The Battle of Machines: CNC vs. Manual
Let’s dig into the strengths and weaknesses of each approach.
Speed and Efficiency
- CNC machining takes the lead in speed, especially for large production runs. With its automation, it handles repetitive tasks with remarkable efficiency.
- Manual machining, however, offers flexibility in one-off tasks and small batches. For quick, simple cuts, setting up a manual machine might even be faster.
Precision and Consistency
- CNC machines consistently deliver high precision, as they follow the exact programmed paths without deviation.
- Manual machining can achieve high precision, too, but it relies heavily on the operator’s skill and experience. Minor variations can occur, especially with complex parts.
Complexity and Capability
- CNC machines excel with complex geometries and intricate patterns. If you need something with elaborate details, CNC is the way to go.
- Manual machining is limited to simpler shapes, although skilled machinists can produce surprisingly complex parts.
Skill Level Required
- CNC machining requires knowledge of programming and software, making it a tech-savvy trade.
- Manual machining demands hands-on experience and in-depth knowledge of materials, tools, and machining techniques. It’s a skill learned over years of practice.
Topics of Interest
Cost Comparison: How does CNC’s high upfront cost balance with operational costs and scalability? Is manual machining more cost-effective for small workshops?
CNC machining comes with a higher upfront cost, but its efficiency and scalability significantly reduce unit costs in large-scale production. For small workshops or low-volume production tasks, manual machining is often more cost-effective due to lower equipment and maintenance costs. CNC is ideal for high-precision, repetitive tasks, while manual machining provides more flexibility, fitting well with custom and small-batch production.
Career Opportunities and Skills: How do the career paths for CNC machinists differ from manual machinists? Which skills are most valuable in today’s market?
CNC machinists focus on programming and numerical control skills, aligning well with trends in automation and smart manufacturing, so technical knowledge and CNC programming are highly valuable skills. On the other hand, manual machinists rely on hands-on operation and material handling experience, which makes them well-suited for roles in repair and custom machining. In today’s market, CNC programming and automation skills are in high demand, but manual machinists remain essential for small-batch and custom projects.
Technology Trends: What are the recent developments in CNC technology? Are there hybrid machines that combine the strengths of both methods?
CNC technology is advancing in areas like multi-axis machining, automation, and intelligent control. For example, hybrid machines that incorporate laser cutting and 3D printing functions allow for high precision and complex shape processing. These hybrid machines combine CNC’s high efficiency with the flexibility of manual machining, making them an increasingly popular solution for tasks that require multifunctional operations and complex machining in modern manufacturing.
Sustainability in Manufacturing: How do these two methods impact sustainability, and which one is more environmentally friendly?
CNC machining is often more environmentally friendly because its precise cutting paths reduce material waste, and its high efficiency enhances productivity in large-scale production. While CNC equipment consumes more power, its faster production speed can lower overall energy usage. Manual machining, due to its lower efficiency, tends to require more time and may increase resource consumption. For tasks requiring high efficiency and repeatability, CNC machining has a sustainability advantage.
Industry Applications: Why do some industries favor CNC while others still value manual machining, and how does this affect product quality?
High precision and consistency make CNC machining a preferred choice in industries like aerospace, automotive, and electronics, where stable quality and mass production are essential. However, manual machining remains highly valued in custom, repair, and arts and crafts fields due to its flexibility for special or small-batch tasks. CNC machining ensures consistent product quality, while manual machining adds a personalized touch and detailed craftsmanship. Both methods have unique strengths, impacting product quality differently based on industry needs.
Choosing the Right Method: What factors should one consider when choosing between CNC and manual machining for a specific project?
Choosing between CNC and manual machining depends mainly on the complexity, volume, precision requirements, and budget of the project. CNC machining is ideal for high-precision, large-volume, and complex part production, especially when timing and consistency are critical. Manual machining, on the other hand, suits low-volume, custom, or repair tasks, offering flexibility with a lower initial cost. Ultimately, the choice should consider processing needs, budget limitations, and specific project requirements.
Conclusion: Finding the Balance
While CNC and manual machining each have their strengths, knowing when to use one over the other can yield different results. Manual machining will always attract those who value craftsmanship and direct control, while CNC represents the future, making manufacturing faster, more precise, and more flexible.
Are you ready to explore the possibilities that CNC and manual machining can bring to your projects? At Minnuo Group, we specialize in cutting-edge CNC equipment and are here to answer your questions and support your manufacturing needs. Visit our website to learn more, and let’s work together to provide the perfect machining solution for your requirements!