In modern manufacturing, the combination of air compressors and machine tools forms a “golden duo,” bringing significant convenience and efficiency to all types of workshops. Whether it’s lathes, milling machines, or CNC centers, air compressors play a crucial role. They not only supply a reliable power source for machine tools but also boost production efficiency, ensure operational safety, and extend the lifespan of the equipment.
By powering pneumatic clamps, cooling systems, and chip removal processes, air compressors offer high-efficiency, stable support for machine operations. This synergy elevates productivity, prolongs equipment life, and reduces operational risks, making compressed air the ideal auxiliary for any machine tool.
Let’s explore how air compressors and machine tools work together to add substantial value to your manufacturing process.
What is an Air Compressor?
An air compressor works by compressing air to a higher pressure, generating pressurized air with stored energy. This compressed air can drive various pneumatic tools and mechanical equipment. Imagine it as a powerful “air pump” that not only supplies strong and steady power to devices but also plays an essential role in countless applications.
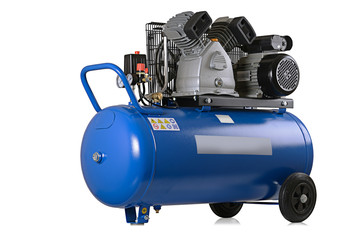
Types of Air Compressors
Air compressors fall into several main categories based on their working principles and applications:
- Reciprocating Compressors
These compressors use a piston that moves back and forth to compress air, making them one of the most common types. With high-pressure output and the ability to handle heavy loads, they find wide use in fields like automotive repair and manufacturing. - Screw Compressors
Screw compressors use two rotating screws to compress air, providing continuous output with high efficiency. They suit applications requiring a steady air supply, such as food processing, textiles, and pharmaceutical production. Because of their compact structure and low noise levels, many businesses prefer these compressors. - Centrifugal Compressors
Centrifugal compressors compress air using centrifugal force, making them ideal for large-scale industries like petrochemicals and power facilities. They handle large air volumes and are perfect for extended, stable operation. However, they come with higher costs, so they best fit larger companies with more substantial budgets. - Rotary Vane Compressors
These compressors rely on sliding vanes within a stator to compress air. Their benefits include smooth operation and low noise, making them a good fit for small to mid-sized industrial applications, such as refrigeration systems and air conditioning.
Air Compressor Applications in Machine Tools
- Pneumatic Clamps
Many machine tools are equipped with pneumatic clamping systems, which allow for quick and precise workpiece fixation during machining. Compressed air powers these clamps, ensuring that the workpiece stays securely in place on the worktable. This type of clamping not only provides fast operation but also allows for precise control over clamping force by adjusting air pressure, reducing the risk of workpiece deformation. - Cooling and Lubrication
During machining, machine tools must maintain optimal temperatures to prevent overheating. Air compressors supply cooling air flows or work with coolant spray systems to keep the tool and workpiece at appropriate temperatures throughout the cutting process. Especially in high-speed and heavy-load machining environments, compressed air effectively removes heat, helping to prevent wear and tear on both the machine tool and cutting tools. - Chip Removal
Turning, milling, and other machining operations generate significant amounts of metal chips and dust. If not cleared promptly, these chips can impact machining precision and even damage the equipment. Air compressors provide powerful airflow that allows operators to quickly blow chips and debris off worktables and guideways, keeping the machine clean and improving both precision and tool lifespan. - Pneumatic Tool Operation
Compressed air is also essential for routine machine tool maintenance. Many tools and devices, such as pneumatic wrenches and grinders, rely on compressed air for operation. These pneumatic tools can significantly enhance the efficiency of machine setup and maintenance, and they offer a lighter, safer alternative to traditional electric tools.
Why Are Machine Tools Inseparable from Air Compressors?
Machine tools rely heavily on air compressors for multiple reasons, as they significantly boost production efficiency, reduce operational costs, and offer key advantages in various areas:
- Enhanced Machining Efficiency
With the help of pneumatic clamps, cooling systems, and automation control devices, compressed air greatly enhances the efficiency of machining operations. Many automated production lines depend on compressed air for fast clamping, automatic feeding, and automated cleaning, which reduces manual intervention and allows for more precise, high-speed production. - Energy Cost Savings
Air compressors consume less energy than electric equipment, and air-driven systems are typically safer, especially for high-power machine tools. Using compressed air to drive pneumatic devices and control systems can drastically cut down on electricity consumption, leading to substantial savings in operational costs. - Improved Operational Safety
Compressed air systems provide a safer option, particularly in humid or hazardous environments. Many machine tools utilize compressed air to power pneumatic systems, which helps avoid risks associated with electrical failures. Additionally, pneumatic tools are often lighter than electric tools, reducing operator fatigue and lowering the risk of workplace injuries. - Extended Equipment Life
Compressed air not only helps to clear chips from cutting operations but also provides effective cooling to the machine. This cooling effect prevents damage to cutting tools and machine parts from excessive heat. In high-load, prolonged machining processes, cool compressed air lowers the temperature of tools and components, reducing wear and overheating, ultimately extending the equipment’s lifespan.
How to Choose the Right Air Compressor for Machine Tools
Selecting an air compressor suitable for your machine tools involves considering a few key factors:
- Match Pressure and Flow with Process Requirements
Different machine tool operations require varying levels of air pressure and flow. For example, machining centers and CNC machines need a steady and continuous compressed air supply, making screw compressors a better choice. On the other hand, smaller benchtop machines can perform well with portable or compact reciprocating compressors. - Consider the Working Environment
If the machine tool operates in a dusty or humid environment, look for an air compressor with protective features, such as an oil-free compressor with a filtration system. This type of compressor keeps the machine free from contamination, ensuring a clean and reliable air supply. - Focus on Energy Efficiency and Maintenance Costs
Energy-efficient compressors help reduce long-term electricity costs, and those with lower maintenance requirements fit the demands of modern manufacturing floors. Choosing a compressor that is both cost-effective to maintain and simple to operate aligns well with the needs of today’s workshops.
The Future of Air Compressors and Machine Tools Working Together
As manufacturing trends lean towards automation and smart technology, the integration of air compressors and machine tools continues to advance. In the future, we’ll see more intelligent air compressors in machine tool environments. These devices can automatically adjust air pressure, monitor operating conditions, and issue early warnings before potential breakdowns, which ensures consistent, stable performance for machine tools.
Additionally, as IoT technology develops, the synergy between machine tools and air compressors becomes even more efficient. Some workshops already use compressed air monitoring systems that enable real-time tracking of air flow and pressure, keeping machine tools in optimal condition throughout production. This synergy not only enhances productivity but also optimizes energy usage, enabling truly green manufacturing.
Conclusion: The Indispensable Role of Air Compressors in Machine Tools
Air compressors are more than essential “assistants” to machine tools; they are integral to efficient industrial production. By providing power and support, compressed air simplifies and enhances various production tasks. As compressed air technology evolves, its role in manufacturing grows, offering new levels of versatility. Understanding how to select the right air compressor not only boosts your machine tools’ productivity but also brings greater energy savings and safety benefits to your workshop.
The seamless collaboration between air compressors and machine tools unlocks new possibilities for countless manufacturing enterprises. Whether you’re a workshop manager, a manufacturing engineer, or simply someone interested in machining, this powerful combination delivers robust support for your production and design needs.