In every workshop, there’s always that one machine known as the reliable “right-hand tool,” and the Knee Mill—this classic knee-type milling machine—fits that role perfectly. As an ideal choice for precision work and small-batch production, the Knee Mill meets diverse manufacturing needs with its impressive flexibility, high accuracy, and robust durability. This sturdy machine can handle complex part machining, quickly adapt to design changes, and offers straightforward operation at a reasonable cost—this is the true charm of the Knee Mill.
The Knee Mill refers to a traditional vertical milling machine with a unique “knee” structure. This knee, mounted on the machine’s column, moves vertically, with the worktable typically installed on it. Operators can precisely adjust cutting height along this vertical axis, allowing precise control over various machining processes.
Let’s dive into the advantages, operation tips, and selection points for this classic machine, and see how it continues to shine in modern manufacturing.
What is a Knee Mill?
A Knee Mill is a type of vertical milling machine named for its unique knee-shaped structure. The worktable on this machine can move vertically, allowing operators to adjust the height up and down. This height adjustment feature enables precise control over the cutting depth during machining.
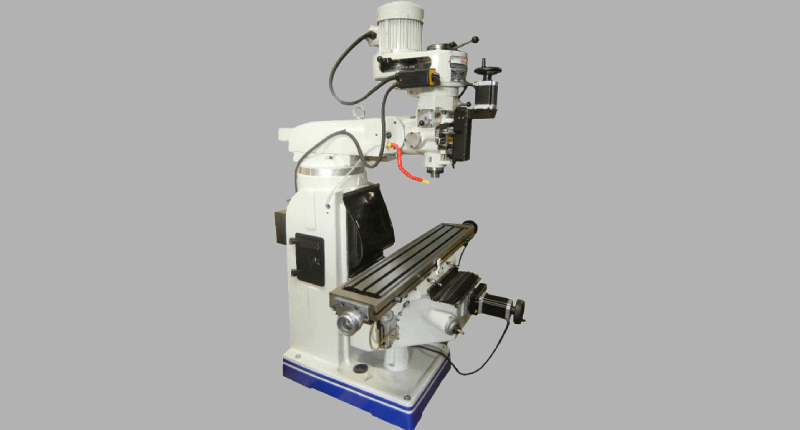
A typical Knee Mill includes the following main components:
- Spindle: Primarily rotates the cutting tool.
- Table: Holds the workpiece securely and moves horizontally.
- Knee: Mounted on the column, it supports the table’s vertical movement.
- Saddle: Connects the table and the knee, and usually moves back and forth, adding flexibility to the table’s range of motion.
Advantages of a Knee Mill
The Knee Mill has remained popular over time mainly due to the following structural and functional advantages:
- Versatility
The Knee Mill suits both light-duty machining and more demanding tasks. Its knee structure allows for adjustable table height, making it adaptable to various workpiece thicknesses and shapes. Plus, many Knee Mills enable the spindle to tilt, allowing for angled and sloped cuts. - High Precision
The design of the Knee Mill offers excellent precision control, particularly valuable for prototyping and small-batch production. The precise height adjustment feature helps operators achieve high levels of accuracy in their machining processes. - Ease of Operation
Operating a Knee Mill is straightforward, with simple mechanical controls and easy maintenance. Even those with limited experience can quickly learn to use it effectively, making it accessible for a wide range of users. - Cost-Effectiveness
Compared to more advanced CNC milling machines, the Knee Mill comes with lower purchase and maintenance costs. For small workshops and independent craftsmen, it provides a budget-friendly and efficient option.
How to Choose the Right Knee Mill
When selecting a Knee Mill, consider these key aspects based on your specific needs:
- Table Size
The size of the table directly affects the dimensions of the workpieces you can handle. For small-batch production and complex parts, a larger table offers more workspace. However, for small prototypes and light-duty machining, a smaller table brings greater flexibility and ease of use. - Spindle Horsepower
Higher spindle horsepower allows the machine to handle a wider variety of materials. Greater horsepower is suitable for machining tougher materials like steel and stainless steel, while lower horsepower spindles work best with lighter materials such as aluminum. - CNC Capabilities
Many modern Knee Mills include CNC (Computer Numerical Control) features, which are ideal for operations requiring high precision and repeatability. If your workshop needs to produce complex shapes or adhere to specific tolerances, opting for a Knee Mill with CNC functionality is advisable. - Brand and Parts Availability
Choosing a reputable brand, such as Bridgeport, ensures better quality and reliable after-sales support. Well-known brands typically offer easier access to replacement parts, making maintenance and repairs more convenient over time.
Common Applications of a Knee Mill
The Knee Mill’s versatility makes it widely useful across various applications:
- Prototyping: Ideal for machining small batches of prototype parts, it quickly adapts to changing design requirements.
- Repair and Remanufacturing: Useful for repairing and remanufacturing parts, particularly those with complex shapes or strict tolerance requirements.
- Light and Medium Cutting: Capable of handling light to medium material machining tasks, such as working with aluminum, plastic, and certain types of steel.
- Craft and Artisan Work: Due to its high precision, many artisans and small-scale manufacturers use it to machine intricate parts or create decorative items.
How to Use a Knee Mill: Operation Tips
When using a Knee Mill, the following tips can help improve machining efficiency and quality:
Alignment and Leveling
Ensure the machine is placed on a stable surface and properly aligned. Accurately leveling the table and spindle is essential for achieving precise machining results and maintaining high-quality work.
Choose the Right Cutting Tool
Select the appropriate tool based on the material you’re working with. For harder materials, such as steel, carbide tools work best. On the other hand, for aluminum and plastic, high-speed steel tools provide better results and efficiency.
Regular Maintenance
Routinely lubricate the guideways and spindle, and keep the machine clean to extend its lifespan and maintain stable performance. Additionally, check and adjust the knee structure’s screws to prevent any looseness that could impact accuracy.
Monitor Cutting Speed
Controlling the cutting speed is crucial with a Knee Mill. Slower speeds work well for hard materials, while softer materials, like aluminum, allow for faster speeds. Be mindful, as overly high or low speeds can lead to increased tool wear or a rough surface finish on the workpiece.
The Future of the Knee Mill
As automation advances in the manufacturing industry, the Knee Mill continues to evolve with upgrades and innovations. More and more Knee Mills now include CNC capabilities, meeting the high precision and complexity demands of modern production environments. In the future, Knee Mills integrated with automation and smart technology will likely play an even more crucial role in small to medium-sized production settings, offering flexible and efficient solutions to support a wide range of manufacturing needs.
Conclusion: The Modern Value of a Classic Machine
The Knee Mill stands as a classic in the world of vertical milling machines. Its versatility and cost-effectiveness make it an indispensable part of the manufacturing industry. Whether you’re focused on precision machining, prototyping, or repair and remanufacturing, the Knee Mill delivers reliable performance and efficient productivity. Selecting the right Knee Mill and using it properly will help you achieve your machining goals and unlock greater production potential in your workshop.
Whether you’re an experienced operator or new to the Knee Mill, this machine offers endless possibilities. If you have further questions about choosing used machine tools, we’re here to offer professional advice and support. Visit Minnuo Group’s website, and let us help you find the perfect equipment to bring your manufacturing dreams to life.