Long ago, our ancestors discovered how to combine mechanical movement with design. This innovation led to the creation of a new manufacturing method known as five-axis machining. We have evolved from simple machining techniques to today’s efficient automation. Each innovation reshapes the rules of the industry. Now, it is undoubtedly at the core of many products in our lives. Whether it is cars, airplanes, or buildings, all of this is thanks to our continuous pursuit of machining technology. This pursuit allows our industrial equipment to operate efficiently and enables a flow of innovative products.
Five-axis machining is an advanced technology in modern manufacturing. It involves five independent motion axes, which allow the machine to move in multiple directions at the same time. Specifically, the five axes usually include three linear axes: the X, Y, and Z axes, and two rotary axes: the A and B axes. The combination of these axes allows tools to cut at complex angles and along intricate paths. This capability achieves higher precision and enables the machining of more complex shapes. Through it, manufacturers can complete multi-faceted cutting in a single setup. This process significantly improves production efficiency and machining quality.
Today, let us explore each axis in five-axis machining and discuss their roles.
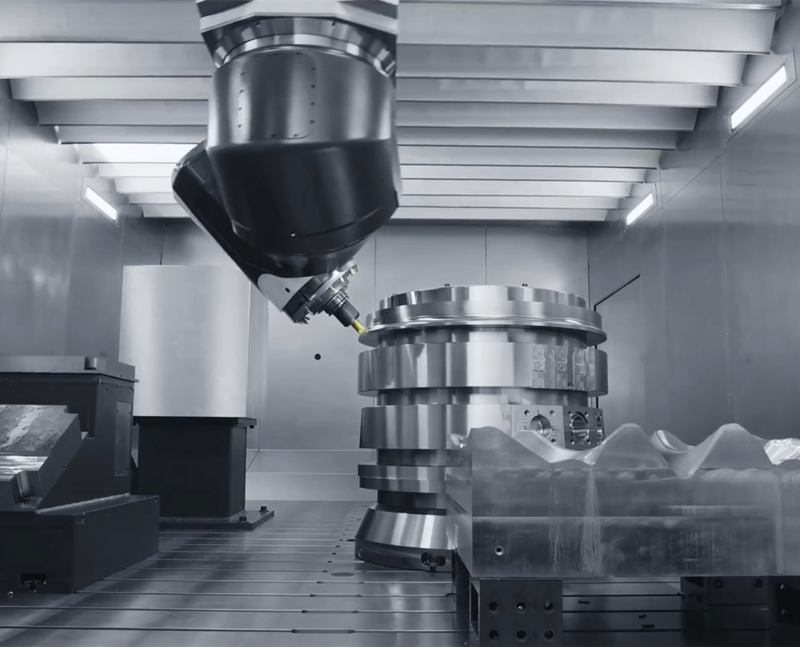
What is five-axis machining?
In simple terms, it refers to a machine tool that can move and rotate the tool or workpiece in five different directions at the same time. Traditional three-axis machining (X, Y, Z) usually can only move within a single plane. However, five-axis machining adds two rotary axes to this setup. This addition makes machining more flexible and suitable for various complex shapes and surfaces.
The main advantages of five-axis machining are that it allows for the completion of multiple angles in one setup. This capability significantly enhances precision and efficiency.
What are the five axes?
In five-axis machining, there are three linear axes and two rotary axes:
- X Axis: This axis usually moves left and right. It represents the movement of the workpiece or tool in the horizontal direction.
- Y Axis: This axis moves up and down. It allows the workpiece or tool to move in the vertical direction.
- Z Axis: This axis moves forward and backward. It is perpendicular to the X and Y axes and represents movement in the depth direction.
- A Axis: This axis typically rotates around the X axis. It enables the tool or workpiece to rotate around the horizontal axis.
- B Axis: This axis rotates around the Y axis. It allows the workpiece or tool to rotate around the vertical axis.
The introduction of the A and B axes allows the tool to approach the surface of the workpiece more freely without being limited by angles. This feature makes it especially suitable for machining curves and complex shapes. Now, let’s explore how these axes work together and discuss their individual characteristics.
X, Y, Z Axes: The Foundation of Three Axes
In all machining operations, the X, Y, and Z axes are the most fundamental three axes. They define the basic directions of movement in three-dimensional space. The three axes usually perform simple cutting and drilling in a plane. However, when machining complex surfaces or needing to contact the workpiece from multiple angles, the limitations of the three axes become apparent. Five-axis machining builds on the three axes by adding rotary axes, which further expands the possibilities of machining.
A Axis and B Axis: The Flexibility of Rotary Axes
The introduction of the A and B axes allows five-axis machining centers to tilt, rotate, and even make multi-angle contacts with the workpiece. This flexibility is particularly important when machining complex aerospace parts, medical devices, or automotive components. For example, when machining a turbine blade for an aircraft, the tool needs to work from multiple angles. The flexibility of the A and B axes enables the tool to easily reach every surface that requires machining.
- A Axis: The A axis rotates around the X axis. It allows the workpiece or tool to adjust angles with 360 degrees of freedom. For instance, when machining cylindrical objects, the A axis helps the machine easily work around various angles of the object.
- B Axis: The B axis rotates around the Y axis. It further enhances the tool’s freedom, especially in machining complex shapes. The B axis is commonly used for angled machining. It ensures that more angles can be achieved without moving the workpiece.
Advantages of Five-Axis Machining
The advantages of five-axis machining lie not only in its flexibility but also in its efficiency and precision. Because it can complete machining from multiple angles in a single setup, it reduces the need for repeated fixtures. This reduction saves time and significantly minimizes errors. These benefits make five-axis machining widely used in high-precision industries such as aerospace, medical, and automotive.
- Increased Production Efficiency: Traditional machining methods usually require multiple setups and realignments. However, it allows for the completion of all angles in one setup. This capability significantly shortens machining time.
- Reduced Fixture Usage: Five-axis machining decreases the errors caused by multiple setups and repositioning. This is especially beneficial when machining large or complex workpieces, greatly enhancing precision.
- Precision Machining: For complex surfaces and irregular parts, it provides a high degree of flexibility and accuracy. It can achieve surface finishes and details that traditional three-axis machines cannot.
How to Choose the Right Five-Axis Machining Center
Different configurations and designs of five-axis machining centers suit various machining needs. Some five-axis machines are ideal for mass production of precision parts, while others focus more on flexibility and versatility. When selecting it’s center, consider the following points:
- Machining Materials: Different five-axis machines have varying capabilities for machining hard metals, alloys, and composite materials. Ensure that the chosen equipment is suitable for the type of material you will be machining.
- Machining Precision: Choose the appropriate machine configuration based on the precision requirements of the workpiece. Some high-end five-axis machines offer better precision control and tool life management features.
- Table Design: Select a worktable that matches the size and structure of the workpiece. This selection ensures stability and safety during the machining process.
Conclusion
Five-axis machining is not just a technical breakthrough; it has become an essential part of modern manufacturing. From the basic X, Y, and Z axes to the flexible A and B rotary axes, each axis provides greater freedom for machining centers. As technology advances, five-axis machining centers continue to improve in intelligence and automation, bringing higher production efficiency and precision to various industries. Whether you are an engineer interested in five-axis machining or a business owner planning to invest in a five-axis machine, I hope this article has given you a deeper understanding of the “axes” in five-axis machining.
The future of five-axis machining is full of endless possibilities. It will continue to bring new heights and more innovations to the manufacturing industry. If you are looking for high-quality five-axis machining centers, feel free to contact Minnuo Group. We are dedicated to providing advanced and reliable machining equipment to help you stand out in the competitive market.