In today’s fast-paced and innovative world, from cars to smartphones to complex architectural designs, every product you can imagine relies on powerful behind-the-scenes technology. Two of the most essential technologies in this process are CAD (Computer-Aided Design) and CAM (Computer-Aided Manufacturing). Though they seem closely related, CAD and CAM play distinct roles at different stages of production.
So, what are the key differences between CAD and CAM? And how do they work together to drive the process from sketch to finished product? CAD and CAM each tackle different parts of the design and manufacturing process, with one common goal: using computer technology to boost efficiency. CAD focuses on the creative and design side, helping designers create virtual models. CAM, on the other hand, concentrates on turning these virtual models into physical objects, making sure the designs come to life through manufacturing processes. For any modern production system, CAD and CAM are both crucial.
Let’s explore the differences between CAD and CAM from several angles, to help you understand how they work together in industrial design and production.
Definition and Function Differences
CAD: Computer-Aided Design
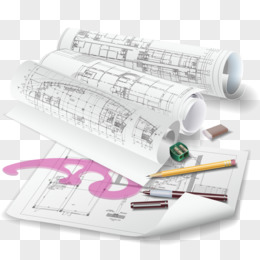
CAD is a digital tool used for designing and creating products. It allows engineers and designers to use software to create precise 2D or 3D models, replacing traditional hand-drawn blueprints. With CAD, designers can visualize the structure, dimensions, materials, and functions of a product. They can also make changes, optimize designs, and even simulate real-world tests like stress analysis or fluid dynamics. The main functions of CAD include:
- Product design: CAD helps designers create the shape and structure of a product in 2D or 3D.
- Modification and optimization: Designers can modify the design at any time and make real-time adjustments and improvements.
- Simulation and analysis: CAD allows for simulation tests, such as strength testing and thermal analysis, to ensure the design is practical.
- Generating drawings: CAD software can automatically produce the technical drawings and files needed for manufacturing.
By offering these features, CAD becomes an essential tool for creating and refining designs before moving into production.
CAM: Computer-Aided Manufacturing
CAM is a technology used to control the manufacturing process. After the design phase is completed, CAM takes the CAD-generated design and translates it into specific manufacturing steps, guiding CNC machines or other automated equipment to produce the product. CAM software generates toolpaths and provides detailed parameters like cutting speed and depth. Its main functions include:
- Manufacturing planning: CAM converts the CAD model into machine-readable code (G-code) that directs the operation of production equipment.
- Toolpath generation: It creates optimized toolpaths based on design requirements to improve machining efficiency and precision.
- Simulation and correction: CAM simulates the machining process before actual cutting begins, helping to prevent collisions and machining errors.
- Automated production: It integrates with CNC machines to enable automated and mass production.
These functions make CAM essential for turning designs into physical products with high precision and efficiency.
Workflow Differences
The workflows of CAD and CAM have different focuses, and each plays a key role at different stages of design and manufacturing.
- CAD stage: Engineers first use CAD software for designing and optimizing the product. With design tools, they create the product’s geometry, dimensions, and other attributes. This stage emphasizes creativity and design.
- CAM stage: Once the design is complete, CAM takes over the model and uses computer programs to control the actual manufacturing equipment. This stage focuses more on execution and production, ensuring the product is manufactured efficiently and accurately according to the design specifications.
In other words, CAD focuses on solving design problems, while CAM handles the process of turning the design into real-world production.
Roles and Collaboration in the Workflow
- Role of CAD
In the manufacturing process, CAD is typically involved in the early design phase. Designers and engineers use CAD tools to conceptualize, prototype, and optimize products, focusing on virtual modeling and testing. In a typical project, CAD engineers closely collaborate with other departments, such as production, marketing, and quality control, to ensure the design meets functional requirements and is feasible for manufacturing. - Role of CAM
CAM plays its role in the manufacturing preparation stage, after the design is finalized. It acts as a bridge between CAD and manufacturing by converting designs into specific machining tasks. The job of CAM engineers is to optimize the manufacturing process, ensuring that production equipment can create the desired product efficiently, safely, and cost-effectively. CAM engineers also work closely with factory operators and CNC programmers to solve real-world manufacturing issues.
This teamwork ensures smooth transitions from design to production, making the entire process more efficient.
Different Users
- CAD users: CAD software is mainly used by designers, engineers, and architects. Their job is to transform a product or building concept into a detailed design. For these professionals, precise models, flexible modifications, and efficient simulation testing are their core needs.
- CAM users: CAM software is primarily used by manufacturing engineers and CNC operators. Their focus is on how to efficiently produce the design. Key details like tool selection, machining speed, and toolpath generation are the main concerns for CAM users.
Each group has distinct responsibilities, but both are essential for turning ideas into reality.
Technical Relevance
Although CAD (Computer-Aided Design) and CAM (Computer-Aided Manufacturing) serve different purposes and users, they are often closely related. In modern manufacturing, these two technologies frequently connect seamlessly through integrated CAD/CAM software. After the design is completed, CAM can directly read the data from the CAD files. This process eliminates the need for remodelling, and it ensures consistency between design and manufacturing.
Such integrated software significantly reduces human errors. Additionally, it improves efficiency and shortens the time from design to finished product. Therefore, using CAD/CAM software together benefits manufacturers by streamlining the workflow and enhancing overall productivity.
Examples of Common Software
Some industry-standard CAD and CAM software can help us better understand their differences in practical applications.
- CAD Software: Common CAD software includes AutoCAD, SolidWorks, CATIA, and Creo. These programs find widespread use in various industries, such as mechanical design, architecture, and electronic product design.
- CAM Software: CAM software includes Mastercam, Fusion 360, and Edgecam. These programs usually connect with CNC (Computer Numerical Control) machines, and they help automate the manufacturing process.
Some software provides both CAD and CAM functions. For example, Autodesk’s Fusion 360 offers integrated capabilities. This type of software is especially popular in small manufacturing businesses because it allows for a complete workflow from design to manufacturing in one platform.
Application Scope in Different Industries
CAD Applications
CAD has a broad range of applications and covers nearly all industries that involve design:
- Mechanical Engineering: CAD is used for designing parts, machinery, and tools.
- Architectural Engineering: In building design and civil engineering, CAD helps create architectural blueprints, interior designs, and urban planning.
- Electronic Products: CAD is essential for designing circuit boards and product enclosures.
- Fashion and Jewelry Design: CAD assists in creating design models for clothing and jewelry in the fashion industry.
CAM Applications
CAM mainly focuses on industrial manufacturing, especially in sectors that require high precision and automation:
- Automotive Manufacturing: CAM is used for machining complex parts such as engines and chassis.
- Aerospace: CAM helps manufacture high-precision components, including airplane engines and fuselages.
- Mold Manufacturing: The mold industry relies on CAM technology to achieve high precision and complex structures.
- Medical Devices: CAM plays a critical role in manufacturing precise medical equipment, including surgical instruments and implants.
Conclusion
CAD and CAM not only differ in functionality and application but also focus on various aspects such as data processing, skill requirements, time costs, and industry applications. As essential components of the manufacturing industry, CAD and CAM each handle different stages of design and manufacturing. With the advancement of technology, the integration of CAD and CAM has become increasingly close, making them indispensable tools for modern manufacturing enterprises.
In everyday work, understanding the distinctions and collaborative methods between CAD and CAM is crucial for engineers, designers, and manufacturing professionals. A good design is not only creative but also must be produced efficiently and accurately. This highlights the value of combining CAD and CAM in the manufacturing process.