Laser cutting, as a modern precision processing technology, is quickly changing the rules in manufacturing and processing industries. From metal sheets to plastic materials, laser cutting can deliver efficient and precise cuts. But when faced with various processing methods, is laser cutting the best option? The answer depends on several factors, like process costs, precision requirements, material characteristics, and production volume. Knowing the pros and cons of laser cutting helps companies and technicians make smart choices and avoid costly mistakes from choosing the wrong process.
When companies consider using laser cutting, they often face a balance between efficiency and budget. Laser cutting’s high precision and automation make it ideal for high-quality products and complex requirements, but the costs are often higher. Especially for metal materials or intricate geometries, finding the right balance between equipment investment and output efficiency is a key challenge.
This article will dive into the advantages and disadvantages of laser cutting, examining factors like precision, costs, and operational flexibility. We’ll also share suggestions for different use cases, helping you find the best cutting method for your production needs.
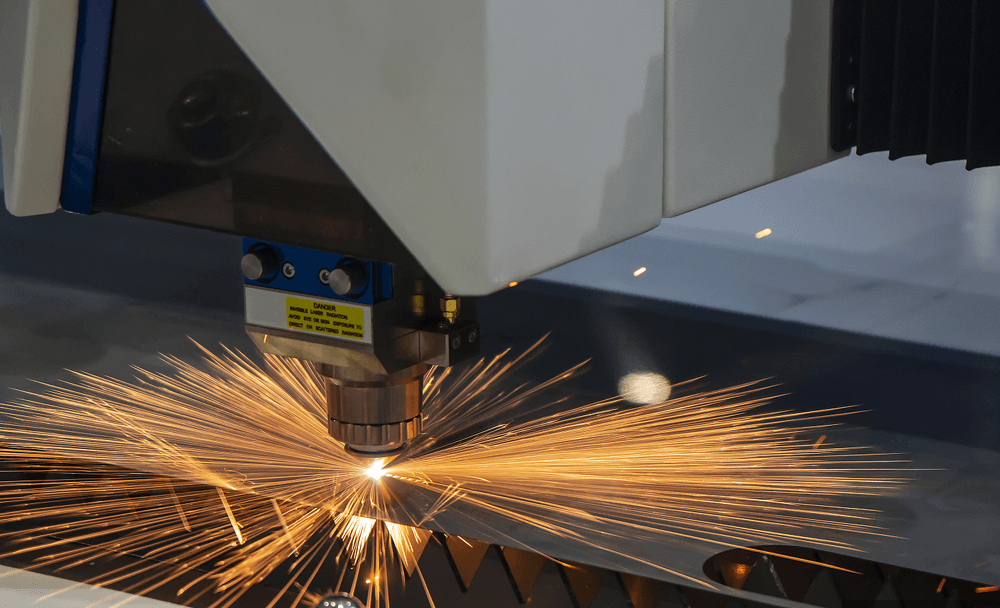
Why Is It So Popular?
High Precision and Clean Cuts
Laser cutting stands out not just because it’s “fast,” but because it’s “fast and precise.” By focusing the laser beam’s high heat, materials can be melted or vaporized instantly, producing smooth, burr-free edges. For precision manufacturing or complex designs, laser accuracy is almost unbeatable.
Non-Contact Processing, Less Material Deformation
It is a non-contact process, meaning the cutting head doesn’t physically touch the material, which helps prevent surface damage. This feature is a major advantage for delicate materials, like ceramics, or those requiring surface integrity.
High Automation and Flexibility
Modern laser cutting machines can integrate with CAD/CAM systems, automating the entire process from design to cut, and reducing manual errors. It also adapts well to various material shapes and thicknesses, accommodating a range of materials like metals, plastics, and wood. This adaptability is ideal for small-batch, customized production.
Efficient Energy Usage
Compared to traditional cutting methods, it is more energy-efficient. Especially for thin materials, laser cutting significantly speeds up the process, reduces waste, and improves material utilization.
What Are the Potential Limitations of Laser Cutting?
High Equipment and Maintenance Costs
Despite its impressive capabilities, it doesn’t suit every application. High-power laser cutting machines come with high purchase costs, and maintenance can be costly too. Components like lasers, lenses, and nozzles need regular care to ensure cutting quality, which can be a significant expense for smaller shops with limited budgets.
Limited Efficiency on Thick Materials
It shines with thin materials, but its speed and quality decrease when working with thicker materials (typically over 20 mm). For companies with high demands for thick plate processing, considering alternatives like plasma or water jet cutting may offer better efficiency and results.
Heat-Affected Zone Issues
Laser cutting generates high temperatures, and while precision controls reduce the heat-affected zone, sensitive materials may still experience slight changes in edge structure that impact mechanical performance. This factor becomes especially important for precision components used in industries like aerospace or medical manufacturing.
Material Limitations
It has difficulty with certain materials, such as highly reflective metals or ceramics, which may reflect the laser and disrupt cutting or even damage the equipment. For these cases, additional auxiliary gases or specific laser wavelengths may be necessary to achieve suitable results, increasing both complexity and cost.
Laser Cutting Application Suggestions
Precision Parts and Custom Production
For industries with strict size requirements, like automotive, electronics, and precision instruments,it offers clear advantages in precision. It ensures consistent, high-quality parts, making it a top choice for such applications. Here, opting for lower-power fiber laser machines can help optimize costs.
High-Volume Thin Sheet Processing
If a company’s primary need is high-volume thin sheet processing, as in sheet metal manufacturing, laser cutting’s speed and energy efficiency can significantly boost production. For this use, choosing mid- to high-power laser machines can enhance both cutting speed and productivity.
High-Quality Non-Metal Cutting
For industries like advertising and decorative design that work with non-metal materials, Laser Machining enables complex, high-quality shapes. It is particularly effective with materials like acrylic and wood, producing cuts without dust or contact damage. When non-metal cutting is the primary focus, a CO₂ laser machine specifically designed for this purpose may be ideal.
Thick or Heat-Resistant Material Processing
For cutting thicker metal plates (over 20 mm) or heat-resistant materials, such as those used in aerospace, companies can consider alternative methods. Plasma or waterjet cutting, for instance, often perform better for thicker materials, while laser cutting can serve as a complementary tool for specific tasks.
Investment Cost
Laser cutting machine prices vary widely, depending mainly on laser type, power, brand, and feature configurations. Typically, small, low-power fiber laser machines start around $10,000 to $50,000, which works well for cutting thin metals or non-metal materials. Medium-power laser machines, suitable for thicker materials, range from $50,000 to $200,000. High-power industrial laser machines, designed for thick metal plates and large-scale processing, often cost over $200,000, with some models reaching upwards of $500,000. Furthermore, customization options, automation features, and after-sales services can also impact the price.
Conclusion
Laser cutting is like a “magic pen” in manufacturing, offering both speed and precision while making complex cuts easy to handle. Whether you need precision parts or high-volume production, it can meet these demands and make your products more competitive. Of course, when choosing laser cutting equipment, it’s essential to consider your budget and needs to find the right power and type to fully unlock its advantages. With the growth of smart manufacturing, it will only become more widely used. If you’re looking to make production more efficient and worry-free, it’s definitely a technology worth exploring.