In the field of 3D printing, choosing the right materials impacts not only the print quality but also the performance and durability of the final product. Whether you’re printing detailed models, producing engineering-grade parts, or creating components for long-term outdoor use, different materials offer distinct advantages. With such a wide variety of 3D printing materials available, selecting the most suitable option for your project can be challenging, especially when considering budget, environmental conditions, or complex design requirements.
Among the many materials, PLA, ABS, and PETG are the most common. Each brings unique benefits: PLA is easy to print and eco-friendly, making it ideal for cost-effective models; ABS offers toughness and durability, perfect for engineering applications; and PETG provides durability and UV resistance, making it a top choice for outdoor parts. Beyond these basics, materials like nylon, TPU, and carbon-fiber composites are also popular among professionals for their suitability in high-strength, flexible, or rigid components. Additionally, water-soluble PVA and removable HIPS support materials play a crucial role in complex print designs.
In the following sections, we’ll break down the characteristics, applications, and recommendations for these essential 3D printing materials. This guide will help you make informed choices, streamline your material selection process, and effectively tackle various printing challenges, leading to the best possible results.
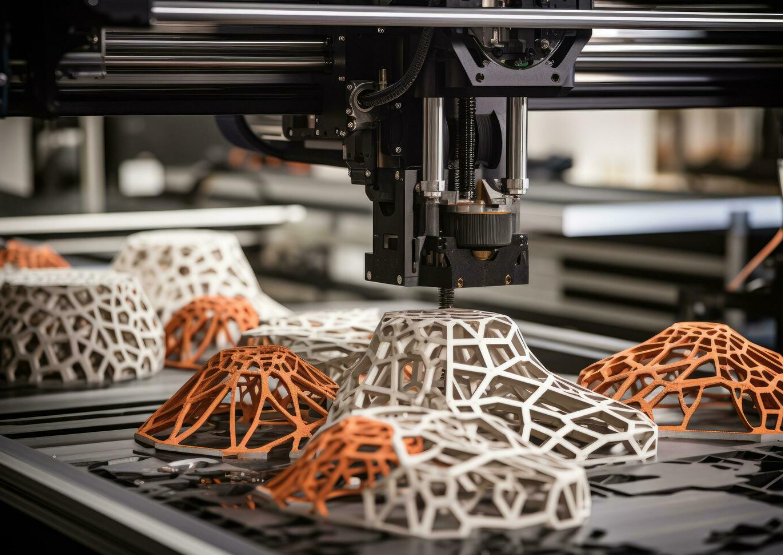
Common Types of 3D Printing Materials
1. PLA (Polylactic Acid) – Ideal for Beginners
PLA, a bioplastic made from cornstarch, is perfect for creating affordable prototypes and display models.
- Printing Temperature: 130–180°C
- Advantages: Easy to print, eco-friendly, and food-safe
- Disadvantages: Limited durability and poor UV resistance, so it has limited use cases
- Typical Applications: Models, educational tools, and art pieces
- Best For: 3D printing beginners and those who need quick prototype designs
2. ABS (Acrylonitrile Butadiene Styrene) – For Engineering Applications
ABS is highly durable, making it an excellent choice for projects with high strength requirements.
- Printing Temperature: 220–250°C
- Advantages: Impact-resistant, chemically resistant, and suitable for outdoor use
- Disadvantages: Higher printing difficulty and requires a high-temperature environment
- Typical Applications: Tools, mechanical parts, and toys
- Best For: Engineers and manufacturers who need strong, durable parts
3. PETG (Polyethylene Terephthalate Glycol-modified) – For High-Performance Applications
PETG combines the easy printability of PLA with the durability of ABS, making it ideal for outdoor applications.
- Printing Temperature: 230–250°C
- Advantages: Chemical-resistant and UV-resistant
- Disadvantages: Prone to stringing and requires a clean printing environment
- Typical Applications: Outdoor decor and household items
- Best For: Users looking for durability and outdoor applications
Recommended Materials for Different Applications
Each 3D printing material offers unique benefits, so here are material recommendations based on specific application needs to help users make better choices.
1. Rapid Prototyping
Models for rapid prototyping often prioritize low cost and speed.
- Recommended Material: PLA
- Reason: PLA is affordable and easy to use, making it ideal for simple display models.
2. Outdoor and High-Strength Parts
Parts that need long-term outdoor exposure should use materials that are UV-resistant, heat-resistant, and wear-resistant.
- Recommended Materials: PETG, ABS
- Reason: PETG offers strong UV resistance, while ABS is impact-resistant, making both suitable for durable parts.
3. Support Materials for Complex Structures
For models with complex geometries, choosing the right support material is essential.
- Recommended Material: PVA (Water-Soluble Polyvinyl Alcohol)
- Reason: PVA dissolves in water, which makes it easy to remove support structures without damaging the finished model.
4. High-Precision and Industrial Parts
Industrial or high-precision parts need materials with high strength and dimensional stability.
- Recommended Materials: Nylon, Carbon Fiber-Reinforced Material
- Reason: Both materials provide excellent rigidity and wear resistance, ideal for structural components.
Key Factors for Choosing 3D Printing Materials
When selecting 3D printing materials, it’s essential to consider not only their properties but also balance several factors based on the specific application needs.
1. Match Material Properties to Application
The physical properties of each material determine where it’s best used, so prioritize the functional needs of the final product when choosing. For example:
- For high-strength parts, ABS or Nylon is recommended.
- For prototypes requiring precision and aesthetics, PLA or PETG works well.
2. Printing Difficulty and Cost
More complex materials often come with higher printing difficulty and specific printing conditions. For instance, ABS and PC require a heated bed, while carbon fiber-reinforced materials can clog nozzles. Therefore, think about equipment requirements and budget before selecting these materials.
3. Environmental Factors
Some materials are sensitive to humidity, which can cause instability in print quality. For instance, Nylon and TPU need to stay dry to prevent printing defects. Additionally, ABS and HIPS release odors during printing, so ensure a well-ventilated space for these materials.
PLA vs. ABS vs. PETG: Comparison of Three Common Materials
Here is a comparison of PLA, ABS, and PETG to help users better understand the differences among these three materials:
Property | PLA | ABS | PETG |
Tensile Strength | High (65 MPa) | Medium (40 MPa | Medium (53 MPa) |
Rigidity | High | Medium | Medium-High |
Ease of Use | Easiest | Requires high-temperature equipment | Easy to print, no warping |
Chemical Resistance | Average | Good | Excellent |
Recommended Applications | Rapid prototyping, display models | Industrial parts, outdoor tools | Outdoor decor, functional models |
This comparison highlights how each material serves different needs. For example, PLA offers simplicity and is ideal for prototypes, while ABS works well in industrial applications, and PETG excels in outdoor and functional projects.
Practical Tips for Choosing 3D Printing Materials
Define Budget and Requirements: Clarifying the budget and specific needs of the printed object is essential. For example, if you’re only creating a simple display model, PLA offers great cost-effectiveness. For parts that need high durability, ABS or Nylon would be better choices.
Test Small Samples and Optimize Parameters: When working with new materials, start by printing a small sample to test temperature, flow rate, and form. This approach helps you avoid issues when scaling up to larger prints.
Manage Storage and Environment: Materials that easily absorb moisture, like Nylon, TPU, and PVA, need dry storage to prevent defects from humidity. For ABS and HIPS, use a well-ventilated space during printing to ensure safety.
Choose Reliable Brands: When it comes to material stability and quality, trusted brands tend to offer better results. High-quality materials play a key role in achieving consistent print quality and durability in any 3D printing project.
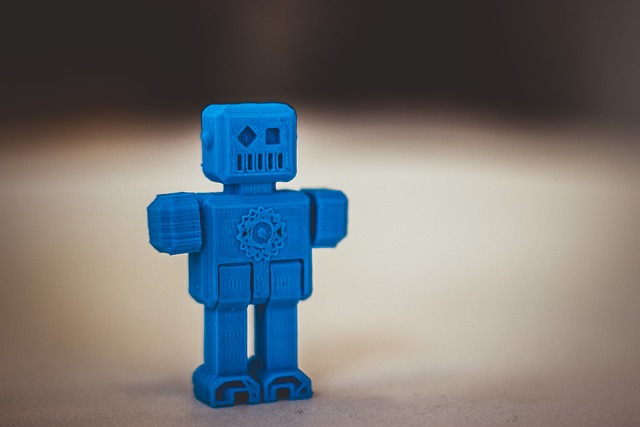
Frequently Asked Questions
1. Which is better, PLA or ABS? How should I choose?
PLA and ABS are the most common 3D printing materials, but they suit different applications. Think about the printed object and its final use.
- PLA is great for models, rapid prototypes, and display items. It’s simple to use and good for low-cost printing.
- ABS is more durable, ideal for impact-resistant and wear-resistant engineering parts, though it’s harder to print and requires a heated bed and proper ventilation.
Tip: If you’re a beginner, start with PLA. For more durable parts, go with ABS.
2. Why does ABS warp and crack during printing?
ABS tends to shrink while cooling, which leads to warping and cracking. This happens because the material cools unevenly from a high temperature.
- Solution: Make sure to heat the print bed to the right temperature (usually 95–110°C) and, if possible, use an enclosed 3D printer to maintain stable temperatures.
- Another Tip: Add a “brim” around the model to increase stability, or use ABS-specific adhesive for better adhesion.
3. Is PETG or PLA better for outdoor use?
PETG works better outdoors because it resists UV and chemicals, making it more durable than PLA. PLA can become brittle with prolonged outdoor exposure, especially in sunlight.
Tip: For outdoor projects, PETG is a better choice since it won’t degrade as quickly as PLA.
4. How can I prevent nylon from absorbing moisture?
Nylon is highly absorbent, and moisture can cause bubbling and stringing during printing, affecting print quality.
- Solution: Dry nylon in a dry box or oven at a low temperature (around 60°C) for a few hours before printing, and use a desiccant during printing.
- Storage Tip: After printing, store nylon in a sealed container with a desiccant to keep it dry.
5. Can carbon fiber-reinforced materials damage the nozzle?
Yes, carbon fiber-reinforced materials can wear down regular brass nozzles quickly because the carbon fibers are very hard and abrasive.
- Solution: Use a wear-resistant nozzle, like one made of hardened steel or tungsten carbide, to extend nozzle life. Tip: Check the nozzle regularly for wear and replace it as needed to ensure high print quality.
6. What’s the difference between TPU and TPE?
Both TPU (thermoplastic polyurethane) and TPE (thermoplastic elastomer) are flexible materials, but their elasticity and hardness vary.
- TPU is relatively harder and more resilient, ideal for high-elasticity items like protective cases or shock-absorbing parts.
- TPE is softer, suitable for applications needing more flexibility, like comfortable grips or soft padding.
Tip: For greater hardness and abrasion resistance, choose TPU. For higher softness, go with TPE.
7. How should I choose 3D printing support materials?
Support materials are essential for complex structures to hold overhangs and intricate parts, with PVA and HIPS being the most common options.
- PVA (Polyvinyl Alcohol): Water-soluble and works well with PLA; easy to remove, though more expensive.
- HIPS (High Impact Polystyrene): Compatible with ABS and dissolves in D-limonene; requires good ventilation during printing.
Tip: Consider compatibility with the main material and the ease of post-processing when choosing a support material.
8. How do I handle printing in a humid environment?
In high humidity, some materials (like Nylon, TPU, and PVA) absorb moisture, which can negatively impact print quality.
- Solution: Store materials in a dry box or use materials with low moisture absorption, like PLA or PETG. Tip: If using absorbent materials in a humid environment, keep exposure to air as brief as possible.
9. What common issues occur with PVA support material?
PVA is prone to absorbing moisture, which can lead to printing interruptions and quality issues.
- Recommendation: Store PVA in a dry container and keep it dry while printing. After printing, immerse the model in water to easily remove the support.
Choosing the right 3D printing materials is a crucial step to ensure both print quality and durability. Our company offers a wide range of high-quality materials, along with an experienced team of experts dedicated to providing tailored material recommendations and print solutions for each project. With our all-in-one service, you can easily access instant quotes and professional support, so every printing need is met with efficiency and reliability.