In today’s manufacturing industry, thread milling has gradually become an essential machining technique. In sectors like aerospace and automotive, the high precision and efficiency of thread milling make it a “hardcore” choice for quality thread production. Compared to traditional thread turning, thread milling handles more complex workpieces and provides significant advantages in machining speed and tool life. For companies pursuing exceptional machining results, choosing the right thread milling equipment is undoubtedly crucial for improving both product quality and production efficiency.
However, the variety of thread milling equipment on the market can be overwhelming. Different machines vary in tool compatibility, feed methods, suitable materials, and machining precision. For manufacturers, selecting the right thread milling machine can be challenging. Some companies focus on high precision, while others look for a balance between machining efficiency and ease of use. Plus, various materials and thread specifications require specific machine capabilities. So, before making a purchase, it’s essential to understand the technical features and performance of each option.
To address these issues, this article explores the principles of thread milling, equipment types, and application scenarios. It provides a scientific guide to help you choose the most suitable thread milling equipment, empowering you to achieve more efficient and precise production.
What is Thread Milling? — A Precision Tool for High-Accuracy Thread Machining
It uses a rotating thread mill that feeds along the thread axis, enabling precise thread cutting. Unlike traditional thread turning, thread milling works especially well with high-hardness materials and larger-diameter threads. Compared to conventional methods, it offers notable advantages in machining speed, precision, and tool life.
Applications of Thread Milling
Thread milling finds extensive use in demanding industrial sectors, especially in these scenarios:
- Large-Diameter Threads and High-Hardness Materials: Ideal for materials like titanium alloys, stainless steel, and hardened steel.
- Complex Threading: Suitable for multi-start threads, tapered threads, and fine precision threads.
- High-Volume Production: With high efficiency, it handles large-scale, precision production with ease.
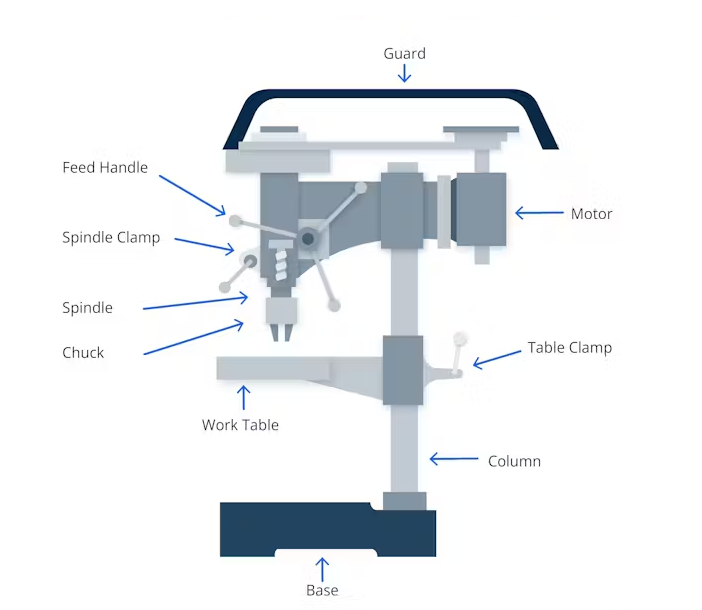
Types of Thread Mills
Choosing the right thread mill is essential for achieving high-precision thread milling. Based on different machining needs, here are the main types of thread mills:
- Single-Point Thread Mills
Single-point thread mills work well for smaller production runs, especially when machining large-diameter or deep threads. These mills have a simple design, allowing high flexibility and easy adjustment. - Multi-Point Thread Mills
Multi-point thread mills remove material from multiple thread teeth in a single feed, making them highly efficient for large-scale production. With multiple cutting edges, they excel in shorter thread machining and help reduce production time significantly. - Solid Carbide Thread Mills
Made from durable carbide, solid carbide thread mills are ideal for high-hardness materials, offering excellent wear resistance. These mills maintain precise cutting performance and work well for challenging materials like stainless steel and titanium alloys. - Indexable Thread Mills
With replaceable inserts, indexable thread mills meet various pitch and diameter requirements, perfect for high-hardness materials in large production runs. Replacing inserts helps extend tool life and reduce costs, making them economically beneficial. - Insert Thread Mills
Insert thread mills allow insert changes during operation, adapting easily to different thread specifications. These mills suit multi-spec, varying diameter thread production, making them especially flexible in batch production.
When selecting a thread mill, consider factors like workpiece material, thread specification, and production volume. Our thread milling equipment supports a wide variety of tool types to meet the diverse needs of each user.
Why Choose Thread Milling? — Advantages Over Traditional Machining
When selecting a threading method, many users consider the balance of efficiency, precision, and cost. Thread milling, with its unique process, offers several advantages in these areas:
- High Precision: It keeps the tool and workpiece in a stable position, ensuring higher cutting accuracy. It’s especially suitable for high-precision internal and external threading.
- Increased Efficiency:It usually completes in a single pass, maintaining high efficiency even when processing large-diameter and deep threads.
- Extended Tool Life: It distributes heat evenly during cutting, reducing excessive wear and extending tool life. This minimizes replacement frequency and lowers costs.
- High Versatility: With CNC programming adjustments, it easily handles threads with varying pitches, diameters, and materials, making it ideal for customized machining needs.
How to Choose the Right Thread Milling Equipment — A Practical Buying Guide
When selecting it, these steps can help you identify the best configuration based on your production needs.
Step 1: Define Thread Type and Size Requirements
Different thread types and sizes require specific capabilities from milling equipment. For example, large-diameter threads and multi-start threads need machines with higher power and rigidity, while smaller pitch or precision threads demand a high-accuracy control system. Identifying these needs helps narrow down the equipment options.
- Tip: List the thread specifications you need, including diameter, pitch, and type, to choose the appropriate machine.
Step 2: Assess Equipment Precision and Efficiency
Machining precision and efficiency directly impact the final product quality and production costs. For facilities with high production volumes, prioritize machines with automatic feed and high-speed milling. Efficient equipment significantly reduces processing time and boosts production rates.
- Tip: Choose models with automated control and high feed speed based on your production volume to maximize efficiency.
Step 3: Consider Tool Selection and Flexibility
Tools play a critical role in thread milling, as they determine the equipment’s versatility and cost-effectiveness. High-quality tool designs reduce wear and extend lifespan. Multi-functional equipment that supports various tool specifications can handle a range of thread types and sizes.
- Tip: Select equipment compatible with multiple tool types to easily switch between different processing needs. Our thread milling machines offer diverse tool configurations, making them adaptable to various production requirements.
Step 4: Analyze Long-Term Maintenance Costs
Maintenance costs are often overlooked when choosing equipment. High-quality machines generally perform better in terms of maintenance intervals and lifespan, helping save on long-term maintenance expenses. Choosing a supplier with solid after-sales support also ensures smooth production.
- Tip: Fully understand the maintenance needs and tool replacement cycle of the equipment, and confirm that the supplier provides reliable technical support and maintenance services.
How Our Thread Milling Equipment Boosts Production Efficiency
Conclusion: Finding the Ideal Thread Milling Solution for Your Needs
As an advanced threading technique, thread milling not only meets modern industry demands for high precision and efficiency but also helps producers reduce costs while enhancing product quality. We hope this technical overview and buying guide provide you with scientific insight into selecting the right thread milling equipment. If you have further questions or specific requirements, feel free to contact our expert team. We’ll work with you to find the best solution, helping you achieve efficient and seamless production.