In modern manufacturing, CNC systems serve as the “brain” of machine tools like lathes and milling machines, playing a crucial role in production efficiency, machining accuracy, and equipment stability. With the continuous development of intelligent manufacturing and automation technology, numerous brands and models of CNC systems have emerged on the market. From global leaders like Fanuc and Siemens to domestic brands like Huazhong CNC and GSK, each CNC system has its unique advantages and areas of application.
Choosing the right CNC system can be a challenge when facing different machining tasks. Every CNC system has its strengths and limitations, and making the wrong choice may impact machining efficiency, accuracy, and even product quality. For example, in mass production, Fanuc’s stability and efficiency can make a significant difference; however, for high-precision machining of complex parts, Siemens or Heidenhain would be a better fit. Making the right decision between these systems is a problem every manufacturing company must solve.
This article will help you gain a deeper understanding of the main CNC systems available today, their features, and their application scenarios, guiding you to make the best choice for lathes, milling machines, and complex part machining.
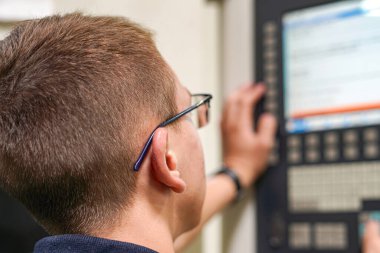
Introduction to Major CNC System
Fanuc System
Features and Advantages
Fanuc is one of the most widely used CNC systems globally, known for its excellent stability, ease of operation, and compatibility. The system has strong self-diagnosis capabilities and rich automation support, making it suitable for various types of machining, such as turning, milling, and multi-axis operations. It also provides excellent path control and thermal compensation, performing exceptionally well in high-precision and large-volume production.
Advantages
- Strong Stability: Maintains high accuracy during long hours of machining.
- Global Compatibility: Widely used around the world, with extensive service and support networks.
- Good Compatibility: Supports various types of machines, allowing for easy integration across different devices.
Siemens System
Features and Advantages
The Siemens system is well-known for its powerful multi-axis control and flexible programming, making it ideal for high-precision and complex machining processes. The system excels in graphical programming, path control, and thermal compensation, accurately controlling the geometry of workpieces and ensuring process continuity and stability. It is especially suitable for precise machining of complex surfaces and can be integrated into smart factory management systems.
Advantages
- Multi-Axis Control: Supports five-axis or more precise synchronization, suitable for complex geometries.
- Intelligent Features: Seamlessly integrates with smart manufacturing systems, supporting remote monitoring and diagnostics.
- Flexible Programming: User-friendly programming interface, supporting multiple programming methods.
Heidenhain System
Features and Advantages
Heidenhain is known for its ultra-high precision, micron-level control, and excellent dynamic response, making it ideal for ultra-precision machining scenarios. The system supports accurate control of complex contours and has high-sensitivity error compensation, making it perfect for the production of electronic components, high-end molds, and precision instruments. Heidenhain’s intuitive programming interface and rich self-diagnostic functions make it popular in precision manufacturing industries.
Advantages
- High Precision: Provides micron-level control with minimal error.
- Fast Dynamic Response: Ideal for real-time path control in high-precision machining.
- Wide Range of Applications: Particularly suitable for machining complex surfaces and ultra-fine structures.
Mitsubishi System
Features and Advantages
The Mitsubishi system is favored by mid-level manufacturing companies due to its good dynamic response and stability. It performs reliably in batch production and medium complexity machining, especially in turning and milling processes. The system offers excellent cost-performance, making it suitable for industries like electronics, home appliances, and automotive parts. Mitsubishi also provides high automation integration, simple operation, and is easy to learn, making it ideal for small and medium-sized businesses.
Advantages
- Cost-Effective: Offers high stability and economy in medium-complexity machining tasks.
- Easy Operation: Relatively simple programming and operation, suitable for quick factory training.
- Good Automation Integration: Supports automation equipment, ideal for batch production.
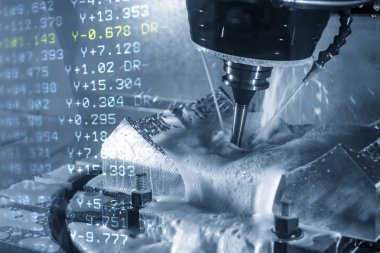
Domestic CNC System (e.g., Huazhong CNC, GSK, Kaidi)
Features and Advantages
In recent years, domestic CNC systems have significantly improved in stability, precision control, and automation. Brands like Huazhong CNC, GSK, and Kaidi have gained popularity in China, especially among small and medium-sized enterprises, due to their high cost-performance and strong after-sales service. These systems offer simple user interfaces, support Chinese and standard CNC operation logic, and are suitable for common machining tasks like turning and milling, meeting the domestic manufacturing industry’s needs for standardized part production.
Advantages
- Affordable: High cost-performance with low maintenance costs.
- User-Friendly: Simple and intuitive interface, suitable for domestic operators’ habits.
- Complete After-Sales Service: Fast local support, timely technical service, and spare parts supply.
Advantages of Different CNC Systems in Typical Machining Types
CNC System Selection for Lathe Machining
- Fanuc System: In lathe machining, Fanuc holds a key position due to its excellent stability and speed control. The Fanuc system supports precise positioning and high-speed cutting, making it ideal for processes with high precision and batch requirements, such as automotive parts and mechanical shafts. It performs exceptionally well in long-duration operations, maintaining accuracy even during continuous use.
- Domestic Systems (e.g., Huazhong CNC, GSK): Domestic systems perform well in standard turning operations. They offer high cost-performance and sufficient stability, making them suitable for small to medium-sized enterprises with daily turning tasks. The control response and positioning accuracy meet general machining needs and are ideal for medium to low-precision batch production.
Selection for Milling
- Siemens System: Siemens systems stand out in milling, supporting complex tool paths and multi-axis high-precision control, especially for high-end molds and complex geometric parts. The system is highly flexible in programming, excelling in five-axis control, and adapting well to continuous high-precision milling, making it the preferred choice in the high-end mold manufacturing industry.
- Mitsubishi System: Mitsubishi systems perform reliably in batch milling and moderate complexity tasks. They offer good dynamic response and path control, suitable for conventional parts in batch milling, especially in the automotive parts industry.
CNC System Selection for Multi-Axis Machining
- Siemens System: Siemens systems excel in multi-axis machining, especially in five-axis control and complex surface machining. They offer strong multi-axis coordination, maintaining path precision and stability when machining complex parts or high-precision molds. This system is widely used in industries like aerospace and precision medical devices, where high-precision multi-axis machining is critical.
- Fanuc System: Fanuc also offers excellent multi-axis control, particularly for four-axis or three-axis combined turning and milling. Its stability is suitable for moderately complex multi-axis machining, with widespread use in automotive and industrial equipment part production.
Applicability of Different Systems in Complex Part Machining
High-Precision Part Machining
- Siemens System: Siemens systems are ideal for high-precision control, with outstanding error compensation and path stability. They are perfect for complex contours and multi-axis synchronized control. For parts like complex molds or turbine blades, Siemens systems can ensure high-precision machining with their thermal compensation features.
- Heidenhain System: Known for its micron-level precision and high-end machining capabilities, Heidenhain systems are especially suited for electronic components and high-end mold manufacturing. Their precise trajectory control and dynamic response ensure consistent and stable machining of complex surfaces, making them the first choice for micro-machining.
Medium Complexity Part Machining
- Mitsubishi System: Mitsubishi systems perform excellently in batch production of medium-complexity parts. They offer strong path control and dynamic response, making them suitable for industries like electronics and home appliance manufacturing. Their stability meets the demands of batch production for general molds and contour parts.
CNC Systems’ Adaptability to Materials
Adaptability to High-Hardness Materials
- Fanuc System: The Fanuc system is highly adaptable to high-hardness materials. It has excellent path stability and automatic compensation features, which effectively reduce tool wear. The Fanuc system performs excellently in batch processing of titanium alloys and stainless steel, making it widely used in industries like automotive and mechanical engineering.
- Siemens System: In the processing of high-strength alloys and heat-resistant materials, Siemens systems stand out with their advanced thermal compensation and vibration suppression capabilities. This ensures accuracy, making it especially suitable for aerospace applications that require high-hardness material processing.
Adaptability to Difficult-to-Machine Materials
Difficult-to-machine materials (such as nickel-based alloys and ceramic materials) demand higher dynamic response and error control from CNC systems to ensure stable tool feeding and prevent thermal deformation.
- Siemens System: The Siemens system excels in high-precision control for difficult-to-machine materials, especially in the processing of nickel-based alloys and titanium alloys. Its feed control and error compensation features are particularly outstanding, meeting the stringent cutting performance requirements of high-end manufacturing industries.
- Heidenhain System: The Heidenhain system performs exceptionally well in micro-machining of brittle materials like ceramics. With its high dynamic response and precise feed control capabilities, it ensures the accuracy required for machining brittle materials, making it ideal for micron-level tasks that require extreme precision.
Adaptability to Common Metal Materials
For common metal materials such as aluminum alloys and carbon steel, the choice of CNC system is more flexible, though factors like efficiency, accuracy, and tool wear still need consideration.
- Domestic Systems: Domestic systems perform well in standard machining of common metal materials, offering good cutting stability and path control. These systems are suitable for daily machining needs in small to medium-sized enterprises, such as turning and milling of aluminum alloys and carbon steel.
- Mitsubishi System: The Mitsubishi system is stable in mass production, particularly for processing carbon steel and aluminum alloys. It offers good efficiency and path control, making it well-suited for batch processing in industries like automotive parts and general mechanical manufacturing.
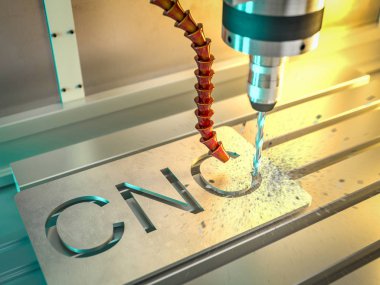
Conclusion: CNC System Selection Recommendations
For high-precision and complex part machining:Siemens and Heidenhain systems excel in multi-axis control and high-precision path management. These systems are ideal for complex surfaces and precision machining, especially in aerospace and high-end mold manufacturing.
For medium-complexity and mass production:Fanuc and Mitsubishi systems offer stability and high efficiency. These systems are well-suited for batch production tasks in industries such as automotive, home appliances, and electronics.
For standardized and routine machining: domestic systems and Mitsubishi systems offer high cost-performance. They are particularly suitable for processing common materials and standard parts, meeting the everyday machining needs of small and medium-sized enterprises.