In today’s rapidly developing manufacturing industry, tool wear has quietly become the “invisible killer” in factory workshops. Have you ever thought that even small-looking wear on the surface, caused by the high-speed rotation of tools colliding with hard metals, can lead to a series of issues, such as decreased production efficiency, soaring costs, and even serious quality problems? With the arrival of Industry 4.0, more and more companies are realizing the huge impact of tool wear on manufacturing precision and production cycles. In this race between tools, time, and cost, manufacturers face urgent issues such as how to choose the right tools, optimize cutting parameters, and reduce the burden on tools.
Tool wear is a common problem in the manufacturing process, and its influencing factors are complex. High cutting speeds, excessive feed rates, and deep cutting depths, among other cutting parameters, can all accelerate tool wear. Additionally, the choice of tool materials, coating technology, cooling and lubrication methods, and control of machine tool rigidity all play important roles in extending tool life. Meanwhile, tool wear is not just a material issue; it is also a comprehensive challenge involving cutting processes, technological innovation, and equipment optimization.
This article will deeply analyze how to minimize tool wear and improve processing efficiency through proper cutting parameter settings, scientific tool material selection, advanced coating technologies, and cooling and lubrication solutions.
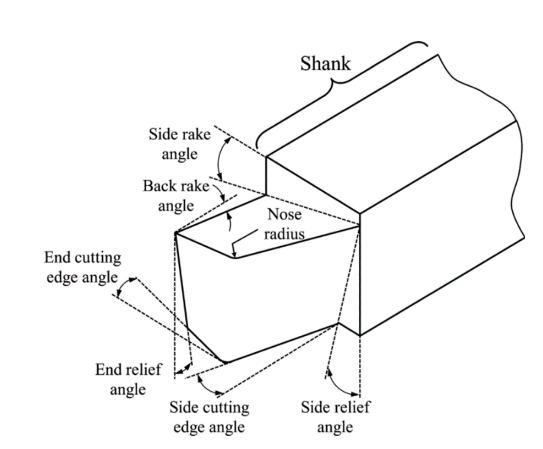
Optimization of Cutting Parameters and Their Relationship with Tool Wear
The selection of cutting parameters plays a crucial role in tool wear. High cutting speeds, large feed rates, and deep cutting depths increase the thermal load on the tool and generate excessive cutting forces, accelerating tool wear. According to cutting mechanics principles, cutting speed (v), feed rate (f), and cutting depth (a) are the main factors influencing tool wear. During cutting, friction and shear between the tool’s rake and flank faces and the workpiece generate significant heat. This heat propagates between the tool surface and the workpiece surface, raising the tool temperature and causing thermal damage, ultimately leading to tool material fatigue and wear.
Studies show that the relationship between cutting speed and feed rate and wear is complex. For example, in the application of carbide tools, cutting speed is inversely related to tool life: excessively high cutting speeds can raise the tool surface temperature, accelerating oxidation and melting; while large feed rates increase cutting forces, creating stress concentrations on the tool surface that cause localized chipping and wear. Therefore, optimizing cutting parameters is key to reducing tool wear.
1.1 The Impact of Cutting Speed and Optimization Strategies
Cutting speed is a significant factor influencing tool wear. At higher cutting speeds, friction between the tool and workpiece increases, leading to a sharp rise in tool temperature. Increased temperature not only accelerates thermal fatigue of the tool material but can also cause oxidation and melting, further speeding up wear. For example, in carbide tool machining, excessive cutting speed can push the tool surface temperature beyond its heat resistance limit, altering the tool’s material structure and accelerating wear .
To optimize cutting speed, the following strategies can be adopted:
- Select the optimal cutting speed range: Based on the workpiece material and processing requirements, choose an appropriate cutting speed range. For example, carbide tools are suitable for higher cutting speeds, while materials like high-temperature alloys and titanium alloys should use lower cutting speeds to avoid excessive thermal load.
- Balance cutting force and thermal load: Through numerical simulations and experimental research, the distribution of thermal load during cutting can be predicted. This helps adjust cutting speed and feed rate to reduce excessive friction between the tool and workpiece.
- Gradual acceleration and deceleration: In multi-pass cutting, adopt a progressive cutting speed change, starting from a lower speed and gradually increasing it to avoid sudden temperature spikes and reduce thermal damage.
1.2 The Impact of Feed Rate and Optimization Strategies
Feed rate is another key parameter affecting Cutting Tool wear. Excessive feed rate increases cutting forces, thereby raising the tool load and increasing contact pressure between the tool and workpiece. During cutting, the tool experiences high shear and compressive stresses, which cause stress concentrations at the tool edge, leading to localized chipping and wear. For example, high feed rates increase tool stress concentration, especially during high-speed cutting or machining harder materials, making early tool damage more likely.
You can take the following measures to optimize feed rate:
- Set an appropriate feed rate: Select a suitable feed rate according to the machining needs. For high-hardness materials, reduce the feed rate. Reducing the cutting load per pass can effectively reduce the impact and stress concentrations on the tool, minimizing edge wear.
- Step-feed control: For deep or heavy cutting processes, use step-feed methods, controlling the feed rate within a smaller range to reduce the tool burden and prevent premature wear.
- Dynamic feed adjustment: By monitoring vibration, cutting forces, and other parameters in real-time during cutting, feed rate can be dynamically adjusted to achieve optimal cutting conditions and prevent wear caused by excessive feed rate.
1.3 The Impact of Cutting Depth and Optimization Strategies
Cutting depth is another important factor influencing tool wear, especially during heavy cuts. Excessively deep cutting depths increase the cutting area, raising cutting forces and tool load, which accelerates wear. In particular, when using harder tool materials, deep cutting depths not only increase cutting forces but also lead to localized overheating of the tool, resulting in thermal damage.
To optimize cutting depth, the following strategies can be adopted:
- Control cutting depth: Determine the appropriate cutting depth through cutting tests, ensuring that the tool maintains low cutting forces and temperatures during machining. For harder workpiece materials, reduce the cutting depth to decrease tool load.
- Layer-by-layer cutting: For workpieces requiring high precision, adopt a layer-by-layer material removal method, gradually increasing the cutting depth to reduce tool stress and wear during each pass.
- Coordinate cutting depth with other parameters: When adjusting cutting depth, consider the relationship with cutting speed and feed rate. For instance, when increasing cutting depth, reduce cutting speed or feed rate to avoid excessive thermal load or cutting forces.
1.4 The Relationship Between Cutting Force and Tool Wear and Optimization Strategies
Cutting force is a critical factor affecting tool wear. During cutting, the cutting force directly influences the tool’s temperature distribution, friction, and wear pattern. Excessive cutting force results in a higher tool load, and the shear and friction forces generated during cutting accelerate wear. Research shows that cutting force is closely related to cutting speed, feed rate, and cutting depth. The distribution of cutting force is also linked to tool geometry, cutting conditions, and material properties.
To reduce tool wear, the following optimization strategies are effective:
- Reduce cutting force: By optimizing cutting parameters, especially reducing feed rate and cutting depth, cutting forces can be effectively reduced. In addition, designing the tool geometry, particularly the rake and relief angles, can further reduce cutting forces.
- Accurate cutting force prediction models: Using cutting force models and numerical simulation techniques, the cutting force under various parameter settings can be predicted accurately. This helps engineers optimize processing conditions and reduce cutter wear.
Selection of Tool Coatings and Materials
The selection of tool materials plays a crucial role in extending tool life. Tool manufacturers widely use high-performance materials such as carbide, ceramics, and cubic boron nitride (CBN) due to their excellent wear resistance, oxidation resistance, and high-temperature stability.Studies show that the wear rate of tools is closely related to their hardness and resistance to thermal cracking. Generally, tools made from harder materials tend to have longer lifespans.
However, a single tool material may not meet the demands of efficient machining under complex cutting conditions. To address this, coating technology has been developed. Common coatings such as TiN, TiAlN, and CrN effectively reduce friction between the tool and the workpiece, lower the wear rate, and provide additional protection under high-temperature conditions. For example, TiAlN coatings have excellent high-temperature resistance, making them particularly suitable for high-speed cutting applications . Coating technology has shown significant effectiveness in extending tool life, especially when machining high-strength alloys, titanium alloys, and other hard-to-machine materials, significantly improving tool durability.
Optimization of Cutting Fluids and Cooling Lubrication Technology
Cooling and lubrication are crucial for controlling cutter wear. Cutting fluids not only remove heat from the cutting zone, reducing the tool temperature and preventing thermal cracking, but also effectively lubricate the friction between the tool and the workpiece, thereby reducing wear. Traditional water-soluble emulsions are commonly used in cutting processes, but their cooling effectiveness is often limited by flow rate and spray angle control. Additionally, these fluids consume large quantities and contribute to significant environmental pollution.
In recent years, Minimum Quantity Lubrication (MQL) and gas cooling technology have become research hotspots in tool wear control. MQL technology combines a very small amount of lubricant with gas and sprays it into the cutting zone. This approach significantly reduces the use of cutting fluid and lowers environmental pollution. Compared to traditional cooling methods, MQL can notably reduce the friction coefficient on the tool surface and slow down the wear rate . MQL shows particularly strong advantages under high-speed and high-temperature cutting conditions, effectively enhancing the tool’s durability.
Optimization of Tool Geometry
The design of tool geometry is a key factor affecting cutter wear. Studies show that the rake angle, clearance angle, and cutting edge shape directly influence cutting force and temperature distribution. For example, a small rake angle or a large clearance angle increases the contact area between the tool and the workpiece, resulting in higher cutting forces . In contrast, proper geometric angle design can effectively disperse cutting forces, reduce friction, and lower tool surface temperatures.
When machining high-hardness materials, using a lower rake angle can reduce cutting forces and extend tool life. Moreover, tool coating technology and geometric optimization often complement each other. The coating not only provides extra protection but also works together with the tool geometry to further enhance tool performance.
Improving Machine Tool Rigidity and Vibration Control
The rigidity of a machine tool also plays a significant role in tool wear. Low machine tool rigidity can cause vibrations between the tool and workpiece during cutting. These vibrations increase cutting forces and accelerate tool wear. To improve machine tool rigidity, researchers have proposed various solutions, such as active vibration control, optimized structural design, and the use of high-rigidity materials. Enhancing machine tool rigidity effectively reduces cutting vibrations, which in turn lowers the rate of tool wear.
Conclusion
The issue of rapid tool wear is not caused by a single factor; it results from the interaction of multiple factors. By optimizing cutting parameters, selecting the right tool materials and coatings, improving cooling and lubrication, optimizing tool geometry, and increasing machine tool rigidity, we can effectively control tool wear and improve both processing efficiency and product quality. In the future, monitoring and early warning technologies for tool wear, intelligent machining technologies, and the development of new tool materials will be key directions for solving the tool wear problem. In this area, MINNUO, with its outstanding machine tools, provides the ideal platform for optimizing tool wear control. Our high-rigidity machine tools not only improve processing accuracy but also effectively reduce tool wear, enhancing overall production efficiency. Feel free to consult us anytime to learn more about our solutions and boost your productivity.