In modern manufacturing, the demand for production efficiency and machining precision continues to rise. As one of the key manufacturing tools, the machining center (MC) has become essential for companies to enhance productivity and stay competitive. Whether in aerospace, automotive manufacturing, or mold processing, machining centers are indispensable in factory workshops due to their versatility and high automation. With continuous technological advancements, machining centers now offer a wider range of types and functions, meeting the industry’s need for high-efficiency and high-precision machining.
A machining center is a multifunctional, automated CNC machine tool that can perform a variety of tasks such as milling, drilling, and boring. It uses an automatic tool changer (ATC) for fast tool replacements, greatly improving both production efficiency and machining accuracy. The machining center consists of several key components, including the spindle system, tool magazine, automatic tool changer, and chip and coolant management systems. These parts work together to ensure the machine’s efficiency and stability. Based on different machining needs, machining centers come in various types, such as vertical, horizontal, and five-axis models, each suited to different industries and tasks. The price of a machining center depends on factors like the type of machine, control system, automation configuration, and required machining precision. Therefore, when choosing a machining center, companies must consider performance, cost, and their specific needs to make the best choice.
This article will provide a detailed analysis of the core components of machining centers, the characteristics of different types, and the main factors that influence their prices. It aims to help you find the optimal balance between budget and performance, so you can select the most suitable machining center for your company.
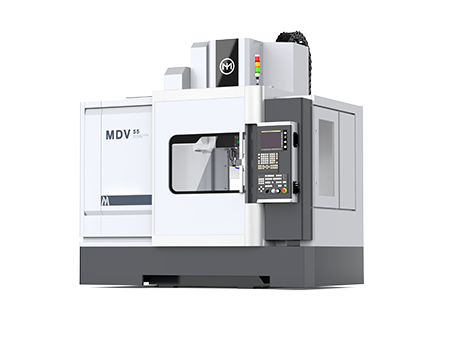
What is a Machining Center?
A machining center (MC) is a multifunctional, automated CNC machine tool capable of performing complex machining tasks. Unlike traditional machine tools, a machining center is not limited to just one operation (such as milling). It can quickly change between different cutting tools during the machining process through an automatic tool changer (ATC) system, allowing it to perform milling, drilling, boring, tapping, and other operations. Therefore, a machining center offers high flexibility and production efficiency.
A machining center is more than just a CNC machine tool. Its key features include automation, precision, and multitasking ability. By integrating an automatic tool changer and other automated functions, the machining center significantly improves production efficiency, shortens production cycles, and reduces human intervention and errors. The introduction of machining centers has made manufacturing processes smarter and more efficient. They are now essential equipment in high-end manufacturing industries.
Main Components of a Machining Center
A machining center consists of several important components that work together to ensure its efficient operation. Below are some of the key parts and their functions:
Spindle System
The spindle is one of the core components of the machining center. It provides the rotational motion needed for cutting. Driven by a high-precision motor, the spindle ensures that the workpiece achieves the desired surface quality and accuracy during the machining process. The stability and rigidity of the spindle play a crucial role in the machining accuracy, making it a key part in maintaining the precision of the machining center.
Automatic Tool Changer (ATC)
The automatic tool changer (ATC) is a highlight of the machining center. It allows the center to automatically change tools for different tasks, greatly improving production efficiency. The ATC system includes a tool magazine, which stores various cutting tools and can select the appropriate tool based on the machining requirements. With the ATC system, the machining center can perform continuous machining of complex parts, reducing the time spent on manual tool changes and improving overall production efficiency.
Tool Magazine
The tool magazine is part of the ATC system and is primarily used to store various cutting tools. Common types of tool magazines include chain-type and rotary-type, with the latter offering faster tool change speeds. The capacity of the tool magazine and its ability to manage tools directly affect the efficiency and flexibility of the machining center.
Chip and Coolant Management System
The chip and coolant management system is responsible for collecting chips produced during the machining process and providing the necessary coolant to the cutting area. This helps extend the life of the tools and ensures the quality of the workpieces. Modern machining centers are typically equipped with automatic chip removal and coolant circulation systems, further enhancing machining efficiency and stability.
Overload Protection and Wear Monitoring System
Machining centers are also equipped with overload protection devices and wear monitoring systems. These systems can detect abnormal conditions during the machining process, such as tool wear or overload, and promptly issue alarms or adjust machining parameters. These protection systems help prevent equipment failures, extend the life of the machine tool, and maintain machining accuracy and stability.
Types of Machining Centers
Machining centers come in various types based on different work requirements. Each type has unique advantages and is suitable for specific applications. Below are some common types of machining centers:
Horizontal Machining Center (HMC)
The horizontal machining center (HMC) uses a horizontal spindle and is ideal for machining large, heavy workpieces. These centers are often equipped with an Automatic Pallet Changer (APC) system, allowing for continuous processing without manual intervention. HMCs are especially suited for mass production due to their high material removal rate (MRR). Additionally, HMCs effectively prevent chip accumulation, ensuring stable and efficient machining. They are commonly used in industries like automotive and aerospace for large part machining.
Vertical Machining Center (VMC)
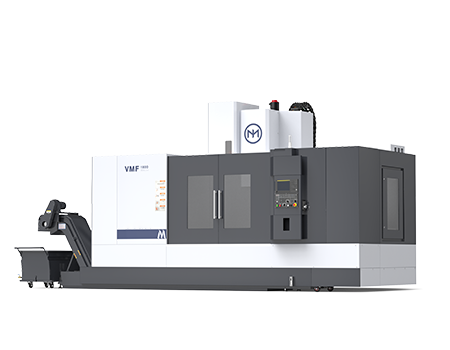
The vertical machining center (VMC) features a spindle that is perpendicular to the worktable, making it suitable for machining smaller parts. The design of VMCs is more compact, which makes them ideal for environments with limited workshop space. VMCs are commonly used for milling, drilling, and tapping operations, and they can precisely machine complex workpiece shapes. Due to their versatility, VMCs are widely used in mold making, mechanical part production, and other applications.
Universal Machining Center (UMC)
The universal machining center (UMC) combines the features of both HMC and VMC. It can perform cutting operations in both horizontal and vertical directions on the same machine. This dual capability increases the flexibility and precision of machining. Many high-end UMCs are equipped with a 5-axis control system, enabling multi-surface machining in a single setup. UMCs are commonly used in aerospace, automotive manufacturing, and other advanced industries.
5-Axis Machining Center
A 5-axis machining center allows movement along five independent axes to machine complex shapes and geometries. The key advantage of a 5-axis machining center is that it can perform multi-surface cutting on a single worktable, eliminating the need for multiple setups. This greatly improves machining accuracy and efficiency. 5-axis machining centers are particularly suitable for high-precision and complex parts, such as aerospace engine components and mold making.
Why Use a Machining Center?
- Increased Production Efficiency
The automatic tool change system in machining centers allows for quick tool swaps, reducing tool change time and significantly boosting production efficiency. This is especially beneficial for mass production or the machining of complex parts. - Multi-tasking Capability
A machining center can perform not only milling but also drilling, tapping, and other operations. This reduces the time spent on multiple setups, improving both machining accuracy and flexibility. - Improved Precision and Stability
The high-precision spindle and automation systems ensure high-quality machining. This reduces human errors and guarantees the stability of parts during the process. - Reduced Manual Intervention
With high levels of automation, the machining process relies less on manual labor. This not only minimizes human errors but also lowers operating costs. - Adaptation to Smart Manufacturing
Machining centers are integrated with intelligent functions like online monitoring and smart diagnostics. These features help businesses increase production efficiency and meet the demands of modern smart manufacturing
Price of Machining Centers: Factors and Market Trends Analysis
As a key piece of equipment in modern manufacturing, the price of machining centers is influenced by various factors such as technology, functionality, configuration, market demand, production scale, brand, and after-sales service. For businesses, selecting the right machining center requires more than just focusing on performance and accuracy. Understanding the price structure is also essential to avoid blind purchasing. This article will analyze the factors that affect the price of machining centers and provide helpful insights for decision-making.
Main Factors Affecting the Price of Machining Centers
Type and Specifications
The type and specifications of a machining center play a major role in determining its price. Based on different processing needs, machining centers come in various types, including vertical machining centers, horizontal machining centers, and 5-axis machining centers. Each type has its own price range, depending on the tasks they are designed for.
- Vertical Machining Centers (VMC):
Vertical machining centers are typically used for simpler tasks, making them ideal for small and medium-sized enterprises. Their prices are relatively lower. The price range for vertical machining centers is generally between $50,000 and $120,000, depending on the brand, control system, and configuration. - Horizontal Machining Centers (HMC):
Horizontal machining centers are favored for their superior stability and efficiency, especially in high-precision, large-batch production scenarios. The price for HMCs is usually higher than that of vertical machining centers, ranging from $90,000 to $230,000. - 5-Axis Machining Centers:
5-axis machining centers can control five axes simultaneously, which makes them suitable for high-precision machining of complex parts. Due to their advanced technology, 5-axis machining centers tend to be more expensive, with prices ranging from $150,000 to $450,000.
Control System
The control system (CNC system) is one of the core components of a machining center. Prices vary significantly depending on the CNC system. Common CNC system brands include Siemens, FANUC, and Mitsubishi.
- High-end CNC Systems:
Brands like Siemens and FANUC offer advanced systems that are more expensive but offer better stability, accuracy, and operability. Machining centers equipped with these systems tend to have a higher price tag. - Mid-range and Low-end CNC Systems:
Some domestic or budget-friendly brands offer CNC systems at more affordable prices. These are suitable for companies with less demanding performance needs. The price of machining centers with such systems tends to be more economical.
Automation and Intelligence Features
With the rise of smart manufacturing, many machining centers are now equipped with automation and intelligent features. These added functionalities can significantly increase the cost of the equipment. For example:
- Automatic Tool Change System (ATC):
A high-performance ATC can improve machining efficiency and reduce tool change time. The price of ATC systems varies depending on their capacity and technology level. - Robot Loading/Unloading System:
Some high-end machining centers come with robotic systems for automatic loading and unloading, further enhancing automation. The integration of robotic systems increases the overall price of the machining center. - Online Monitoring and Intelligent Control:
Some machining centers feature real-time data collection and intelligent diagnostic systems, which can improve production efficiency and equipment maintainability. However, these systems contribute to higher prices.
Machining Precision and Performance Requirements
The accuracy and stability of a machining center directly impact the quality and efficiency of production. Therefore, machining centers with high precision requirements are typically more expensive. Industries like aerospace, precision molds, and high-precision manufacturing demand very strict accuracy standards. These machining centers are often equipped with high-precision spindles, servo motors, and precision rails.
Price Range for Different Types of Machining Centers
Based on the type and configuration, the price of machining centers in the market generally falls within the following ranges:
- Basic Vertical Machining Centers:
Price range: $40,000 to $120,000. - High-performance Vertical Machining Centers:
Price range: $120,000 to $200,000. - Horizontal Machining Centers:
Price range: $90,000 to $230,000. - 5-Axis Machining Centers:
Price range: $150,000 to $450,000. - High-end Custom Machining Centers:
For special custom equipment, prices may exceed $450,000.
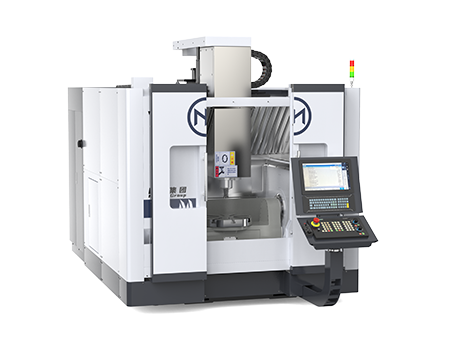
Common Issues and Defects of Machining Centers
Precision Issues
- Problem Description:
The precision of a machining center is one of its most critical indicators, affecting the quality of the workpieces and production efficiency. Common precision problems in machining centers include positional accuracy, repeatability, and geometric accuracy. For example, the machine may experience precision deviations after long periods of operation or improper handling, leading to increased machining errors. - Cause Analysis:
- Spindle and Guideway Wear: Over time, the spindle and guideway systems may wear out, causing a loss in precision.
- Temperature Changes: Changes in the environment’s temperature can affect thermal expansion, leading to instability in the machine’s accuracy.
- Mechanical Part Loosening or Wear: Components like ball screws and bearings can wear out, leading to insufficient positional accuracy.
- Solution:
- Regularly inspect and calibrate the equipment and replace worn-out parts in time.
- Implement better temperature control to maintain a stable machine environment.
- Use high-precision spindles and guideways.
Automatic Tool Change System (ATC) Failures
- Problem Description:
The ATC system is a vital part of a machining center. It allows automatic tool changes during the machining process, improving efficiency. However, the ATC often experiences failures, causing production downtime and increased maintenance costs. - Cause Analysis:
- Tool Library Jamming: Improper tool placement or system faults may cause the tool library to malfunction.
- Sensor Issues: Faulty sensors during tool changes can lead to inaccurate tool-switching actions.
- Mechanical Wear: The transmission parts and slots of the tool change mechanism may wear out due to long-term use.
- Solution:
- Regularly clean and check the tool library and tool-changing mechanisms to ensure smooth tool placement and transfer.
- Periodically calibrate and replace sensors to ensure proper function.
- Strengthen maintenance and care of the ATC system to prevent excessive wear.
Spindle Failures
- Problem Description:
The spindle is one of the core components of a machining center, responsible for the rotation of the cutting tool. When the spindle fails, it often leads to a decline in machining quality or production stoppages. - Cause Analysis:
- Bearing Damage: Spindle bearings are prone to wear or damage due to prolonged high-load operation or inadequate lubrication.
- Spindle Motor Failure: A malfunctioning spindle motor can prevent the spindle from operating normally, affecting cutting performance.
- Overheating: Excessive heat can cause spindle components to deform, affecting machining precision.
- Solution:
- Regularly inspect and replace spindle bearings to ensure normal operation.
- Maintain a good lubrication system to prevent spindle overheating.
- Implement temperature control and cooling for the spindle.
Unstable Cutting Quality
- Problem Description:
During machining, unstable cutting quality may occur, manifesting as rough surfaces, rapid tool wear, or workpiece deformation. - Cause Analysis:
- Improper Cutting Parameters: Incorrect feed rates, cutting depths, and cutting speeds can cause unstable cutting conditions.
- Improper Tool Selection: The tool material, coating, or geometry may not be suitable for the task, leading to poor cutting efficiency or surface quality.
- Cooling Fluid Issues: Insufficient flow, pressure, or quality of the cooling fluid may cause excessive heat during cutting, affecting machining quality.
- Solution:
- Adjust cutting parameters based on the material and workpiece shape to ensure tools perform under optimal conditions.
- Use suitable tools and regularly inspect for wear, replacing them in time.
- Ensure a steady supply of cooling fluid to maintain the right temperature at the cutting zone and extend tool life.
Chip Handling Issues
- Problem Description:
Chip removal is a crucial aspect of machining. Failure to clear chips in time or a poorly functioning chip removal system can lead to machine jams, poor machining, or overloading of the equipment. - Cause Analysis:
- Chip Accumulation: Chips may accumulate on tools, workpieces, or inside the machine, causing cutting difficulties or errors.
- Cooling Fluid Drainage Issues: After mixing with chips, if the drainage system becomes clogged, it may lead to chip blockages.
- Solution:
- Regularly clean the interior of the machine, especially during heavy-duty machining.
- Ensure proper functioning of the cooling fluid drainage system and regularly clean the filters to avoid blockages.
Electrical and Control System Failures
- Problem Description:
The electrical and CNC systems of a machining center control the entire machining process. Failures in these systems directly affect machine operation and machining precision. - Cause Analysis:
- Unstable Power Supply: Voltage fluctuations or power interruptions can cause the control system to malfunction.
- Software Failures: CNC system software may encounter errors or data loss, disrupting operations.
- Aging Electrical Components: Aging components like relays and contactors may prevent the equipment from starting normally or cause control signals to be lost.
- Solution:
- Ensure a stable power supply by installing an uninterruptible power supply (UPS) to prevent sudden outages.
- Regularly inspect and maintain electrical systems to ensure all components are working properly.
- Update and back up the control system software to ensure smooth operation.
Conclusion:
Machining centers are essential equipment in modern manufacturing. Different types and configurations of machining centers can meet various production needs. From high-precision 5-axis machining centers to horizontal machining centers suitable for mass production, each machine has its unique advantages. With the continuous development of automation and smart technologies, companies should consider not only the performance and precision of the equipment but also the cost-effectiveness and future development needs. Whether you aim to improve production efficiency or require precision machining solutions, we offer a range of machining centers tailored to your needs. Feel free to visit us at Minnuo anytime for more personalized selection advice.