In today’s rapidly evolving manufacturing industry, precision machining technology continues to advance, becoming one of the key factors in improving production efficiency and product quality. As the demand for high-efficiency and high-precision production grows, optimizing cutting speed has become a critical part of enhancing competitiveness. Among the various machining parameters, Surface Cutting Speed (SFM) is undoubtedly one of the core indicators that directly impacts machining results. How to precisely control SFM has become a pressing technical challenge for manufacturers.
SFM, as a key factor that determines tool performance, workpiece quality, and production efficiency, is closely related to cutting force, temperature control, tool life, and surface finish. By setting SFM correctly, manufacturers can improve machining efficiency, reduce costs, and extend tool life, while ensuring part accuracy. Whether in milling, turning, or complex CNC machining, the right SFM setting provides a solid foundation for efficient production.
Whether you are new to precision machining or an experienced expert, adjusting SFM according to different materials, tools, and machine conditions is key to improving production efficiency and product quality. Next, we will guide you through the fundamental concepts and optimization strategies of SFM, helping you achieve the best cutting results in daily production and ensuring each machining task is completed successfully.
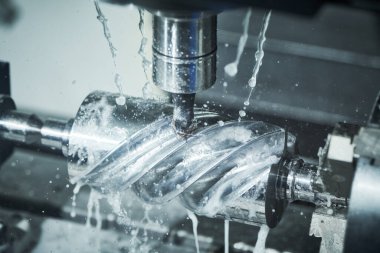
What is Surface Cutting Speed(SFM) in machining?
SFM (Surface Feet per Minute) is a unit used to represent the speed at which a cutting tool contacts the surface of the workpiece. It measures the distance the tool moves relative to the workpiece surface per minute. SFM is crucial for determining cutting speed and directly impacts tool life, surface quality, and overall machining efficiency.
How does SFM affect the machining process?
SFM plays a significant role in the efficiency and quality of the machining process. Setting the correct SFM can improve surface finish, extend tool life, and increase production efficiency. On the other hand, an incorrect SFM setting can cause rapid tool wear, poor surface quality, and even tool damage. A successful machining process requires finding a balance between too high and too low an SFM.
Surface speed and SFM

Surface speed refers to the speed at which the cutting tool makes contact with the workpiece surface, while SFM is the unit of measurement for surface speed. When using inches or feet as units, SFM directly represents surface speed. The correct surface speed ensures efficient operation of the cutting tool, reduces tool wear, and helps prevent cutting defects. Higher surface speeds are generally suitable for harder materials, while lower surface speeds are more appropriate for softer materials.
What is the unit for measuring Surface Cutting Speed(SFM)?
The unit for SFM is feet per minute (ft/min), which represents the distance the cutting tool travels relative to the workpiece surface each minute. By using the SFM unit, operators can determine the correct cutting speed to achieve the desired machining results.
Is SFM the Same as RPM?
No, SFM and RPM (Revolutions per Minute) are related but not the same. RPM refers to the number of times the tool or workpiece completes a full rotation in one minute, while SFM measures the distance traveled by the cutting edge. To find the relationship between SFM and RPM, you need to know the tool radius or diameter. The formula to convert between RPM and SFM is:

Where:
- SFM is the surface feet per minute.
- D is the diameter of the cutting tool in inches.
- RPM is the revolutions per minute.
How to Calculate SFM in Machining?
To calculate SFM, you need the following formula:
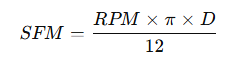
Where:
- RPM is the revolutions per minute.
- D is the diameter of the cutting tool in inches.
- The constant π is approximately 3.1416.
What Tools and Techniques are Needed for Accurate SFM Calculation?
Accurate SFM calculation requires precise measurement of the tool diameter and a solid understanding of the material’s properties. The essential tools include:
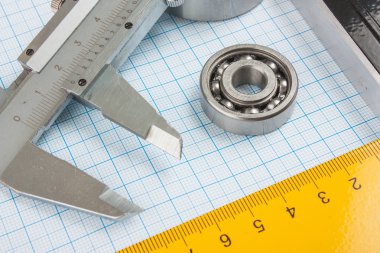
- Micrometers and Calipers for measuring tool diameter.
- Speeds and Feeds Tables or software to reference optimal cutting speeds based on material type.
- CNC Machines with programmable features that allow for real-time adjustments to cutting speed based on SFM settings.
Additionally, some CNC systems come equipped with real-time monitoring tools that can adjust SFM automatically, ensuring consistent machining quality and efficiency.
The Relationship Between SFM Optimization and Cost Efficiency
How can optimizing SFM reduce machining costs?
Choosing the right tools and cutting parameters:
The optimal SFM range varies for different tools and materials, so optimizing cutting parameters is an effective way to reduce costs. Selecting the right tool materials and coatings allows the tool to handle higher cutting speeds while maintaining a lower wear rate. For example, coated tools can extend tool life at higher SFM, reducing the costs of replacements and regrinding.
Proper use of coolants and lubrication:
Adequate coolant and lubrication can reduce heat buildup during the cutting process, preventing tool damage and workpiece quality issues caused by excessively high SFM. By precisely controlling the coolant flow and placement, you can reduce coolant waste and effectively lower operating costs.
Increasing automation:
Introducing automated processing equipment, such as automatic tool changers and robotic loading systems, can increase production efficiency without lowering SFM. Automation reduces human intervention and errors, while efficiently managing tool usage, thus balancing cutting speed and cost.
Optimizing production processes and workflow:
Careful process design and production planning can help avoid waste caused by excessive or insufficient SFM. Through simulations and testing, you can find the ideal SFM settings that achieve optimal production efficiency with minimal machining time and tool wear.
Batch production and optimized scheduling:
For large-scale production, you can adjust SFM based on material type, processing requirements, and equipment performance. Properly scheduling production batches reduces tool change frequency and lowers unit costs. When high precision is required, you may choose a lower SFM, but for mass production, optimizing SFM can increase output.
Balancing SFM Settings and Production Costs
In practical production, balancing SFM settings and production costs is crucial. You need to adjust SFM based on specific machining conditions, such as material type, machine performance, tool life, and quality requirements:
For hard materials or high-strength alloys, increasing SFM slightly can speed up cutting and reduce machining time. Using the right tool coatings and efficient cooling methods can prevent excessive wear, extend tool life, and ultimately lower overall costs.
For soft materials or parts requiring high surface quality, you may need to reduce SFM to avoid surface defects and rapid wear. However, this means machining time will increase, so it is essential to balance production efficiency and cost.
For mass production, properly setting SFM and using efficient equipment can result in higher output and lower unit costs. Using multifunctional equipment and automation can reduce downtime and improve overall production efficiency.
How CNC Tools Affect Surface Cutting Speed
Tool Material and Coating:
Different tool materials, such as carbide, ceramics, and superhard materials, are suitable for different SFMs. Carbide tools can usually handle higher SFM because they have better wear resistance and thermal stability. Coated tools, such as those with TiN or TiAlN coatings, further improve the tool’s durability at high SFM, reducing wear and tool temperature.
Tool Geometry:
The geometry of the tool, such as tool angles, edge shapes, and the number of cutting edges, affects the mechanical behavior during the cutting process, which in turn influences the choice of SFM. For example, sharp cutting edges can reduce cutting forces, allowing for higher SFM without causing excessive wear.
Sharpness of the Cutting Edge:
Sharp tools reduce friction and heat generation during cutting, which helps maintain machining precision at high SFM and extends tool life. Blunt tools increase cutting resistance, requiring a lower SFM to prevent premature damage.
Cooling and Lubrication:
CNC tools generate significant heat when working at high SFM. Proper cooling and lubrication help control the tool temperature, preventing overheating and ensuring tool stability and longevity. The selection and use of cutting fluids are crucial for optimizing SFM.
Tool Machining Adaptability:
Different types of CNC tools, such as end mills, turning tools, and drills, have different levels of adaptability to SFM. During milling, the cutting angles and methods vary, affecting tool load and cutting efficiency, so SFM adjustments are necessary based on the tool type.
What Happens When Surface Cutting Speed is Set Incorrectly?
When SFM is set incorrectly, several issues may arise:
- High SFM can generate excessive heat, causing rapid tool wear and even tool failure. It can also affect surface finish, leading to material chipping or deformation.
- Low SFM results in poor cutting efficiency, longer machining times, and surface quality issues due to excessive friction and heat buildup.
How to Adjust Surface Cutting Speed Based on Heat-Treated Materials
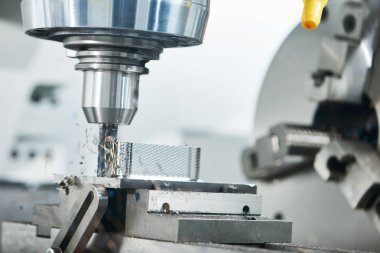
In practical machining, SFM settings need to be adjusted based on material characteristics such as hardness, toughness, and cutting performance. For materials that have undergone different heat treatment processes, follow these guidelines to adjust the SFM:
- Hardened steels and alloys: Lower the SFM to reduce tool wear, improve machining stability, and extend tool life.
- Annealed steels and aluminum alloys: Increase the SFM appropriately to enhance machining efficiency and reduce processing time.
- High-temperature alloys and titanium alloys: For these high-strength alloys, usually lower the SFM and use appropriate cooling fluids and cutting tools to prevent rapid tool wear.
How to Adjust Surface Cutting Speed for Different Materials
Different materials require different SFM settings to optimize cutting performance. Here are some common materials and their SFM adjustment methods:
- Hard metals (such as stainless steel, titanium alloys): These materials require a lower SFM to prevent rapid tool wear and control heat generation. Typically, the cutting speed ranges from 50 to 150 SFM.
- Soft metals (such as aluminum, copper): These materials can handle higher SFM to improve efficiency and productivity. The typical SFM range is from 300 to 900.
- Plastics: Plastics usually need higher SFM to achieve good surface finish. Depending on the type of plastic, the SFM range can vary from 500 to 2000.
Conclusion
SFM is a critical parameter in machining that directly affects tool performance, part quality, and production efficiency. By understanding the relationship between SFM, RPM, and material characteristics, operators can optimize cutting speeds for different materials, tools, and operating conditions. Whether using CNC machines, manual lathes, or milling machines, setting the correct SFM is essential for achieving high-quality machining results and extending tool life.
Accurately calculating and adjusting SFM helps manufacturers maintain cost efficiency and smooth operations while ensuring optimal machining outcomes. If you have more questions about precision machining equipment or SFM optimization, feel free to visit our Minnuo‘s website for more information. We offer professional solutions to meet your needs.