In the field of precision manufacturing, traditional machining methods such as turning, milling, and drilling are gradually facing many limitations as technology advances. With the increasing demand for complex workpiece shapes and high-hardness materials, overcoming the bottlenecks of traditional machining methods has become a pressing issue for manufacturers. Electrical Discharge Machining (EDM), as a non-traditional method, has gradually filled the gap left by traditional technologies with its unique working principles and technical advantages. It has emerged as a key solution in many high-precision and high-difficulty machining scenarios.
Although EDM outperforms traditional machining methods in many cases, it is not a universal solution. The combination of EDM with traditional methods is crucial. In actual production, selecting the right machining method for different workpiece needs—while ensuring machining efficiency and maintaining high precision—presents a significant technical challenge for many manufacturers. EDM shows unmatched advantages, especially in areas like high-hardness materials, complex shapes, thin-walled structures, or deep-hole machining.
This article will explore the reasons why EDM outperforms traditional machining in seven typical scenarios. It will also provide practical advice on optimizing the process flow with specific cases, helping you make more informed decisions when selecting machining methods.
7 Situations Where Electrical Discharge Machining Outperforms Traditional Machining
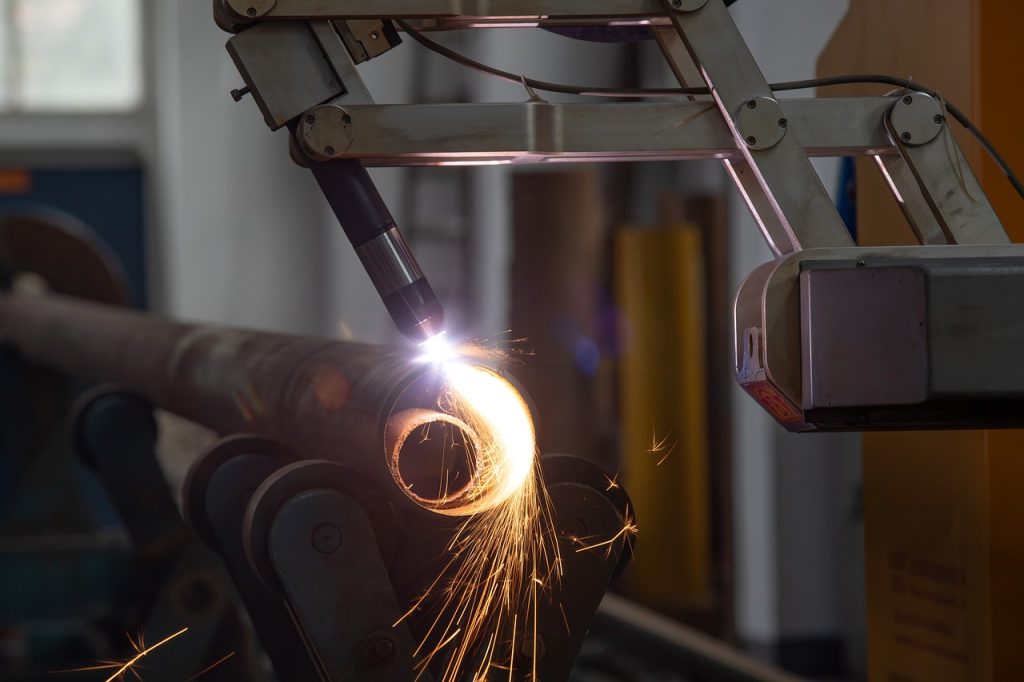
In modern manufacturing, precision machining demands increasingly higher technological standards. Traditional machining methods such as turning, milling, and drilling often face limitations. To overcome these challenges, Electrical Discharge Machining (EDM) has emerged as a non-traditional machining method with unique working principles and technical advantages. It has become a crucial tool in high-precision manufacturing. So, in which situations does EDM provide better results than traditional machining?
EDM Handles Ultra-Hard Materials
Traditional cutting methods are often limited by the hardness of materials. When the workpiece material is too hard, such as tungsten carbide, hardened steel, or certain alloys, traditional machining processes like turning and milling may not be effective. They could even result in excessive tool wear. EDM, however, does not rely on physical cutting. Instead, it uses high-frequency electric sparks to melt and vaporize metal. As a result, EDM can easily process materials with hardness up to 65 HRC or even higher. This makes EDM essential in hard tool, mold processing, and some special alloy machining.
More Flexible for Complex Shapes
Traditional machining methods often require very complex tool paths and multiple machining steps to process complex geometries. EDM, on the other hand, allows for free “sculpting” of workpieces through the shape of the electrode. It can precisely process complex shapes, such as intricate cavities, precision holes, and fine grooves, in a single step. This flexibility makes EDM especially valuable in the production of precision molds and aerospace components.
No Mechanical Force Required, Ideal for Thin-Walled Structures
Traditional machining on thin-walled structures often results in significant deformation or stress, affecting part accuracy. EDM is a non-contact process that does not apply any mechanical force to the workpiece. Therefore, for thin-walled or easily deformed parts, EDM ensures shape and dimensional accuracy while avoiding deformation issues common in traditional machining.
Precision Machining with Micron-Level Tolerances
One of EDM’s notable advantages is its high precision. EDM can achieve very fine machining, typically achieving micron-level tolerances (such as ±0.002mm). The surface finish is also high, usually reaching Ra0.2-0.4µm. For industries that demand high precision, such as semiconductors, medical devices, and precision molds, EDM is an irreplaceable choice compared to traditional machining methods.
Avoidance of Material Heat-Affected Zones (HAZ)
Traditional machining, especially high-temperature processes, can create a heat-affected zone (HAZ) on the surface of the workpiece. This can impact the material’s mechanical properties and surface quality. EDM, however, uses brief high-temperature sparks to heat metal in a very small area, avoiding excessive heating of the entire material and large-scale heat-affected zones. As a result, EDM machined parts maintain better material properties, making it ideal for applications where material performance is critical.
Capability to Process Difficult Materials
Certain difficult-to-machine materials, such as high-temperature alloys, ultra-high-strength steels, metal ceramics, and other hard-to-cut materials, may be difficult or expensive to process using traditional methods. EDM is not limited by material hardness, toughness, or brittleness and can efficiently machine these difficult materials. In industries such as aerospace, automotive, and energy, the application of EDM can significantly improve production efficiency and machining quality.
Advantages in Deep and Micro Hole Machining
Deep hole machining is a challenging task for traditional processes, especially when dealing with deep holes with a high length-to-diameter ratio. Traditional drilling methods often struggle to achieve precise machining. EDM, however, can accurately machine a variety of deep and micro holes with its small electrodes, even reaching areas that traditional machining methods cannot. Moreover, EDM avoids mechanical damage to the hole walls during the process, preserving the hole’s accuracy and surface quality.
After understanding the advantages of Electrical Discharge Machining (EDM) over traditional machining, it becomes clear that EDM’s unique characteristics allow it to outperform traditional methods in many specific applications. However, in actual production, choosing the right machining method based on the different needs of the workpiece remains a challenge for many manufacturers. Both traditional machining and EDM have their own strengths and weaknesses. By making a reasonable selection and combining the two, manufacturers can maximize machining efficiency.
Next, we will explore how EDM can be used in conjunction with traditional machining to address specific machining requirements.
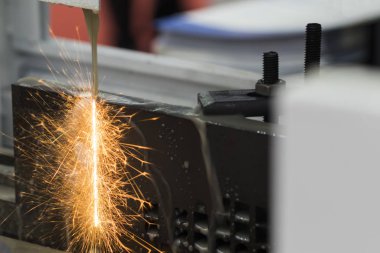
Using EDM in combination with traditional machining: How to effectively pair and optimize the process flow in production?
Analysis of the advantages and disadvantages of traditional machining
To achieve effective process pairing, let’s first understand the characteristics of traditional machining:
Traditional cutting machining: It applies mechanical force through tools to remove material quickly and is suitable for large-scale production. Cutting speed is fast, and efficiency is high. However, for high-hardness materials or complex internal structures, tool wear is severe, and it is difficult to meet the requirements for machining extremely small features.
Rational Combination of Electrical Discharge Machining and Traditional Machining
In actual process flows, the combination of EDM and traditional machining is commonly used in the following situations:
Efficient Processing of Hard Materials
For hard materials like quenched steel or titanium alloys, traditional cutting machining tends to experience significant tool wear and high processing difficulty. EDM can be used to pre-shape hard materials, reducing tool wear. Then, traditional machining can be used for rough machining or shape refinement of the remaining material.
Example: In high-hardness mold processing, EDM is often used for pre-processing complex internal structures and hard materials, followed by traditional cutting for precision shaping of the outer surfaces. This balances both processing cost and efficiency.
Processing of Complex Cavities and Fine Structures
For parts with complex internal structures or special shapes, traditional machining tools may struggle to access or process deep holes and fine slots. EDM can precisely remove material from internal structures. After that, traditional machining can be used for external finishing such as grinding or polishing.
Example: In the processing of complex mold cavities, EDM can be used for fine cavity and small hole machining, while traditional machining handles rough processing of the overall mold structure, ensuring precision and surface quality for both internal and external features.
High Precision and High Surface Finish Machining
EDM can achieve higher surface finish and micron-level dimensional tolerances, making it ideal for high-precision machining needs. First, traditional machining can remove most of the material, then EDM can be used for fine processing of specific critical surfaces or features to meet high precision and finish requirements.
Example: Precision molds and optical device components, which have strict surface quality requirements, can benefit from this combination of techniques to enhance overall results.
Processing of Composite Structure Parts
For composite structure parts that require different machining methods, a combination of EDM and traditional machining can be effective. For instance, traditional machining can be used to drill holes or chamfer metal sheets, and then Electrical Discharge Machining can be used for fine detailing and deep-hole processing. This combination reduces tool wear and minimizes deformation during machining.
Example: In the processing of precision electronic component housings, traditional machining handles the overall shaping, and EDM is used for detailed internal hole processing after the main form is established. This combination ensures both efficiency and precision.
Processing of Composite Structure Parts
For composite structure parts that require different machining methods, a combination of EDM and traditional machining can be effective. For instance, traditional machining can be used to drill holes or chamfer metal sheets, and then EDM can be used for fine detailing and deep-hole processing. This combination reduces tool wear and minimizes deformation during machining.
Example: In the processing of precision electronic component housings, traditional machining handles the overall shaping, and EDM is used for detailed internal hole processing after the main form is established. This combination ensures both efficiency and precision.
Material and Structural Analysis
Select the appropriate machining method based on the material’s hardness, toughness, and other characteristics. For hard materials or easily deformed thin-wall structures, consider using EDM for pre-shaping or fine machining. For low-hardness materials or large components, traditional machining can be used for rough processing.
Rough Machining Step: Removing the Majority of Material
Use traditional cutting machining for large-scale material removal and initial shape profiling. This method is fast, helping to shorten overall processing time and reduce the use of EDM.
Example: In mold manufacturing, traditional machining handles initial shape carving and flat milling to leave sufficient material for subsequent EDM processing.
Precision Pre-processing: Ensuring Accuracy in Critical Areas
Use EDM to pre-process critical locations or internal structures of the part. This step ensures the dimensional accuracy and positional accuracy of specific areas while leaving precise reference points for subsequent traditional machining.
Example: In mold manufacturing, EDM can be used to pre-shape cavities and guide holes, ensuring the foundation for later detailed processing.
Semi-Finish Machining Step: Refining Shapes
In areas that do not require high precision, continue with traditional machining to further refine the part’s outline. In this step, traditional milling, turning, and other methods complete most of the shape machining.
Finish Machining: Fine Detailing of Key Surfaces and Complex Parts
For areas that require high surface finish and precision, use EDM for fine surface treatment, ensuring the surface finish and dimensional tolerances meet the requirements.
Example: In fine mold processing, EDM finalizes the surface finish of the internal cavity, ensuring the mold achieves high-quality surface properties for use.
Final Polishing and Surface Treatment
Based on the part’s final needs, perform necessary polishing, grinding, or surface coating treatments. For parts requiring extremely high surface finish, EDM-machined surfaces may need further polishing to improve appearance and performance.
Example: After the mold achieves the desired surface finish, apply coating or heat treatment to enhance durability and precision.
Key Considerations in Process Flow Design
When designing the process flow for EDM and traditional machining, the following points should be carefully considered:
Rationally Plan the Machining Sequence: Determine which parts should be processed by EDM and which by traditional machining to maximize overall efficiency. Avoid frequent switching between processes to reduce clamping and setup times.
Electrode and Tool Wear Control: Plan the use of electrodes and tools in advance to ensure that electrode wear does not affect subsequent machining in batch production. A strategy for replacing electrodes and tools can effectively reduce production costs.
Maintaining Precision Reference Points: When switching from one machining method to another, maintaining consistent reference points is crucial. This reduces machining errors and ensures final assembly accuracy.
Conclusion:
By analyzing the advantages of Electrical Discharge Machining compared to traditional machining, we can see that EDM offers unique technical advantages in many complex and high-precision machining requirements. However, the key challenge remains how to effectively combine EDM with traditional machining in practical production settings. By rationally integrating both processes, manufacturers can improve machining efficiency while ensuring the accuracy and quality of parts.
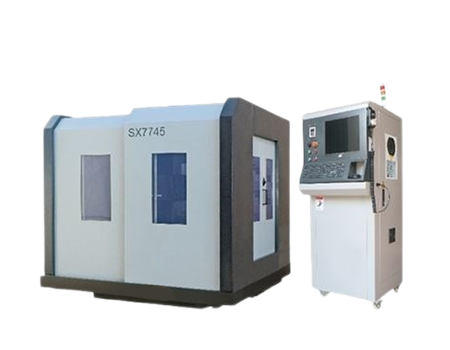
CNC Abrasive Wire Cutting Machine SXH Series
If you have any questions about selecting machining methods or optimizing process flows, feel free to reach out to our technical team. As an industry leader, Minnuo not only offers high-quality EDM equipment but also provides comprehensive technical support to help you solve specific production challenges. Let’s work together to deliver the best solutions for your manufacturing needs!