In modern manufacturing, the demand for efficient and high-precision machining equipment continues to rise, especially in industries like automotive, aerospace, and mold making. Choosing a high-performance machining center has become a key factor for businesses to stay competitive. Faced with complex and ever-changing machining scenarios, ensuring both production efficiency and machining quality is the core focus of every manufacturing enterprise. The MINNUO MDH series horizontal machining center is designed to tackle these challenges head-on.
The MDH series horizontal machining center, inspired by Japan’s advanced OKK technology, is ideal for machining precision box components, housings, discs, and irregularly shaped parts in industries like machinery manufacturing. With a single setup, it can automatically complete multiple processes on four faces, including milling, boring, drilling, reaming, and tapping. It offers high automation, strong reliability, simple operation, and user-friendly features. Its design is both aesthetically pleasing and highly integrated with modern electromechanical technology.
Next, we will explore its key technologies, core performance, and real-world applications to demonstrate how the MINNUO MDH series horizontal machining center delivers efficient and reliable machining solutions through innovative technology and thoughtful design.
Overview of Key Technical Features
This machine integrates multiple advanced technologies to fully meet the demands of high-performance and high-precision machining. It includes a patented mechanical cam-type tool magazine that enables efficient tool changes. With an 8000/12000 rpm high-speed spindle and 1000Nm high-torque spindle, it handles various machining scenarios with ease. The machine uses spindle constant temperature technology and spindle temperature compensation technology to control spindle heat rise effectively, ensuring long-term machining accuracy.
Additionally, its key components are optimized through finite element analysis. It features constant temperature control at the motor ends and a hollow screw oil cooling system, which further enhance thermal stability and machining precision. Structurally, the machine adopts three-axis roller guides, an integrated Y-axis screw bracket and column casting design, and a standard-pressure worktable structure. These innovations deliver outstanding structural rigidity and load capacity.
With its large travel range on all three axes, the machine supports machining of large workpieces. The combination of these technologies provides an exceptional machining experience with high efficiency, reliability, and precision.
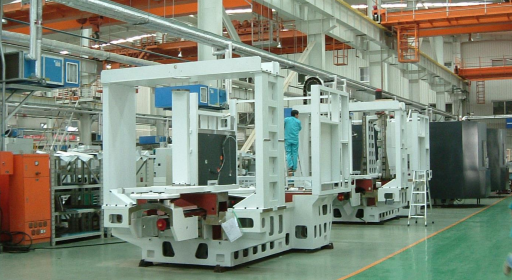
How to Achieve High Precision
The X, Y, and Z axes of the machine use advanced high-precision hollow cooling technology for the ball screws, with real-time temperature control of the cooling oil. Both the motor flange and spindle are equipped with forced constant temperature cooling devices. These measures keep temperature changes within a narrow range, effectively addressing heat deformation during machining and significantly improving machining precision. This ensures that the MDH65 achieves full travel accuracy in a semi-closed loop state: positioning accuracy of 0.008mm and repeat positioning accuracy of 0.005mm.
High-Precision Rotary Table Positioning and Clamping Mechanism
The machine uses Japan’s Kosme positioning taper pins combined with Japan OGIC gear disc structures. This design ensures exceptional precision for the MDH50/MDH65/MDH80 models:
- Gear disc indexing accuracy: ≤±2.5″
- Gear disc repeat indexing accuracy: ≤±1″
- Circular grating indexing accuracy: ±5″
Spindle Temperature Compensation Technology
The machine uses the FANUC 31i CNC system with thermal error compensation software. This system incorporates the principles and program design of thermal error compensation, which has been fully applied in the MDH series horizontal machining centers. By mastering this core technology, it avoids thermal errors caused by temperature changes and cutting force errors caused by force deformation, greatly improving machining precision.
Programming is done through the FANUC system’s PMC, integrating the compensation software into the control system. Using FANUC PICTURE, it provides an intuitive and user-friendly interface for applying temperature compensation in practice. The PLC program calculates compensation values to control the movement of the Z-axis (as well as the X/Y/Z axes), ensuring precise relative positioning between the tool and spindle.
Hollow Oil-Cooled Ball Screw Technology
The X, Y, and Z axis ball screws of the machine use advanced hollow oil cooling technology, with real-time temperature control for the cooling oil. This keeps temperature changes within a narrow range, reducing thermal deformation during cutting and rapid movement. It also increases the torsional rigidity of the ball screws, enhances machining precision, and effectively reduces the inertia of the worktable during high-speed motion.
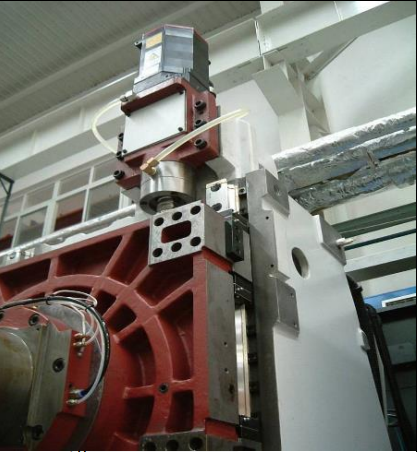
How to Achieve High Rigidity
The machine base uses a high-phosphorus resin sand casting with a T-shaped design, offering excellent rigidity and precision retention. The exchange worktable and tool magazine arm are directly mounted on the machine base, ensuring overall structural rigidity. The base design undergoes finite element analysis to ensure a well-optimized structure with proper rib placement, providing high static and dynamic rigidity and maintaining long-term accuracy.
Compact High-Rigidity Main Structure
- The machine’s main body features a thick-walled box-type high-rigidity design. By increasing the thickness of the base and column, it enhances rigidity and minimizes deformation caused by temperature changes, maintaining high precision over extended periods.
- The X-axis uses a left-and-right moving column design, while the Z-axis moves the exchange worktable back and forth. This reduces the space requirements by 30% compared to previous models.
- It is ideal for machining automotive engine blocks, steel, cast iron, and aluminum components.
- The compact structure supports high-efficiency machining and saves space.
Finite Element Analysis for Bed Design
- The MDH series horizontal machining centers use ANSYS Workbench finite element analysis software to evaluate the bed design. Natural frequency is used as a benchmark for the dynamic performance of the bed. The analysis identifies weak points in structural rigidity, laying the foundation for optimizing key components like the machine bed.
- Finite element models are created for all MDH series machines. Using specialized software, the models are analyzed to improve the natural frequencies of key components. We optimize the dimensions to meet design goals and integrate the characteristics of the joint surfaces in moving parts into digital simulation models.This approach enhances the rigidity of the machine components.
- During structural optimization, key parts undergo topology optimization to improve the machine’s static and dynamic performance.
How to Achieve High Performance and High Reliability
High Performance
The machine uses a high-speed electric spindle with two internal speed ranges. The low-speed range provides high torque, ensuring excellent low-speed machining performance. The high-speed range ensures precise machining at higher speeds. The spindle features a forced constant temperature cooling system, effectively controlling heat deformation during machining. The standard spindle ring-spray cooling function delivers highly accurate and powerful cooling, greatly protecting the cutting tools, and improving machining efficiency and performance. For even better results, an optional high-pressure coolant-through-spindle function can be selected.
High Reliability
- Early-stage fault testing enhances machine reliability, especially through experiments on key components like the spindle, tool magazine, automatic tool changer, and worktable pressure resistance. Rigorous testing reduces failure rates during later use.
- Continuous analysis of alarms and fault information drives improvements in component design. For example, long-term experience has helped optimize clearance to prevent tool magazine jams.
- Finite element analysis enhances both dynamic and static rigidity of components, and improvements in processes, manufacturing, and assembly increase overall reliability.
- We choose high-quality, well-known brand components and outsource parts with strict quality standards to further enhance machine reliability.
Additional Technical Guarantees
Every machine undergoes servo optimization and ball-bar testing before leaving the factory to maximize performance, reliability, and precision. The ball-bar test checks and compensates for assembly precision, contour accuracy, and backlash in the motion system. Servo optimization software fine-tunes the CNC system to suppress vibrations, improve machining progress, enhance surface quality (roughness), and reduce machining time.
Vibration Suppression Optimization
Servo optimization software detects vibrations in the machine and uses the system’s vibration suppression features to control vibrations. This increases cutting speed, reduces surface roughness, and enhances machining efficiency.
Contour Accuracy Optimization
Functions like feedforward control and friction error compensation improve the contour machining accuracy of CNC machines, ensuring precise results in demanding applications.
High-Speed, High-Precision Cutting Optimization
Optimizing parameters such as velocity gain, feedforward, and fine acceleration/deceleration compensates for dynamic errors and improves frequency response. These adjustments ensure the machine reaches its best state, with improved servo stiffness and response. This increases the accuracy of small-line machining (ideal for mold production), reduces surface roughness, and shortens machining time significantly.
Conclusion
The MDH series horizontal machining centers integrate four key advantages: high precision, high rigidity, high speed, and high reliability, fully meeting diverse machining needs. Using spindle temperature compensation, hollow-cooled ball screws, and the FANUC thermal error compensation system, they significantly improve machining accuracy. The high-rigidity structure, optimized through finite element analysis, ensures long-term stability. High-speed guides and a servo system enable fast movements and efficient cutting, while the variable-speed automatic tool changer system greatly boosts production efficiency.
Additionally, rigorous pre-delivery testing and servo optimization ensure consistent performance and reliability. The MDH series offers an ideal machining solution, balancing precision, efficiency, and stability to meet the strict demands of complex machining scenarios.
If you have any questions about this machine or want to learn more about its specific features and applications, feel free to contact us anytime! MINNUO is ready to provide professional solutions for your machining needs!