In today’s era of smart manufacturing, CNC machine tools have become a key tool for enhancing productivity. Among them, slant bed CNC lathes are especially popular due to their outstanding stability and flexibility in machining. From automotive parts to aerospace components, from mass production to custom machining of complex parts, these machines are capable of handling nearly any task. Among the many options available, the DT Series slant bed CNC lathe stands out as the top choice for many manufacturing companies due to its excellent performance and high adaptability.
The DT Series is a perfect example of both technology and design. It achieves flexibility through modular design, allowing free combinations of components like the servo tool turret, hydraulic tailstock, and sub-spindle to meet various machining needs. At the same time, the use of high-rigidity roller guides, pre-stretched ball screws, and spindle temperature compensation technology ensures that the machine’s precision far exceeds industry standards. Moreover, the option for chip removal from the right side or rear adds to its versatility, making it ideal for high-speed automated production. Efficiency, precision, and flexibility come together perfectly in the DT Series, which is why it leads the industry.
Whether for high-precision short shaft machining or the production of complex multi-face parts, the DT Series can handle it with ease. Next, we will explore its core technological advantages and real-world applications to see how it can help you improve efficiency and optimize costs.
The Technology and Advantages of Slant Bed Design
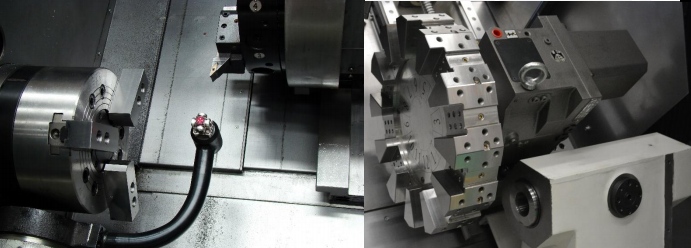
Core Advantages of Modular Design
Flexible Configuration to Meet Diverse Machining Needs
The DT Series CNC lathe supports the free combination of various functional modules, such as servo tool turrets, hydraulic tailstocks, sub-spindles, and Y-axis functions. This flexibility allows users to configure the machine based on their specific production requirements and create customized machining solutions. For example:
- For short shaft parts, users can select a high dynamic response servo tool turret and powered tooling for turning and milling operations.
- For long shaft parts, the hydraulic tailstock provides strong support, ensuring machining stability and precision.
- For complex or multi-face machining, users can choose the sub-spindle and Y-axis modules for integrated front-and-back machining, reducing clamping times.
Optimized Process Flow to Enhance Production Efficiency
Modular design allows multiple functional modules to be efficiently integrated into one machine. For example:
- The sub-spindle module supports machining different surfaces on the same equipment, avoiding the need for part transfers between multiple machines, saving time and increasing production speed.
- With the powered tool turret and servo tool turret configurations, the DT Series easily performs compound operations like milling and drilling, reducing process steps and shortening overall machining time.
Lower Equipment Investment to Save Production Costs
Modular design significantly reduces the need for multiple machines by integrating several functions into a single device. For example, tasks that would typically require both a lathe and a milling machine in traditional setups can now be completed with just one machine in the DT Series. This configuration reduces equipment purchase costs, saves space, and lowers maintenance costs in the long run.
Main Modules and Function Analysis
Servo Tool Turret
- High Dynamic Response: Supports powered tools with fast tool change speeds and smooth tool switching, ideal for compound machining requirements.
- Multiple Tool Positions: The 12-position servo-powered tool turret can carry a wide range of tooling configurations, meeting the needs of complex part machining.
Hydraulic Tailstock
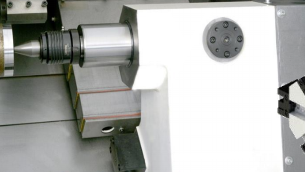
- Strong Support: Provides robust axial support, suitable for machining long shaft parts.
- Servo Control Option: The programmable tailstock enables precise feeding and retraction, simplifying the operation process and reducing manual intervention.
Sub-Spindle Module
- Integrated Front-and-Back Machining: The sub-spindle module allows the machine to complete both sides or multiple surfaces of a part in one setup, significantly reducing clamping time and positioning errors.
- High-Speed Support: The sub-spindle can reach speeds of up to 5,000 rpm, ensuring efficient cutting.
Y-Axis Function
- Eccentric Machining Support: The Y-axis travel of ±50mm enables machining of complex shapes, such as eccentric holes and keyways, expanding machining capabilities.
- Multi-Surface Machining Capability: Combined with the powered tool turret, the Y-axis supports multi-axis linked operations, particularly suited for asymmetric parts.
Multiple Chip Removal Options
The machine tool supports chip removal from either the right side or the rear, allowing users to choose based on the workshop layout and automation needs. This adaptable design makes it easier for the machine to integrate into the production line. It is especially effective in high-speed automated machining environments, where its flexibility stands out.
Performance Features of the DT Series
1. Outstanding Precision
The core precision indicators of the DT Series slant bed CNC lathe exceed national standards by more than 50%, ensuring high machining accuracy. This is made possible by the use of high-rigidity roller guides and high-quality ball screws, along with spindle temperature compensation technology that significantly reduces errors caused by thermal deformation.
High-Rigidity Roller Guides: Ensuring Load Capacity and Stability
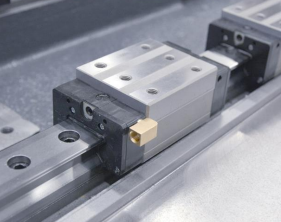
- Design and Features of Roller Guides
The DT Series CNC lathe uses high-rigidity roller linear guides on the X/Z axes. Key features include:
- High Load Capacity: Compared to traditional ball guides, roller guides offer a larger contact area and significantly improved load-bearing capacity.
- Low Friction and Long Service Life: Roller guides have a lower coefficient of friction under heavy loads, ensuring smooth movement and longer service life.
- Excellent Dynamic Response: The rigid structure of the roller guides provides better dynamic stability during high-speed cutting, ensuring machining accuracy is not affected by vibration.
High-Quality Ball Screws: The Key to Motion Accuracy
- Bi-Directional Pre-Stretch Structure
The DT Series uses pre-stretched ball screws, where tension is applied to both ends of the screw to eliminate thermal expansion during high-speed motion. This design offers the following advantages:
- Ensured Linear Accuracy: The pre-stretch eliminates position errors caused by thermal deformation, maintaining linear motion precision.
- Improved Torsional Rigidity: It enhances the screw’s torsional rigidity during rapid feeding and heavy-duty machining, improving overall machining stability.
- Precision Processing and Installation of Ball Screws
- The screws are made from high-quality materials and processed with high precision, achieving a positioning accuracy of 0.008mm.
- Special calibration equipment and processes are used during installation to ensure the coaxiality between the ball screw and guide, reducing cumulative errors during operation.
Spindle Temperature Compensation Technology: Intelligent Dynamic Accuracy Adjustment
- Impact of Temperature on Accuracy
During high-speed operation, the spindle experiences thermal deformation due to cutting friction and changes in ambient temperature. This deformation directly impacts machining accuracy, leading to dimensional errors and even part scrap. - Implementation of Temperature Compensation Technology
The DT Series CNC lathe solves this issue with its spindle temperature compensation system:
- Real-Time Temperature Control System
Temperature sensors continuously monitor spindle temperature, and the cooling oil circulation system adjusts the temperature quickly to keep it within a stable range. - Error Compensation Algorithm
The CNC system has built-in thermal error compensation software that automatically adjusts the machining position based on collected temperature data, eliminating errors caused by thermal deformation. - Improved Machining Stability
With this technology, thermal expansion in the spindle during prolonged operation is effectively suppressed, ensuring consistent machining accuracy.
2. High Speed and High Efficiency
The spindle of the DT Series CNC lathe reaches a maximum speed of 4500 rpm. Combined with the servo-powered tool turret, it can complete complex machining tasks more efficiently. Additionally, the optimized feed system significantly improves the rapid movement speeds of the X/Z axes, shortening machining cycles.
3. Multi-Function Expansion Capability
The DT Series supports the configuration of a Y-axis and synchronous operation of the main and sub-spindles, making it ideal for machining complex-shaped parts. This functionality allows the machine to not only perform standard turning tasks but also execute milling, drilling, and other compound machining operations, offering users a broader range of machining capabilities.
Typical Application Scenarios
The DT Series slant bed CNC lathe is widely used in various industries due to its stability and adaptability:
- Automotive Parts: Ideal for the efficient machining of engine blocks, shafts, gears, and other components.
- Aerospace: Used for machining complex rotational parts, meeting high-precision requirements.
- Energy Equipment: Suitable for high-rigidity cutting tasks of large parts.
- General Machinery: Flexible for both mass production and small-batch custom machining needs.
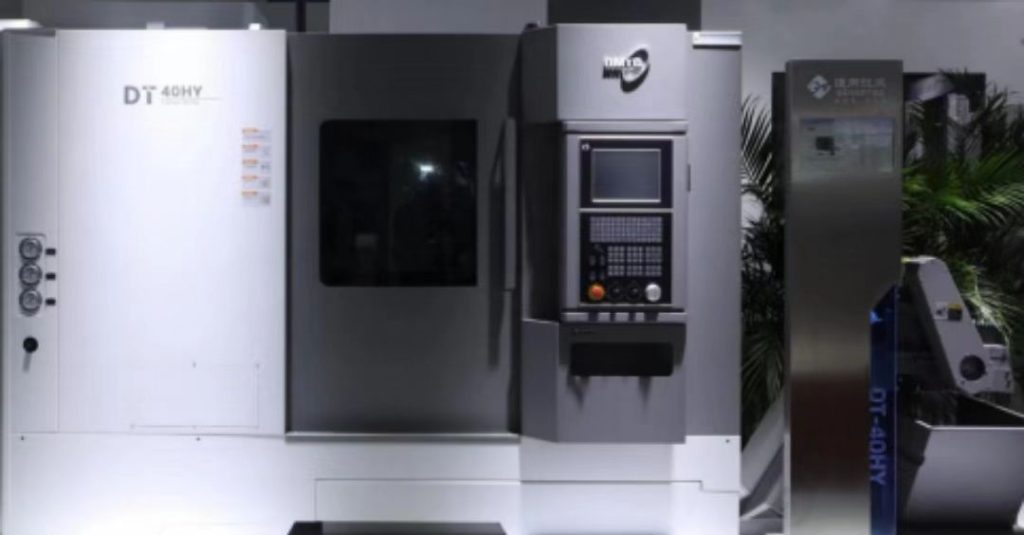
Why Choose MINNUO‘s DT Series?
MINNUO Machine Tools relies on over 80 years of technological expertise and modern production lines to ensure that the DT Series consistently leads the industry in quality, performance, and service. Key advantages include:
- Quality Assurance: Each machine undergoes double inspection according to international standards to ensure it meets stringent precision requirements before leaving the factory.
- Technical Support: A comprehensive after-sales service system and a professional technical team provide efficient solutions to customers.
- Intelligent Upgrade Potential: The DT Series is compatible with Industry 4.0 technology, supporting the transformation and expansion of intelligent production lines.
Conclusion
The DT Series slant bed CNC lathe offers excellent performance, flexible configuration, and wide adaptability, providing efficient machining solutions for the manufacturing industry. Whether you are seeking extreme machining precision or aiming to improve production efficiency, this series can meet your needs. If you are interested in the DT Series, we encourage you to explore its modular configurations and real-world application cases. Our MINNUO team will provide tailored professional support to meet your specific requirements.