The rapid development of CNC technology is leading the manufacturing industry into the era of smart manufacturing. As the “heart” of CNC machines, the CNC spindle not only determines the precision and efficiency of machining but also plays a key role in high-end manufacturing. From mass production of automotive parts to the precision machining of complex surfaces in aerospace, CNC spindles have become an essential piece of equipment for efficient manufacturing. Choosing the right spindle to meet your specific needs directly impacts production efficiency and market competitiveness.
There are many types of CNC spindles, with different drive methods, performance parameters, and cooling systems. The variety of options can confuse many businesses when it comes to selecting the right one. For high-end processing that requires extreme precision, a high-speed spindle is crucial. On the other hand, for heavy cutting or multi-tasking applications, high torque and stability are essential. With so many different needs, understanding spindle types and their characteristics is the first step to improving production efficiency.
This article will start by defining and classifying CNC spindles, then systematically analyze how to choose the best CNC spindle for your specific processes, based on real-world applications and technical characteristics.
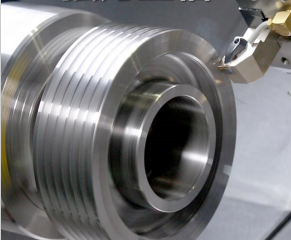
Types of CNC Spindles
Classification by Drive Method
(1) Belt-driven Spindle: The motor and spindle are connected by a belt, making it suitable for medium to low-speed machining.
(2) Gear-driven Spindle: Gears transmit power to the spindle, making it ideal for heavy cutting scenarios that require high torque.
(3) Direct-drive Spindle: The motor directly drives the spindle without a transmission mechanism. This design is common in modern high-end machine tools.
Classification by Purpose
(1) Tool-driving Spindle: This spindle drives the rotation of tools and is commonly found in milling machines, drilling machines, and machining centers. It operates at high speeds and high precision, making it ideal for cutting various materials.
(2) Workpiece-holding Spindle: This spindle is used to rotate the workpiece and is primarily used in lathes. The spindle speed is variable and suitable for workpieces of various sizes and weights.
(3) Specialized Spindle: Designed for specific machining needs, such as grinding spindle or woodworking machine spindles. These spindles are optimized based on the process and have targeted functions.
Classification by Cooling Method
(1) Natural Cooling Spindle: This spindle relies on air convection for heat dissipation, without the need for additional cooling equipment.
(2) Air-cooled Spindle: A fan or airflow dissipates the heat generated by the spindle during operation.
(3) Water-cooled Spindle: A water circulation system cools the spindle, commonly used in high-speed and heavy-load machining applications.
CNC Spindle Applications
Turning Machining
The CNC spindle is responsible for holding and rotating the workpiece. With stable speed control, it ensures the smoothness of the machined surface and can withstand large radial and axial forces, making it suitable for workpieces of various sizes and weights. It is widely used in precision machining of automotive components, such as shafts and gears, as well as the manufacturing of large machine component housings.
Milling Machining
The spindle mainly drives the tool rotation to complete milling, drilling, and tapping operations. Its high-speed, high-precision performance is ideal for machining complex curved surfaces. When combined with multi-axis coordination technology, it enables efficient multi-angle and multi-surface machining. It is commonly used in mold manufacturing and the production of precision parts for the aerospace industry.
Grinding Machining
The spindle drives the grinding wheel at high speeds to achieve precise grinding of the workpiece surface. It features high rigidity and high-speed capabilities, ensuring a smooth grinding surface while requiring a stable cooling system to prevent heat deformation that could affect machining accuracy. Typical applications include the processing of precision bearing inner and outer rings, as well as surface finishing for optical instruments and medical equipment.
Drilling and Tapping Machining
The spindle drives the drill bit or tap to perform precision hole machining. It provides high torque to meet the tapping resistance requirements and adjusts speed to accommodate different material processing needs. It is widely used in the electronics industry for PCB drilling and in the manufacturing of threaded holes in precision equipment housings.
Composite Machining Centers
The spindle must handle various operations such as turning, milling, and drilling, showcasing its powerful multitasking capability. It allows multiple processes to be completed with a single setup, significantly improving machining efficiency. This is commonly seen in integrated manufacturing of automotive engine blocks and large, complex components.
Specialized Machining
The CNC spindle also plays a key role in processes like laser cutting, water jet machining, and woodworking carving. By adapting to specific parameters, it ensures precision operations and efficiently processes non-metallic and special materials. Examples include adjusting lenses in laser cutting and pattern machining in woodworking engraving machines.
Advantages of CNC Spindles
High Precision Intelligent Control
Our CNC spindles use temperature compensation and closed-loop control technology to monitor and adjust the spindle’s thermal deformation in real-time. This ensures that machining accuracy is maintained even during extended high-load operations. Equipped with high-resolution sensors and supported by FANUC CNC systems, the spindle achieves micron-level positioning accuracy and surpasses industry standards for repeatability. This makes it ideal for precision-demanding industries like aerospace and mold manufacturing.
Modular High-Rigidity Design
Minnuo’s CNC spindles are optimized through finite element analysis and feature a modular design. Both the spindle body and bearing system are made from high-rigidity materials, capable of withstanding heavy cutting and high-impact forces in complex working conditions. The spindle’s high dynamic response ensures a balance between machining efficiency and quality, particularly excelling in heavy workpieces and high-torque scenarios.
Flexible and Efficient Drive Options
Our CNC spindles support various drive modes, including direct-drive electric spindles and gear-driven spindles, catering to both high-speed precision machining and low-speed heavy cutting. The high-speed electric spindle reaches up to 12,000 rpm, making it suitable for complex surface machining, while the gear-driven spindle, designed for high torque, is perfect for heavy-duty cutting. This demonstrates Minnuo’s deep understanding of diverse machining needs.
Intelligent Integration and Cooling System
The CNC spindle comes equipped with an internal cooling and high-pressure cooling system that precisely controls spindle temperature, significantly reducing errors caused by overheating. The intelligent cooling unit, combined with thermal error compensation algorithms, keeps temperature fluctuations to a minimum, further enhancing machining quality. Additionally, the automatic lubrication and real-time monitoring systems effectively extend the spindle’s lifespan and reduce maintenance costs.
Reliability and Long Service Life
From the outset, our CNC spindles are designed with durability in mind. Through rigorous durability testing and vibration-optimized designs, the spindle runs more smoothly, and its mean time between failures (MTBF) far exceeds industry standards. High-quality components, such as Japanese NSK bearings and imported ball screws, provide reliable support for long-term, stable spindle operation.
Diverse Application Scenarios
With exceptional performance, Minnuo’s CNC spindles are widely used in industries like automotive parts machining, aerospace engine manufacturing, and rail transportation component production. From precision machining to mass production, our CNC spindles efficiently meet customer demands and provide comprehensive support for smart manufacturing.
CNC Spindle Maintenance and Care
Daily Maintenance of CNC Spindles
(1) Keep it Clean
- Regularly clean the exterior of the spindle and spindle housing to prevent chips, dust, and other contaminants from accumulating, which can affect heat dissipation and operation.Clean the spindle taper hole and tool interface to ensure there is no oil or residue, improving clamping stability and precision.
- Regularly check the lubrication system to ensure that the spindle bearings and drive components are adequately lubricated.Ensure the cooling system (such as internal or oil cooling) is functioning properly. Replace the cooling fluid periodically to maintain effective heat dissipation.
- Install spindle monitoring devices to check key parameters such as temperature, vibration, and speed. Any abnormal signals, such as high temperature or excessive vibration, should be investigated immediately.
- Pay attention to the spindle’s service life, and record the cumulative running time. Perform professional maintenance or replace worn components at the specified intervals.
CNC Spindle Fault Repair
(1) Common Fault Analysis and Solutions
- Spindle Overheating:
- Cause: Insufficient lubrication, failure of the cooling system, or prolonged high-speed operation.Solution: Check if the cooling system is blocked, ensure adequate lubrication, and reduce load if necessary.
- Cause: Damaged bearings, reduced balance, or improper cutting parameters.Solution: Inspect and replace bearings, recalibrate the spindle balance, and optimize the cutting parameters.
- Cause: Leaks in the pneumatic clamping system or wear in the clamping devices.Solution: Check the air circuit seals and replace damaged components.
- Ensure the maintenance environment is clean and tidy to prevent contamination of the spindle during servicing.
- Use the recommended tools and parts from the manufacturer to avoid secondary damage due to compatibility issues.
- After maintenance, perform dynamic testing, including speed, temperature rise, and vibration checks, to confirm that the spindle meets performance standards before resuming use.
Tips to Extend CNC Spindle Life
- Use the spindle reasonably to avoid overloading or operating at extreme speeds for long periods.
- Select the appropriate tools and processing parameters to reduce excessive wear on the spindle and tools.
- Conduct a comprehensive annual inspection of the spindle, and replace worn or aged components in time to ensure long-term stable operation.
How to Choose the Right CNC Spindle for Your Application
The Best Solution to Meet Your Processing Needs
Different processing scenarios require different types of spindles.
- If you pursue high-efficiency production: Minuo’s high-speed electric spindle is your best choice. With speeds of up to 12,000 rpm, it is ideal for high-precision applications like mold processing and complex surface machining. This spindle easily meets the high standards of modern industrial manufacturing.
- If you focus on heavy cutting: For machining engine blocks, gears, and similar components, our high-torque gear spindle (with a maximum torque of 1529 Nm) is designed specifically for heavy-duty cutting. It ensures stable performance even under high loads.
- If you want flexibility: The dual-speed spindle combines low-speed, high-torque capabilities with high-speed precision machining, allowing a single machine tool to handle multiple tasks. This greatly enhances the adaptability of your equipment.
Whether you are engaged in mass production or high-precision small-batch customization, we can provide the right spindle solution for your needs.
Outstanding Performance for More Efficient and Precise Machining
The CNC spindles from Minuo Machine Tool stand out in performance, helping you easily meet tough processing demands with cutting-edge technology:
- Stable at high speeds, ready for any challenge: The spindle is equipped with temperature compensation and an internal cooling system. Even during long hours of high-speed operation, it maintains accuracy. With fast tool change technology (tool-to-tool time as low as 2 seconds), you can significantly reduce processing cycles, improving overall efficiency.
- Powerful torque, showcasing strength: The high-torque spindle provides up to 1529 Nm of output, enabling smooth performance even during heavy-duty or hard material machining. With strong power and stable cutting, it enhances overall workpiece quality.
- Smart design reduces wear: The internal cooling and high-pressure lubrication system protect both the tool and the spindle, extending the equipment’s lifespan while making operation more cost-effective.
These advanced features not only improve machining quality but also optimize production costs, ensuring that every investment delivers great value.
Full Lifecycle Support for Worry-Free Operation
We understand that choosing a spindle is not just about meeting current needs, but also ensuring future sustainability. The spindle solutions we offer at Minuo Machine Tool not only provide excellent performance but also help save costs over time:
- Low maintenance costs: Our spindles have an average time between failures (MTBF) that far exceeds industry standards. They require minimal maintenance and run stably, reducing downtime on your production line and increasing efficiency.
- High scalability: Depending on your needs, you can equip your spindle with various smart modules, such as high-pressure cooling devices and tool detection systems. This allows you to easily adapt to future production upgrades.
- Comprehensive service: We provide customized spindle selection advice, installation guidance, and after-sales support to ensure your equipment always operates at its best.
A Win-Win Choice for Quality and Efficiency
Minnuo Machine Tool is committed to providing customers with efficient, cost-effective, and reliable processing solutions. Whether you seek high precision, high efficiency, or overall cost performance, our CNC spindles will be a powerful tool in helping you achieve your goals. By choosing Minuo Machine Tool, you are not just choosing equipment—you are choosing a long-term guarantee for efficiency, quality, and trust.
Conclusion
The CNC spindle is the core component of machine tools. It not only determines the equipment’s machining performance but also greatly impacts production efficiency and product quality. Based on outstanding technology, Minnuo Machine Tool focuses on providing customers with high-precision, high-reliability, and diversified CNC spindle solutions. Our spindle products cover high-speed, high-torque, and multi-tasking functions. Whether you need precision machining, heavy cutting, or complex surface processing, we can tailor the optimal solution for you. Contact us today, and let’s create your next success story together!