As manufacturing technology continues to advance, waterjet cutting has emerged as a key solution in the processing industry due to its versatility and high precision. Particularly in the realm of thick material cutting, waterjet technology has demonstrated advantages that surpass those of laser and plasma cutting, making it a preferred choice across various industries.
The thickness that a waterjet can cut depends on several critical factors, including water pressure, material properties, abrasive parameters, and cutting speed. Under optimal conditions, waterjets can cut through materials over 300 millimeters thick, such as steel, stainless steel, stone, and composites. Additionally, compared to other cutting methods, waterjets maintain a heat-free cutting process and high-quality results across a wider thickness range, making them the premier choice for thick material processing.
This article provides an in-depth analysis of the key factors affecting waterjet cutting thickness, the unique capabilities of waterjets in handling thick materials, and a comparison of waterjet cutting with other cutting methods.
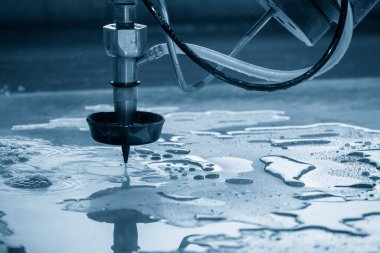
Factors that Influence a Waterjet’s Upper Thickness Limit
Waterjet cutting is renowned for its versatility and precision, but its maximum cutting thickness is not a fixed value. Instead, it is influenced by a variety of factors, ranging from the equipment configuration to the properties of the material being cut. These factors determine the efficiency, quality, and overall capability of waterjet cutting systems when dealing with different thicknesses. Below is a detailed exploration of the critical factors that influence a waterjet’s upper thickness limit.
Water Pressure: The Core Driving Force
The waterjet’s ability to cut through material relies heavily on the water pressure it generates.
- Pressure Levels: Most industrial waterjets operate at pressures between 60,000 to 90,000 psi. Higher pressure levels allow for deeper penetration into thicker materials. However, extreme pressures may require specialized equipment to maintain system stability and efficiency.
- High-Performance Pumps: Advanced intensifier pumps or direct-drive pumps provide steady and powerful pressure, which is essential for cutting thick materials consistently.
Material Properties: The Nature of the Target Material
The characteristics of the material being cut play a crucial role in determining the achievable cutting thickness.
- Hardness and Density: Hard materials like titanium or stainless steel are more challenging to cut and have a lower thickness limit compared to softer materials like aluminum or plastics.
- Material Structure: Homogeneous materials such as stone are easier to cut to greater depths, whereas layered or composite materials may pose challenges due to their internal inconsistencies
Abrasive Type and Parameters: The Cutting Edge of the Process
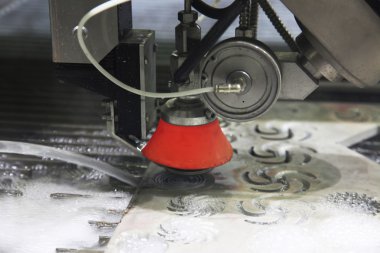
Abrasives are a critical component in waterjet cutting, especially for hard or thick materials.
- Abrasive Selection: Garnet is the most commonly used abrasive due to its hardness and durability, making it ideal for thick materials. Other abrasives like silicon carbide or quartz may be used for specific needs but might limit cutting capacity.
- Abrasive Flow Rate: The flow rate of abrasives must be carefully calibrated. Too low a rate reduces cutting efficiency, while too high a rate can lead to wastage or surface degradation.
- Abrasive Size: Finer abrasives provide precision for thinner materials, while coarser abrasives are better for cutting greater thicknesses.
Cutting Speed: Balancing Efficiency and Depth
The cutting speed significantly impacts the waterjet’s ability to handle thick materials.
- Slower Speeds for Greater Depths: Reducing the cutting speed allows the waterjet to focus its energy more effectively on thicker materials, achieving deeper penetration.
- Faster Speeds for Efficiency: While faster speeds can increase productivity, they may limit the maximum thickness that can be cut.
Nozzle Design and Maintenance: The Key to Performance
The nozzle is a critical component of the waterjet system, and its design and condition directly influence cutting capabilities.
- Nozzle Diameter: A larger nozzle diameter allows higher flow rates of water and abrasives, enabling the cutting of thicker materials. However, this may reduce precision.
- Nozzle Material: High-quality materials like tungsten carbide or diamond enhance durability, ensuring consistent performance over extended periods.
- Nozzle Wear: A worn nozzle can disperse the waterjet stream, reducing cutting efficiency and limiting thickness capacity. Regular maintenance is essential.
Environmental and Operational Factors
External conditions and operator expertise can also affect the maximum cutting thickness of a waterjet.
- Water Quality: Impurities in the water can clog the system or reduce pressure, limiting cutting performance.
- Operator Skill: Experienced operators can optimize settings based on material and system characteristics to maximize thickness capabilities.
- Machine Stability: Cutting thick materials requires a stable system with minimal vibration to maintain precision and prevent structural damage.
How Thick Can Waterjet Cut?
The maximum cutting thickness of a waterjet depends on several factors, including the equipment’s specifications, the material properties, and the cutting parameters. Generally, industrial waterjets can cut materials ranging from a few millimeters thick to over 300 millimeters, with some specialized setups achieving even greater thicknesses. Below is a detailed exploration of the cutting thickness capabilities of waterjets for different materials and conditions.
Typical Cutting Thickness for Common Materials
The cutting thickness of a waterjet varies significantly depending on the type of material:
Metals
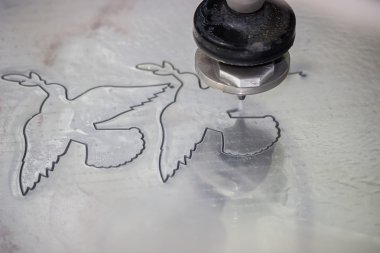
- Steel and Stainless Steel: Commonly cut between 50 to 150 millimeters, waterjets can handle extreme cases up to 250 millimeters or more, depending on the system’s configuration.
- Aluminum and Light Metals: With lower density, aluminum can be cut to over 200 millimeters with ease, and sometimes beyond.
- Titanium: Known for its strength and durability, titanium is typically cut up to 100–150 millimeters thick with a waterjet.
Non-Metals
- Stone: Materials such as granite and marble can be cut to depths of 100–200 millimeters, with a maximum range exceeding 300 millimeters in some cases.
- Glass: While glass can be cut accurately, its brittleness limits thickness to around 50–100 millimeters. Special laminated or safety glass may accommodate greater depths.
- Composites: Layered or fiber-reinforced materials vary widely in thickness capacity but generally fall within 50–150 millimeters.
Other Materials
- Plastics and Foam: Due to their low density, plastics and foam can often be cut to over 300 millimeters, with minimal resistance.
What Are the Benefits of Cutting Thick Material with a Waterjet Cutter?
Cutting thick materials can be challenging for many traditional methods, but waterjet cutters offer several unique advantages that make them an excellent choice for this task. From precision and versatility to environmental friendliness, waterjets excel at handling even the most demanding thick material cutting applications. Below are the key benefits:
No Heat-Affected Zone (HAZ)
One of the most significant advantages of waterjet cutting is its cold-cutting process.
- Preserves Material Properties: Since no heat is generated, the material’s structural integrity remains intact, which is crucial for metals like titanium and high-strength steels.
- Prevents Cracking: Fragile materials such as glass or ceramics can be cut without the risk of thermal cracking or warping.
Exceptional Precision and Quality
Waterjet cutters maintain high precision even when cutting thick materials.
- Smooth Edges: Cuts are clean and smooth, eliminating the need for secondary finishing in most cases.
- Consistent Performance: Waterjets can maintain precision across varying thicknesses, ensuring reliable results for detailed designs or complex geometries.
Versatility Across Materials
Waterjet cutters are capable of cutting a vast range of materials regardless of thickness.
- Metallic and Non-Metallic Materials: From steel and aluminum to stone and composites, waterjets handle all with ease.
- Layered and Composite Materials: Waterjets can cut through layered materials without delamination or damaging the internal structure.
Eco-Friendly and Safe Operation
Waterjet cutting is an environmentally friendly process with minimal waste.
- No Harmful Emissions: Unlike methods that generate fumes or heat, waterjets produce no toxic gases or pollutants.
- Cleaner Work Environment: The absence of slag or sparks ensures a safer and cleaner workspace.
Cost-Effective for Thick Materials
Although initial setup costs for waterjet systems may be higher, they offer cost savings in the long run:
- No Tool Changes: Unlike mechanical cutting, waterjets don’t require frequent tool replacements when working with varying thicknesses.
- Reduced Material Waste: Waterjet’s precise cuts minimize material loss, especially valuable for expensive materials like titanium or exotic alloys
Ability to Handle Extreme Thickness
Waterjets are among the few cutting technologies that can manage extremely thick materials.
- Single-Pass Cutting: Waterjets can cut through thick materials in a single pass, avoiding the need for multiple cuts or steps.
- Adaptability: By adjusting parameters like cutting speed and abrasive flow, waterjets can tackle thicknesses that are beyond the capabilities of many other cutting methods.
Comparing Waterjet Cutting Thickness with Other Cutting Methods
Waterjet cutting stands out in handling thick materials compared to other technologies:
- Laser Cutting: Best suited for thin to medium-thickness materials, typically up to 30mm. Beyond this, efficiency and quality decline significantly.
- Plasma Cutting: Effective for cutting metal up to 50mm thick but struggles with precision and surface quality as thickness increases.
- Mechanical Cutting: Capable of cutting extremely thick materials but is time-consuming, unsuitable for complex shapes, and prone to thermal effects.
For more detailed comparative analyses, visit our dedicated page:
- Waterjet vs. Electrical Discharge Machining (EDM)
- Waterjet vs. Plasma Cutting
- Waterjet vs.CNC Laser Cutting
Endnotes
Waterjet technology has gained popularity for its ability to handle a wide range of cutting requirements, from thin materials a few millimeters thick to dense metals or composites over 12 inches thick. Its precision and versatility make it an essential tool for many industries.
Should you have any questions about waterjet cutting technology or need assistance selecting the right product for your project, don’t hesitate to contact MINNUO. Our expert team is always ready to provide answers and help you find the best solution.