Machine tools are the core equipment of modern manufacturing. They produce a wide variety of parts through precision cutting, forming and machining operations. Whether it is the automotive, aerospace or electronics industry, machine tools play a vital role. For manufacturers, it is crucial to understand and choose the right type of machine tool, which is not only related to production efficiency, but also affects the quality of the final product.
Machine tools are essential for precision manufacturing and include seven basic types: lathes, milling machines, drilling machines, grinding machines, shaping machines, planing machines, and sawing machines. Each type is designed for specific tasks such as turning, cutting, drilling, grinding, and shaping materials.
This article will introduce seven basic machine tool types in detail and explore their functions, common applications, advantages and limitations to help you make an informed decision when choosing a machine tool.
Overview of the Basic Types of Machine Tools
- Lathes
- Milling Machines
- Drilling Machines
- Grinding Machines
- Shaping Machines
- Planing Machines
- Sawing Machines
Detailed Breakdown of Each Machine Tool Type
1. Lathes

Lathes are versatile machines designed to rotate a workpiece while a cutting tool removes material from it. They are primarily used for turning operations, which can shape cylindrical, conical, or spherical parts.
Common Applications: Lathes are widely used in industries for producing parts such as shafts, spindles, bushings, and other rotating components. They are commonly found in automotive, aerospace, and toolmaking industries.
Advantages:
- Precision: Lathes provide excellent dimensional accuracy and surface finish, especially in turning operations.
- Versatility: Lathes can handle various operations, such as facing, threading, and boring, depending on the attachments.
- Speed: They are ideal for high-volume, repetitive tasks, making them efficient for mass production.
Limitations:
- Limited Shape Options: Lathes are mainly suited for cylindrical parts and may not perform well when producing non-cylindrical or complex shapes.
- Additional Machinery: For tasks such as milling, drilling, or grinding, additional machines may be needed, increasing the overall cost.
Considerations: While lathes are versatile, the workpiece must be able to rotate, making them unsuitable for some types of non-rotational shapes or certain delicate operations.
2. Milling Machines
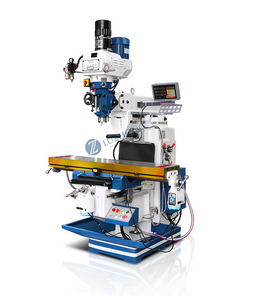
Milling machines use rotating cutters to remove material from a workpiece. They can operate horizontally or vertically, depending on the machine configuration, and are capable of performing a range of cutting, drilling, and boring tasks.
Common Applications: Milling machines are used for creating flat surfaces, grooves, slots, and complex contours. They are common in industries such as metalworking, mold making, and aerospace, particularly for parts requiring precision cuts and intricate designs.
Advantages:
- Multi-Functionality: Milling machines can perform multiple functions like drilling, cutting, and even some light turning operations. They are versatile and able to work with various materials.
- High Precision: With the ability to make intricate cuts, milling machines are ideal for creating precise components with complex geometries.
- Flexibility: Milling machines can be manually controlled or automated through CNC (Computer Numerical Control), offering flexibility in production.
Limitations:
- Complexity: Milling machines require skilled operators, particularly for complex tasks, as they may involve intricate programming and setup.
- Speed: While they are precise, milling machines may be slower for simple tasks like drilling or cutting.
Considerations: Milling machines are highly adaptable, but their performance depends on the operator’s skill and the material used. A CNC version increases accuracy but can raise costs and setup time.
3. Drilling Machines
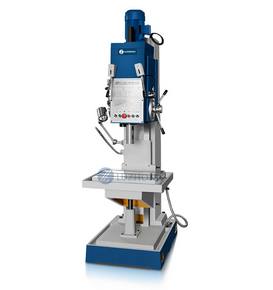
Drilling machines are designed to make holes in materials through rotary cutting action. They come in various types, including pillar drills, radial drills, and CNC drilling machines.
Common Applications: Drilling machines are essential for tasks requiring holes to be drilled in materials such as metal, wood, and plastics. They are used in applications like automobile assembly, aerospace components, and manufacturing of small and large parts.
Advantages:
- Specialized for Drilling: Drilling machines are optimized for precision hole-making, which they can perform quickly and efficiently.
- Simple Operation: They are easy to use and don’t require highly skilled operators for basic tasks.
- Cost-Effective: For drilling operations, they are relatively low-cost, making them ideal for high-volume production of hole-centric parts.
Limitations:
- Limited Operations: Drilling machines are specialized and can only handle operations like drilling, tapping, and reaming. They cannot handle more complex machining tasks like turning or milling.
- Hole Size Restrictions: While they can drill a variety of hole sizes, drilling machines are limited by the size of the tool and the material’s properties.
Considerations: Drilling machines are essential for operations that require repetitive, high-volume drilling of precise holes but are not as versatile for general machining tasks.
4. Grinding Machines
Grinding machines use abrasive wheels to remove material from a workpiece. They are used for finishing operations, where surface finish and precision are crucial. Types of grinding machines include surface grinders, cylindrical grinders, and internal grinders.
Common Applications: Grinding is used to achieve smooth finishes on parts, sharpen tools, and create high-precision dimensions. It is commonly employed in toolmaking, automotive, aerospace, and metalworking industries.
Advantages:
- High Precision: Grinding machines are known for their ability to achieve extremely tight tolerances and excellent surface finishes.
- Versatility: Grinding can be applied to a wide range of materials, including metals, ceramics, and plastics, and can be used for both surface and cylindrical grinding.
- Tool Sharpening: These machines are often used for sharpening cutting tools and other precision parts.
Limitations:
- Slower Process: Grinding is slower compared to other machining processes, and may not be ideal for high-volume production unless it’s automated.
- Tool Wear: Grinding wheels wear out faster than cutting tools used in turning or milling operations, requiring frequent replacements.
Considerations: Grinding is ideal for high-precision applications but may not be necessary for less critical processes. It’s best for finishing rather than rough machining.
5. Shaping Machines
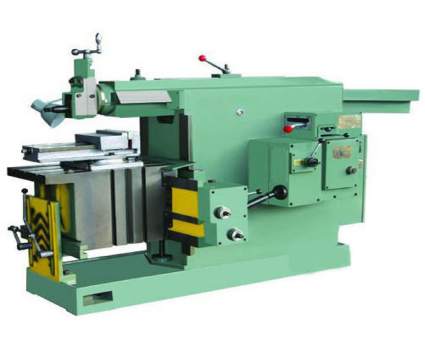
Shaping machines remove material using a single-point cutting tool, where the tool moves in a linear, reciprocating motion. They are ideal for creating flat surfaces and grooves on parts.
Common Applications: Shaping machines are used in tool and die making, as well as in applications requiring simple, flat surfaces, such as mold components and general machine parts.
Advantages:
- Simple Operations: Shaping machines are relatively easy to operate and suitable for small batch production or tool-making tasks.
- Cost-Effective: They are a more affordable option for producing flat surfaces when compared to more complex machines.
Limitations:
- Slow Speed: The reciprocating motion of shaping machines makes them slower than other machines, such as milling machines or CNC machines.
- Limited to Simple Geometries: While they can produce flat surfaces, they are not suitable for creating intricate or complex shapes.
Considerations: Shaping machines are best for simple, low-volume tasks but may not be the best option for high-speed or complex production runs.
6. Slotting machines
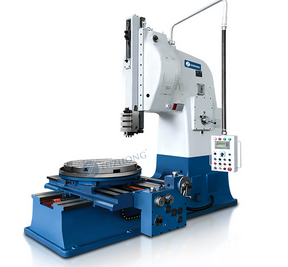
Slotting machines, like shapers, use a reciprocating motion to remove material from a workpiece. They are used primarily for larger parts that require a smooth finish on a flat surface.
Common Applications: Slotting machines are typically used to machine large parts like machine beds, molds, and frames.
Advantages:
- Heavy-Duty: Slotting machines are ideal for large, heavy parts due to their robust construction.
- Precision: Despite their size, Slotting machines can achieve high precision on large surfaces.
Limitations:
- Slow Processing: Slotting machines are not the fastest machines, and their slow speed makes them less suitable for high-volume production.
- Size Limitations: Slotting machines are designed for larger parts, so they are not practical for smaller, intricate components.
Considerations: Slotting machines are best for large-scale, heavy-duty operations but are limited in terms of versatility compared to modern CNC equipment.
7. Sawing Machines
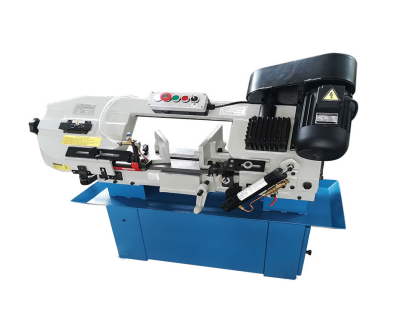
Sawing machines use a toothed blade or wire to cut materials into desired shapes. These machines include band saws, hacksaws, and circular saws.
Common Applications: Sawing machines are widely used for cutting metals, wood, and plastics. They are often used in construction, woodworking, and metalworking.
Advantages:
- Simple and Cost-Effective: Sawing machines are inexpensive and easy to operate, making them ideal for cutting tasks that require basic straight-line cuts.
- Versatility: Sawing machines can cut through a variety of materials, from thin sheets to thick blocks.
Limitations:
- Limited Precision: Sawing machines are not known for high precision and may leave rough edges, requiring additional finishing steps.
- Speed: While cost-effective, sawing can be slower compared to other machine tools when cutting thick materials.
Considerations: Sawing machines are perfect for simple, straight cuts and are valuable for initial material shaping but may not offer the precision needed for fine-tuning or intricate cuts.
Conclusion
Each type of machine tool has its own unique features and advantages. From lathes to milling machines, to grinders and saws, each machine tool plays an indispensable role in the manufacturing industry. When choosing a machine tool, you should consider factors such as the type of material being processed, the complexity of the part, and the required production speed. Understanding the advantages and limitations of each machine tool will help you make more informed decisions during the production process.
If you still have questions, you can always visit the official website and contact MINNUO, and we will provide you with more detailed answers!