The lathe machine is widely used in manufacturing, and cutting tools are essential on a lathe.People often find it confusing to choose the right lathe cutting tools, but don’t worry, this article will explain the detailed steps for selecting them.
Brief Introduction to Lathe Cutting Tools
Before you choose the right lathe cutting tools, it’s important to have some understanding about the tools.
What is Lathe Cutting Tools
Lathe cutting tools are the tools installed on a lathe used for cutting materials. They are responsible for carrying out cutting tasks on the lathe, ultimately completing the manufacturing of parts.
Types of Lathe Cutting Tools
Depending on their different features, lathe cutting tools can be divided into many types.
1. Based on Material:
- High-speed Steel:
High-speed steel is hard, wear-resistant, and can withstand high temperatures. It’s suitable for rough and semi-finishing work. Compared to other materials, it has a lower cost.
- Carbide:
Carbide is harder than high-speed steel and can be used to process both metals and nonmetals. Due to its high hardness and wear resistance, it is often used for parts that require complex operations, but it is more expensive.
- Diamond:
Diamond has extremely high hardness and wear resistance. It is usually used for complex surfaces and ultra-precision machining. It is very expensive.
- Cubic Boron Nitride:
Cubic boron nitride has hardness second only to diamond. It is typically used for machining super hard materials and high-hardness workpieces. It is relatively expensive.
2. Based on Feed Direction:
- Right-Hand lathe cutting tools:
This type of tool has its cutting edge facing to the right, used on a right-hand lathe to match the cutting direction.During machining, the tool moves from right to left.The outer turning tool and the cutoff tool are usually installed on the right side. The outer turning tool is typically used to work on the outer round surface of the workpiece, while the cutoff tool is commonly used for grooving and cutting the workpiece.
- Left-Hand lathe cutting tools:
This type of tool has its cutting edge facing left, suitable for left-side cutting operations. During machining, the tool moves from left to right. Boring tools are often installed on the left side and are used for machining the inside holes of a workpiece.
- Round Nose Lathe Cutting Tools:
This type of tool has a semi-circular cutting edge, able to move from left to right and from right to left. It’s typically used for making curved and smooth surfaces with rounded corners.
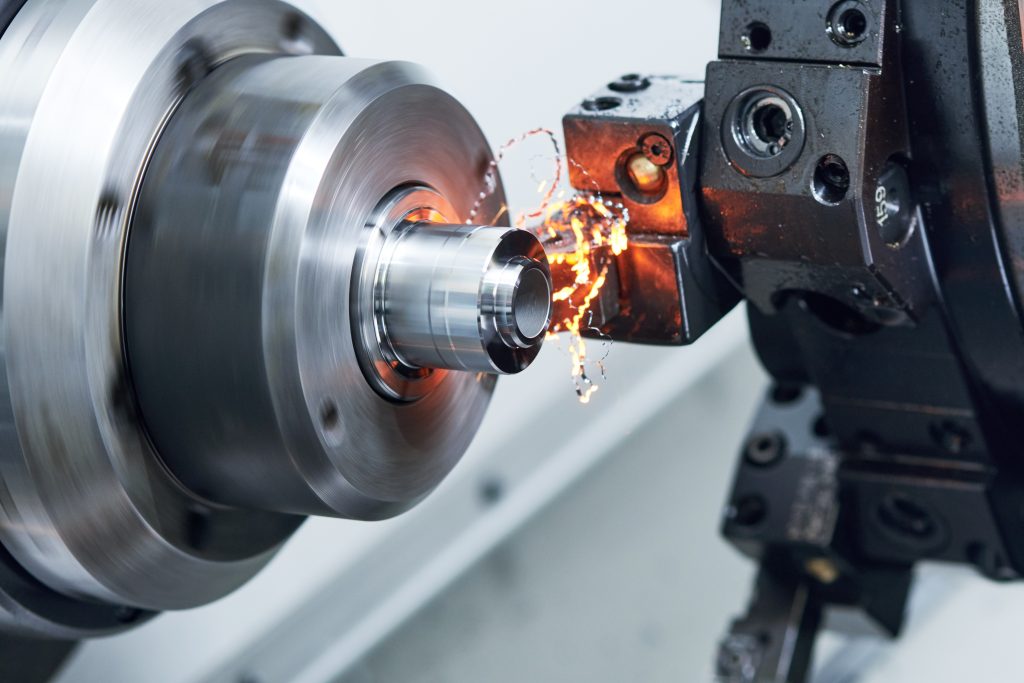
Confirm Your Needs and Make Choice
Tools are meant for cutting materials. Different materials, precision, and processing requirements determine what kind of tool is suitable and efficient. Therefore, choosing a tool begins with understanding your machining needs.
Materials:
- Hard Metals: When cutting hard metals like iron, steel, etc., the cutting material should be harder than the metal being cut. You can choose carbide or high-speed steel as cutting materials. Both of these materials are wear-resistant and can withstand high temperatures and pressures during the machining process.
- Soft Metals: When cutting soft metals like aluminum, copper, etc., you can choose high-speed steel tools. During the processing of soft metals, long chips are easily produced, and high-speed steel tools have good toughness to prevent tool breakage.
- Plastic:Plastic is a synthetic material made up of polymer compounds, it’s not as hard as metal, and you can choose carbide or high-speed steel tools. Plastic has poor heat resistance, so tool design must consider preventing the plastic from melting.
- Wood: Wood is less hard than metal and has a grainy structure. When choosing tools, you need to consider their stiffness and durability. You can choose carbide or high-speed steel tools.
Sizes:
- Large Size:You can choose large-sized turning tools that have strong rigidity and cutting power to meet your machining needs.
- Medium Size:You can choose standard turning tools or turning inserts. Turning inserts can be used for turning, roughing, and semi-finishing operations.
- Small Size:You can choose small diameter turning tools or micro turning tools to ensure machining precision and speed. Micro turning tools can be used to manufacture precision parts, while small diameter turning tools can ensure machining accuracy.
Shapes and Operations:
- When doing rough turning, you can choose carbide cutting tools. Carbide can withstand greater cutting force and impact due to its wear resistance and hardness.
- During finishing operations, which involve processing smooth surfaces, you can choose carbide cutting tools. The choice of tool material may vary depending on the material being cut.
- When turning inner holes, you can choose between boring tools and hole boring tools. Boring tools are for working on the inside surface of the hole, and for deeper holes, hole boring tools are the better choice.
- When turning the outer circle, you can choose between the outer turning tool or the internal and external circular arc cutting tool. The internal and external circular arc cutting tool can be used for chamfering and turning the outer circle radius.
- When cutting threads, you can choose thread cutting tools for working on both internal and external threads.
- When chamfering, you can choose either a regular turning tool or a chamfering tool. A chamfering tool can be used to chamfer the edges and hole entrances of a workpiece. A regular turning tool can only be used for chamfering in specific situations.
Lathe Cutting Tool Structures
The different structures of cutting tools can affect the process , and the following information can help you better understand this.
Integral Structure:
The integral structure has cutting edges made on the tool body, and the blades cannot be replaced. It offers high stability and rigidity, making it suitable for high-speed and high-precision machining.
Welded Structure:
The welded structure involves welding blades onto the tool body. It offers high rigidity, flexible welding shapes, and can adapt to special machining needs.
Mechanical Clamping Structure:
There are two types of mechanical clamping structures. One type secures the blade to the tool body, and the other secures the brazed blade head to the tool body. This type of tool structure allows for easy replacement and is suitable for mass production and different types of workpieces.
Lathe Cutting Tool Coatings
Choosing the right coating is important because it affects the cutting performance and processing quality of lathe cutting tools, which in turn determines the tool’s lifespan.
Titanium Nitride Coating (TiN):
TiN is a common coating that can enhance the hardness of cutting tools, suitable for high-speed steel tools or forming tools.
Chromium Nitride Coating (CrN):
CrN coating is suitable for high-speed steel tools, carbide tools, and forming tools due to its excellent anti-bonding properties.
Titanium Carbonitride Coating (TiCN):
TiCN coating is suitable for high-speed steel tools.
Titanium Aluminum Nitride Coating (TiAlN):
TiAlN coatings are suitable for dry or semi-dry cutting of carbide tools, and they have high-temperature resistance characteristics.
How many lathe cutting tools should I buy?
The number of lathe cutting tools depends on the following factors:
- Production Plan: The production plan sets the requirement for the number of tools.
- Machining Quantity: If there is a large quantity of machining, you need to prepare more cutting tools for replacement.
- Machining Types: For complex part operations, you need to prepare different types of lathe cutting tools for machining.
- Cutting Material: For workpieces with higher hardness, lathe cutting tools wear out quickly and have a shorter lifespan. To operate normally, you need to have an adequate number of tools.
- Operating Environment: Poor cutting lubrication conditions can easily damage the tools.
Considerations Before Purchasing
- Brand and Quality: High-quality tools reduce downtime during machining and also result in greater precision for the finished products. It’s important to choose a well-reputed tool brand that has safety certifications.
- Safety: The design of cutting tools should meet safety standards, ensuring stable operation during machining.
- Cost-effectiveness: Lathe cutting tools wear out easily, so consider both price and lifespan when choosing. A good brand may be more expensive but offers a longer lifespan, making it cost-effective.
- After-sales Service: When purchasing tools, consider whether the supplier offers warranty, maintenance, technical support, training, and customization services.
Conclusion
That’s all about choosing lathe cutting tools. If you want to learn more about lathes, you can contact us. Thank you for reading!