Milling processes are critical in the manufacturing and machining industries, offering precision and efficiency for creating parts and components. Two primary milling methods are face milling and end milling.
Face milling and end milling are fundamental machining processes in manufacturing. Face milling uses the cutter’s face to create flat surfaces and remove large material amounts, while end milling uses the cutter’s periphery for intricate profiles, slots, and contours.
Imagine you’re in the middle of a critical project, and you need a perfect surface finish on a large metal workpiece. Should you opt for face milling or end milling? Making the right choice can save time, reduce costs, and ensure product quality. This comprehensive guide dives deep into face milling vs. end milling distinctions, helping you make informed decisions for your next machining task.
Basics of Milling Processes
Milling is a machining process involving the removal of material from a workpiece using rotary cutters. Milling machines can perform various operations, including cutting, drilling, and slotting, on different materials such as metal, plastic, and wood.
Milling is a machining process that uses rotary cutters to remove material from a workpiece by advancing in a direction at an angle with the axis of the tool. It covers a wide variety of different operations and machines, on scales from small individual parts to large, heavy-duty gang milling operations.
Different Milling Techniques
Beyond face and end milling, techniques include slab milling, slot milling, contour milling, and plunge milling. Each has specific applications and advantages depending on the machining requirements.
What is Face Milling?
Face milling involves using a cutter with a cutting face at the end to machine flat surfaces perpendicular to the cutter’s axis. This method is highly efficient for removing large amounts of material quickly and creating a smooth, flat finish.
Face milling is primarily used to machine flat surfaces. The cutting action occurs primarily at the end corners of the milling cutter.
Characteristics of Face Milling:
Tool Design: Face milling cutters, often known as face mills, have a large diameter with multiple cutting edges arranged around the periphery. The cutting edges or inserts are positioned to engage the workpiece and remove material effectively.
Cutting Mechanism: The cutting action primarily takes place on the face of the cutter, with the cutting edges slicing through the material to create a flat surface. The rotational movement of the cutter ensures that each cutting edge engages the material sequentially.
Surface Finish: Face milling typically results in a smooth and even surface finish. The large diameter of the cutter allows for efficient material removal while maintaining surface quality.
Key Advantages and Disadvantages:
Advantages:
- High Material Removal Rate: Face milling is highly efficient at removing large amounts of material quickly, making it ideal for roughing operations and preparing workpieces for subsequent machining.
- Smooth Surface Finish: The cutting action and design of face mills result in a uniform and smooth surface finish, which is essential for achieving dimensional accuracy and reducing the need for additional finishing processes.
- Versatility: Face milling can be used on various materials, including metals, plastics, and composites. It is also suitable for different workpiece sizes and shapes, making it a versatile option for a wide range of applications.
Disadvantages:
- Limited to Flat Surfaces: Face milling is primarily designed for machining flat surfaces and may not be suitable for complex profiles or intricate features.
- Tool Wear: The high material removal rates can lead to increased tool wear, especially when machining hard materials. Frequent tool changes and maintenance may be required to maintain cutting efficiency.
- High Initial Tool Cost: Face milling cutters and inserts can be expensive, especially for high-performance tools with advanced coatings and materials.
When to Choose Face Milling:
Face milling is ideal for operations requiring the rapid removal of material from large, flat surfaces, such as preparing a workpiece for further machining or creating a uniform surface. It is also suitable for applications where a smooth and even surface finish is essential.
Key Steps in Face Milling:
- Tool Selection: Choose a face mill with an appropriate diameter and insert configuration based on the material and desired surface finish.
- Setup: Secure the workpiece and set the machine parameters, including cutting speed, feed rate, and depth of cut.
- Machining: Perform the face milling operation, ensuring even material removal by adjusting the feed rate and cutting depth as needed.
- Inspection: After machining, inspect the surface finish and dimensional accuracy to ensure that the desired specifications are met.
Main Applications of Face Milling:
- Flattening Large Surfaces: Face milling is commonly used to create flat surfaces on large workpieces, such as machine bases, frames, and structural components.
- Preparing Workpieces for Further Machining: Face milling is often used as a preliminary step to create a uniform surface before performing additional machining operations, such as drilling, tapping, or contour milling.
- Creating Smooth, Uniform Finishes on Metal Plates: Face milling is ideal for producing smooth and even surface finishes on metal plates, which are used in various industries, including automotive, aerospace, and construction.
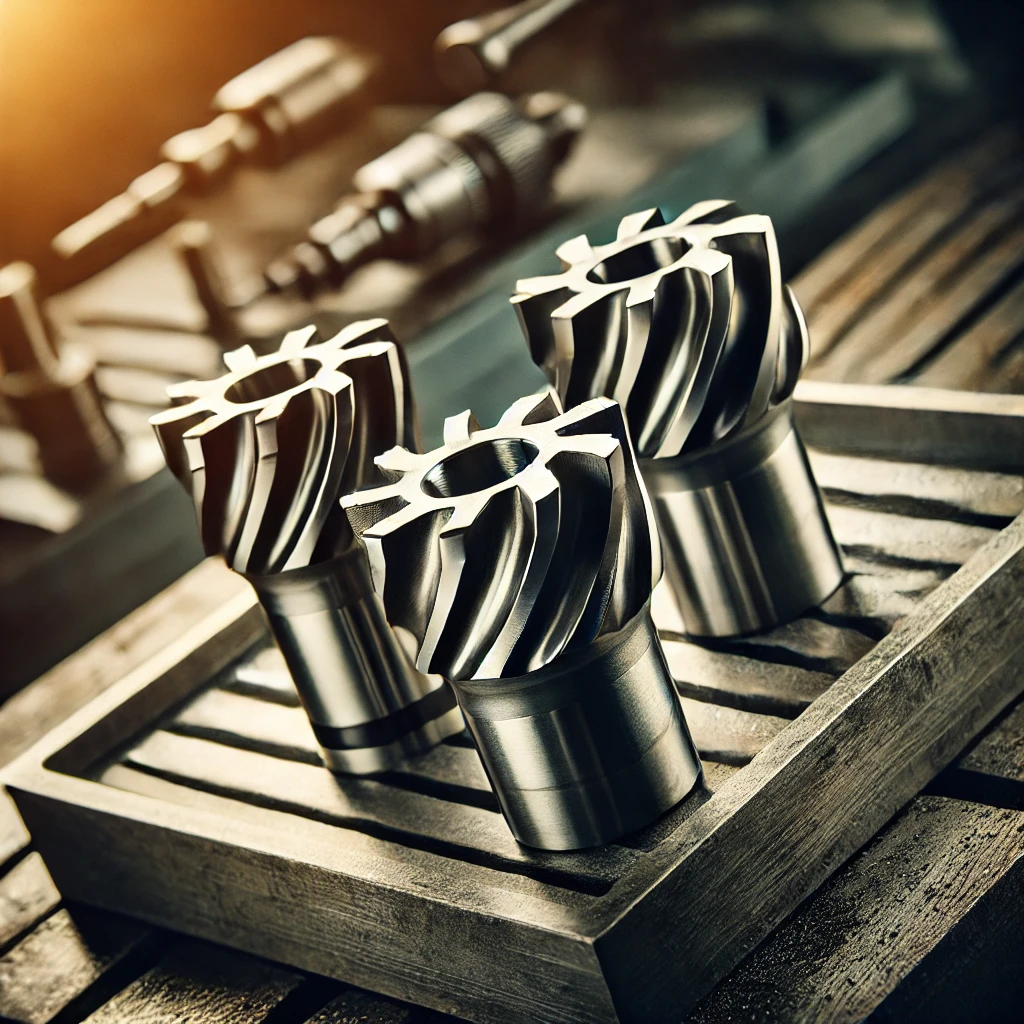
What is End Milling?
End milling is the use of a cutter with teeth on the periphery and face to machine intricate profiles, slots, and contours. It is a versatile method that can create various shapes and features on a workpiece.
End milling is used to machine vertical surfaces, horizontal surfaces, slots, pockets, and other intricate details. The cutting action occurs both at the end of the cutter and along the sides.
Characteristics of End Milling:
- Tool Design: End mills have cutting edges on the periphery and the end of the tool, allowing them to cut in multiple directions. They come in various shapes, including flat, ball nose, and corner radius, to accommodate different machining requirements.
- Cutting Mechanism: The cutting action occurs primarily at the end and along the sides of the end mill. The tool’s flutes (spiral grooves) help remove chips from the cutting area, ensuring efficient material removal and preventing tool clogging.
- Surface Finish: End milling can achieve high precision and fine surface finishes, making it suitable for both roughing and finishing operations. The choice of tool geometry, cutting parameters, and machining strategy can significantly impact the surface quality.
Key Advantages and Disadvantages:
Advantages:
- High Precision and Versatility: End milling is capable of machining complex shapes and features with high precision. It can create slots, pockets, contours, and intricate profiles, making it a versatile option for various applications.
- Suitable for Both Roughing and Finishing Operations: End mills can be used for initial roughing operations to remove large amounts of material and for finishing operations to achieve tight tolerances and fine surface finishes.
- Wide Range of Tool Geometries: End mills are available in various geometries, allowing machinists to select the optimal tool for specific applications. Options include flat end mills for general-purpose machining, ball nose end mills for curved surfaces, and corner radius end mills for improved tool strength.
Disadvantages:
- Slower Material Removal Rate Compared to Face Milling: End milling generally has a lower material removal rate compared to face milling, especially when machining large surfaces. Multiple passes may be required to achieve the desired depth and finish.
- Increased Tool Wear: Machining intricate features and profiles can lead to increased tool wear, particularly when using small-diameter end mills. Proper tool selection, cutting parameters, and coolant usage are essential to minimize wear and maintain tool performance.
- Potential for Chatter and Vibration: End milling operations, especially those involving long tool overhangs or deep cuts, can be prone to chatter and vibration. This can negatively impact surface finish and dimensional accuracy, requiring careful setup and machining strategies.
When to Choose End Milling:
End milling is ideal for operations requiring high precision and the creation of intricate features, such as slots, pockets, and contours on a workpiece. It is also suitable for applications where both roughing and finishing operations are needed.
Key Steps in End Milling:
- Tool Selection: Choose an end mill with the appropriate diameter, flute count, and material based on the workpiece material and desired features.
- Setup: Secure the workpiece and set the machine parameters, including cutting speed, feed rate, and depth of cut.
- Machining: Perform the end milling operation, making multiple passes if necessary to achieve the desired depth and finish.
- Inspection: Inspect the features and surface finish after machining to ensure they meet the desired specifications.
Main Applications of End Milling:
- Creating Slots and Pockets: Use end milling to machine slots and pockets in various workpieces, including keyways, grooves, and channels.
- Machining Intricate Profiles and Contours: End milling is ideal for creating complex shapes and features, including contours, curves, and intricate profiles on workpieces.
- Drilling and Finishing Operations: Use end mills for drilling operations like creating holes and counterbores, as well as for finishing operations to achieve tight tolerances and fine surface finishes.
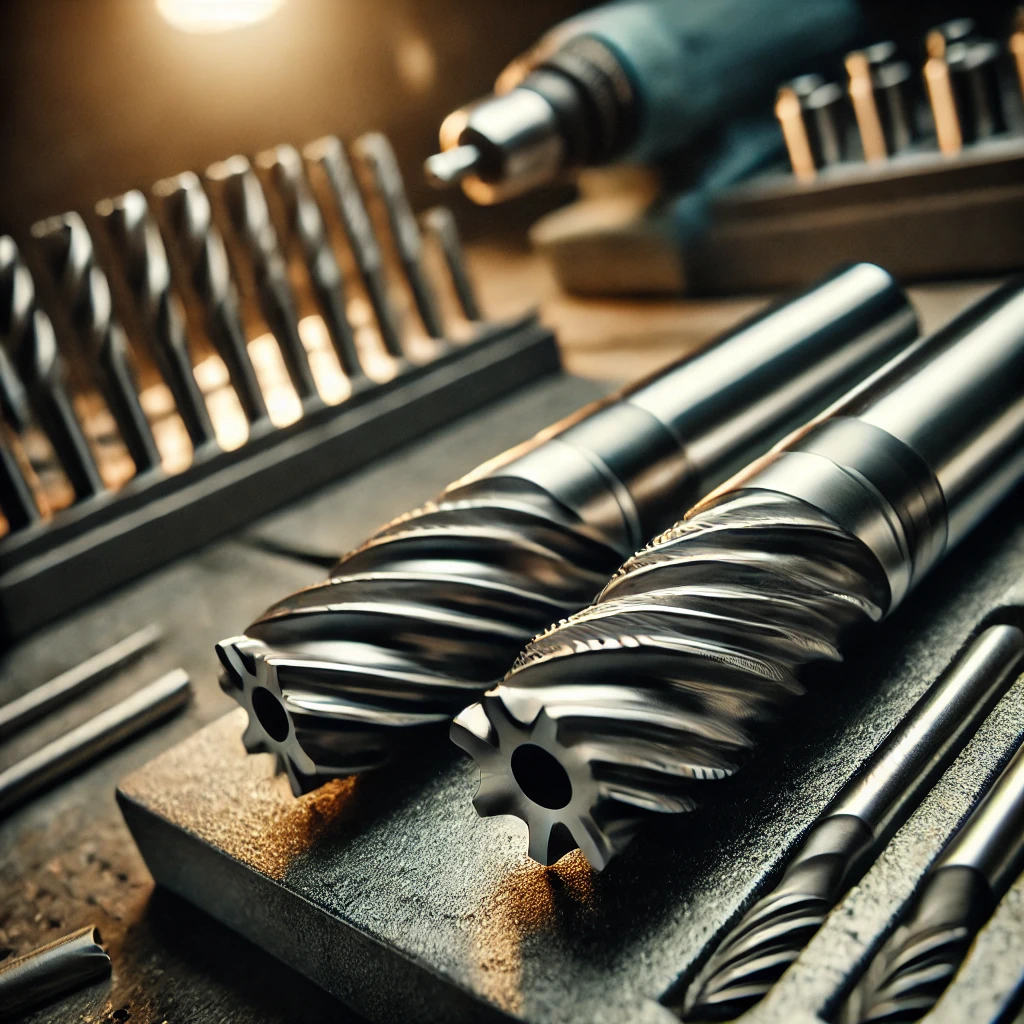
Detailed Comparison: Face Milling vs. End Milling
To get a better understanding of the differences between face milling and end milling, let’s take a closer look at a few factors, including tool design, cutting action, surface finish, material removal rate, applications, and overall efficiency. Below is a more detailed comparison of these factors:
1. Tool Design and Structure:
Face Milling Tools:
- Larger Diameter: Face mills are typically larger in diameter than end mills, ranging from a few inches to more than a foot in diameter. The larger diameter allows for higher material removal rates and better surface finishes.
- Multiple Cutting Inserts: Face mills have multiple cutting inserts that are usually made of carbide or other durable materials. These inserts can be indexed and replaced when they wear out, reducing downtime and maintaining cutting efficiency.
- Insert Configuration: The inserts are arranged around the circumference of the cutter, with each insert engaging the workpiece in sequence. The number and configuration of inserts can vary depending on the specific face mill design and application.
End Milling Tools:
- Smaller Diameter: End mills are available in smaller diameters than face mills, ranging from less than an inch to a few inches in diameter. The smaller diameter allows for greater precision and versatility in machining intricate features.
- Various Shapes: End mills come in various shapes, including flat end mills (square end), ball nose end mills, corner radius end mills, and specialty end mills (e.g., chamfer, roughing, and T-slot cutters). Each shape is designed for specific applications and machining requirements.
- Flute Count and Helix Angle: End mills have cutting flutes (spiral grooves) that help remove chips from the cutting zone. The number of flutes and the helix angle can vary, with common configurations including two, three, four, and more flutes. The choice of flute count and helix angle depends on the material, cutting conditions, and desired surface finish.
Cutting Action:
Face Milling:
- Cutting Action: The primary cutting action occurs on the face of the cutter, with the cutting edges slicing through the material to create a flat surface. The rotation of the cutter ensures that each cutting edge engages the material in sequence.
- Radial and Axial Forces: Face milling generates both radial and axial cutting forces. Radial forces act perpendicular to the cutter’s axis, while axial forces act parallel to the axis. Proper management of these forces is critical to prevent tool deflection and achieve a smooth surface finish.
End Milling:
- Cutting Action: The primary cutting action occurs at the end and along the sides of the end mill. The flutes of the tool help remove chips from the cutting zone, ensuring efficient material removal and preventing the tool from clogging.
- Radial Forces: End milling primarily generates radial cutting forces, which act perpendicular to the cutter’s axis. Proper management of these forces is critical to maintain tool stability and achieve accurate machining results.
Surface Finish and Precision:
Face Milling:
- Smooth, Flat Surface: Face milling is designed to produce a smooth, flat surface finish, making it ideal for applications that require high surface quality and dimensional accuracy. The large diameter of the face mill allows for efficient material removal while maintaining surface quality.
- Insert Type and Cutting Parameters: The surface finish achieved in face milling depends on the type of inserts used (e.g., geometry, material, coating) and the cutting parameters (e.g., cutting speed, feed rate, depth of cut). Optimizing these factors is critical to achieve the desired surface finish.
End Milling:
- High Precision and Fine Surface Finishes: End milling is capable of achieving high precision and fine surface finishes, making it suitable for both roughing and finishing operations. The choice of tool geometry, cutting parameters, and machining strategy can significantly impact the surface quality.
- Tool Geometry and Feed Rates: The surface finish achieved in end milling depends on the tool geometry (e.g., flute count, helix angle, corner radius) and the feed rates. Optimizing these factors is critical to achieve the desired surface finish and dimensional accuracy.
Material Removal Rate:
Face Milling:
- High Material Removal Rate: Face milling is highly efficient at removing large amounts of material quickly, making it ideal for roughing operations and preparing workpieces for subsequent machining. The large diameter of the face mill and the multiple cutting inserts contribute to the high material removal rate.
- Ideal for Large Surfaces: Face milling is particularly effective for machining large surfaces, making it ideal for rapidly removing material and achieving smooth surface finishes on machine bases, frames, and structural components.
End Milling:
- Lower Material Removal Rate: End milling generally has a lower material removal rate compared to face milling, especially when machining large surfaces. Multiple passes may be required to achieve the desired depth and finish.
- Suitable for Finishing and Detailed Work: End milling is suitable for both roughing and finishing operations, particularly when machining intricate features and profiles. The choice of tool geometry and cutting parameters can significantly impact the material removal rate and surface quality.
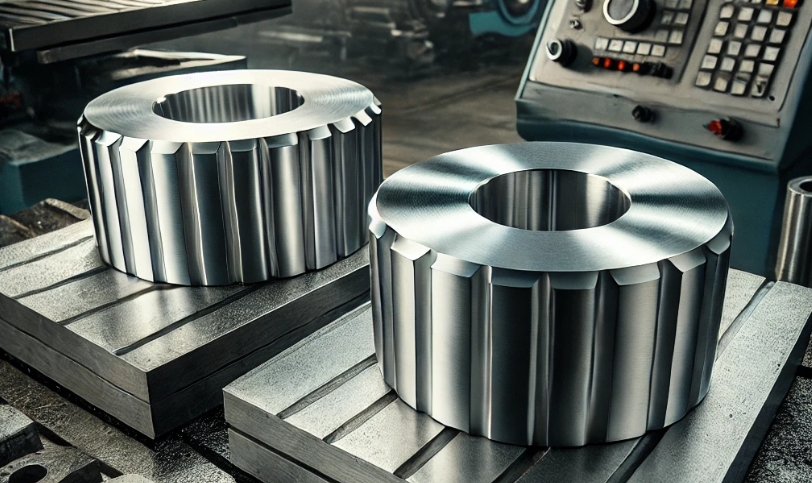
When to Use Face Milling vs. End Milling
- Face Milling:
Use face milling for large, flat surfaces, such as machine bases, frames, and structural components. The high material removal rate and smooth surface finish make it ideal for preparing workpieces for subsequent machining operations.
- End Milling:
Use end milling for machining intricate profiles and features, such as contours, curves, and intricate profiles. The high precision and versatility of end mills make them suitable for a wide range of applications.
Face Milling vs. End Milling Efficiency
Face milling is generally more efficient at removing large amounts of material quickly, while end milling is more precise and versatile for detailed work.
Face Milling vs. End Milling Workpieces
- Face Milling:
Face milling is best suited for machining large, flat surfaces where rapid material removal and smooth surface finishes are required. It is not suitable for machining intricate features or complex profiles.
- End Milling:
End milling is ideal for workpieces requiring intricate features, such as slots, pockets, and contours. We use face milling to machine workpieces of various shapes and sizes.
Face Milling vs. End Milling Cost
- Face Milling:
Face milling cutters and inserts can be more expensive compared to end mills, but the high material removal rate and efficiency of face milling contribute to lower operational costs.
- End Milling:
End mills are generally less expensive compared to face mills, but the cost can increase for specialty end mills and high-performance tools.
Face Milling vs. End Milling Precision
End milling typically provides higher precision and better surface finish for intricate features, while face milling is excellent for achieving smooth, flat surfaces quickly.
Face Milling vs. End Milling Materials
- Face Milling:
Face milling is suitable for a wide range of materials, including metals, plastics, and composites. It can handle tougher materials, such as hardened steels and superalloys, with the use of appropriate cutting inserts and advanced coatings.
- End Milling:
End milling is versatile for machining various materials, including metals, plastics, and composites. The performance of end mills depends on the tool material and coating.
Face Milling vs. End Milling Tool Life
- Face Milling:
Face milling cutters typically offer a longer tool life because of their larger size and multiple cutting inserts. They excel in heavy-duty operations, effectively roughing large surfaces and quickly removing large amounts of material.
- End Milling:
End mills may have a shorter tool life in heavy-duty applications, particularly when machining hard materials or intricate features. Frequent tool changes may be required for detailed work.
Criteria for Choosing the Right Tool
To choose the right tool for your specific materials, you need to consider the tool’s geometry, the material you’re cutting, the coating on the tool, and the capabilities of your machine. You also need to balance tool life and cost to make sure you’re milling efficiently.
1. Choose the Right Tool for Your Specific Materials
Different materials require different tool properties. For example, you might need carbide inserts for hard metals, while you can use high-speed steel tools for softer materials.
2. Consider Tool Life and Cost
While high-quality tools might cost more, they last longer and perform better, which can reduce your overall costs.
3. Consider the Capabilities of Your Machine
Make sure the tool you choose works with the speed, feed rate, and power capabilities of your machine.
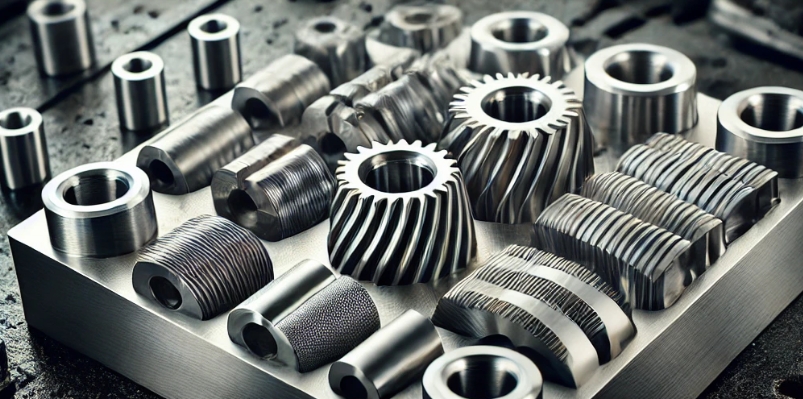
Technical Parameters and Setup
1. Optimize Speeds and Feeds
Choosing the right cutting speeds and feed rates is critical to maximizing tool life and getting the surface finish you want.
2. Consider Setup and Alignment
Properly setting up and aligning your workpiece and tool will help you get the accuracy you need and minimize tool wear.
3. Think About Tool Holding and Rigidity
Holding your tool securely and having a rigid machine are critical to maintaining accuracy and preventing your tool from deflecting.
Practical Tips for Milling Success
Face Milling Best Practices:
Use the right insert type and configuration.
Optimize your cutting parameters for your material and tool.
Keep your feed rate consistent.
End Milling Best Practices:
Choose the right tool geometry for your application.
Use the right cutting speeds and feed rates.
Make multiple passes for deep cuts or intricate features.
Common Mistakes to Avoid:
Using the wrong tool for your application.
Setting up and aligning your workpiece incorrectly.
Ignoring tool wear and not doing regular maintenance.
Case Studies and Examples
Face Milling Applications:
Case Study 1: A manufacturer uses face milling to prep large metal plates for further machining. They can remove a lot of material quickly and get a smooth surface.
Case Study 2: An automotive parts manufacturer uses face milling to get consistent surfaces on engine blocks, which makes assembly easier.
End Milling Applications:
Case Study 1: A CNC shop uses end milling to make intricate parts for aerospace components. They need to be precise and high quality.
Case Study 2: A medical device manufacturer uses end milling to create detailed features on surgical instruments. They need to be very precise and have a smooth finish.
Compare the Results:
Face Milling vs. End Milling: When you compare them side by side, face milling is more efficient for removing a lot of material from a large surface, while end milling is better for creating detailed features with high precision.
Future Trends in Milling Technology
- Advances in Milling Tool Design: New tool materials, coatings, and geometries make milling perform better and last longer. For example, polycrystalline diamond (PCD) tools have made a big difference in how well you can machine non-ferrous materials.
- The Impact of Automation and AI on Milling: Automation and AI make milling more efficient, more precise, and less expensive. Smart CNC machines can automatically adjust their parameters in real time to make sure they’re performing their best and their tools last as long as possible.
- Sustainability and Environmental Considerations: Being green and using green tools is important. For example, using biodegradable cutting fluids and recycling your metal chips.
FAQs
Which milling process provides a better surface finish?
End milling typically provides a better surface finish for intricate features, while face milling excels in creating smooth, flat surfaces quickly.
How do I choose the right milling process for my application?
Consider the type of surface, material removal rate, precision requirements, and tool cost to choose between face milling and end milling.
What are the latest advancements in milling tools?
Advancements include improved tool materials, coatings, geometries, and integration of automation and AI technologies.
What is the difference between end milling and slab milling?
End milling involves cutting with the periphery and face of the cutter, while slab milling uses the cutter’s peripheral teeth to remove material from large, flat surfaces.
What is the difference between end milling and plain milling?
End milling can create intricate profiles and features, while plain milling typically involves machining flat surfaces with a cutter’s peripheral teeth.
What is the difference between an end mill and a milling machine?
An end mill is a type of milling cutter used in milling machines, which are tools for machining processes involving rotary cutters to remove material.
What is the difference between a face mill and a shell mill?
A face mill uses the face of the cutter to machine surfaces, while a shell mill is a type of face mill mounted on an arbor, used for heavier cutting operations.