In recent years, global manufacturing has been undergoing a revolution driven by artificial intelligence, the Internet of Things, and automation technologies. Whether it’s the construction of smart factories or the widespread application of the “Industry 4.0” concept, both are pushing companies to transition to more efficient and precise production methods. In this transformation process, choosing the right machining technology, especially vertical and horizontal machining, has become an important decision for manufacturers. This choice not only impacts production efficiency but also directly affects product quality and cost control. Therefore, understanding and mastering the characteristics of these two machining methods has become a key factor for companies to stand out in a highly competitive market.
Vertical and horizontal machining differ significantly in terms of machine structure, machining methods, and areas of application. Vertical machining, with its compact design and operational flexibility, is widely used for precision machining, especially for small and medium-sized workpieces requiring high accuracy. On the other hand, horizontal machining shows greater advantages when working with large, heavy workpieces. Its powerful cutting ability and high stability allow it to handle complex multi-surface machining tasks effectively.
In the following sections, we will analyze how to choose the most suitable machining method based on different production needs, helping you make more targeted decisions when selecting equipment.
What is Vertical Machining?
Vertical machining is a cutting method mainly used for vertical direction machining. It relies on vertical machine tools to perform operations such as hole processing, surface cutting, and complex surface machining. Due to its compact structure and flexible operation, it is widely used in the manufacturing industry.
- Basic Structure of Vertical Machining
- Vertical Spindle: The spindle is arranged vertically and is responsible for tool installation and rotation. It operates with high speed and precision.
- Worktable: The table fixes the workpiece, allowing it to move along the X and Y axes, while the spindle controls the Z-axis movement, enabling multi-directional machining.
- Feed System: The feed system adjusts the position of the tool and workpiece either manually or via CNC control, ensuring smooth and precise cutting.
- Working Method and Application Scenarios
- Working Method: The spindle rotates to cut the workpiece surface, and different tools are used for operations such as drilling, milling, and tapping.
- Application Scenarios: Vertical machining is suitable for high-precision processing of small or medium-sized workpieces. It is often used for precision hole processing, surface milling, and complex mold surface machining.
Advantages and Disadvantages of Vertical Machining
Vertical machining has several advantages, including ease of operation, high efficiency, and strong flexibility. It is ideal for precision hole machining and end face milling, especially in small workshops. Due to its small footprint, it is well-suited for multi-variety, small-batch production. Vertical machining supports quick tool changes and multi-process operations, making it capable of machining complex-shaped workpieces. However, vertical machining also has some limitations. It is not suitable for large or heavy workpieces, and when performing deep hole machining, the tool length limits the machining depth. Additionally, vertical machine tools generally have lower stability and rigidity, which can affect machining accuracy, particularly when processing large or high-precision workpieces. As a result, machining efficiency and adaptability are also lower in these cases.
What is Horizontal Machining?
Horizontal machining is a machining method centered around horizontal milling machines, primarily used for workpieces that require horizontal cutting. The design is typically suited for processing larger or heavier workpieces, with significant advantages in complex multi-surface milling.
Basic Structure of a Horizontal Milling Machine
- Horizontal Spindle: The spindle is arranged horizontally, ensuring smooth and stable high-torque cutting during operation.
- Worktable: The worktable supports the workpiece and allows movement in multiple directions. It is commonly used for processing four or more surfaces.
- Tool Holding System: This system fixes and changes tools, often using automatic tool changers that support various tool types.
Working Method and Application Scenarios
- Working Method: The horizontal spindle rotates the tool to mill the workpiece surface, making it suitable for complex multi-surface machining.
- Application Scenarios: Horizontal machining is widely used in industries such as automotive, aerospace, and energy. It is particularly suitable for processing heavy, large workpieces or components requiring high stability.
Advantages and Disadvantages of Horizontal Machining
Advantages
- Machining Large Workpieces: The horizontal design provides greater stability during machining, making it ideal for precise processing of complex, multi-surface parts.
- Improved Machining Accuracy: Multiple surfaces can be processed with a single setup, reducing positioning errors and improving accuracy.
- Powerful Cutting Capacity: The horizontal spindle delivers greater cutting torque, making it suitable for heavy cutting tasks.
- Efficient Chip Removal: The horizontal structure facilitates quick chip removal, keeping the machining area clean and reducing tool wear.
Disadvantages
- Larger Footprint: Compared to vertical machines, horizontal machines are larger and take up more space in the workshop.
- Higher Operational Complexity: The arrangement of the worktable and spindle makes operation and setup more complex, especially when dealing with intricate workpieces.
- Higher Cost: Horizontal machines tend to be more expensive, especially those with high precision.
Differences Between Horizontal and Vertical Machining
Comparison Item | Horizontal Machining | Vertical Machining |
Structural Difference | The spindle is horizontally arranged, suitable for large workpieces | The spindle is vertically arranged, suitable for small workpieces |
Machining Adaptability | Suitable for large, heavy workpieces | Suitable for small, precision workpieces |
Machining Efficiency | Strong cutting force, ideal for heavy cutting | Quick tool change, suitable for multi-variety production |
Operation and Maintenance | Complex operation, requires high skill | Simple operation, easy maintenance |
How to Choose the Right Horizontal or Vertical Machining
Workpiece Size and Weight
- Vertical Machining: Vertical machine tools are suitable for small and medium-sized workpieces, especially for precision parts. They offer clear advantages in precision control and stability, making them ideal for parts with a size under 500mm. In precision part production, vertical machines can achieve positioning accuracy of ±0.005mm and complete complex multi-station operations in a smaller space.
- Horizontal Machining: Horizontal machine tools are suitable for large, heavy workpieces. They can handle workpieces weighing up to 3000kg, which vertical machines typically cannot. Horizontal machines also have strong load-bearing capacity, making them especially suitable for large workpieces in industries such as aerospace and heavy machinery. For instance, the MINNUO MDH series horizontal machining center uses a high-rigidity structure, providing excellent stability and maintaining positioning accuracy of ±0.008mm even under high loads.
Machining Precision and Depth Requirements
- Vertical Machining: Horizontal machines excel at high-precision machining, especially when working with materials like steel and castings, as they reduce errors during machining and improve product consistency.
- Horizontal Machining: Horizontal machining excels in deep hole machining and meets high-precision requirements. Studies show that horizontal machines with hollow oil-cooled ball screw technology (such as MINNUO’s MDH series machines) effectively reduce thermal deformation, thus maintaining higher accuracy. Horizontal machines excel at high-precision machining, especially when working with materials like steel and castings, as they reduce errors during machining and improve product consistency.
Production Efficiency
- Vertical Machining: The quick tool change system and high cutting efficiency make vertical machines ideal for diverse production needs. Vertical machines can change tools in less than 2.5 seconds, which is crucial for production lines with frequent process changes.
- Horizontal Machining: Horizontal machines, with stronger cutting capabilities and higher stability, can achieve high-speed cutting for large-scale production. The MINNUO MDU series horizontal machining center reaches cutting speeds of up to 20m/min, enabling complex multi-surface machining in a short time. This significantly improves production efficiency, particularly in the production of automotive and aerospace parts.
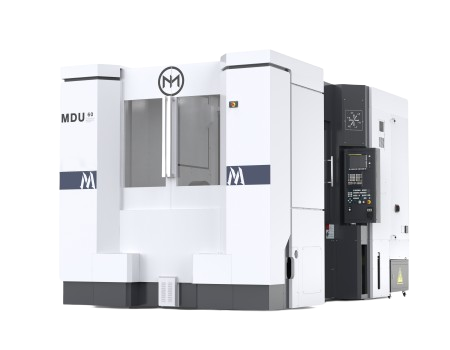
Work Environment and Space
- Vertical Machining: Vertical machines have a compact design, making them suitable for small workshops or environments requiring high flexibility. In space-constrained situations, vertical machines ensure both machining accuracy and high production efficiency in limited spaces.
- Horizontal Machining: Due to the larger size of horizontal machines, they are better suited for larger workshops, particularly in environments where higher stability and load-bearing capacity are needed.
Cost and Maintenance
- Vertical Machining: Vertical machines have lower initial investment costs and, due to their simple maintenance and ease of operation, also have lower long-term maintenance costs.
- Horizontal Machining: Horizontal machines require a higher initial investment but have lower overall long-term costs. Their stability and rigidity mean they require less maintenance during prolonged high-load operations, leading to longer service life and lower maintenance needs over time.
Conclusion
Choosing the right machining method is key to improving production efficiency and product quality. Both vertical and horizontal machining have their own strengths, and understanding their characteristics will help you make a more informed decision. If you have any questions about selecting the right equipment for your needs, feel free to contact us. We will provide professional advice and solutions to help guide your production decisions.