As the manufacturing industry continues to develop, CNC machine tools play an increasingly important role in processing efficiency and precision. Four-axis machines are flexible and efficient processing equipment that includes various types, such as tip four-axis, disc four-axis, cradle four-axis, and tailstock tip four-axis.
Choosing the right four-axis machine (tip, disc, cradle, and tailstock tip) is crucial for improving production efficiency and processing precision. Key factors to consider include processing needs (type and precision of workpieces), production efficiency (batch size and diversity), cost budget (equipment and maintenance costs), technical support (supplier services), and space requirements. Understanding the characteristics and application areas of each machine, as well as focusing on future trends like automation and intelligence, helps companies make informed choices to meet specific processing needs.
Understanding the basic concept of four-axis machines:
Before choosing a four-axis machine, it is important to understand its basic concept. A four-axis machine refers to a machine that can process on four independent axes. Common motion axes include the X, Y, Z, and one rotating axis (such as the A axis). This allows the machine to perform cutting operations in multiple directions, enhancing processing flexibility.
Characteristics of Different Types of Four-Axis Machines:
Tip Four-Axis:
- Structural Characteristics: The tip four-axis machine holds the workpiece with a tip and primarily relies on the linear movements of the X, Y, and Z axes and the rotational movement of the A axis for processing.
- Application Areas: It is suitable for processing long shaft-type parts and is widely used in machinery, aviation, and automotive industries.
- Advantages and Disadvantages:
- Advantages: It offers high stability, high processing precision, and is suitable for multi-surface machining.
- Disadvantages: Its application range is limited and mainly suited for specific types of workpieces.
Disc Four-Axis:
- Structural Characteristics: The disc four-axis machine fixes the workpiece using a rotating disc and combines this with linear movement for processing.
- Application Areas: It is suitable for processing gears, discs, and similar parts, especially performing well in mass production.
- Advantages and Disadvantages:
- Advantages: It offers high efficiency, enables multi-surface machining, and reduces the need for fixture changes.
- Disadvantages: The equipment has a high cost and involves complex maintenance.
Cradle Four-Axis:
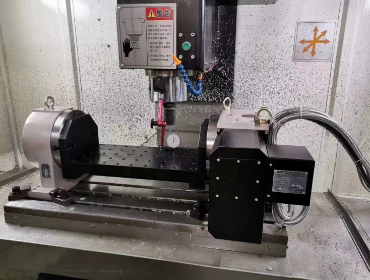
- Structural Characteristics: The cradle four-axis machine uses a cradle structure that allows the workpiece to move flexibly across multiple axes.
- Application Areas: It is widely used for processing complex-shaped parts, such as aerospace components and molds.
- Advantages and Disadvantages:
- Advantages: It offers high flexibility and adaptability, capable of machining various shapes.
- Disadvantages: It has complex technology and high requirements for maintenance and operation.
Tailstock Four-Axis:
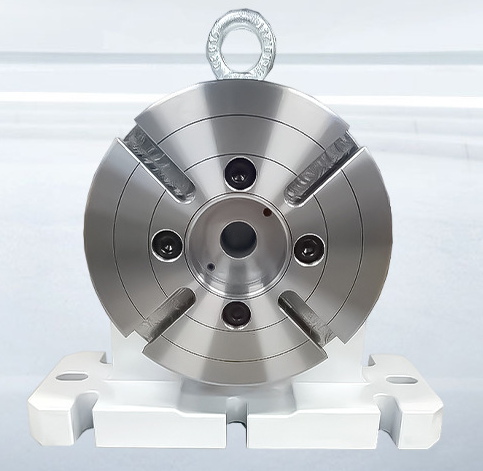
- Structural Characteristics: Equipped with a tailstock, it provides additional support to ensure the stability of long workpieces.
- Application Areas: It is suitable for processing long rod and pipe parts, commonly found in the machinery and energy industries.
- Advantages and Disadvantages:
- Advantages: It improves machining precision and is suitable for long workpiece processing.
- Disadvantages: It occupies a large space and has relatively high equipment costs.
Key Factors for Choosing a Four-Axis Machine Tool:
When choosing a four-axis machine tool, the following factors are crucial:
Processing Requirements:
- Workpiece Type: First, consider the type of workpiece to be processed, including shape, size, and material. For example, long shaft parts suit a tailstock four-axis, while disk-shaped parts suit a disc four-axis.
- Processing Precision: Different types of machines have varying processing precision. Choose the appropriate machine based on production requirements.
Production Efficiency
- Mass Production: If the production volume is large, it is advisable to choose a disk four-axis machine. Its ability to perform multi-surface processing and high efficiency will greatly enhance production efficiency.
- Diverse Needs: If you need to process various shapes of parts, the flexibility of the cradle four-axis machine will be an important advantage.
Cost Budget:
- Equipment Cost: Different types of machine tools have varying costs. You should consider the company’s budget when making a choice.
- Maintenance Cost: Consider the costs of maintenance and upkeep. Choosing machines that are easy to maintain and cost-effective will benefit long-term operations.
Technical Support and Training
- Technical Support: When choosing a supplier, consider the quality of their technical support and services.
- Operator Training: Different types of machines have varying technical requirements for operators. Ensure operators receive appropriate training.
Space Requirements
- Equipment Space: Different machines require different amounts of space. You need to choose a suitable machine based on the factory layout.
- Working Environment: Consider the machine’s working environment requirements, such as ventilation and temperature.
Applicable Scenarios for Different Types of Four-Axis Machining Centers
To better understand how to choose different types of four-axis machining centers, here are examples of applicable scenarios for each type of machine:
- Taper Four-Axis: Suitable for machining aerospace parts, especially long rod and shaft products.
- Disk Four-Axis: Ideal for manufacturing gears and disk components in large-scale production.
- Cradle Four-Axis: Used for machining complex-shaped parts, such as aerospace engine components and molds.
- Tailstock Taper Four-Axis: Suitable for machining long tubular parts, meeting the needs of the energy industry’s long workpieces.
Future Development Trends:
With technological advancements, the selection and application of four-axis machines continue to evolve. Future trends may include:
- Intelligent systems: More machines will integrate smart control systems to enhance adaptive capabilities and intelligence.
- Automation: The spread of automated production lines will promote the integration of four-axis machines with robots and other automation equipment.
- Material compatibility: The emergence of new materials will drive the application of four-axis machines in more fields.
Conclusion:
Choosing the right four-axis machine is key to improving production efficiency and machining accuracy. The tip four-axis, disk four-axis, cradle four-axis, and tailstock four-axis each have unique features suitable for different processing needs. When making a choice, you should consider factors like workpiece type, production efficiency, cost budget, technical support, and space requirements. By selecting the right machine, businesses can better cope with market competition and achieve sustainable development. If you want to find the most suitable four-axis machine, feel free to visit us. You can provide your drawings, and we will customize the best solution for you and offer professional consultation.