In the wave of the automation era, “speed, precision, and savings” have almost become the mantra of manufacturing. Companies are pushing to produce higher-quality products with fewer resources and in less time. Laser cutting equipment has become the “secret weapon” in achieving this. Whether for automotive manufacturing or high-end electronics, having an efficient laser cutter has become standard for modern factories. Choosing the right laser can act as an accelerator for your production line; choosing the wrong one, however, could trap your business in inefficiency.
Today, global manufacturing focuses not only on efficiency but also on tackling supply chain pressures and meeting energy-saving, eco-friendly goals. With three popular laser options—fiber lasers, CO₂ lasers, and disk lasers—it’s normal to feel uncertain: “Which one should I choose?” Is it better to go for low power consumption or higher cutting precision? Don’t worry, you’re not alone in this. Many companies wrestle with this decision, knowing it impacts product quality, operating costs, and future competitiveness.
Next, we’ll break down the advantages and best applications for each of these lasers, helping you avoid potential pitfalls and find the laser that truly meets your needs. Whether you’re aiming to boost production speed, reduce energy usage, or tackle new precision processing challenges, here you’ll find practical solutions to help you make an informed choice.
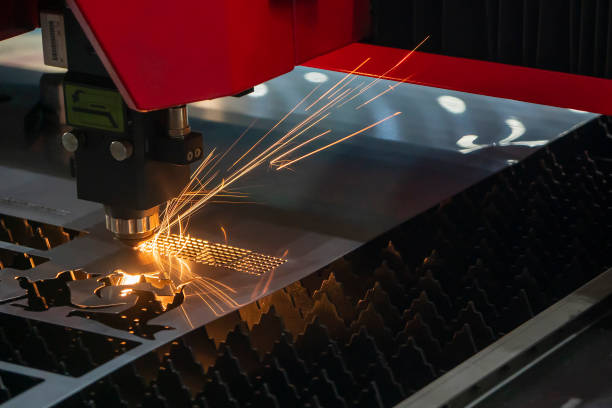
What Material Are You Cutting? — Defining Material Requirements
The first step in choosing a laser cutting equipment is to clarify the type of material you will primarily work with. Different lasers perform very differently when cutting metals versus non-metals, which can impact not only cutting efficiency but also the final quality and cost.
Metal Materials (e.g., Carbon Steel, Stainless Steel, Aluminum Alloys):
Fiber lasers are often the best choice for metal cutting. Their short wavelength (around 1.06 microns) absorbs well into metals, making them effective for cutting thin to medium-thickness metals. Plus, fiber lasers have high energy conversion efficiency, which helps reduce energy consumption during extended cutting.
If your main focus is on thin metal sheets (≤20 mm), fiber lasers can offer both high-speed cuts and precise edges, ideal for large-scale production. They handle materials like stainless steel and carbon steel excellently. However, for reflective metals like copper or brass, fiber lasers may require specific adjustments to optimize performance.
Non-Metal Materials (e.g., Wood, Plastic, Acrylic):
CO₂ lasers work best for these materials. With their longer wavelength (10.6 microns), CO₂ lasers excel at cutting non-metals, producing smooth edges ideal for applications in advertising, furniture, and other fields requiring large-area cuts in non-metals. For businesses needing to cut various non-metal materials, the versatility of CO₂ lasers allows for maximum return on investment.
Precision Metal Cutting or Complex Shapes:
For high-precision metal components, disk lasers are the top choice. Disk lasers maintain stability and precision even at high power levels, making them ideal for industries like aerospace and automotive, where precision is critical. Disk lasers can handle complex shapes and high-quality cuts on thick metals, making them a reliable option for intricate work.
What Are Your Production Capacity and Budget Requirements? — Balancing Equipment Costs and Production Efficiency
The next key factor is understanding your budget and production capacity needs. Initial investment, operating costs, and production efficiency directly impact the long-term return on laser equipment. Let’s dive into the investment costs and long-term operating expenses of the three main laser types.
- Fiber Lasers: For metal cutting, fiber lasers offer the highest electro-optical conversion efficiency (about 30%-35%), meaning lower energy consumption and reduced operating costs. If your production line needs to run continuously, fiber lasers’ low energy use can save substantial costs over time. Additionally, fiber lasers rarely require optical component replacements, keeping maintenance costs low. However, initial investment can be high, so fiber lasers are ideal for businesses with high production needs and long-term plans.
- CO₂ Lasers: CO₂ lasers come with a lower initial equipment cost, yet their electro-optical efficiency remains relatively low (typically 10%-15%). They require substantial power and cooling support, leading to higher long-term operating expenses. While capable of cutting metals, CO₂ lasers generally fall short of fiber lasers in both speed and quality when cutting thicker metals. For businesses focused on non-metal cutting and limited by an initial budget, CO₂ lasers are a practical choice, but consider the higher energy costs over time.
- Disk Lasers: Disk lasers strike a balance between fiber and CO₂ lasers in performance and application, offering an electro-optical efficiency close to that of fiber lasers while maintaining precision at high power outputs. With a more complex design, disk lasers tend to have higher initial costs, suiting businesses with a strong budget and high precision requirements. For industries like aerospace or medical equipment, where precision part processing is essential, disk lasers deliver exceptional performance and reliability.
What Are Your Precision and Production Stability Requirements? — Selecting Based on Workpiece Complexity and Process Needs
The cutting precision and operational stability of a laser cutting equipment are key factors affecting product quality, especially when processing complex-shaped or high-precision parts. Stability plays a vital role in maintaining consistent product quality and reducing waste.
- Fiber Lasers: In metal cutting, fiber lasers deliver smooth, precise edges, making them ideal for industries with strict dimensional requirements, like automotive parts and sheet metal fabrication. Fiber lasers perform excellently in large-scale, long-term production, with high stability and conversion efficiency that allow almost continuous operation in high-volume metal processing.
- CO₂ Lasers: While CO₂ lasers excel in non-metal cutting, they can struggle with stability when cutting thicker metals, particularly in applications requiring high precision. If your primary focus is large-format non-metal cutting, CO₂ lasers remain a dependable option, though it’s essential to consider their cutting speed and edge smoothness.
- Disk Lasers: For applications requiring extremely high precision—such as complex geometries or intricate metal components—disk lasers offer unmatched cutting accuracy. This precision proves especially beneficial in high-end manufacturing fields like aerospace and medical devices. Disk lasers ensure consistent quality with their high power and stable operation, even over extended periods, maintaining reliability and cutting consistency across demanding projects.
How to Consider Equipment Maintenance and Lifespan? — Ensuring Long-Term Reliability
When selecting a laser cutter, consider not only cutting capability and initial investment but also maintenance costs, equipment lifespan, and after-sales support.
- Fiber Lasers: With few vulnerable optical components, fiber lasers offer low maintenance costs. Their fiber transmission technology remains stable, providing a long lifespan. For companies aiming to minimize downtime and reduce maintenance interruptions, fiber lasers create a stable and efficient operating environment over the long term.
- CO₂ Lasers: Although CO₂ lasers come with a lower initial investment, their optical systems are sensitive to dust and other contaminants. Regular lens and mirror replacements can drive up maintenance expenses. Additionally, CO₂ lasers typically require extensive cooling support, which further increases operational and maintenance costs.
- Disk Lasers: Disk lasers, with their compact design and excellent heat dissipation, tend to have a longer lifespan. While initial costs are higher, disk lasers need minimal maintenance, making them ideal for industries requiring high precision over extended use.
Conclusion: How to Make the Final Decision?
Based on the analysis of key factors above, you can select the laser cutter that best suits your needs by considering the following:
- Material Requirements: For primarily metal cutting, fiber lasers offer the best choice. For non-metal cutting, CO₂ lasers excel. For high-precision metal cutting, disk lasers provide optimal performance.
- Budget and Production Capacity: For businesses focusing on long-term operation with low running costs, fiber lasers are ideal. For companies with a limited initial budget but high non-metal requirements, CO₂ lasers are a good match. For enterprises with a high budget and strict precision needs, disk lasers will meet your demands.
- Precision and Stability: Disk lasers are the top choice for high-precision, complex part processing, while companies engaged in large-scale metal production should prioritize fiber lasers.
By understanding the characteristics of fiber lasers, CO₂ lasers, and disk lasers, you now have a clearer picture of how to choose the best laser cutting equipment for your needs. Whether your aim is to improve cutting efficiency, handle diverse materials, or achieve high-precision processing, the right equipment choice will bring significant efficiency and cost advantages.