Milling cutters are essential tools in modern manufacturing, playing a crucial role in metalworking, woodworking, and other fields. Choosing the right milling cutter is vital for improving processing efficiency and enhancing product quality. We will explore the types of milling cutters, selection criteria, and application tips to help you make informed decisions during milling operations.
When choosing the right milling cutter, consider several factors. First, identify the type of material being processed, such as soft or hard metals, to select the appropriate cutter. Next, take into account the cutting depth and feed rate to choose a cutter with the right diameter. The geometry and coating of the tool also affect cutting performance, so pay attention to these aspects when selecting. Regularly check the wear of the cutter to ensure processing quality and efficiency. Considering these factors will help you make an informed choice of milling cutter.
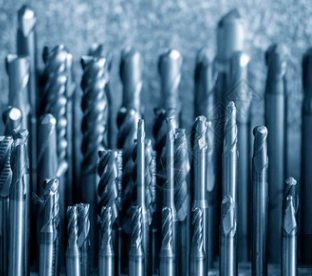
Basic Concept of Milling Cutters
A milling cutter is a cutting tool used for milling operations. It typically removes material from a workpiece to form the desired shape and size. The milling cutter makes contact with the workpiece through rotational motion, using the relative movement of the cutting edges for machining. Milling cutters can work on various materials, including metals, plastics, and wood.
Components of Milling Cutters
A milling cutter mainly consists of three parts: the body, the cutting edges, and the shank. The body is the main part of the milling cutter, typically made from steel or carbide. The cutting edges are the parts that perform the cutting, and their shape and number directly affect cutting performance. The shank is used to secure the milling cutter to the milling machine.
Classification of Milling Cutters
Milling cutters can be classified based on different standards, mainly including the following categories:
Cutting Method:
- Face Mill: Suitable for face milling with flat cutting edges.
- End Mill: Cutting edges are vertical to the tool axis, ideal for complex shape machining.
Material:
- High-speed steel end mills: Suitable for machining soft metals and plastics, with good wear resistance.
- Carbide end mills: Ideal for hard materials, offering excellent wear resistance and high-temperature performance.
Function:
- Cylindrical end mill: used for general milling operations.
- Ball end mill: suitable for machining complex curved surfaces.
Common types of end mills.
There are various types of end mills, each with its own characteristics.
- End mill: Used for flat milling and processing complex shapes, suitable for various materials.
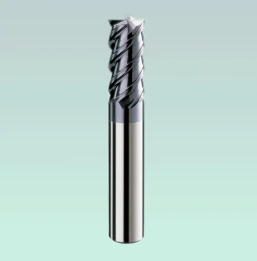
- Face mill: An ideal choice for flat machining, especially performs well in large-scale production.
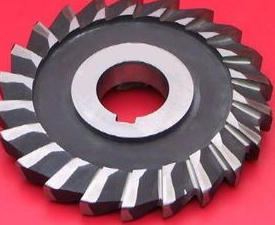
- Ball end mill: Specially designed for machining curves and molds, adaptable to complex shapes.
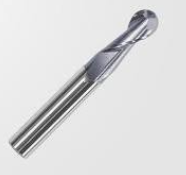
- Angle cutter: Suitable for machining inclined surfaces, increasing cutting flexibility.
- Carbide end mill: Wear-resistant, suitable for high-speed cutting and high-strength materials.
How to Choose the Right End Mill
Processing Materials
First, consider the type of material you will process. Different materials require different types of end mills. For soft metals such as aluminum and copper, it is advisable to use high-speed steel or coated end mills, as these options can significantly enhance cutting efficiency. Conversely, when working with hard metals like stainless steel and alloy steel, hard carbide end mills prove to be more suitable due to their superior wear resistance and thermal stability. Additionally, for materials like plastics and wood, high-speed steel end mills are appropriate since they typically do not necessitate high wear resistance. By considering these recommendations, you can optimize your milling processes effectively.
Cutting Depth and Feed Rate
Cutting depth and feed rate are key factors affecting milling performance. When selecting a milling cutter, it is essential to determine these based on the cutting conditions.
- Shallow cutting: You can choose a smaller cutting width and depth, suitable for using small-diameter milling cutters.
- Deep cutting: You need larger diameter milling cutters to improve cutting efficiency while ensuring the cutter’s strength.
Tool geometry.
The geometry of the milling cutter significantly affects cutting performance. Focus on the following aspects:
- The number of cutting edges: More edges increase cutting efficiency, but they also raise cutting force.
- The front angle and back angle: The front angle affects the sharpness of the cut, while the back angle influences the smoothness of cutting.
Tool Coating
The coating on milling cutters can significantly improve their performance. Common coatings include:
- TiN (Titanium Nitride): Increases wear resistance and thermal stability, suitable for processing various materials.
- TiAlN (Aluminum Titanium Nitride): Performs well at high temperatures, suitable for high-speed cutting.
- DLC (Diamond-Like Carbon): Suitable for non-metal and metal materials, offering good wear resistance and low friction coefficient.
Tool specifications and diameter.
Tool specifications and diameter are another key factor when selecting an end mill. Choose the appropriate diameter based on your machining needs and equipment conditions. Generally, a larger diameter suits rough machining, while a smaller diameter is ideal for fine machining.
Tips for Using End Mills
After selecting the right end mill, mastering some usage tips can further improve milling efficiency and processing quality.
Cutting parameter settings.
- Cutting speed: Choose the right cutting speed to prevent the milling cutter from overheating or wearing out during machining.
- Feed speed: Adjust the feed speed based on cutting depth, milling cutter diameter, and material characteristics to maintain stable cutting conditions.
Cutting fluid provides cooling and lubrication during milling. Choose the appropriate cutting fluid based on the material and cutting conditions to reduce cutting temperature and improve surface finish.
Regular inspection and maintenance.
Regularly check the wear of the milling cutter. Replace or sharpen the cutter promptly to ensure machining quality and production efficiency.
Frequently Asked Questions
How to determine if a milling cutter needs replacement?
During use, if you notice a decline in cutting quality, excessive cutting temperature, or a significant decrease in processing speed, these may indicate tool wear. At this point, you should consider replacing or sharpening the milling cutter.
How to extend the lifespan of a milling cutter?
Setting appropriate cutting parameters, using suitable cutting fluids, and regularly maintaining and checking the milling cutter can significantly extend its lifespan.
Can the same milling cutter be used to process different materials?
Some milling cutters can work with various materials, but to achieve optimal processing results, it is best to choose specialized cutters based on the material.
Conclution:
The choice and use of milling cutters directly affect processing efficiency and quality. By understanding the types, characteristics, and suitable conditions of milling cutters, you can better select the right one. We hope the information in this article helps you make informed decisions, improve production efficiency, and achieve high-quality processing.