With the rapid development of aerospace technology, the design and machining of aircraft engine housings have become more complex. The components of Mechanical Processing of Aircraft Engine Housings must withstand extreme conditions such as high temperatures, high pressure, and high-speed operation. At the same time, they must maintain high strength and precision while meeting lightweight design requirements. Efficient and precise machining of engine housings has become a critical technical challenge in aerospace manufacturing.
To address issues like complex geometries, difficult-to-machine materials, concentricity control for multiple holes, and errors caused by multiple clamping processes, Minnuo provides systematic solutions. We use high-precision five-axis machining centers, mill-turn machines, and dynamic path optimization technology to achieve multi-surface machining in a single clamping. We also rely on efficient cooling systems and specialized cutting tools to overcome the challenges of machining titanium alloys and high-temperature alloys. In addition, we apply flexible fixtures and online inspection technology to ensure the concentricity of multi-hole machining and the overall assembly accuracy.
Next, we will explain Minnuo’s specific methods and technical advantages in addressing these machining challenges. By combining efficient equipment, intelligent control, and customized process planning, we deliver higher quality and more efficient machining solutions for aerospace customers.
Analysis of Challenges in Mechanical Processing of Aircraft Engine Housings
The aircraft engine housing is a critical component of the engine, and its complex structure and specialized materials impose extremely high demands on machining processes.
Complex Geometric Structures
Engine housings often feature intricate designs such as multi-cavity, thin-walled structures, reinforcement ribs, and curved surfaces. These characteristics demand high-precision machining and cannot be completed in a single clamping. Multi-axis machining equipment becomes essential for handling these structures. Moreover, the multi-cavity design further increases the difficulty of process planning.
Difficult-to-Machine Materials
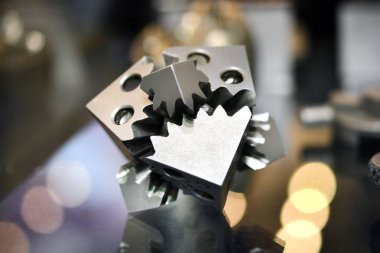
Engine housings are typically made of materials like titanium alloys, high-temperature alloys, or aluminum alloys.
- Titanium Alloys: High hardness and poor thermal conductivity lead to tool wear and heat buildup during cutting.
- High-Temperature Alloys: Strong and heat-resistant, but they harden during machining, which raises cutting challenges.
- Aluminum Alloys: Easier to machine, but thin-walled structures can deform easily during cutting.
Concentricity Issues in Multi-Hole Machining
Engine housings often have multiple interconnected holes, and the concentricity of these holes directly affects assembly quality and performance.
- Machining Challenges: When machining multiple holes, clamping errors or tool deviations often lead to misaligned holes. This misalignment can cause assembly difficulties or uneven stress distribution.
- High Precision Requirements: Multi-hole machining requires strict baseline consistency. Precise path planning and online inspection technology ensure high concentricity of the holes.
Impact of Multiple Clamping on Accuracy
Machining engine housings involves multi-surface processing, requiring multiple clamping stages. Frequent clamping increases the risk of cumulative positioning errors. Each clamping stage can introduce slight shifts in the part, which may compromise the machining accuracy of subsequent operations.
So how do we address these challenges?
How to Address Challenges in the Mechanical Processing of Aircraft Engine Housings with Complex Geometric Structures
The intricate geometry of engine housings poses significant challenges for machining precision and process requirements. Minnuo provides efficient and precise solutions through advanced technology and equipment.
Using Five-Axis Machining Centers to Tackle Multi-Cavity and Complex Curves
To handle multi-cavity designs, curved surfaces, and reinforcement ribs, we recommend high-precision five-axis machining centers, such as the MDH series horizontal machining center. This machine uses a “T” structure, resin sand casting, hollow screw cooling technology, and an electric spindle. These features ensure high rigidity, accuracy, and performance, enabling efficient and fast machining. These multi-axis machines allow multi-surface machining in one clamping, reducing errors caused by multiple setups.
- Precise Multi-Surface Machining: The five-axis machining centers can adjust tool angles flexibly for interference-free machining of complex curves.
- Single-Clamping Process: Completing machining in one setup reduces clamping times, boosting accuracy and efficiency.
- Dynamic Path Optimization: Built-in advanced path optimization calculates tool trajectories automatically, ensuring smooth tool movement on complex geometries.
High-Performance Clamping Systems for Stability and Accuracy
To solve challenges of covering all machining surfaces in one clamping, we offer customized high-performance fixtures:
- Multi-Function Flexible Fixtures: These adjust support points and clamping force according to the housing’s shape, reducing the risk of deformation in thin-walled or curved areas.
- Rotary Clamping Systems: Paired with five-axis machining tables, these fixtures can adjust angles automatically for seamless multi-surface machining.
Optimizing Tools and Cutting Parameters for Surface Quality and Efficiency
Machining complex geometries requires specialized tools and cutting strategies:
- High-Precision Tools: We recommend ball-end mills and coated tools designed for complex curves, improving surface smoothness.
- Dynamic Cutting Parameter Adjustment: The intelligent control system dynamically optimizes feed rates and spindle speeds for stable cutting in different areas, avoiding tool overload or overcutting.
How to Overcome Challenges of Difficult-to-Machine Materials
Machining Titanium Alloys
Challenge: Titanium alloys have high hardness and poor thermal conductivity, causing tool wear and heat buildup that lower efficiency and surface quality.
Our Solutions:
- High-Rigidity Five-Axis Machining Centers: Minnuo’s five-axis centers with rigid spindles and stable guide rails minimize cutting vibrations, improving stability for high-precision titanium machining.
- Optimized Cutting Parameters: Lower cutting speeds and increase chip thickness to reduce heat buildup. The intelligent control system dynamically adjusts feed rates to avoid tool wear from heat accumulation.
- Efficient Cooling Systems: High-pressure internal cooling systems deliver coolant directly to the cutting area, quickly removing heat and preventing tool overheating.
- Wear-Resistant Tools: PVD-coated or carbide tools designed for titanium alloys extend tool life and improve surface quality.
Machining High-Temperature Alloys
Challenge: High-temperature alloys have exceptional strength and heat resistance, leading to surface hardening and increased cutting forces during machining.
Our Approach:
- Mill-Turn Machines: These machines complete multiple operations in one clamping, reducing errors and improving efficiency, ideal for high-temperature alloys.
- Special Coated Tools: TiAlN-coated and ceramic tools maintain wear resistance even at high temperatures, reducing tool damage from cutting forces.
- Heat Deformation Compensation: Real-time temperature control and thermal compensation systems adjust machining parameters dynamically, ensuring accuracy.
- Dynamic Monitoring: Real-time monitoring detects cutting force changes and adjusts feed rates and speeds to prevent surface hardening or cutting defects.
Machining Thin-Walled Aluminum Structures
Challenge: Although aluminum alloys are easier to machine, thin-walled structures deform easily under cutting forces and heat, reducing dimensional accuracy.
Our Solutions:
- High-Speed Machining Centers: High-speed spindles and rapid feed rates remove material quickly, lowering cutting force and reducing deformation risks.
- Stepwise Machining Process: Multiple shallow cuts gradually remove material, avoiding deformation from excessive single cuts while maintaining precision.
- Vacuum Clamping Fixtures: These fixtures distribute clamping forces evenly, reducing deformation in thin-walled parts.
- Mirror-Coated Tools: High-precision tools designed for aluminum improve surface smoothness and minimize heat generation.
How to Solve Concentricity Issues in Multi-Hole Machining
Concentricity in multi-hole machining is critical for part performance and assembly quality. Minnuo delivers effective solutions using high-performance equipment, precise process planning, and intelligent machining technology to ensure high accuracy and consistency in multi-hole machining.
Unified Baseline Design for Consistency
- High-Precision Baseline Positioning: Automated baseline calibration ensures all holes are machined based on a consistent reference, avoiding errors from multiple setups.
- Shared Baseline for Multi-Step Processes: A unified baseline design ensures consistency across all operations, improving concentricity.
High-Performance Five-Axis Machining Centers to Minimize Positioning Errors
- Single-Clamping Multi-Hole Machining: Five-axis centers complete all hole machining in one setup, avoiding errors from multiple clamping.
- Dynamic Path Optimization: Intelligent systems generate optimal machining paths based on hole layouts, ensuring smooth, interference-free operations.
- Rigid Machine Design: High-rigidity machines and stable spindles reduce tool deviations, improving hole consistency.
Custom Fixture Design for Stability
- Flexible Fixtures: Customizable fixtures distribute clamping forces evenly, preventing positional shifts due to fixture stress.
- Multi-Station Fixtures: Designed for complex hole layouts, these fixtures allow machining of multiple holes in one clamping, further improving concentricity.
Precision Tools and Parameter Optimization
- High-Precision Boring and Drilling Tools: Specialized tools enhance hole size and coaxiality accuracy.
- Dynamic Cutting Parameter Adjustment: Load monitoring systems adjust spindle speeds and feed rates based on hole depth and diameter, avoiding overcutting or tool overload.
Online Inspection and Real-Time Correction
- Integrated Probe Systems: Built-in probes inspect hole positions and dimensions in real-time, ensuring every hole meets design requirements.
- Intelligent Compensation Technology: The system automatically adjusts tool positions and paths to correct any detected deviations, ensuring high concentricity.
Efficient Path Planning and Simulation
- Intelligent Path Planning: CAM software optimizes machining order and tool angles for interference-free, efficient cutting.
- Virtual Machining Simulation: Simulations identify potential errors before actual machining, improving accuracy and efficiency.
How to Overcome Accuracy Challenges from Multiple Clamping
Multi-Axis Machines for Single-Clamping Processes
- Smart Path Optimization: Advanced systems automatically generate paths to complete all features in a single setup.
- Rotary Tables: High-precision rotary tables enable seamless multi-surface machining for complex parts.
Customized High-Precision Fixtures to Reduce Errors
- Flexible Fixtures: Designed for complex geometries, these fixtures automatically adjust parts to standard positions, minimizing alignment errors.
- Repeatable Baseline Positioning: Precision pins and blocks maintain consistent baseline alignment across clamping stages.
- Vacuum Clamping: Vacuum fixtures distribute clamping forces evenly, preventing deformation in thin-walled or intricate parts.
Process Optimization and Standardized Operations
- Reduced Clamping Stages: Process optimization consolidates features into fewer operations, reducing cumulative errors.
- Standardized Clamping Protocols: Consistent clamping force and positioning ensure repeatable accuracy.
- Multi-Function Machines: Mill-turn centers like the MTN-B70 series consolidate turning, milling, and other operations in one setup, boosting precision and efficiency.
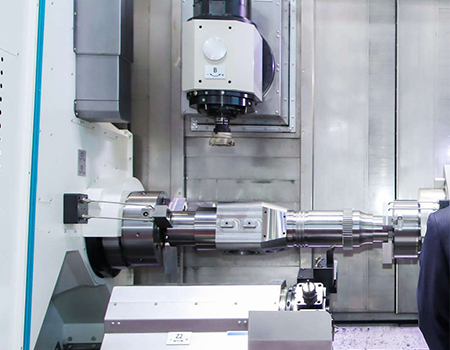
Conclusion:
Through a comprehensive analysis of the challenges in the Mechanical Processing of Aircraft Engine Housings and the implementation of targeted solutions, Minnuo has successfully overcome issues such as complex geometric structures, difficult-to-machine materials, multi-hole concentricity control, and errors from multiple clamping. We have successfully addressed issues like complex geometric structures, difficult-to-machine materials, multi-hole concentricity control, and errors from multiple clamping. With high-precision five-axis machining centers, mill-turn machines, and intelligent machining technologies, we achieve multi-process machining in a single clamping. Combining these with high-performance fixtures, specialized tools, and dynamic machining monitoring, we ensure exceptional precision and consistency. This approach provides customers with efficient and reliable production support.
If you face similar challenges in aerospace component machining or need more detailed solutions, feel free to reach out to Minnuo. Our technical team is ready to provide professional support and customized services tailored to your specific needs. Together, we can improve machining efficiency and product quality, achieving greater success in the high-end manufacturing industry.