With the advent of Industry 4.0, vertical machining centers are no longer just machines; they are at the heart of precision machining solutions. This article will take you into the world of vertical machining centers, exploring how they integrate multifunctional tool libraries, achieve multi-axis machining, and utilize the latest CNC technology to meet the high standards of industries such as aerospace, automotive manufacturing, and medical devices. We will also discuss the crucial role vertical machining centers play in improving machining accuracy, shortening production cycles, and reducing operating costs, highlighting their indispensable position in modern manufacturing.
What is a Vertical Machining Center?
A vertical machining center is a versatile machine tool with the spindle set vertically. It usually has two linear motion axes and a rotary table for horizontal axis rotation, enabling the machining of helical parts. VMCs typically feature a fixed column structure and a rectangular worktable, making them suitable for disk, sleeve, and plate parts, as well as molds and small complex shell parts. Most VMCs have at least three axes and can achieve three-axis simultaneous movement, with options to upgrade to five-axis or six-axis control.
Classification
- By Guideway Type: VMCs can be classified into hard rail and linear rail types. Hard rails are suitable for heavy cutting, while linear rails offer more flexible movement.
- By Spindle Speed: Low-speed VMCs have spindle speeds ranging from 6000-15000 rpm, while high-speed VMCs exceed 18000 rpm.
- By Structure: VMCs can be classified into C-type and gantry-type based on the bed structure.
Key Components
- Machine Body: Includes the base, column, spindle box, and doors. It is the core structure bearing all machining tasks.
- Worktable: Secures the workpiece and enables relative motion between the workpiece and tools, often with multiple work coordinates for complex machining.
- Spindle Box: Comprising the spindle, bearings, lubrication, and cooling systems, it critically impacts machining precision and efficiency.
- Control System: Combines hardware (CNC units, motion control cards, I/O modules, motor drivers) and software (CNC systems and programming software).
- Tool Magazine and ATC: Stores various tools and automatically handles tool changes.
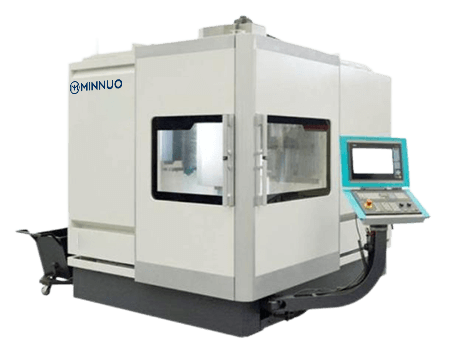
Applications and Workpieces
Vertical machining centers are advanced manufacturing equipment known for their high precision, efficiency, and automation. They are widely used in industries such as machinery manufacturing, automotive, aerospace, and mold making. VMCs can perform various machining operations, including milling, drilling, and tapping, and are essential for modern manufacturing due to their high precision and reliability.
Plate Parts: Machining flat metal plates involving milling, drilling, and tapping.
Disk Parts: Processing gears, pulleys, couplings with end face and outer circle machining.
Box Parts: Machining multi-surface parts like engine blocks and gearbox housings.
Complex Shape Parts: Suitable for parts with complex shapes and high precision requirements.
VMCs can machine both metal and non-metal materials, offering a broad processing range. They are among the most productive tools in CNC machine shops today.
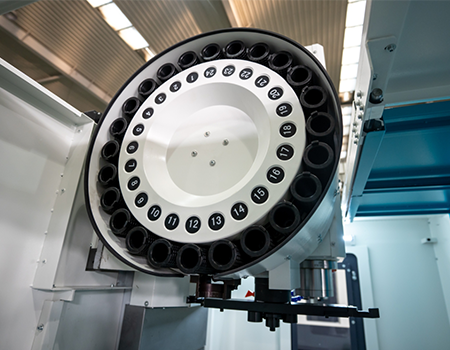
Advantages of Vertical Machining Centers
Vertical machining centers (VMCs) typically feature a fixed column and a rectangular worktable, making them ideal for machining disks, sleeves, and plates. They are known for their simple and convenient setup, ease of operation, clear visibility of the machining process, easy debugging, small footprint, and relatively low cost. Here are some of the key advantages:
- Ease of Operation
VMCs are user-friendly and do not require specialized mechanical knowledge. Basic knowledge of machine tools and CNC systems is sufficient. The interface is intuitive, allowing for program adjustments, integrated graphical and machining simulations, making operation straightforward. Additionally, VMCs boast strong automation capabilities, simplifying tasks in automated machining processes.
- High Machining Precision
VMCs offer extremely high machining precision, with longitudinal machining errors around 0.005mm and transverse errors around 0.01mm. The use of CNC systems for automated control ensures precise completion of various machining tasks, minimizing the impact of component quality and significantly enhancing precision while reducing scrap rates.
- Enhanced Production Efficiency
The machining efficiency of VMCs exceeds that of traditional machining processes by over ten times. Advanced automation technologies streamline machining processes, significantly boosting efficiency. VMCs do not require repositioning of workpieces during machining, simplifying the switch between different workpieces and allowing for multi-tasking and simultaneous processing of different procedures. These features collectively enhance production efficiency.
- Wide Range of Applications
VMCs can machine workpieces made from various materials, including plastic, aluminum alloy, and steel. They are suitable for precision machining of diverse parts and have a wide range of applications across industries such as aerospace, electronics, automotive, communications, and precision instruments.
However, due to the height limitation of the column and tool change constraints, VMCs may not be suitable for machining very tall parts. Therefore, it is essential to consider the size of the workpiece when selecting a vertical machining center.
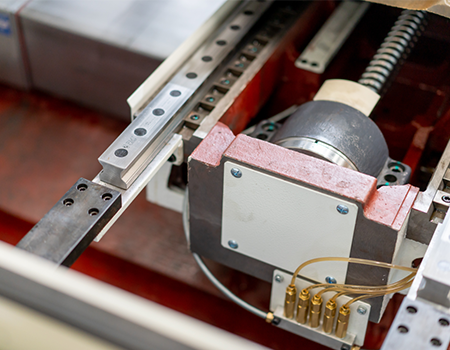
Vertical Machining Center (VMC) vs. Horizontal Machining Center (HMC)
Machining centers are a type of CNC machine tool that can perform complex machining tasks with high efficiency and precision. Among these, vertical machining centers (VMCs) and horizontal machining centers (HMCs) are the most common types. While both are machining centers, there are some key differences between them.
Contents | VMC | HMC |
Table | Perpendicular to the spindle axis | Parallel to the spindle axis |
Structure | Simple structure | Complex structure |
Processing efficiency | High efficiency in machining small parts | Highly effective in machining large and heavy parts |
Chip removal | More difficult than HMC | Simple |
Price | Cheap | Expensive |
Commissioning and Maintenance | Simple | Difficult |
Application | Machining of small workpieces such as disks, bushings, plate parts, etc. | Machining of box-type parts, large and heavy parts |
Maintenance and Troubleshooting
Vertical Machining Centers (VMCs) are high-precision, high-efficiency CNC machine tools widely used in the field of machining. To ensure their normal operation and machining quality, regular maintenance and management are crucial.
Daily Maintenance
- Cleaning and Lubrication: Regularly clean the surface and components of the VMC to prevent dust and cutting fluids from entering the equipment. Lubricate key components such as guide rails, ball screws, and bearings to ensure smooth operation.
- Operation Monitoring: During operation, regularly monitor the VMC’s status, including spindle speed, feed rate, and cutting processes, to ensure the machine is functioning normally.
- Troubleshooting: If any abnormal conditions such as unusual noises, vibrations, or alarms occur, immediately stop the operation and perform troubleshooting and repairs.
Periodic Maintenance
- Replacing Wear Parts: Regularly inspect and replace wear parts such as tools, tool holders, and sensors to prevent equipment failure due to worn-out components.
- Checking Fasteners: Regularly inspect and tighten fasteners like screws, nuts, and clamps to prevent malfunctions caused by loose components.
- Inspecting Electrical Systems: Periodically check and maintain the electrical systems, including motors, cables, and switches, to prevent downtime due to electrical faults.
- Cooling System Inspection: Regularly inspect and maintain the cooling system, including the cooling pump, cooling tower, and water pipes, to prevent overheating caused by cooling system failures.
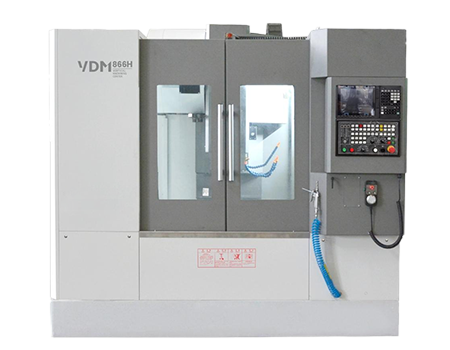
Market Trends and Future Development
With the advancement of smart manufacturing and digitalization, VMCs will continue to enhance their level of intelligence. Future VMCs will feature higher degrees of automation and smarter functions, potentially achieving automatic tool changing, automatic clamping, and online inspection. Additionally, the structure of VMCs will be further optimized to improve rigidity and stability, meeting the demands for higher precision and more complex machining tasks.
Minuo Machinery: Your Expert in Industrial Processing Solutions
Minuo Machinery, a professional Vertical Machining Center manufacturer and supplier in China., also offers horizontal machining centers, gantry machining centers, and high-end flexible production lines with customized services. While we ensure the highest product quality, we continuously strive to enhance our service quality. Our team comprises over 70 senior engineers and professional foreign trade sales experts. If you have difficulty choosing the right model, our engineers are available to provide professional guidance. Minuo Machinery is here to support your success!