Have you ever faced this dilemma: needing to cut a piece of metal but worried that traditional cutting methods might damage it? Cutting with heat, imprecise cuts, or even causing material deformation or cracking? Don’t worry, this is no longer a problem! Today, let’s talk about water jet machining – a tool that can help you say goodbye to these headaches. Whether you’re in manufacturing, design, or repair, water jet technology is a secret weapon you should definitely know about. Let’s take a look at why it’s so popular in modern manufacturing and why it’s worth your attention.
Water jet machining is not just about “water” – it’s a highly precise cutting technology that works on almost all materials, from metals and ceramics to glass and even brittle materials. Unlike traditional cutting methods, water jet cutting has no heat impact, which avoids thermal distortion and material damage. This makes it perfect for applications that require high precision and excellent surface quality.
This article will dive into the working principles, advantages, and key applications of water jet machining. We’ll also analyze practical cases to help you choose the right water jet method based on your specific needs. Whether you’re struggling with material selection or looking for ways to reduce processing costs, this article will offer you practical advice to make the best choices in water jet machining.
Working Principle of Water Jet Machining
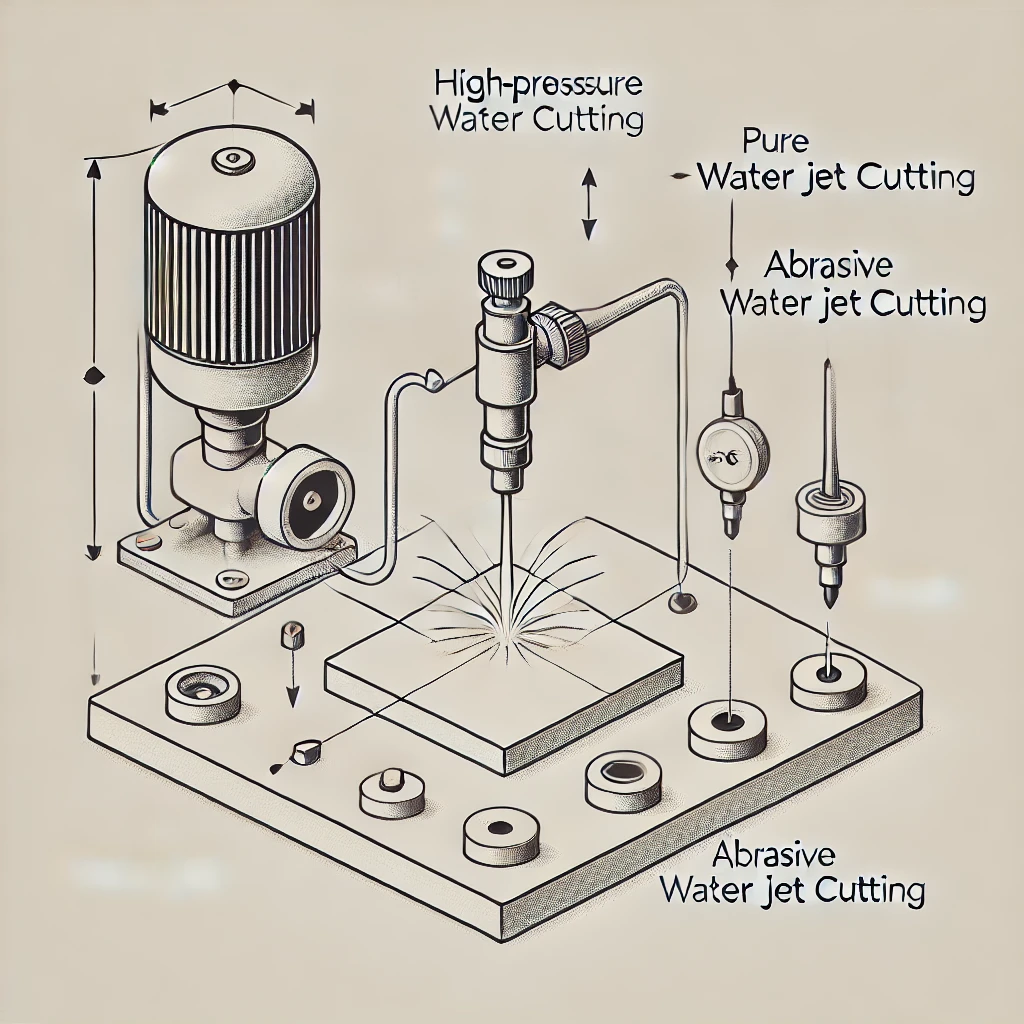
Water jet machining works by focusing high-pressure water through a very fine nozzle, using the high-speed jet of water to cut or penetrate various materials. Depending on the hardness of the material being cut, water jet machining is divided into two types: pure water jet cutting and abrasive water jet cutting.
Pure Water Jet Cutting
- Principle: This method uses only high-pressure water (usually between 30,000 to 90,000 psi), making it suitable for softer materials like rubber, plastic, foam, and others. The water stream is very fine, allowing for smooth cutting edges.
- Applications: It is commonly used for cutting softer materials such as gasket materials, rubber seals, and food products.
Abrasive Water Jet Cutting
- Principle: For harder materials such as metals, ceramics, glass, or stone, abrasives (like garnet) are mixed with the water stream to increase its cutting ability. The abrasive particles help the water jet cut through harder materials.
- Applications: This method is widely used for cutting hard materials like metals, stone, ceramics, and composite materials.
Advantages of Water Jet Machining
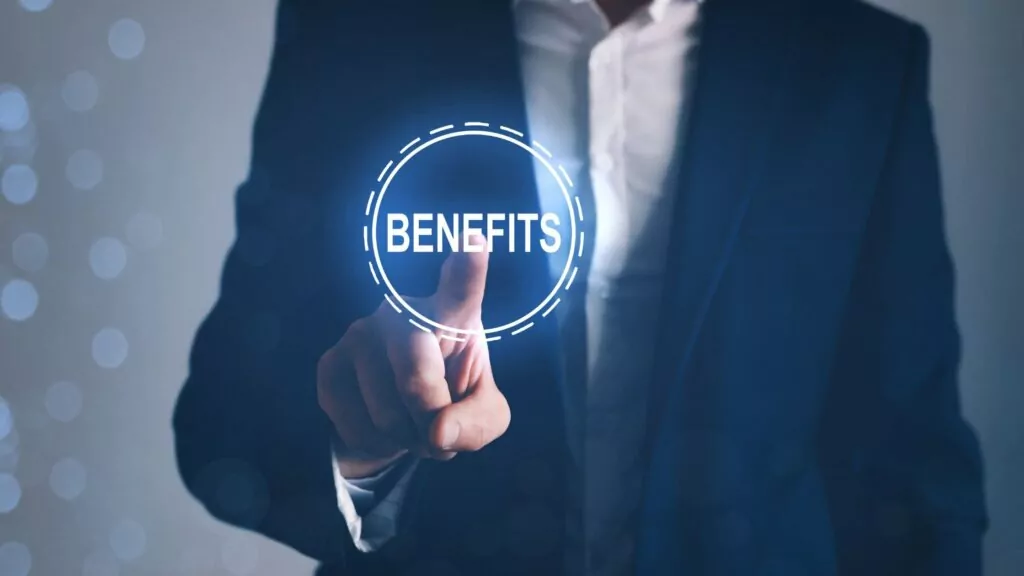
Water jet machining offers many unique advantages, making it an ideal choice for many industries. Below are some of the key benefits of water jet machining:
No Heat Affected Zone (HAZ)
- Advantage: Water jet cutting does not involve a heat source, so there is no heat-affected zone (HAZ). This prevents thermal distortion, discoloration, or hardening of materials. This is especially important for heat-sensitive materials like metals and composites.
High Precision and Fine Cutting
- Advantage: Water jet machining provides high-precision cutting with tolerances as small as ±0.1 mm (depending on the material and thickness). The fine water stream allows for cutting complex and intricate shapes, and the kerf is very narrow.
Wide Applicability
- Advantage: Water jet machining can cut almost all types of materials, including metals, plastics, composites, glass, ceramics, and even food. This wide applicability makes water jet technology suitable for multiple industries.
No Mechanical Stress
- Advantage: Water jet cutting does not apply mechanical stress to the material, meaning the material will not deform, crack, or experience stress due to the process. This is especially important for thin, brittle, or pre-stressed materials.
Environmental Friendliness
- Advantage: Water jet machining is considered an environmentally friendly method because it produces minimal waste, does not release harmful gases or chemicals, and both water and abrasives can be recycled, reducing the environmental impact.
- Sustainability: The water and abrasives used in water jet systems can typically be reused, minimizing waste and contributing to a more sustainable production process.
Materials that Can Be Cut with Water Jet Machining
Water jet machining is a highly versatile cutting technology capable of cutting nearly all types of materials, including soft, hard, and brittle materials. Whether it’s metals, plastics, ceramics, glass, stones, or composites, water jet cutting can handle them effectively. Depending on the material, water jet technology is divided into pure water jet and abrasive water jet cutting. Below, we’ll go over the different materials that water jet machining can cut.
Metal Materials
Water jet cutting is widely used in metalworking, especially for metals like stainless steel, aluminum, titanium alloys, copper, nickel, and various metal alloys.
- Stainless Steel: Water jet can cut stainless steel up to 200 mm thick, with smooth cut surfaces and no heat impact.
- Aluminum: Aluminum cutting is highly suitable for water jet technology, particularly for thicker aluminum plates.
- Titanium Alloys: Titanium alloys have high hardness, and water jet cutting can avoid thermal distortion and metal damage.
- Copper and Nickel Alloys: These metals, commonly found in high-temperature and corrosive environments, can also be effectively cut using water jet technology.
Plastic Materials
Water jet cutting performs excellently on plastic materials, suitable for various thicknesses, including heat-sensitive materials.
- PVC (Polyvinyl Chloride): Water jet cutting has no heat impact on PVC, making it an ideal method for cutting PVC sheets.
- Polycarbonate: This material does not undergo thermal distortion during processing, and water jet cutting ensures high precision and surface quality.
- Acrylic: Acrylic and other transparent plastics achieve smooth cutting edges with water jet cutting.
Stone and Glass
Water jet machining offers significant advantages in cutting stone and glass, especially for complex shapes and delicate cuts.
- Granite, Marble: Water jet technology is ideal for stone cutting, as it can precisely cut complex shapes without damaging the material.
- Glass: Water jet cutting avoids cracks and breakage caused by traditional methods, particularly when cutting fine glass components.
- Ceramics and Tiles: Water jet cutting is also suitable for ceramics and tiles, preventing cracking and thermal damage that may occur with traditional cutting methods.
Ceramics and Composites
Water jet machining is applicable to ceramics and composite materials, particularly those with high hardness and brittleness.
- Ceramics: Water jet cutting can handle various ceramics like silicate ceramics and alumina ceramics, preventing cracks or damage from heat exposure.
- Carbon Fiber Composites: In aerospace and automotive industries, water jet machining precisely cuts carbon fiber composites, avoiding heat damage and material cracking that can occur with traditional machining methods.
Wood and Cardboard
Water jet cutting can cut softer materials like wood and cardboard with precision, in addition to hard materials.
- Wood: Water jet cutting provides heat-free cutting for wood, avoiding burning and deformation that can occur with traditional methods.
- Cardboard: Water jet is also effective for cutting lightweight materials like cardboard, commonly used in packaging and art creation.
Food Processing
In addition to traditional industrial materials, the food industry widely uses water jet machining.
- Meat: Water jet can cut meat into precise shapes without generating heat, preserving the freshness of the food.
- Bread, Cakes, and More: Water jet technology can also be used for fine food cutting, such as bread, cakes, and vegetables, particularly where high precision is required.
Other Specialty Materials
- Composites: Materials like fiber-reinforced plastics (FRP) and fiberglass can be cut without damage using water jet machining.
- Rubber: Water jet is suitable for cutting various rubber materials, making it ideal for processing seals and gaskets.
- Paper and Textiles: Water jet can efficiently cut paper, textiles, and nonwoven fabrics, widely used in packaging, textile, and fashion industries.
Brittle Materials
An important advantage of water jet cutting is its ability to handle brittle materials without causing cracking or damage.
- Glass, Ceramics: Water jet cutting can cut glass and ceramics without creating cracks.
- Composite Glass and Mirror Materials: These materials are prone to cracking with traditional methods, but water jet cutting avoids these issues.
High Hardness Alloys and Super Alloys
Water jet machining is also effective on high-hardness, heat-resistant alloys.
- High-Temperature Alloys (e.g., Inconel, Nickel Alloys): Water jet can effectively cut these hard, corrosion-resistant alloys, widely used in aerospace, automotive, and energy industries.
Inorganic Materials
Inorganic materials such as silicon, bauxite, and quartz are also suitable for water jet cutting, especially in semiconductor manufacturing and high-tech industries.
Factors to Consider When Choosing Water Jet Machining
When deciding whether to choose water jet machining, there are several key factors to consider:
Material Type and Thickness
- Water jet machining is suitable for almost all materials, but the thickness and composition of the material can affect cutting time and quality. To achieve effective cutting of thicker or harder materials, abrasive water jet cutting is usually required.
Cost
- While water jet machining offers significant advantages in terms of precision and material integrity, its cost may be higher than traditional cutting methods for certain materials. When choosing, it’s important to weigh the benefits against the cost to ensure it is the most cost-effective option.
Cost Considerations for Water Jet Cutting
The cost of choosing water jet cutting (or water cutting) depends on several factors, including the type of material, cutting complexity, required precision, processing time, and equipment usage.
Material Type and Thickness
The type of material directly impacts the cost of water jet cutting. Different material hardness and thickness require different processing methods, which in turn affect the cost.
- Soft materials (e.g., plastics, rubber, foam): These are relatively inexpensive, typically costing between $2 and $8 per square meter (about 15 to 60 RMB).
- Hard materials (e.g., stainless steel, aluminum, titanium): Materials with higher hardness require more energy and abrasive materials, making the price range usually between $10 and $30 per square meter (about 70 to 210 RMB), depending on material thickness and cutting requirements.
- Brittle materials (e.g., glass, ceramics): These require precise handling, but water jet cutting can avoid cracking, so the cost typically ranges from $20 to $50 per square meter (about 140 to 350 RMB).
- Bulk materials (e.g., stone, marble, granite): The cost for materials like stone is higher and often requires longer cutting times. Prices usually range from $15 to $40 per square meter (about 100 to 280 RMB).
Cutting Complexity and Precision Requirements
- Simple cuts: For simple straight cuts or larger material sizes, the unit cost tends to be lower because the processing speed is faster and the cutting is simpler.
- Complex cuts: For parts with complex geometries (e.g., curves, internal holes, or intricate cutting profiles), more processing time and finer control are required, which increases the price.
- Precision requirements: If the cut requires high precision (e.g., micron-level accuracy or extremely smooth cut edges), additional time and precision control will also increase the cost.
Cutting Area
The cost of water jet cutting is typically calculated by area, so larger cuts are generally more cost-effective. However, the total cost is still influenced by the processing time. Some companies offer discounts for large-area cutting.
- Large-area cuts: For large-scale production or large-size cuts, the price per square meter tends to be lower because the equipment’s runtime is spread across more material.
- Small batch or small-area cuts: For small batch production or small-area cuts, the processing cost per piece may be higher.
Cutting Time and Equipment Usage
The cost of water jet cutting is also closely related to equipment usage time. Cutting time is a critical factor in determining the overall cost:
- Hourly equipment costs: The equipment charges for water jet cutting typically range from $100 to $200 per hour (about 700 to 1400 RMB), depending on the type of equipment and the complexity of the cut.
- Operator fees: Although water jet cutting is highly automated, manual intervention is still required, particularly in equipment setup and monitoring. Labor costs vary by region and working hours.
Abrasive Use
For hard materials (e.g., metals, stone), abrasive materials are required. The type and consumption of abrasives affect the overall cost.
- Abrasive costs: Common abrasives used in water jet cutting, such as alumina or garnet, are priced between $0.2 and $0.5 per pound (about 1.4 to 3.5 RMB per pound). The exact consumption depends on the material type and cutting thickness.
- Abrasive consumption: Thicker materials (e.g., metal plates over 50mm thick) typically require more abrasives, which directly impacts the cutting cost.
Post-Processing Costs
In some cases, the cut parts may need post-processing (e.g., deburring, polishing, cleaning), which will add extra costs.
- Post-processing: The cost of post-processing depends on the size of the part, surface requirements, and complexity. Generally, deburring and surface polishing will increase the overall cost.
Additional Fees
- Material costs: Special materials, such as high-grade alloys or custom materials, may increase the cost of the material itself.
- Shipping and packaging: If the processed parts need to be shipped or packaged, these costs will also affect the final price.
- Minimum order fees: Some companies may charge a minimum fee for small orders to cover equipment setup and maintenance costs.
Cutting Speed
Although water jet cutting is highly precise, its speed may not be as fast as other cutting methods, such as laser or plasma cutting, especially when handling large volumes or simple shapes. However, water jet cutting ensures high-quality cuts, particularly for complex parts that require fine details.
Post-Processing Requirements
Depending on the material and specific application, some water jet cut parts may require additional post-processing, such as smoothing, polishing, or deburring, especially when the cut edges are rough.
Conclusion: The Future Development of Water Jet Cutting and Minnuo’s Solutions
As nozzle technology, automation levels, and efficiency continue to improve, water jet cutting technology will undoubtedly play a more significant role in the future of manufacturing. This is especially true in industries that require high precision, complex processes, and environmental sustainability. Whether it’s metal, ceramics, glass, or food and precision medical components, water jet cutting offers efficient, accurate, and eco-friendly solutions.
For this reason, choosing the right water jet equipment is crucial. As a leading manufacturer in the industry, Minnuo is dedicated to providing customers with top-tier water jet cutting machines and customized solutions. By combining advanced technology, strict quality control, and excellent after-sales service, we ensure that each customer can fully leverage the advantages of water jet cutting at the most cost-effective rate. Whether your needs involve high-precision cutting, complex shape processing, or higher environmental and sustainability requirements, Minno’s water jet machines will help you achieve the ideal results. When you choose Minnuo, you’re not just selecting equipment; you’re choosing a reliable partner to elevate your manufacturing processes to the next level.
Let’s embrace the endless possibilities that water jet technology offers and stay ahead in the industry together!