The centerless grinding machine represents a significant innovation in the development of grinding machines. It efficiently addresses the challenge of processing long, slender workpieces, effectively compensating for the limitations of cylindrical grinders. Today, let’s take a comprehensive look at what a centerless grinding machine is.
Definition: What is a Centerless Grinding Machine
Centerless grinder is a type of grinding machine that performs grinding without requiring the workpiece to be centered. It mainly consists of three components: the grinding wheel, the regulating wheel, and the workpiece support. The grinding wheel performs the actual grinding, the regulating wheel controls the rotation and in-feed speed of the workpiece, and the workpiece support provides stability during the grinding process. These components work together to achieve precise grinding in a centerless grinder.
Components:
- Grinding Wheel: Removes material from the surface to achieve the desired finish.
- Regulating Wheel: Controls the rotational speed and feed rate of the workpiece.
- Workpiece Support: Provides support to the workpiece during grinding.
Structural Features:
- The machine table moves longitudinally, and the grinding wheel head moves rapidly in and out under hydraulic control. A DC motor drives the workpiece rotation, allowing for stepless speed adjustment within a specific range.
- Separate motors power the lubrication oil pump for the grinding wheel head’s spindle bearings, the coolant pump, and the grinding wheel head.
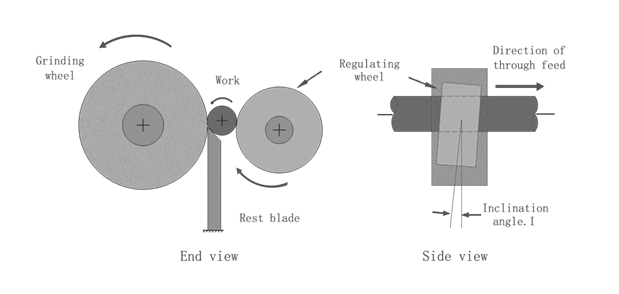
Working Principle of Centerless Grinding Machine
The grinding wheel rotates at high speed for grinding, while the regulating wheel rotates in the same direction at a slower speed, causing the workpiece to rotate and feed in a circular motion. During through-feed grinding, axial feed is achieved by adjusting the inclination angle of the regulating wheel’s axis. In plunge grinding, radial feed is achieved by moving the regulating wheel head or the grinding wheel head.
Types of Centerless Grinding
Based on the feeding method, centerless grinding can be divided into:
Through-Feed Centerless Grinding
The workpiece passes through the grinding wheel, offering high production efficiency for grinding needle rollers, cylindrical rollers, and tapered rollers.
In-Feed Centerless Grinding
The workpiece is manually fed, suitable for complex-shaped workpieces, such as spherical rollers.
End-Feed Centerless Grinding
The workpiece feeds longitudinally, allowing simultaneous feeding and grinding, ideal for workpieces with longer end faces.
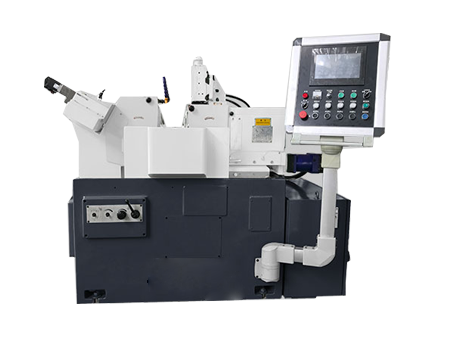
Advantages and Disadvantages of Centerless Grinding
Advantages:
Continuous processing without the need for retraction or clamping saves time and increases productivity.
The support rigidity of the center frame and regulating wheel positioning mechanism is better than that of the tailstock and center frame mechanism of ordinary cylindrical grinders, allowing for larger cutting volumes and making it suitable for processing long, slender shafts. It also facilitates high-speed and powerful grinding.
The grinding allowance is on the workpiece diameter, so the impact of grinding wheel wear, feed mechanism compensation, and repeat positioning accuracy errors of the plunge mechanism on the workpiece diameter precision is only half that of ordinary cylindrical grinders. There is no need to drill center holes, making automation of loading and unloading easier.
Wide grinding wheels and through-feed mechanisms on centerless grinders allow for larger grinding allowances per pass. During plunge grinding, complex profiles can be sequentially ground or multi-wheel grinding can be used, enhancing productivity and broadening the scope of application.
Disadvantages:
Centerless cylindrical grinders lack mechanisms to ensure the relative positional accuracy (such as coaxiality and perpendicularity) between the ground and non-ground surfaces. The roundness of the ground surface can be poor when grinding discontinuous outer surfaces circumferentially.
The ground surface is prone to odd-numbered polygonal roundness, which can lead to the illusion of a smaller measured size than the maximum solid size, affecting assembly quality and performance.
The machine setup is complex and time-consuming. Each time the workpiece diameter changes, the bracket height, distance, and related process parameters must be adjusted, making the adjustment technically challenging and unsuitable for small batch and single-piece production.
Centerless Grinding vs. Cylindrical Grinding
Efficiency: Cylindrical grinding is far less efficient than centerless grinding, leading to higher production costs
Precision: Centerless grinding offers higher precision and easier feed adjustment, with a higher degree of automation.
Workpiece Requirements: Cylindrical grinders are suitable for precise grinding of various cylindrical and conical workpieces, while centerless grinders are ideal for long bar stock or tubing.
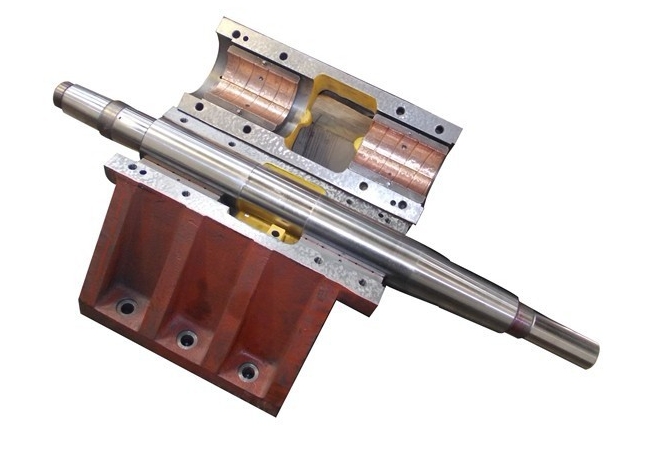
Machinable Parts & Applications
Centerless grinders are suitable for machining cylindrical and conical parts such as shafts, sleeves, rollers, and roller bearing outer rings. Typically, the machining diameter range for shafts is between 0.8mm and 60mm, with lengths around 1000mm.
Shaft Parts: Centerless grinders are commonly used for processing long, thin shaft parts, such as transmission shafts, main shafts, and clutch shafts in automobiles, motorcycles, airplanes, and ships.
Automotive Components: Precision parts like crankshafts, rocker arms, and camshafts in car engines require high-precision machining with centerless grinders to ensure engine reliability and efficiency.
Aerospace Engine Components: These include bearing housings, bearing seat installation holes, and bearing outer rings in aerospace engines.
Molds: Centerless grinders are effective in processing complex plastic molds, deep hole molds, and ejector molds.
Medical Devices: They are crucial for manufacturing surgical instruments and various medical catheters.
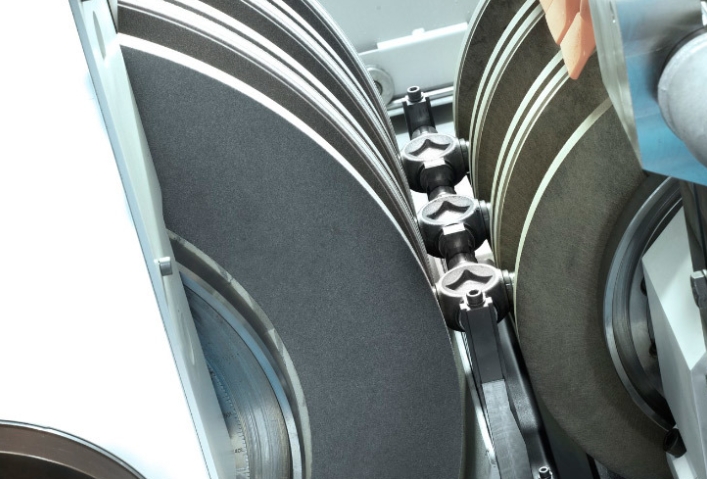
How to Choose a Centerless Grinder
Bed: The bed is the foundation of a centerless grinder, affecting the machine’s stability and precision. Choose a bed that offers strong support, high vibration resistance, excellent flatness, minimal burrs, and a smooth surface finish.
Spindle: The spindle is the core component of a centerless grinder, impacting machining accuracy and efficiency. Opt for a spindle with high speed, heavy load capacity, a cooling system, and high precision to ensure machining accuracy and stability.
Control System: It’s best to purchase a grinder with a unified control system for better operation and maintenance, ensuring consistent operation.
Other Considerations: Consider the machine’s reliability, cost-effectiveness, and other factors based on production needs, budget, and technical requirements.
Choose Minnuo
Minnuo Machinery provides expert product guidance, offering you high-standard grinding techniques and top-quality products at the price of second-hand machines. Contact us to help you succeed!