Internal grinding is a precision machining technique focusing on the inner surface of holes. This method sees extensive use in industries such as machining, automotive manufacturing, and aerospace. These fields demand extremely high standards for part size accuracy, surface quality, and shape precision, making internal grinding the ideal solution. It works with various materials, including metals, ceramics, and plastics, and can handle different shapes and sizes of inner holes, such as cylindrical, tapered, and threaded holes. Due to its high precision and efficiency, internal cylindrical grinding has become an essential part of modern manufacturing.
Definition: What is Internal Grinding?
Internal grinding is a precision machining process that uses a rotating grinding stone to work on the inner surfaces of holes. This technique handles through holes, blind holes, stepped holes, and end faces. It can also grind hardened workpieces, making it widely used in machining. Internal cylindrical grinding achieves high dimensional accuracy.
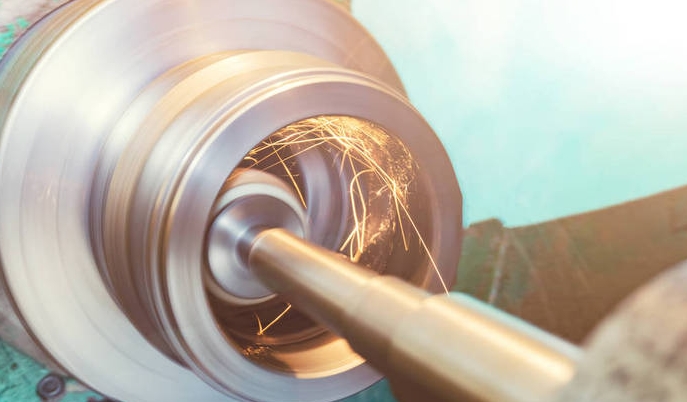
Types of Grinding and Their Comparisons
Grinding uses abrasive tools to process the surface of workpieces. Based on the target and method, grinding can be divided into external cylindrical grinding, internal cylindrical grinding, surface grinding, and centerless grinding. The main differences among these methods lie in the workpiece, type of abrasive tools, machine structure, and processing principles:
- External Cylindrical Grinding: This method focuses on grinding the outer surface of workpieces, such as the outer diameter of shafts. It typically uses a grinding wheel, and the machine structure is relatively simple. During processing, the workpiece rotates while the grinding wheel moves along the workpiece’s axis for grinding.
- Internal Grinding: This technique grinds the inner surfaces of workpieces, like holes and slots. It can use grinding wheels or oil stones, and the machine structure is more complex, requiring specialized grinding heads and support devices. The abrasive tool enters the workpiece for internal grinding.
- Surface Grinding: This method grinds the flat surfaces of workpieces, such as planes and steps. It usually employs a flat grinding wheel, and the machine structure is relatively simple. During processing, the workpiece and grinding wheel move in a relative linear motion.
- Centerless Grinding: This technique also grinds the outer surface of workpieces. Unlike external cylindrical grinding, it does not use a center hole for positioning. Instead, it relies on the pressure between the grinding wheel and a regulating wheel for positioning and grinding. This method is suitable for mass production and workpieces requiring high surface roughness.
In summary, the main differences among these grinding methods lie in the workpiece, type of abrasive tools, machine structure, and processing principles.
Internal Cylindrical Grinding vs. External Cylindrical Grinding
- Smaller Wheel Diameter and Lower Speed: Internal cylindrical grinding uses wheels with smaller diameters. The wheel speed is limited by the internal grinding tool’s speed, typically ranging from 20 to 30 m/s. This lower grinding speed makes it challenging to reduce the surface roughness of the workpiece.
- Greater Contact Arc: The grinding wheel’s outer surface contacts the workpiece’s inner surface in an inscribed circle, resulting in a larger contact arc compared to external cylindrical grinding. This generates higher grinding forces and more heat, causing abrasive grains to dull quickly and making the workpiece prone to overheating, burning, or deformation.
- Difficult Coolant and Chip Removal: Coolant struggles to reach the grinding area, and chips are hard to expel, leading to wheel clogging and negatively affecting the workpiece’s surface quality.
- Lower Rigidity and Vibration Issues: The grinding wheel, extended on a long shaft, lacks rigidity and is prone to deformation and vibration. This affects machining accuracy and surface roughness, also limiting the increase in grinding feed rates.
Methods of Internal Cylindrical Grinding
Internal cylindrical grinding commonly uses the longitudinal method and the plunge-cut method.
- Longitudinal Grinding Method: This method requires thorough cooling and frequent removal of chips from the hole. Careful adjustment of the stop block position ensures the coaxiality of stepped holes.
- Plunge-Cut Grinding Method: This method suits workpieces with short internal lengths, offering higher production efficiency. It demands good rigidity of the extended shaft. The grinding wheel tends to clog and dull quickly, so it should be dressed promptly.
Choosing Internal Grinding Wheels
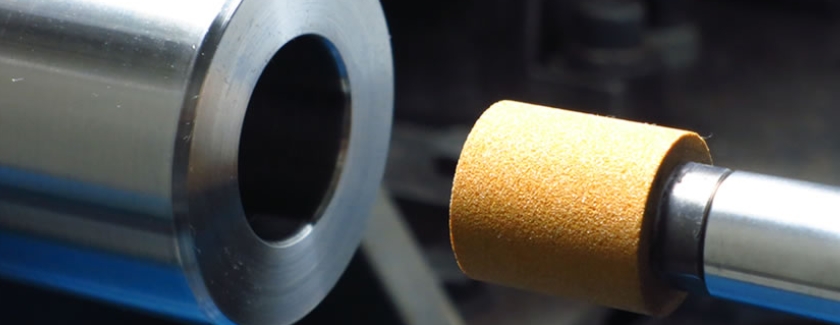
Wheel Diameter: To achieve good grinding results, the wheel diameter should have an appropriate ratio to the hole diameter, typically between 0.5 and 0.9. For larger hole diameters, choose a smaller ratio due to higher circumferential speed, heat, and chip removal challenges. For smaller hole diameters, use a larger ratio to compensate for the lower wheel speed.
Wheel Width: A wider wheel improves surface quality and production efficiency while reducing wheel wear. However, avoid excessively wide wheels as they increase grinding force, potentially causing the extended shaft to bend.
Wheel Hardness:
1. For high-hardness workpieces, use a softer wheel. This ensures worn abrasive grains fall off quickly, maintaining sharp grains and preventing burns from excessive grinding heat.
2. For low-hardness workpieces, choose a harder wheel to slow down grain shedding, optimizing the abrasive action.
3. When the wheel has a large contact area with the workpiece, use a softer wheel to ensure quick grain shedding and avoid surface burns caused by clogged wheels.
4. Use a softer wheel for grinding thin-walled and poor-thermal-conductivity workpieces.
5. For precision and form grinding, opt for a harder wheel to maintain necessary shape accuracy.
6. For wheels with a larger grit size, select a softer wheel to prevent clogging.
Wheel Grit Size: To enhance cutting force while avoiding workpiece burns, use coarser grit sizes. Common internal grinding wheel grits are F36, F46, and F60.
Wheel Structure: Internal grinding poses chip removal challenges. Choose wheels with a more open structure (1-2 grades looser) than those used for external grinding to provide space for chips and prevent early clogging.
Wheel Shape: Common shapes for internal grinding wheels are flat and single-sided recessed. Single-sided recessed wheels can also grind the end faces of stepped holes in addition to internal holes.
Internal Grinding: Workpieces and Applications
Workpiece Types
Internal cylindrical grinding machines specialize in machining the inner holes, diameters, and surfaces of workpieces. These machines use grinding wheels to fine-tune inner diameters and produce high-quality surface finishes. They are commonly used in manufacturing various components for automation equipment and heavy machinery industries, including shafts, sleeves, bearings, gears, and cylinders. Additionally, these machines can produce precision molds, dies, and cutting tools.
Application Fields
Automotive Industry: Internal cylindrical grinding machines grind the inner holes and diameters of high-precision automotive parts such as crankshafts, camshafts, connecting rods, and engine blocks.
Machinery Industry: These machines are frequently used to manufacture mechanical components, especially those related to shafts, including gears, bearings, couplings, and various transmission devices.
Aerospace Industry: In aerospace, internal cylindrical grinding machines produce high-precision and high-quality aerospace engines and components, such as grinding the inner holes and diameters of aerospace bearings.
Electronics Industry: In electronics, these machines process various precision electronic devices, such as magnetic heads and semiconductor chips.
Internal cylindrical grinding also applies to valve seats, oil pump components, mechanical seals, hydraulic parts, and more.
Recommended Internal Grinding Machine
Minnuo internal cylindrical grinding machines handle grinding diameters from 3mm to 250mm, with a maximum effective grinding depth of 1350mm. These machines can grind deep holes, end faces, and internal arcs in a single setup. They utilize Siemens 828D or FANUC-0iTD systems, ensuring high-precision internal cylindrical grinding. For high-quality precision machining and competitive pricing, choose Minnuo’s internal cylindrical grinding machines!