PRODUCTS CATEGORY
Intelligent Manufacturing Production Line
+Machining centers
+Lathe Machine
+Milling Machine
+Grinding Machine
+Drilling Machine
+Metal forming equipment
+Boring machine
+Machine Tool Accessories
+Specialized Machines
+Electrical Discharge Machine
+Related News
CNC Drill & Tap Centre TC-1600
CNC drill and tap centre TC-1600 adopts mechatronic design, spindle box adopts high speed spindle unit, spindle adopts BT40 specification with 5.5/7.5KW motor and Mitsubishi system. It has excellent advantages in precision cutting and heavy cutting for steel and aluminium parts of profile type. After the workpiece is clamped once, the machine tool can automatically and continuously complete a variety of processes such as milling, drilling, boring, expanding, reaming, countersinking, tapping and other processing.
- Bench size (length and width): 1700×400mm
- Triaxial stroke (X / Y / Z): 1600/500/300
- Maximum carrying capacity: 450kg
- Main shaft speed: 20000rpm
Name | Unit | Parameter | |
Range of work | Triaxial stroke (X / Y / Z) | mm | 1600/500/300 |
The distance from the spindle center line to the column guide rail surface | mm | 516 | |
The distance from the main nose to the working top | mm | 150~450 | |
Workingbench | Bench size (length and width) | mm | 1700×400 |
Maximum carrying capacity | kg | 450 | |
T-type groove (slot number, slot width spacing) |
| 3×14×121 | |
principal axis | main shaft speed | rpm | 20000 |
taper hole of spindle |
| BT30/BT40 | |
Power of spindle motor | KW | 5.5/7.5 | |
Speed | Fast moving speed (X / Y / Z axis) | m/min | 30/48/48 |
Cut into give speed | m/min | 10/10/10 | |
Tool magazine | Number of knives | grasp | 21 |
Tool maximum diameter / length / weight of |
| φ 60mm/200mm/3kg | |
Maximum diameter (full / adjacent) | mm | 60/80 | |
Machine tool accuracy | Positioning accuracy (X / Y / Z) | mm | 0.008 |
Repeat positioning accuracy (X / Y / Z) | mm | 0.005 | |
Else | Gas source / air pressure |
| 280L/min 6~8bar |
Total electrical capacity of the machine tool | KVA | 15 | |
Water tank volume | L | 160 | |
Machine Exsize (XYZ) | mm | 3850×2620×2370 | |
Machine tool weight (approx.) | kg | 4100 |
Features
The TC-1600 machine adopts the new FEM (Finite Element Analysis System) simulation and optimisation design method. The overall strength and rigidity of the machine is optimised on the basis of the best machining dynamic performance, and a high degree of unity in man-machine harmony is achieved.
- The TC-1600 utilizes an innovative design of direct connection between the spindle and motor motor, eliminating the noise, backlash and vibration problems associated with traditional belt or gear drives. Speed can reach up to 20,000/24,000/30,000 rpm for high quality tapping results and surface finish.The three-axis movement adopts a linear slide, which makes the three-axis rapid traverse speed up to 30/48/48 meters per minute, and at the same time, it can support heavy loads to ensure the accuracy of positioning.
- The key components of the machine, including the base, table, column, crossbeam, slide saddle and spindle box, are all made of resin sand molding HT300 strength cast iron. Through the secondary annealing treatment, the casting stress and the internal stress generated by rough machining are completely eliminated, thus ensuring the high rigidity and stability of the structure and guaranteeing the product quality.
- In addition, the castings have been analyzed by Finite Element Analysis (FEA) computer calculations to ensure reasonable structural strength and matching of reinforcing ribs, which further enhances the high rigidity of the machinery.
- We also adopt BT30-21T clamping arm type tool changer, the tool change time is only 1.6 seconds, which improves the production efficiency.
Applications
- The TC-1600 machine is widely used in 5G and 3C industries, as well as in small plate parts, disk-shaped parts, and shells in the aviation, aerospace, automotive parts, and medical device industries.
Order number | Host standard configuration |
1 | Main transmission system (including AC servo main motor, spindle, etc.) |
2 | X, Y, Z three-axis dragging system (including AC frequency conversion servo motor, coupling, ball wire rod, linear guide rail, etc.) |
3 | Main components (including base, bench, column, saddle, spindle box, etc.) |
4 | The numerical control system includes CNC cabinet, power module, servo module, PLC, operation unit, display, mobile hand pulse generator, heat exchanger, etc |
5 | Pneumatic triplet |
6 | Automatic lubrication system (including motor, pump, distributor, etc.) |
7 | Cutting fluid system (including motor, pump, chip flushing device and chip storage tray |
8 | X, Y and Z axis guide rail protection |
9 | Working light and warning lights |
10 | Random technical documents(Manual 1 set One set of qualification certificate and one set of packing list) |
In order to meet different market needs, we provide modular, customised solutions, the system uses the Mitsubishi CNC controller can also be upgraded to Fanuc, Siemens, can be any 4-axis combination of machining, there is a need to contact us.
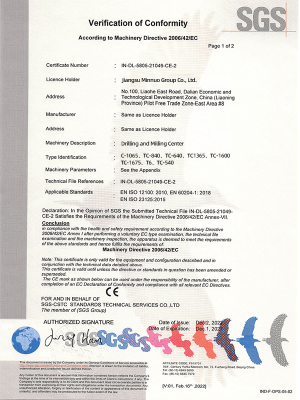

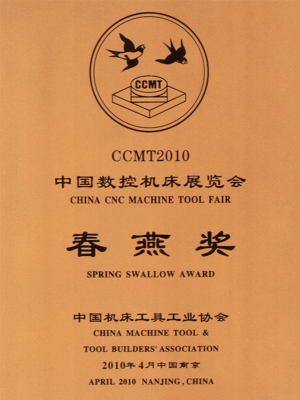
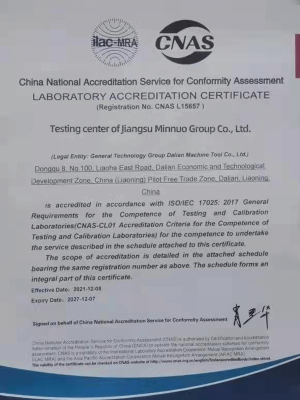
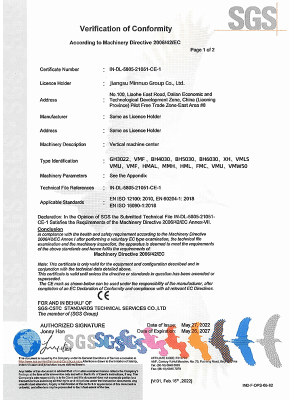
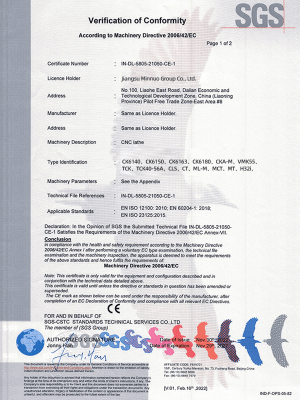
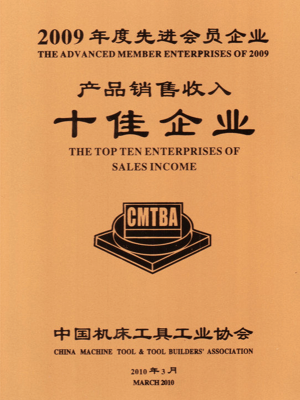
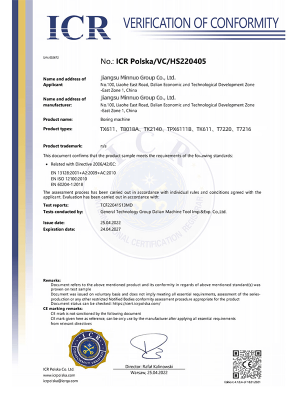
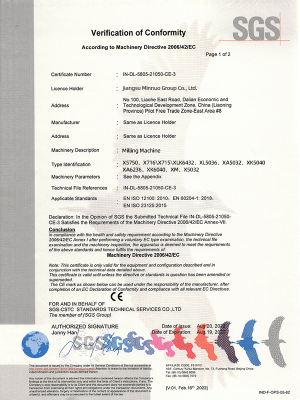
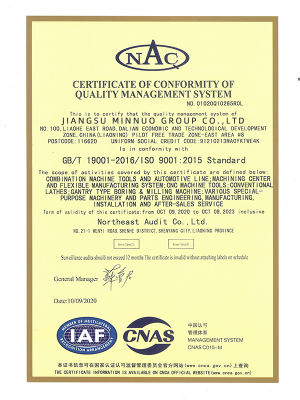
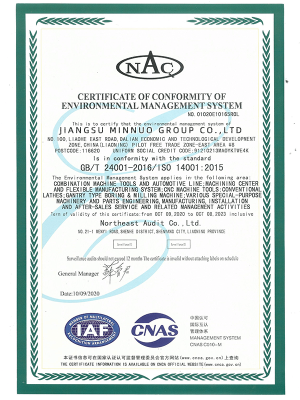
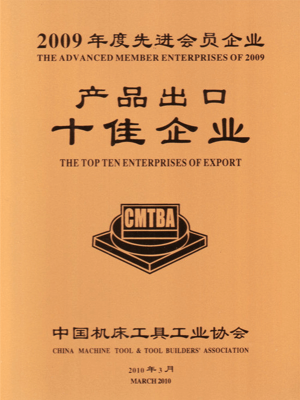
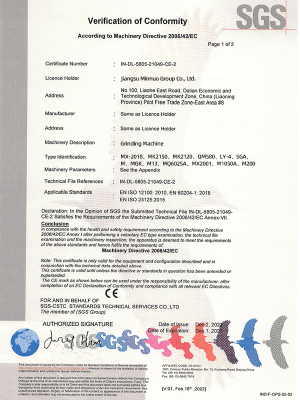

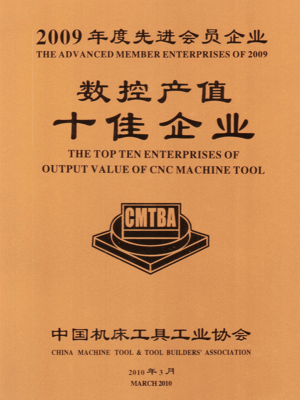
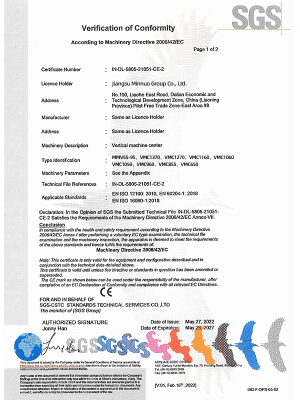
Certified Quality
We are fully committed to the highest standards of quality for our development andmanufacturing processes as well as to preserving the environment. Our products haveobtained a number of domestic and foreign authoritative certifications.
Get In touch
(+86) 13295238763
24 hours online service
Address No. 2 Xintai Road, Economic and Technological Development Zone Jingjiang City Jiangsu Province, China
Email cncitd@minnuo.com