PRODUCTS CATEGORY
Intelligent Manufacturing Production Line
+Machining centers
+Lathe Machine
+Milling Machine
+Grinding Machine
+Drilling Machine
+Metal forming equipment
+Boring machine
+Machine Tool Accessories
+Specialized Machines
+Electrical Discharge Machine
+Related News
9 axis Horizontal Turning and Milling Center MTN-B70ST Series
9 -axis MTN-B70ST series horizontal turning and milling machining centers can realize complete machining of hexahedron by combining various functional parts, truly realizing multi-functional, multi-process and multi-technology composite integration of one machine. With the compound machining capability of turning, boring, milling, drilling, tapping and other functions, it can complete the machining of complex workpieces quickly and with high quality, and is especially suitable for the machining of shaped rotary parts (e.g., barrels, crankshafts, blades, etc.) with complex shapes and high precision requirements in various industries.
- Max. work piece length: 1580/2500/3000mm
- Max.turning diameter: φ700mm
- Max. swing over bed: φ700
- Workpiece weight: 1500kg
PARAMETERS | unit | MTN-B70S | ||
machining | Max. swing over bed | mm | φ700 | |
Max.turning diameter | mm | φ700 | ||
Max. work piece length | mm | 1580/2500/3000 | ||
Chuck Size | Main spindle | inch | 12 (0pt: 15) | |
Sub-spindle | inch | 10 (0pt: 12) | ||
Workpiece weight | kg | 1500 | ||
travel | X/Y axis | mm | 835/+210 | |
Z-axis | mm | 1700/2600/3100 | ||
W-axis | mm | 1600/2600/3100 | ||
B-axis | ° | 士120 | ||
C1/C2 axis | ° | 360 | ||
X2/Z2 axis | mm | — |
Features
- With its orthogonal horizontal Y-axis layout, the machine integrates multifunctional components to realize complete hexahedral machining capability.
- The dual tool magazine system significantly enhances the machining capability of the single machine, while the automatic sliding door and multi-dimensional operator’s console design enhance the humanized operation experience of the machine.
- Its strong power can provide professional turning and milling processing capability.
- Through the combination of B-axis, milling axis, positive and negative spindles and center frame, the machine tool shows powerful compound machining performance, and only one clamping can reach the production efficiency of multiple ordinary equipment, saving time and labor costs, and greatly improving the utilization rate of the equipment.
- In addition, the machine is equipped with a high-precision drive system, including precision ball screws and linear rolling guides, to ensure the rapid stability and high positioning accuracy of the tool holder movement.
- In order to prevent deformation of components due to heat, the 9-axis mill-turn machining center is also specially designed with a cooling device to reduce the generation of thermal displacement. The machine tool cooling and thermal balancing system it is equipped with effectively enhances machining accuracy and stability, while preventing deformation of components and further improving machining accuracy.

Applications
- 9 axis turning & milling composite center DTM-B70ST series by a variety of functional components can achieve six complete processing, truly realize a machine function integration, multi-process, multi-process composite. With turning, boring, milling, drilling, tapping and other functions of complex processing capabilities, can be quickly and high quality to complete the processing of complex workpieces, especially for various industries in the shape of complex, high precision requirements of shaped rotary parts (such as barrels, crankshafts, blades, etc.) processing.
- It is widely used in automotive manufacturing, aerospace, mold manufacturing, machinery manufacturing, electronics industry and other industries with high precision batch processing.

PARAMETERS | MTN-B70S | |
Tool interface | HSK-T63 | ● |
CAPTO C6 | ○ | |
Tool magazine | 40 | ● |
80 | ○ | |
120 | ○ | |
Sub-tool magazine | 6 | ○ |
Workpiece clamping device | 12-inch hydraulic chuck (spindle) | ● |
15-inch hydraulic chuck (spindle) | ○ | |
10-inch hydraulic chuck (sub-spindle) | ● | |
12-inch hydraulic chuck (sub-spindle) | ○ | |
Center frame | K5.1(SMW) | ○ |
K6(SMW) | ○ | |
Tailstock | servo drive | — |
Chip cooling | Internal cooling pressure 2Mpa | ● |
Internal cooling pressure 7Mpa | ○ | |
Magnetic scraper chip conveyor | ○ | |
One Click Self-Cleaning System | ● | |
High precision | X/Y/Z Screw oil cooling | ● |
X/Y/Z Screw oil-air lubrication | ● | |
X/Y/Z scale | ● | |
X2/Z2 scale | — | |
Roller linear guideway | ● |
Note: ● is standard ○ is optional — is not optional
If you have configuration needs you can contact our sales, do professional guidance.
Detailed Advantage
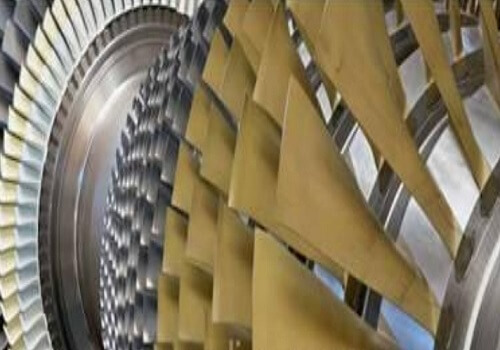
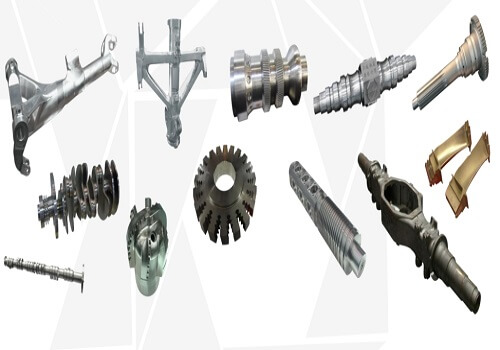
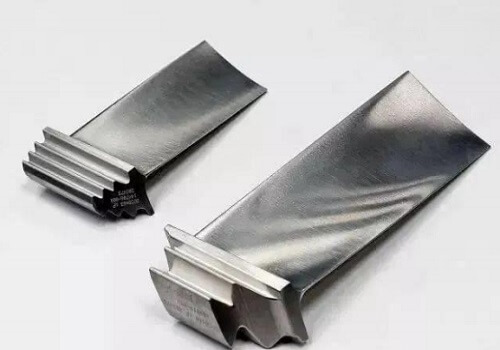
Key technical specifications
1.High-precision machining: Through careful optimization of the structure and machining accuracy of key machine components such as bed, saddle, screw and support, as well as enhanced assembly control, the overall accuracy and reliability of the 9 axis mill&turn machining center has been significantly improved. Repeat positioning accuracy has been significantly improved by 30%, and some of the performance indexes have even reached the standard of precision-grade machine tools, ensuring the accuracy and consistency of the machining process.
2.Efficient and stable operation: the machine is equipped with an automatic lubrication system to ensure that the guideway and ball screw are continuously and effectively lubricated; the automatic chip removal system and the forced cooling function ensure the stability of the machine during long-time, high-intensity machining. The spindle can reach a maximum speed of 3,500 rpm, with a rapid traverse speed of 38 meters per minute and a tool change time of only 1.8 seconds. The combination of these high-performance indicators increases the machine’s machining efficiency by more than 10%, making it ideal for applications that require long periods of continuous operation.
3.Comprehensive Protection and Self-Diagnostics: The 9 axis mill turn machining center adopts a fully enclosed protection design, effectively preventing the leakage of iron chips and coolant and keeping the working environment tidy. The machine is also equipped with limit protection and system self-diagnostic prompts, which can provide timely warnings in case of problems and ensure the continuous and stable operation of the machine, especially adapted to 24-hour uninterrupted work system of the production line, providing a reliable and efficient machining solution for the precision manufacturing industry.
Get In touch
(+86) 13295238763
24 hours online service
Address No. 2 Xintai Road, Economic and Technological Development Zone Jingjiang City Jiangsu Province, China
Email cncitd@minnuo.com